Choosing the Right Casters for Your Carts and Dollies

Selecting the right casters for your OEM carts and dollies is more than just a detail—it's a vital decision that impacts your equipment's performance, longevity, and safety. With the wide variety of options available, from materials and sizes to durabilities and mobility features, choosing the perfect casters can be overwhelming. In this post, we'll guide you through the key factors to consider when selecting casters, helping you make informed decisions that will keep your operations running smoothly and efficiently.

1. Understand Your Application Needs
Before selecting casters for your carts and dollies, there you should consider. It's essential to thoroughly understand the specific needs of your application so you can ensure that your casters perform reliably. Consider factors such as the surface type the casters will roll on, the amount of weight they need to support, and whether they will be exposed to certain environmental conditions or harsh substances.
Load Capacity
It's essential to accurately assess the total weight your carts and dollies will need to handle to ensure that each caster is rated to handle its share of the load. Overloading casters can lead to a range of issues, including increased rolling resistance, difficulty in maneuvering, and premature failure. This not only risks damaging your equipment but also poses safety hazards for operators. Select casters with an appropriate load capacity to ensure greater performance, a longer lifespan, and increased safety in your material handling processes.

Flooring Conditions
Consider the type of flooring your casters will be used on, such as concrete, tile, or carpet, and evaluate its condition, whether it's smooth, rough, or uneven. Hard floors like concrete or tile may require casters with softer tread materials, such as rubber or polyurethane, to reduce noise and prevent damage to the floor. On the other hand, rough or uneven surfaces might necessitate casters with larger wheel diameters and shock-absorbing capabilities, like spring-loaded casters, to reduce vibration. By carefully matching the caster to the flooring type and condition, you can enhance mobility, while protecting your flooring.

Environment
Think about the environment in which the equipment will be used. For example, wet or corrosive environments, such as food processing facilities, outdoor areas, or chemical plants, require casters made from materials that resist rust and corrosion, such as stainless steel or zinc-plated casters. Casters with sealed bearings can also prevent water or corrosive substances from penetrating and damaging the internal components. In contrast, dry and clean environments, like indoor warehouses or office spaces, may not require such specialized materials, allowing for a broader range of options. However, other factors, such as extreme temperatures or the presence of debris, should be considered. Selecting casters designed to withstand the specific environmental conditions ensures reliability, reduces maintenance needs, and extends the lifespan of your equipment, ultimately leading to more streamlined operations.

2. Caster Rig Types
The caster rig, or bracket, is the framework that holds the wheel and attaches it to the equipment. The design and functionality of the caster rig determine how the caster moves, whether it swivels or remains fixed, and how it performs under various conditions. By familiarizing yourself with the primary rig types—such as rigid, swivel, and specialty rigs—you can make informed decisions that provide the perfect balance of mobility, stability, and durability for your specific needs. Here are some common rig types used for material handling carts and dollies.
Rigid Casters

Rigid casters are mounted on a fixed bracket, limiting the wheel to single-directional movement. These provide a fixed direction and are ideal for straight-line movement. Unlike swivel casters, rigid casters do not rotate, but they make up for their reduced maneuverability with increased stability and control. Rigid casters are best suited for applications requiring the movement of heavy loads in a single direction, like dollies, heavy-duty platform trucks, pallet jacks, conveyor carts, and tool carts.
Swivel Casters
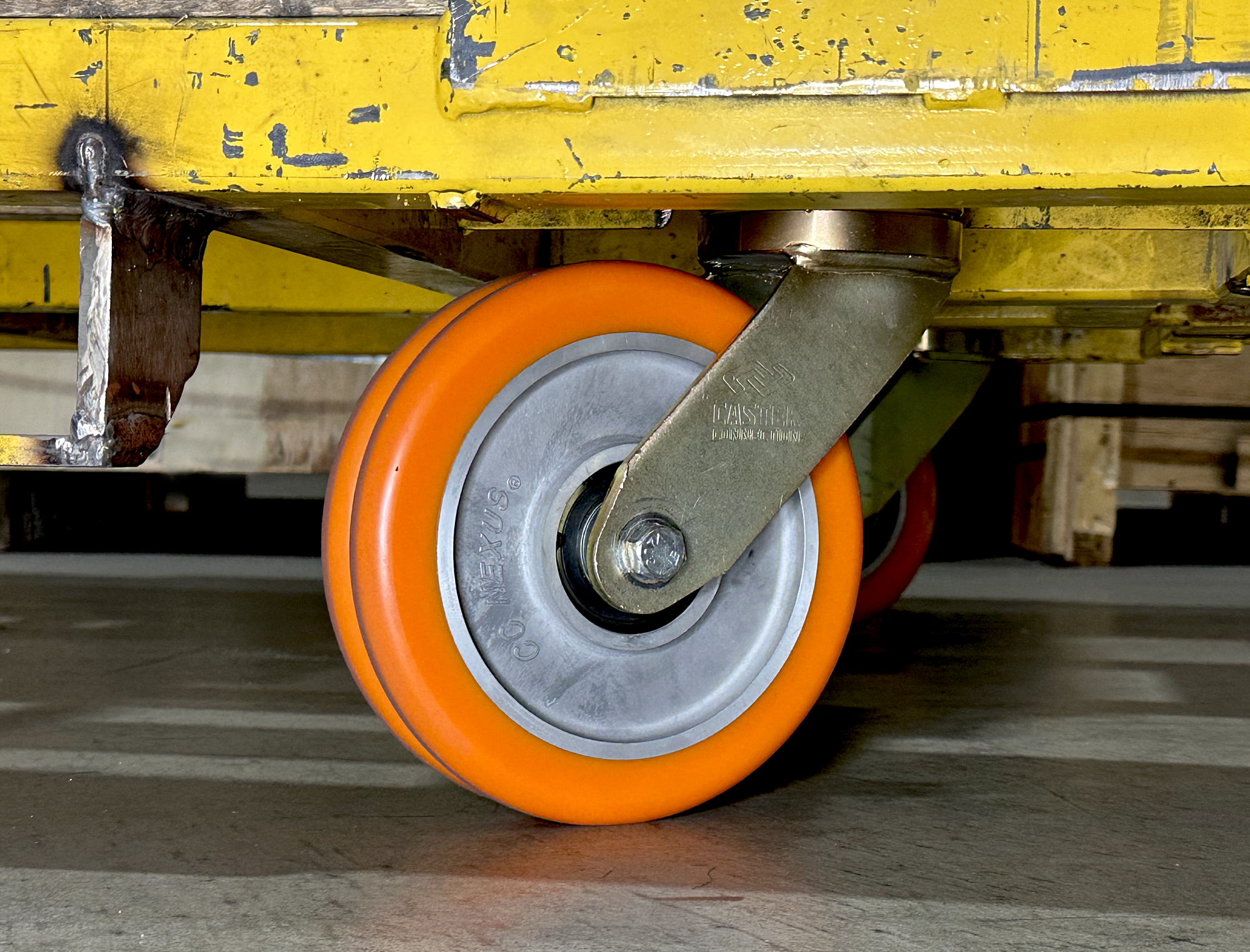