How to Choose the Right Casters for MRO Applications
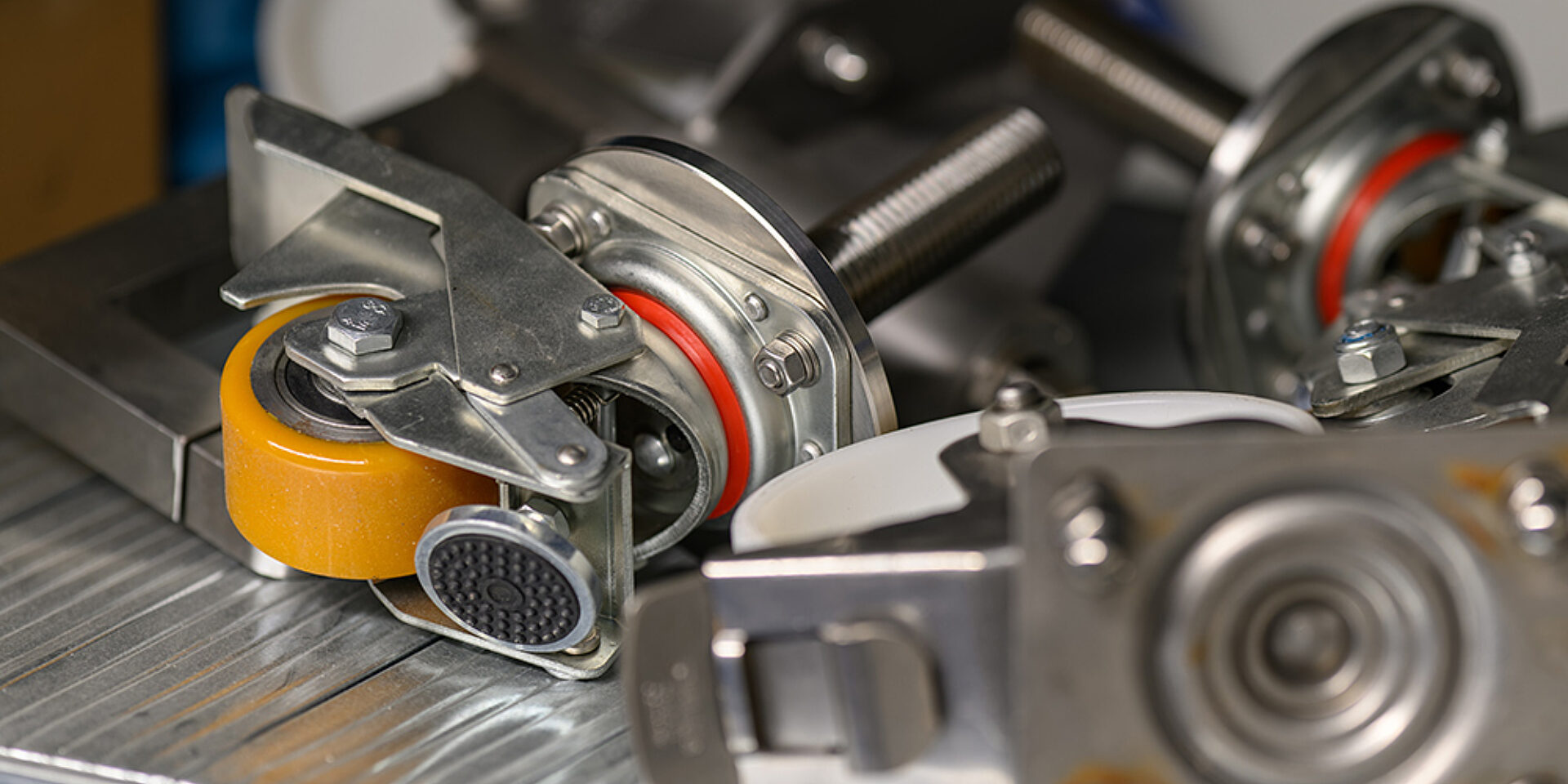
In high-stakes MRO environments, caster failure is more than an inconvenience. It can lead to unplanned downtime, safety risks, and unnecessary maintenance costs. Many teams simply replace failed casters with the same model, assuming it is the quickest fix. In reality, this like-for-like replacement approach often misses opportunities to improve performance, reduce strain on operators, and extend equipment life.
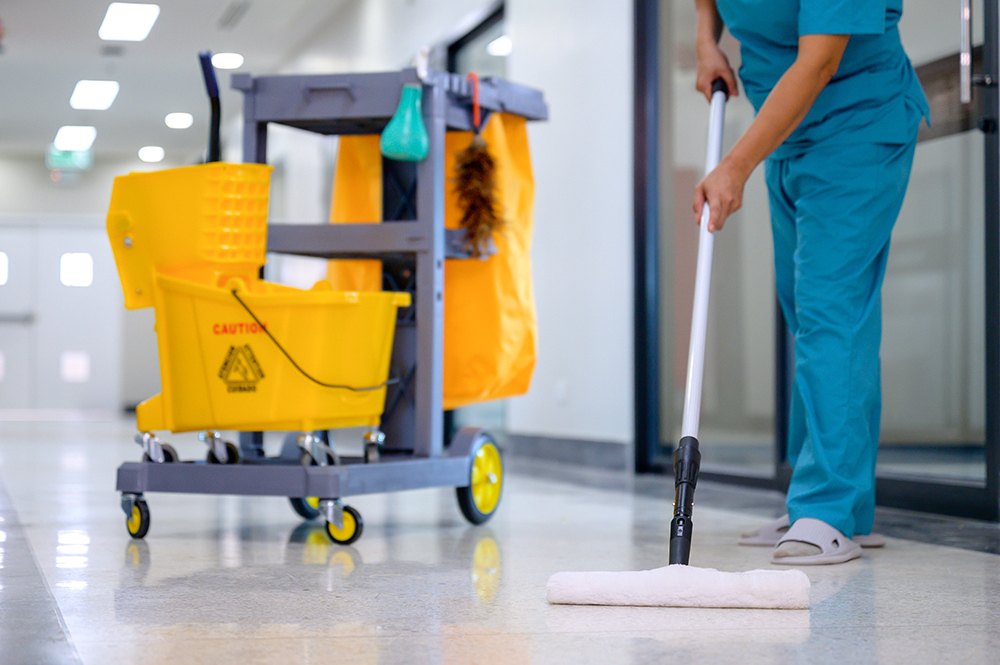
Whether your team manages tool carts, mobile workstations, or heavy-duty dollies, proper caster selection plays a critical role in mobility, safety, and efficiency. This guide outlines how to make informed replacement decisions based on floor type, load, environmental conditions, and more.
Step 1: Match Caster Material to Floor, Load, and Environment
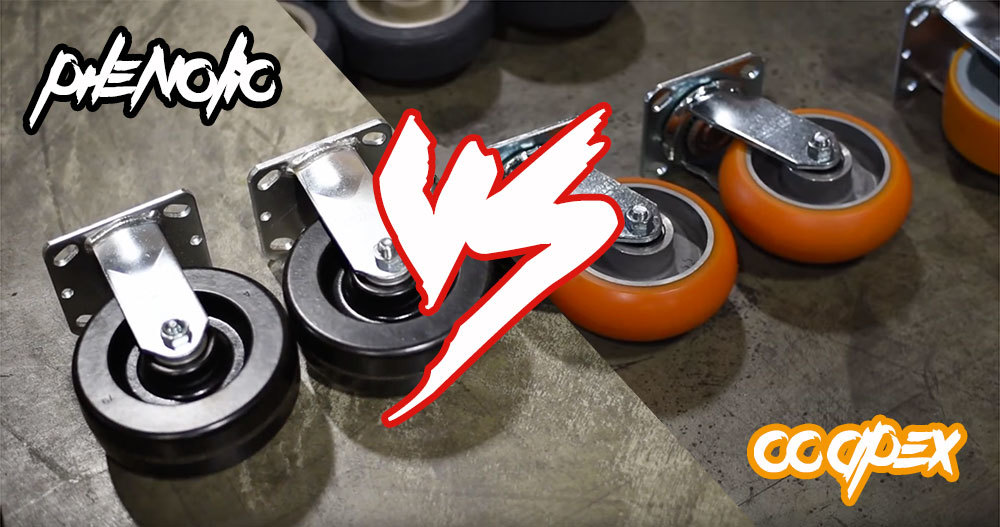
The right caster material depends on where and how it will be used. Mismatched wheels are one of the most common causes of caster failure, but also one of the easiest to avoid.
Floor Type
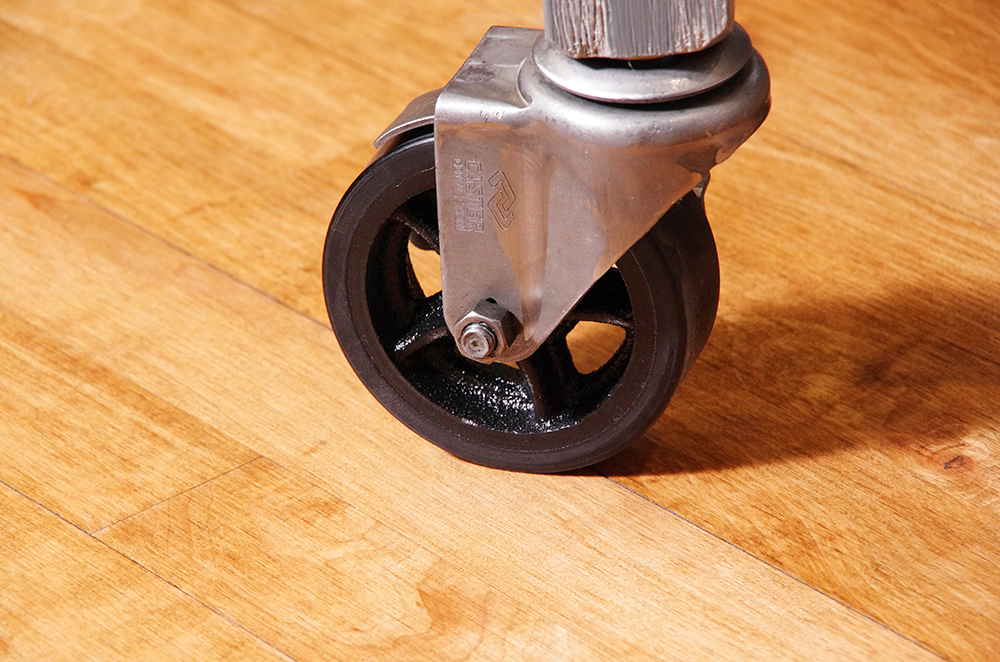
Different floor surfaces place different demands on caster materials. Choosing the right tread for your surface helps preserve floors, reduce noise, and minimize rolling resistance.
Smooth indoor concrete:
Use polyurethane or rubber treads. These materials roll quietly, reduce operator fatigue, and protect floor surfaces.
Rough concrete or asphalt:
Select cast iron, forged steel, or abrasion-resistant polymer wheels that can handle impact and surface irregularities.
Wet or oily floors:
Choose treads with good traction and rigs made from corrosion-resistant materials, like stainless steel. Look for designs that resist chemical degradation and shed buildup.
Load Rating
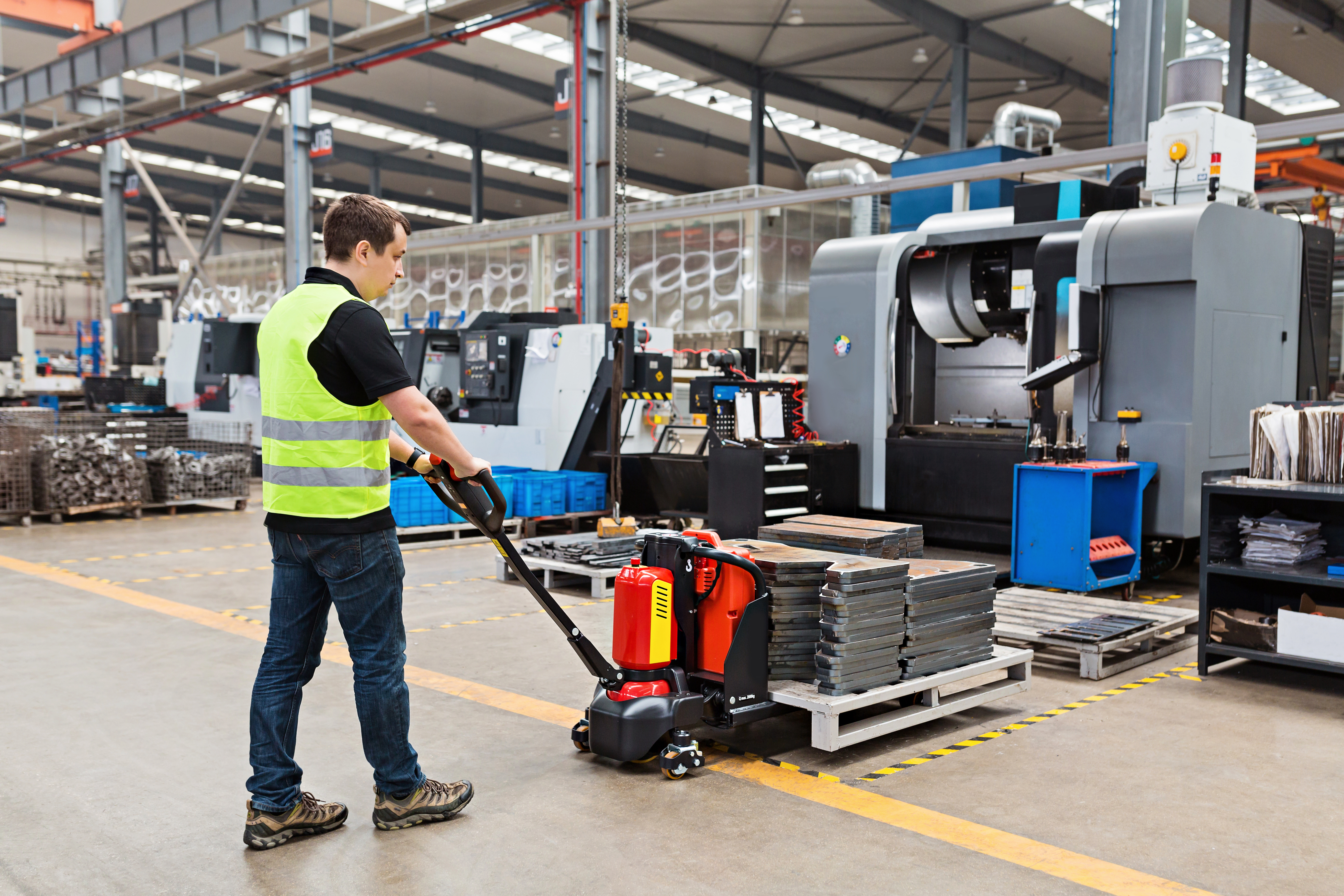
Every caster is rated for a specific load, both in motion (dynamic) and at rest (static). It is important to match this rating to your equipment and use conditions.
Example: If you have a cart that weighs 1,200 pounds and uses four casters, each caster should be rated for at least 400 pounds. Adding a safety margin is strongly recommended for dynamic loads or uneven floors.
Environmental Factors
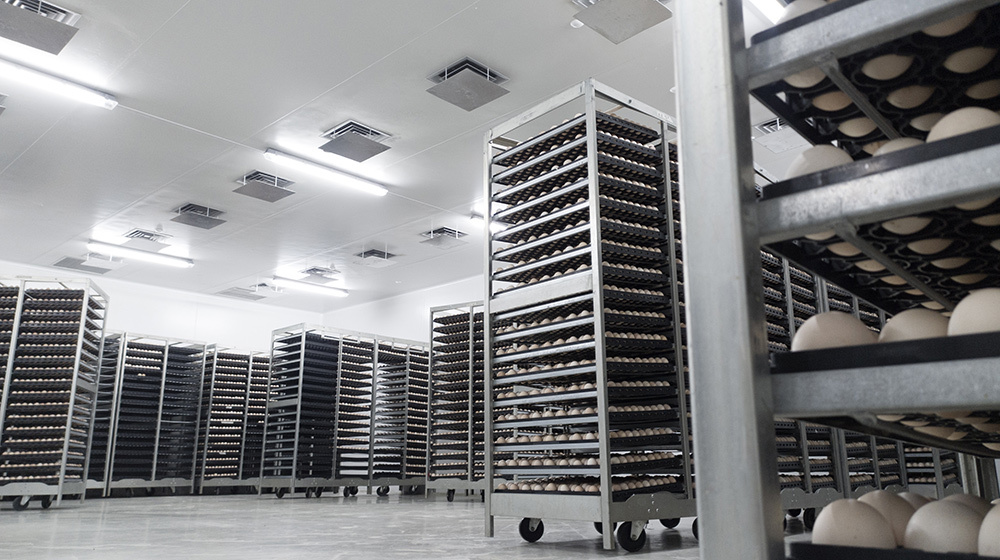
Environmental stressors such as temperature, moisture, or chemicals can quickly degrade standard casters. Selecting materials that match the conditions will significantly increase performance and service life.
-
High-heat zones: Use wheels made from high-temperature compounds and lubricants
-
Cold storage: Select casters that remain flexible and functional in low temperatures
-
Chemical exposure or washdown: Use stainless steel rigs and sealed bearings to prevent corrosion and contamination
You should also consider the tradeoff between durability and floor protection. Harder wheels tend to last longer but can damage floors and increase push/pull force. Softer treads are gentler on surfaces and easier to move, but may wear out faster.
Step 2: Selecting the Appropriate Brake System
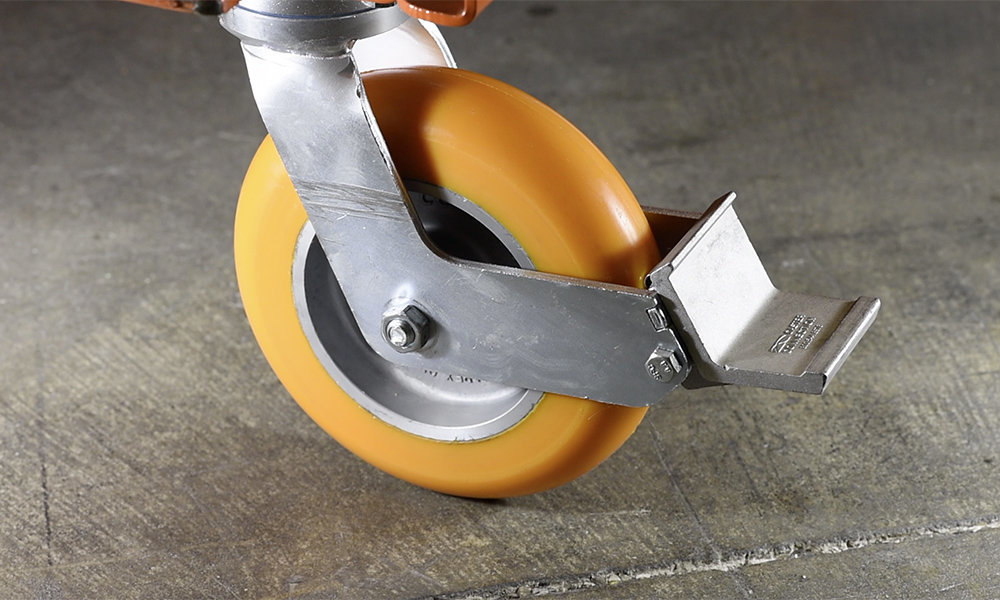
Brake systems are often overlooked but play a critical role in workplace safety and equipment control. Matching the right brake to the application prevents unwanted movement and provides needed stability in high-traffic or incline-prone environments.
Brake Types
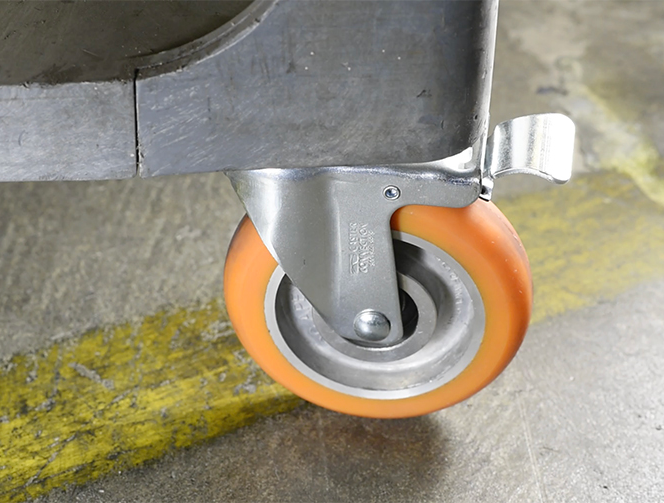
There are several brake options to choose from. Each offers specific advantages based on the type of equipment and conditions.
-
Total-lock brakes secure both the wheel and the swivel. Best for tool carts, mobile workstations, and inspection tables.
-
Floor locks extend down to contact the floor and hold heavy carts in place. Useful during loading or maintenance.
-
Deadman brakes automatically engage when the operator lets go of the handle. These are important on ramps, inclines, and in safety-sensitive areas.
Choosing the Right Brakes for Your Equipment
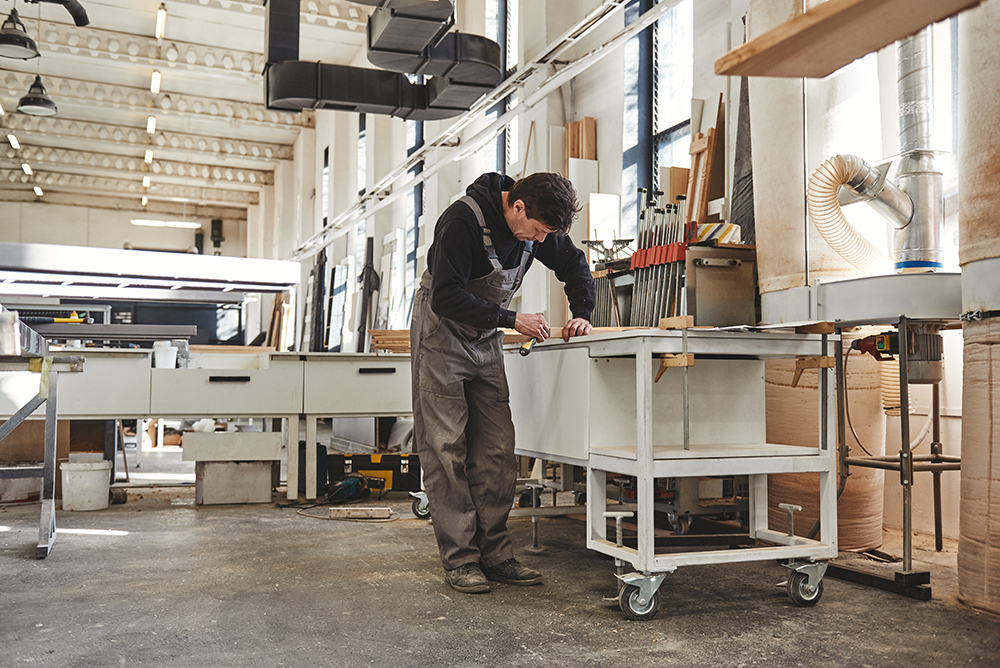
To help narrow your brake selection, here are some common applications and what tends to work best in each scenario:
For toolboxes and mobile workstations:
Total-lock brakes are the most effective choice. They secure both the wheel and the swivel, giving you full stability when you need the equipment to stay in place during use.
For carts in loading or staging areas:
Floor locks are ideal. They provide a firm, direct connection with the ground and prevent movement while items are being added or removed from the cart.
For ramps, inclines, or safety-sensitive zones:
Deadman brakes offer added protection. These brakes engage automatically when the handle is released, helping prevent rollaways and unexpected movement on sloped surfaces.
The right brake system not only improves safety, it also streamlines daily operations by keeping equipment exactly where it is needed.
Step 3: Know When to Upgrade Instead of Replace
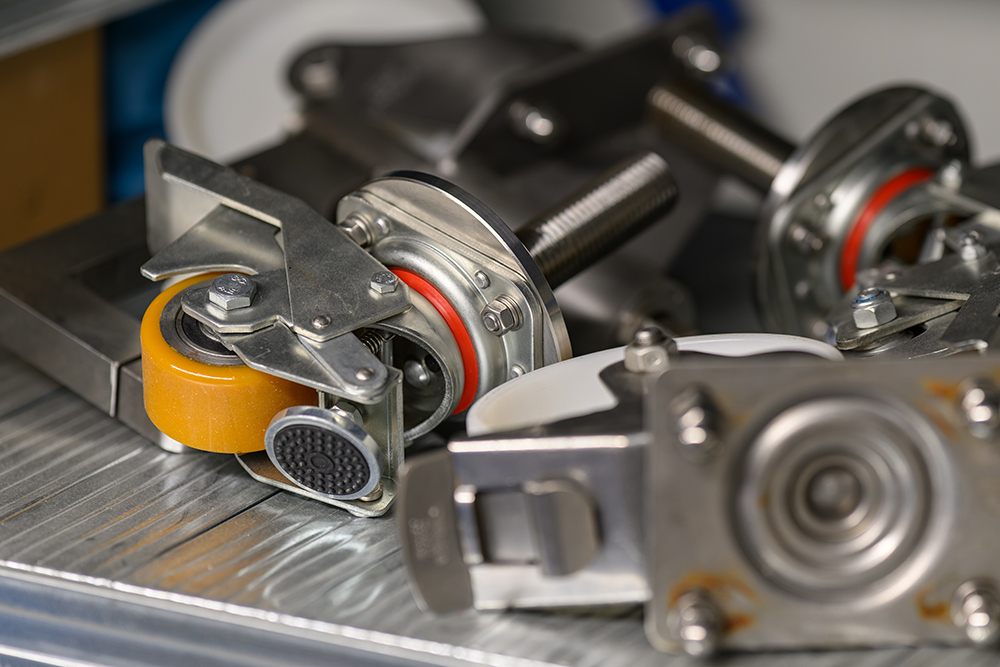
Replacing a failed caster with the same part might seem efficient, but it does not address underlying performance issues. If you are experiencing repeat failures or operator discomfort, an upgrade may provide lasting improvements in both safety and productivity.
Signs You Should Upgrade
- Casters are replaced more than once per quarter
-
Staff report strain, push/pull resistance, or difficulty maneuvering
-
Equipment vibrates, veers off course, wobbles, or drags during use
-
Recent changes in flooring or workflow have introduced new demands
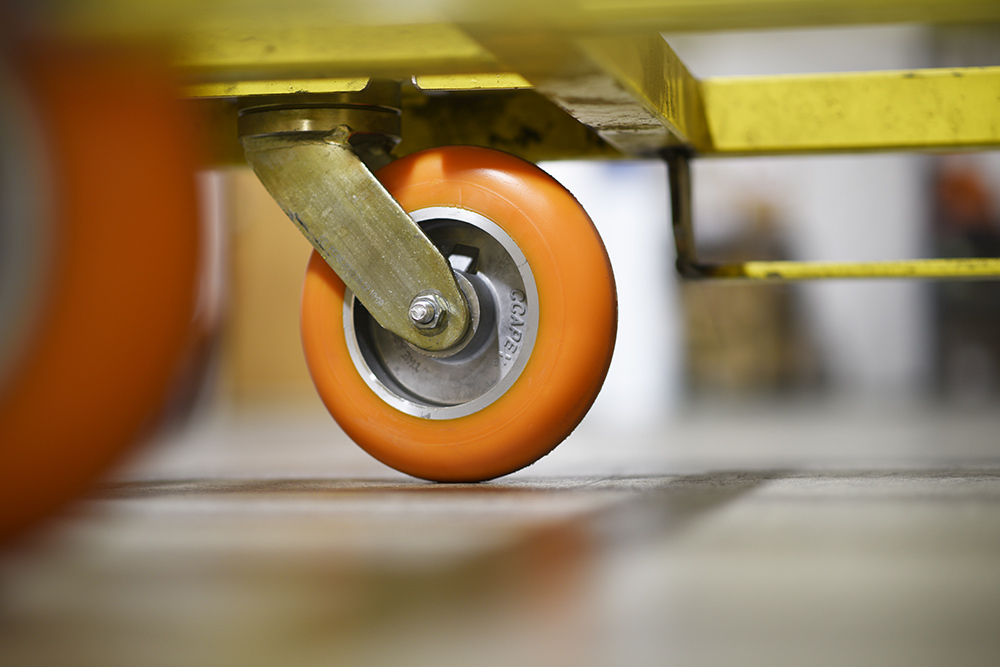
Upgrade Examples
- Steel wheels replaced with polyurethane: Improves shock absorption and reduces vibration
-
Greased rigs upgraded to sealed, maintenance-free rigs: Reduces maintenance time and prevents contamination
-
Standard casters upgraded to ergonomic models: Lowers push/pull force and improves safety for repetitive tasks
Ergonomic caster upgrades can reduce push/pull force by up to 50 percent. That translates to fewer injuries, reduced fatigue, and greater long-term value.
Step 4: Apply the Single Caster Load Formula
Caster load ratings are typically calculated by dividing total equipment weight across all wheels. However, this method assumes that all casters carry equal weight at all times — which is rarely the case on real-world floors.
The Three-Caster Rule
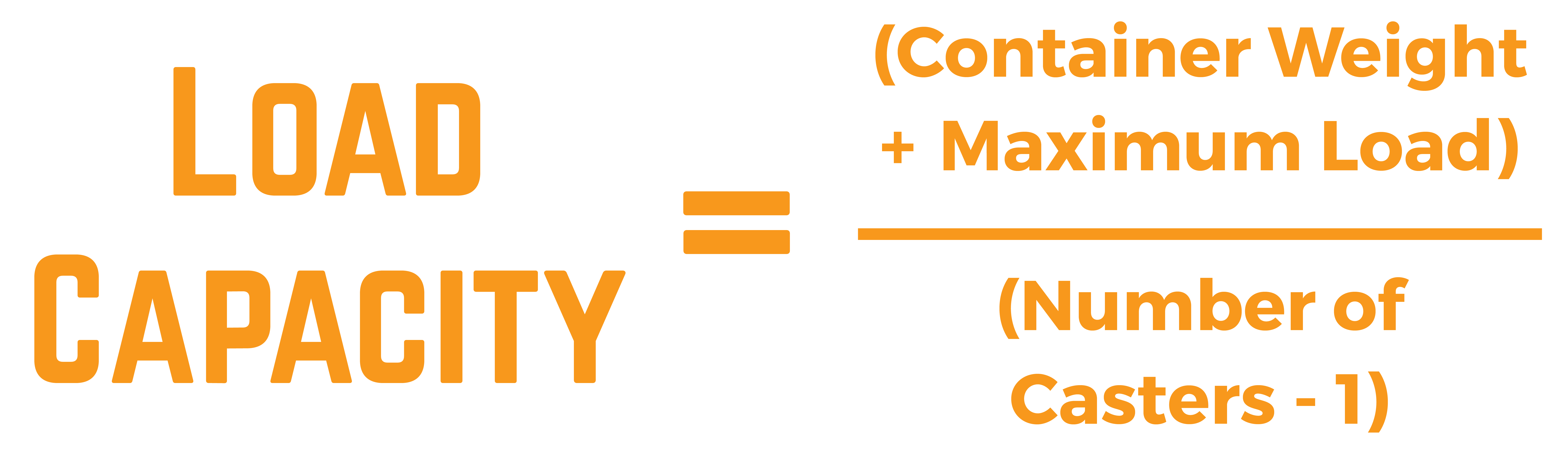
To prevent overload on uneven surfaces, choose casters that can support the entire load using only three of the four wheels.
Example: If your cart weighs 1,000 pounds, each caster should be rated for at least 333 pounds. This ensures stability when one caster temporarily lifts off due to a ramp, threshold, or floor variation.
Our CC Apex line is built with this principle in mind. Each model is designed to perform reliably even when conditions shift and weight distribution is imperfect.
CC Apex: Our Most Trusted MRO Solution
If you are looking for a caster that performs consistently in demanding environments, CC Apex is a proven solution used across a wide range of MRO applications. It is engineered for durability, quiet rolling, and ergonomic performance, even under shifting loads and uneven floor conditions.
CC Apex is especially well-suited for teams that need a dependable caster to support mobile workstations, tool carts, or heavy equipment in dynamic facilities. Its polyurethane tread helps protect floors and reduce push force, while its rugged rig options support long-term use with minimal maintenance.
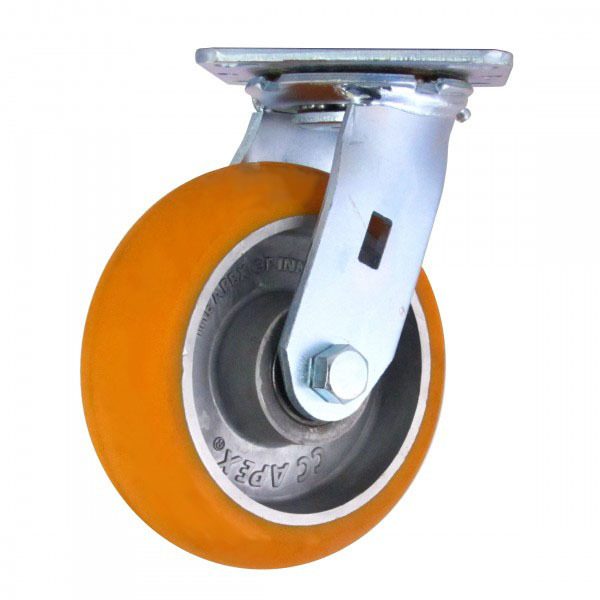
SKU: CC-1210-600200-40-T1
ALT-SKU: CCAPEX-6S
-
- Overall Height
- 7-1/2"
- Wt. Capacity
- 1,000 lbs.
- Wheel Width
- 2"
- Wheel Diameter
- 6"
SKU: CC-1010-600200-40-T1
ALT-SKU: CCAPEX-6R
-
- Overall Height
- 7-1/2"
- Wt. Capacity
- 1,000 lbs.
- Wheel Width
- 2"
- Wheel Diameter
- 6"
6" CC Apex Kingpinless Swivel Caster
SKU: CC-2110-600200-40-T1
ALT-SKU: CCAPEX-6S-KP
-
- Overall Height
- 7-1/2"
- Wt. Capacity
- 1,000 lbs.
- Wheel Width
- 2"
- Wheel Diameter
- 6"
6" CC Apex set - 2 swivel/2 rigid
SKU: CC-10/1210-600200-40-T1-SET4
ALT-SKU: CCAPEX-6S/R-set-2s/2r
-
- Overall Height
- 7-1/2"
- Wt. Capacity
- 1,000 lbs.
- Wheel Width
- 2"
- Wheel Diameter
- 6"
6" CC Peak Maintenance-Free Swivel CC Apex Caster
SKU: CC-3110-600200-40-T1
ALT-SKU: CCAPEX-6S-EMF
-
- Overall Height
- 7-1/2"
- Wt. Capacity
- 1,000 lbs.
- Wheel Width
- 2"
- Wheel Diameter
- 6"
6" Stainless Steel CC Apex Kingpinless Swivel Caster
SKU: DC-S510-600200-45-T1
ALT-SKU: CCAPEX-6S-SS-KP
-
- Overall Height
- 7-1/2"
- Wt. Capacity
- 1,000 lbs.
- Wheel Width
- 2"
- Wheel Diameter
- 6"
6" CC Peak Maintenance-Free Swivel CC Apex Caster w/ Built-In Brake
SKU: CC-3210-600200-40-T1-BIB
ALT-SKU: CCAPEX-6S-EMF-BIB
-
- Overall Height
- 7-1/2"
- Wt. Capacity
- 1,000 lbs.
- Wheel Width
- 2"
- Wheel Diameter
- 6"
SKU: DC-4L10-600200-40-SF
ALT-SKU: CCAPEX-6S-KP-STEM-T1
-
- Overall Height
- 7-3/8"
- Wt. Capacity
- 1,000 lbs.
- Wheel Width
- 2"
- Wheel Diameter
- 6"
Make Mobility Work for You
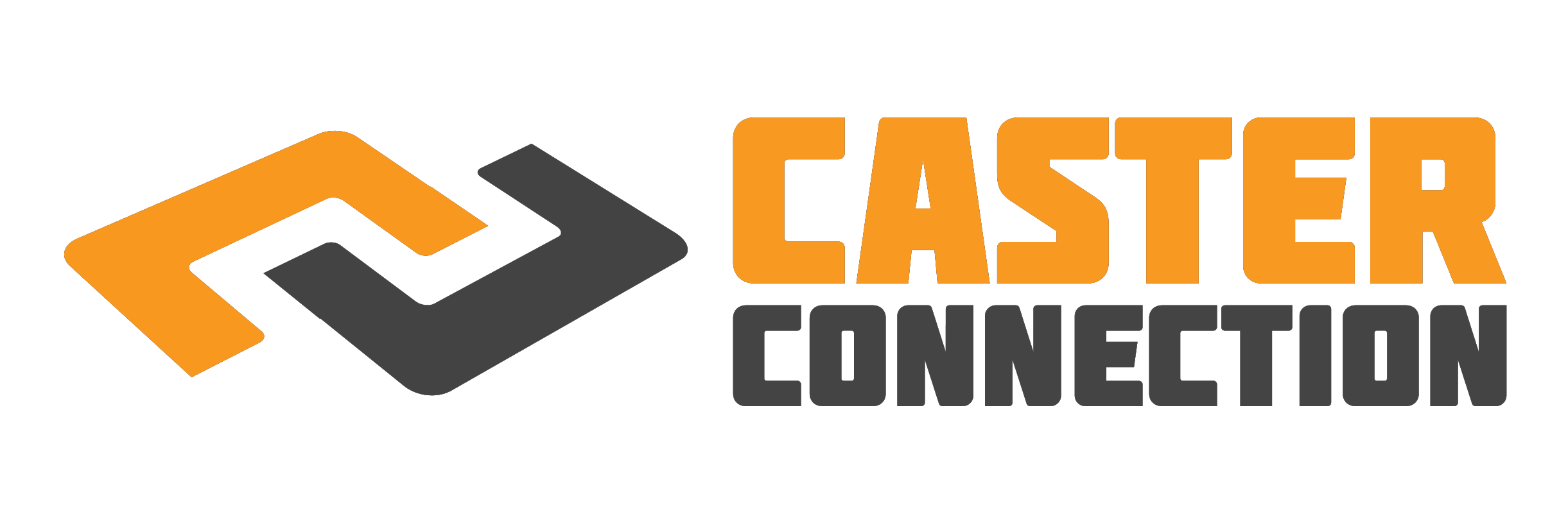
Casters may be small, but their impact on safety, efficiency, and operator well-being is significant. Better caster choices lead to smoother mobility, fewer injuries, and lower maintenance costs.
To recap:
-
Match caster materials to floor type, load weight, and environmental conditions
-
Select a brake system that fits your use case and equipment style
-
Upgrade when repeat failures or ergonomic concerns arise
-
Use the three-caster rule to plan for uneven surfaces
At Caster Connection, we specialize in matching the right caster to the right application. If your current setup is limiting performance or increasing risk, we are ready to help you build something better.
If you are unsure which caster is right for your equipment, we are here to help.
Browse the CC Apex Line
Explore our most versatile caster family, ideal for tool carts, mobile workstations, and heavy-duty industrial applications.
Need Product Selection Help?
Contact our team for guidance. We can help you choose the right materials, wheel size, rig type, and brake features based on your specific environment.