Selecting Casters in the Automotive Manufacturing Industry
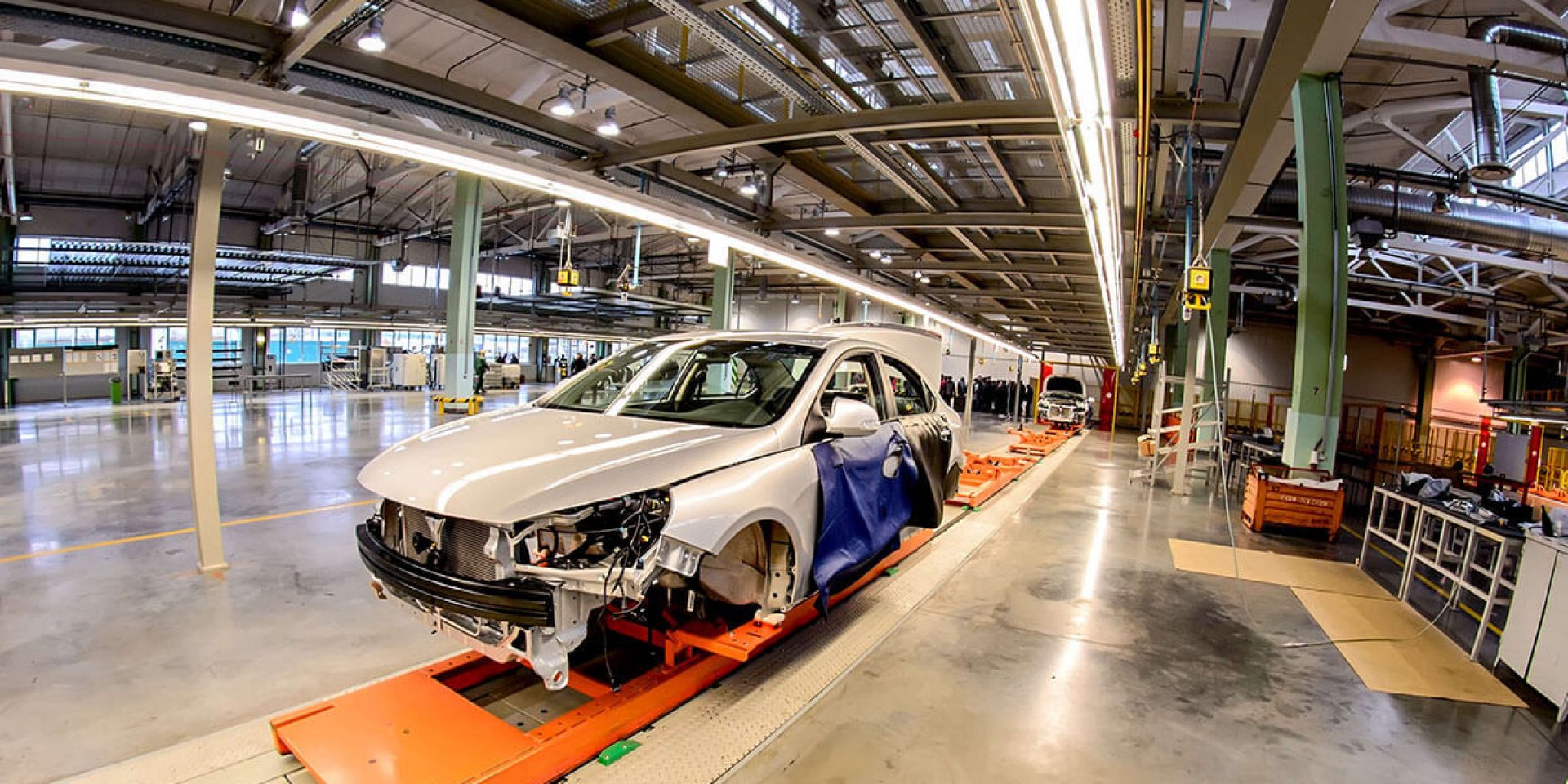
If you’re reading this, then you likely understand the great importance of casters’ role in automotive manufacturing. The proper casters and wheels in your application can mean the difference between uptime and downtime, employee productivity and employee injury, or even maintenance prevention vs. costly maintenance.
Casters play a role in:
- Push/pull force for manual maneuvering of carts
- Performance in towline applications
- Forklift-free initiatives
- Maintenance and repair frequency
- Decibel output
- Floor protection
Read more below for in-depth information regarding the role casters play in each facet of automotive manufacturing.
THE IMPORTANCE OF CASTER COMPONENTS IN AUTOMOTIVE MANUFACTURING
WHEELS
- The resiliency of the wheel is an important factor in determining how the wheel performs when rolling over physical barriers such as thresholds or debris.
- Softer (lower durometer) wheels to some extent conform to the shape of the object(s) that they roll over, meaning debris and barriers do not typically cause damage to softer wheels.
- Wheels that have the proper durometer and resiliency reject embedding of debris and flat-spotting. Embedding typically occurs in hard, non-resilient wheels and can cause floor damage, added rolling resistance, increase noise and vibration.
- Harder wheels typically roll easier than soft wheels. When using hard wheels, one must consider the likelihood of the wheels encountering debris and the floor type.
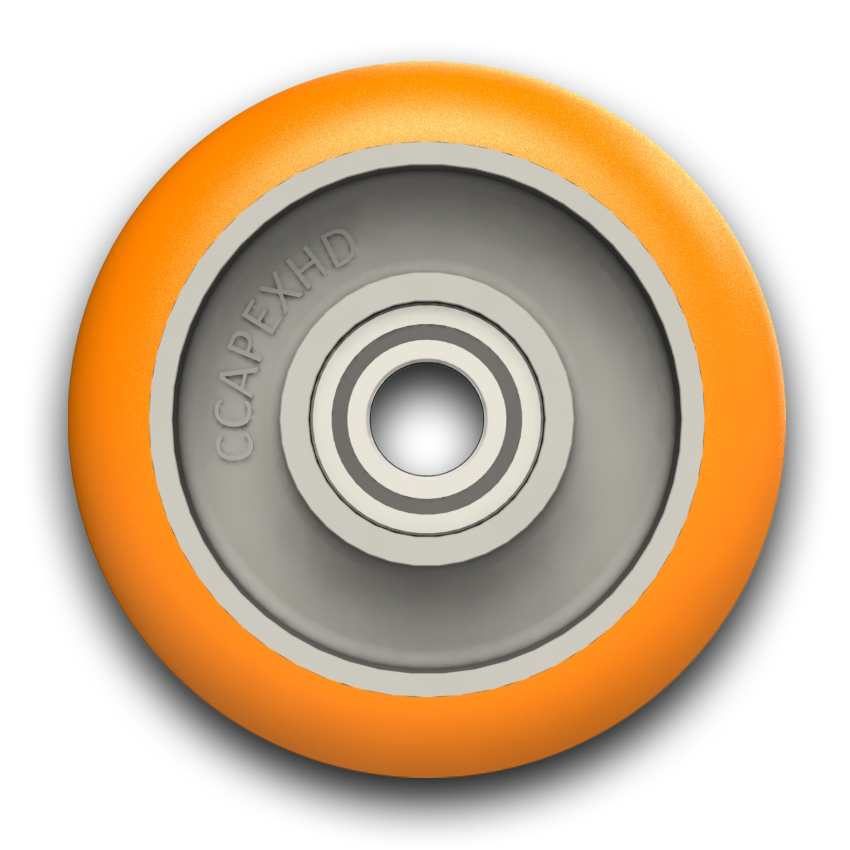
WHEEL DIAMETER
- The larger the diameter of a wheel, the lower the rolling resistance will be. While this is an important factor, it is frequently overlooked.
- The more uneven or coarse a floor is, the larger the wheel’s diameter should be. Rough floor conditions may include thresholds, debris, grates, etc.
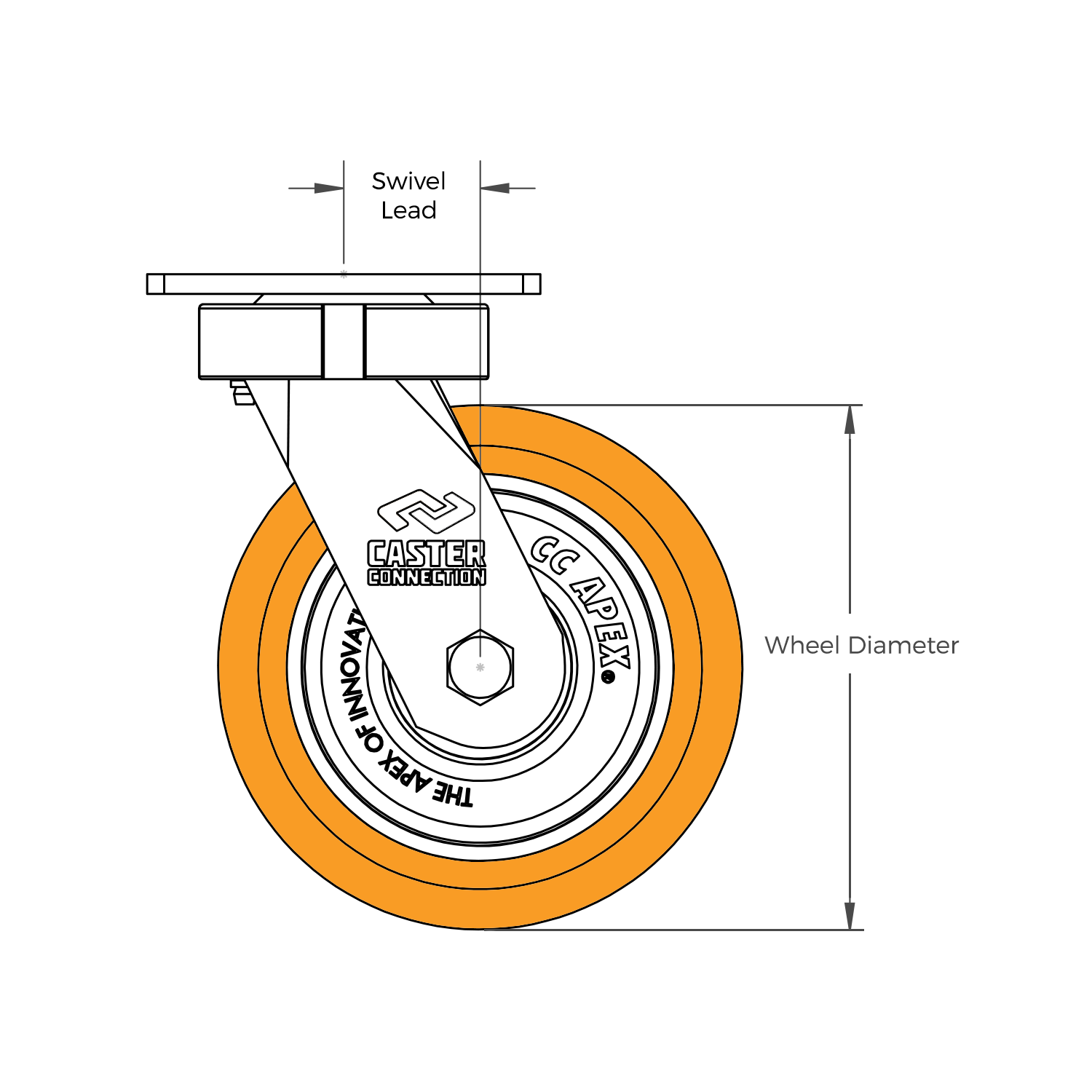
CASTER RIG TYPE
- Ease of swivel and dispersion of load play a humongous role in caster rig ergonomics. The precision of a swivel caster rig’s construction determines how easily a rig is able to swivel, which directly affects manual push/pull ergonomics.
- The kingpinless swivel caster rig is the go-to swivel caster rig for towline use because it can handle heavy weight loads and offers great durability due to its lack of a kingpin. Without the kingpin, a caster is able to more evenly distribute weight and ease the pressure on the caster.
- Casters with a kingpin often fail in towline applications because high velocity towing can wear down the kingpin and cause catastrophic failure.
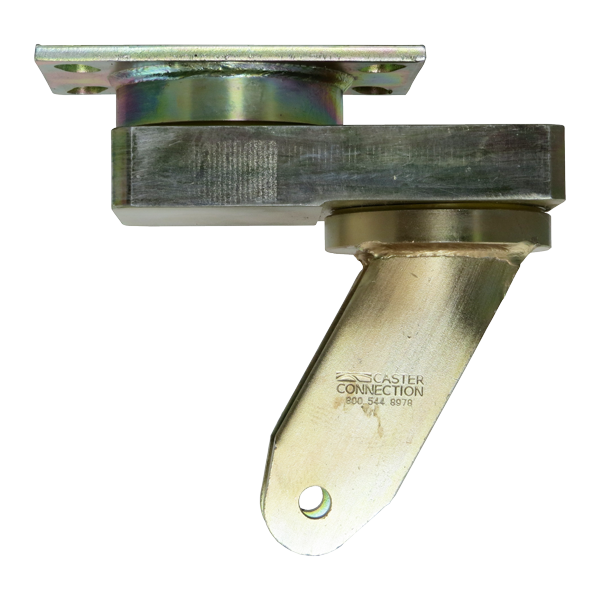
SWIVEL LEAD
- A commonly overlooked factor for caster configuration, swivel lead (the distance between the centerline of the kingpin and the centerline of the axle of a swivel caster) determines the ease with which a caster swivels.
- With a standard swivel lead, an application will likely experience caster flutter. Caster flutter occurs when the caster wheel is not trailing far enough behind the raceway. To alleviate caster flutter, you can extend the lead with an extended-lead rig. An extended-lead rig enables the caster wheel to naturally trail, eliminating caster flutter, reducing noise and strain on the raceway – along with all the moving parts.
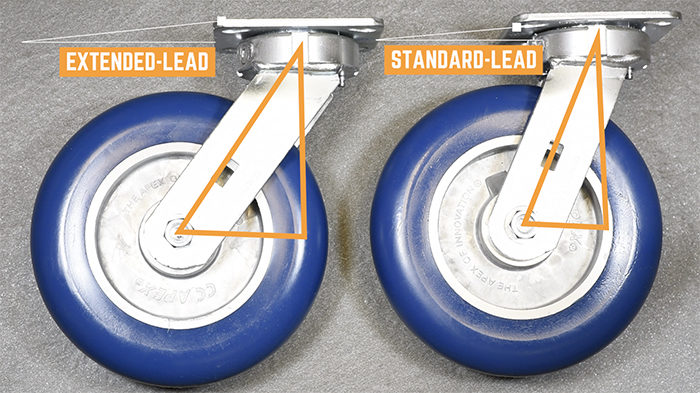
BEARINGS
- Sealed precision ball bearings are ideal for towlines because they’re maintenance free, have low decibel output, and are designed for higher speeds and frequent turns. For manually pushed carts, precision bearings are the preferred choice due to the ease of rollability, providing the best in ergonomic push-pull forces.
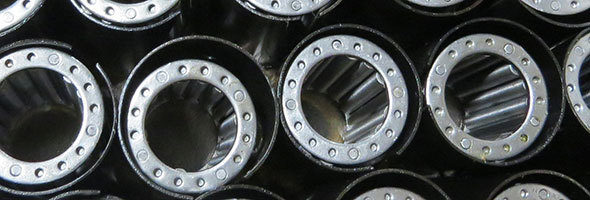
LOAD RATING
- The maximum amount of weight a caster or wheel will hold. The maximum recommended load per caster or wheel based on intermittent operation over smooth floors at speeds not exceeding 3 m.p.h., with no shock loading or adverse environmental conditions.
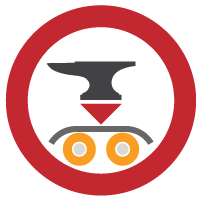
CASTERS’ ROLE IN ERGONOMIC PUSH/PULL PERFORMANCE
Casters play a tremendously large ergonomic role in automotive manufacturing environments where manually pushed and pulled carts are used. Implementing the proper caster solution for your manual push/pull application can help to prevent employee injuries that cause downtime and increased workers’ compensation claim costs.
Some components of casters that affect ergonomic performance include:
- Wheel Tread/Composition
- Wheel Diameter
- Bearing
- Rig/Fork
Some awesome ergonomic solutions for automotive manufacturing include our CC Apex, CC Stark, CC Stout, CC Nylex, and CC Peak lines.
CASTERS’ ROLE IN TOWLINE APPLICATIONS
Casters are of great importance for organizations that utilize towline applications in their automotive manufacturing plants. From our February 2013 blog post Improving Towline Efficiency:
Towlines require casters that will not slide laterally, can endure high speeds and can withstand the heat generated by high-speed towing.
2 awesome solutions for towline applications are our CC Apex wheel paired with the CC Alpha Kingpinless Swivel Rig, as well as our CC Stark line of casters.
6" CC Apex Extended-Lead Kingpinless Swivel Caster
SKU: CC-2210-600200-40-T1
ALT-SKU: CCAPEX-6S-KP-EXT
-
- Overall Height
- 7-1/2"
- Wt. Capacity
- 1,000 lbs.
- Wheel Width
- 2"
- Wheel Diameter
- 6"
8" CC Apex Kingpinless Swivel Caster with Extended Swivel Lead
SKU: CC-2210-800200-40-T1
ALT-SKU: CCAPEX-8S-KP-EXT
-
- Overall Height
- 9-1/2"
- Wt. Capacity
- 1,200 lbs.
- Wheel Width
- 2"
- Wheel Diameter
- 8"
8" x 2" CC Stark Swivel Caster
SKU: CC-5160-800200-40-T2
ALT-SKU: CCSTARK-8S
-
- Overall Height
- 10-1/8"
- Wt. Capacity
- 2,000 lbs.
- Wheel Width
- 2"
- Wheel Diameter
- 8"
CASTERS’ ROLE IN FORKLIFT-FREE INITIATIVES
We explained casters’ role in forklift-free initiatives in our October, 2017 post: Factors to Consider in Choosing Casters for Forklift-Free Initiatives
The forklift-free initiative underway at many manufacturing plants is intended to boost safety and production rate. Despite the United States having some of the most strict health and safety standards in the world, the country still sees over 20,000 people in the hospital every three days due to injuries caused by forklift accidents. In order to help your organization to reduce costs and increase efficiency, we detail factors to consider in choosing casters for forklift-free initiatives.” –
When deciding to take on a fork-free initiative, an organization most commonly implements a tugger cart system and/or carts that are manually pushed and pulled – both of which operate on casters. In our November, 2017 post Forklift-free Initiative: Using Casters to Pull Towards Lean, we consider the ramifications of implementing an improper caster: A forklift-free system improves efficiencies of moving materials within the plant. Dollies need to bring active parts and kits to the assembly line. All these dollies are moving on industrial casters, making casters one of the most significant investments of material handling carts. Purchasing an incorrect caster for a dolly can lead to decreased business profits by:
- Carts being taken out of circulation
- Slowing down production
- Increasing MRO (maintenance, repair and operating supply) expense
A caster’s overall value is measured by its Total Cost of Ownership (TCO) rather than its initial cost. Casters with low total cost of ownership can prevent overspending, returns, or frequent repurchasing. Casters with high total cost of ownership may cause downtime maintenance and pricey rework.
Both the CC Apex and CC Peak are excellent examples of reaping amazing value beyond the initial cost. The CC Apex has proven to handle high load capacities, reject debris and maintain grip in a towline. The CC Peak offers industry-leading performance to towing applications. Unlike kingpin or kingpinless rigs, CC Peak’s construction allows for even dispersion of load to reduce push-pull efforts by 25-50%. The CC Apex and CC Peak both have a low TCO with benefits of:
- Less downtime
- Fewer production interruptions
- Maximizing production capacity

HOW CASTERS CAN AFFECT MAINTENANCE AND REPAIR FREQUENCY
To save time and money for our clients in the long run, Caster Connection places a large focus on Total Cost of Ownership(TCO) when providing solutions. From our January, 2016 blog post Cost Deployment Modeling for Casters:
Initial Cost vs. Total Cost of Ownership When a company is choosing casters for their application, Total Cost of Ownership must be taken into consideration. High-quality products perform better and last longer, and can be defined by their opportunity costs, demonstrated by less downtime, fewer production interruptions, and maximized production capacity to increase profits.
Caster Connection Director of Business Development Eric Hassen expounds upon this point in a May, 2017 interview:
Can you talk about Cost Deployment and how it can relate to casters? EH: The main objective of cost deployment in regards to material handling, and specifically casters, is to identify problems that increase costs, so the issues can be resolved quickly and effectively while maintaining a balance of quality. Increasing costs from a poor caster can materialize as downtime of the dolly (i.e. tens of thousands of dollars per minute), cost of repair (i.e. caster replacement cost) and labor cost. When choosing the correct caster for each application, our goal is to minimize these costs. Caster Connection provides the expertise needed to make an educated decision and consults each client per application to provide the solution necessary in order to capitalize and maximize the WCM pillars of Cost Deployment and Total Cost of Ownership.” Downtime Cost = # of people waiting * Downtime * Man hour cost Cost of mechanic repair = # of people repairing * Repair time * Man hour cost Cost of rework = # of people reworking * Rework time * Man hour cost
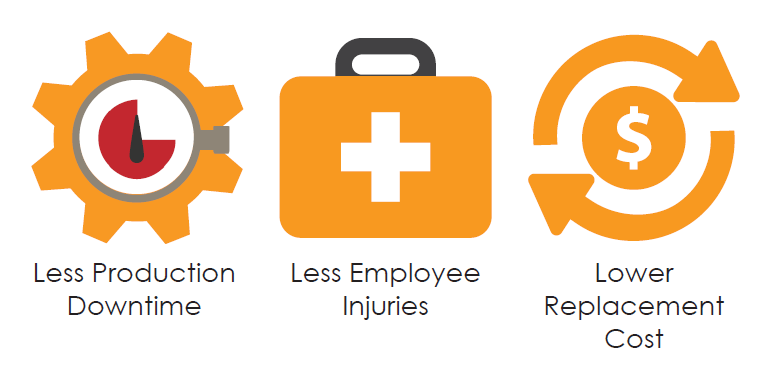
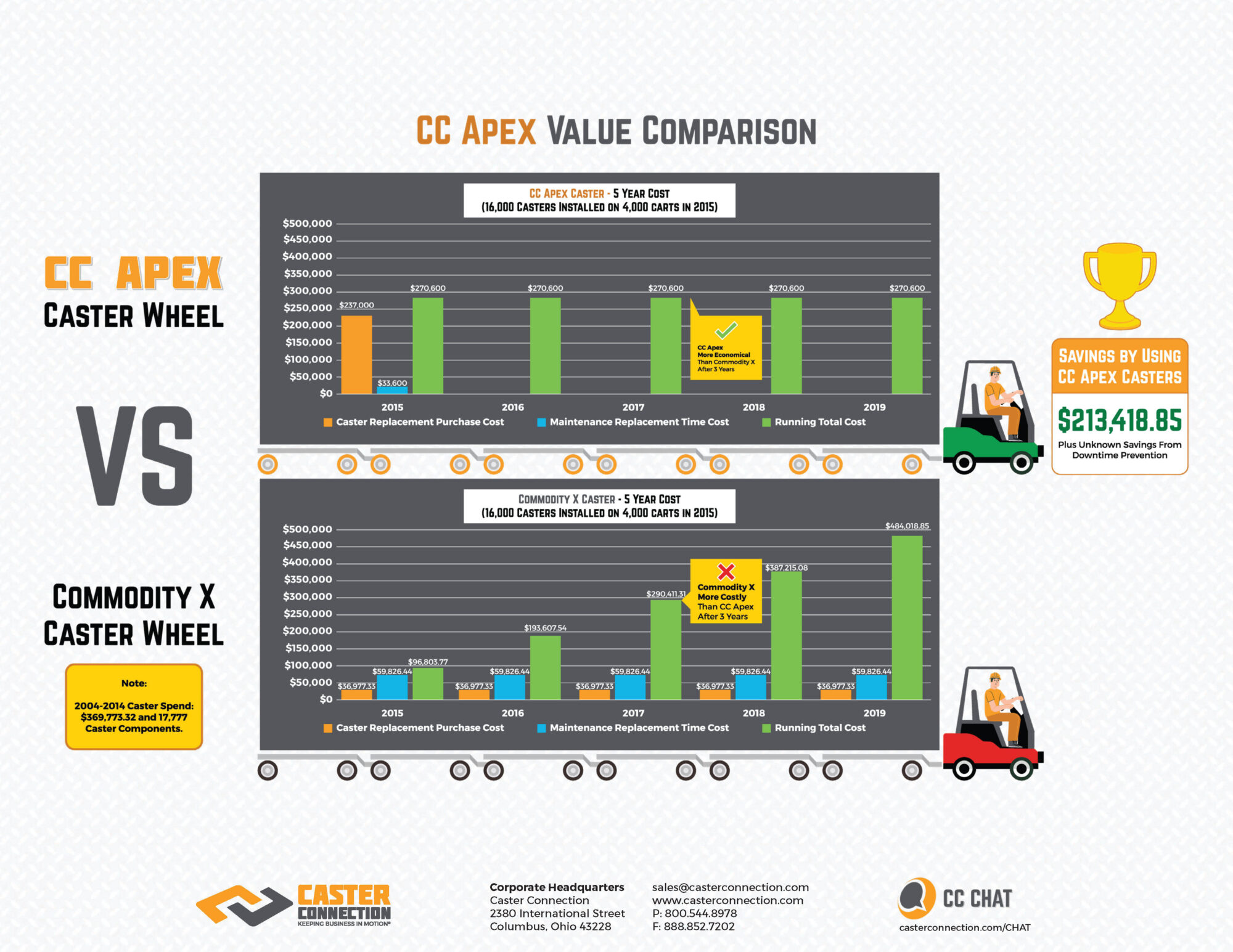