How to Build a Preventative Maintenance Plan for Your RV Factory
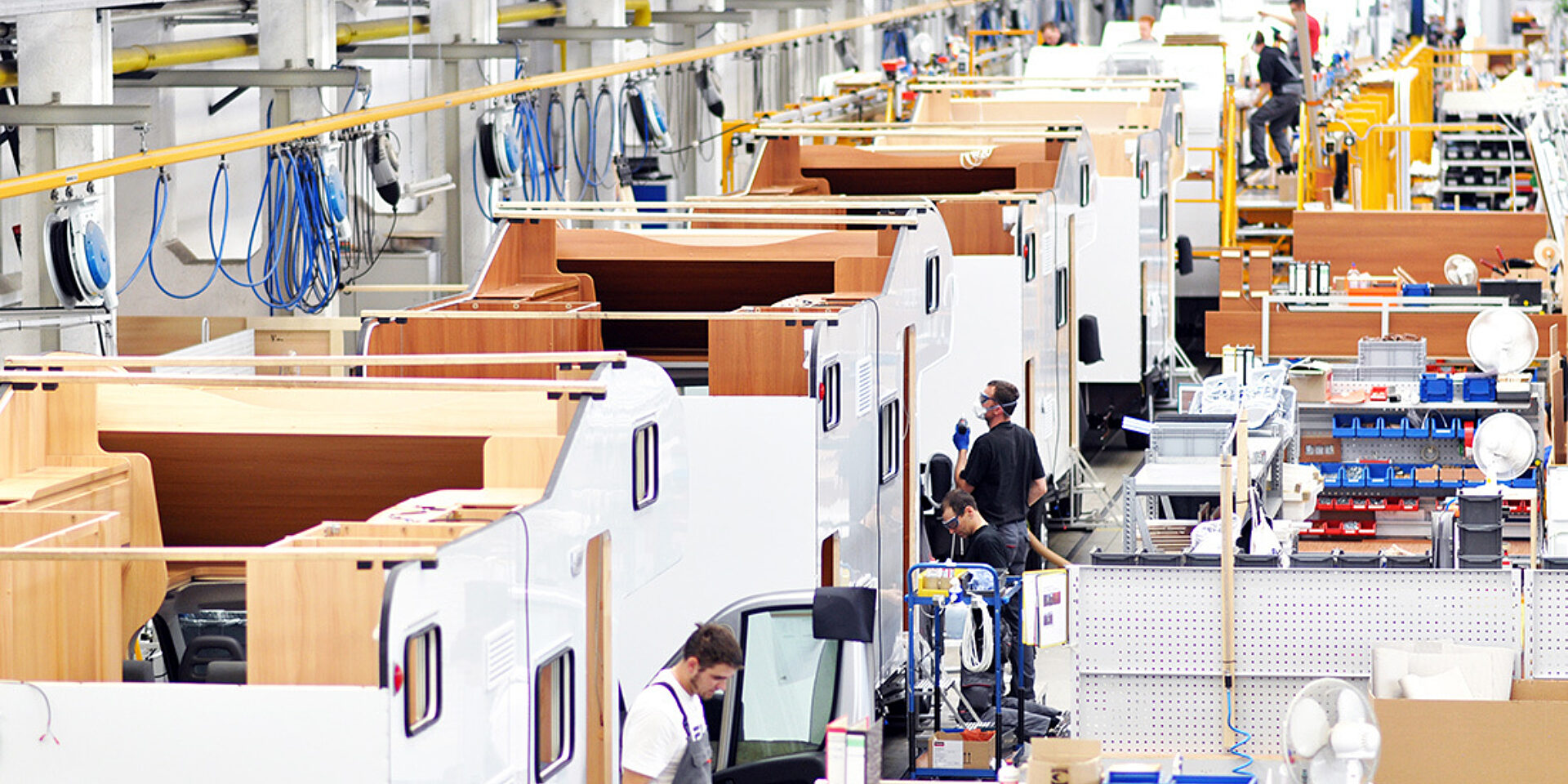
Downtime in RV manufacturing is more than an inconvenience. It can delay production schedules, disrupt workflows, and cost thousands of dollars in lost output. That’s why preventive maintenance is not just a checklist item; it is a critical strategy for keeping your facility safe, efficient, and productive.
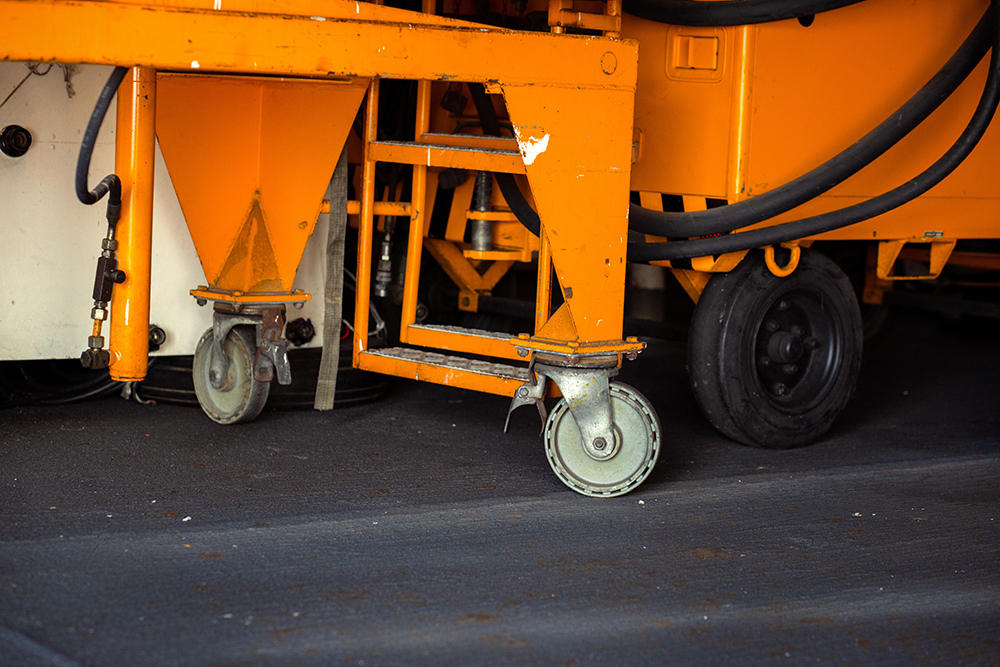
A well-structured maintenance plan helps extend the life of your equipment, reduce unplanned repairs, and support smoother daily operations. This guide outlines how to create a practical and effective plan that covers everything in your facility, from major equipment to the small but essential details like carts and casters.
Step 1: Identify and Prioritize Equipment
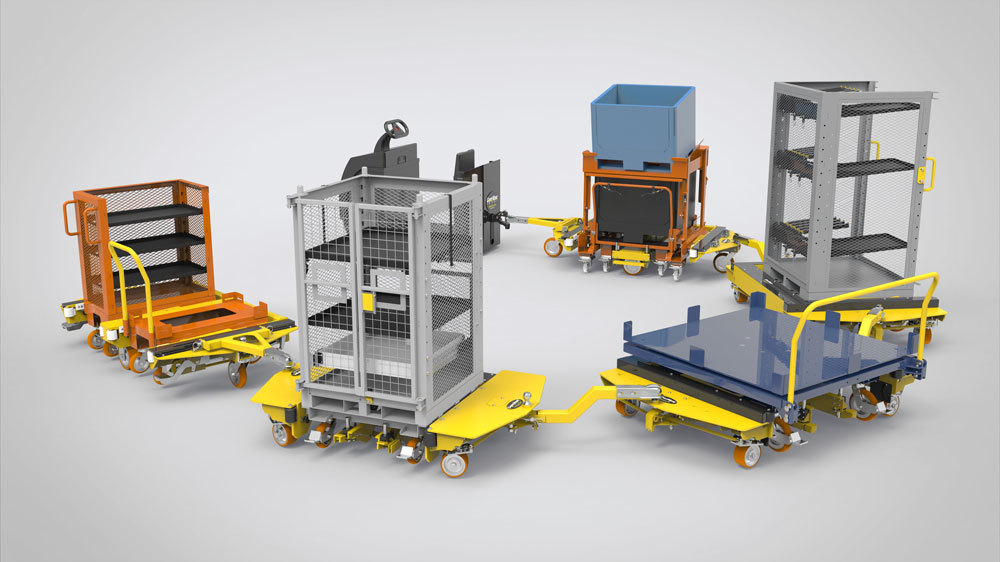
Begin by taking inventory of your equipment and dividing it into logical categories. For an RV manufacturing facility, these commonly include:
-
Weld bays and power tools
-
Conveyor systems and automated stations
-
Pneumatic tools and compressed air systems
-
Paint booths and curing areas
-
Lifting equipment such as hoists or assist arms
-
Ventilation, HVAC, and dust collection systems
Once you have a complete list, assign priority levels based on how critical each asset is to your operation. High-use equipment with potential safety or productivity impact should be inspected more often than less essential machinery.
Step 2: Establish a Routine Maintenance Schedule
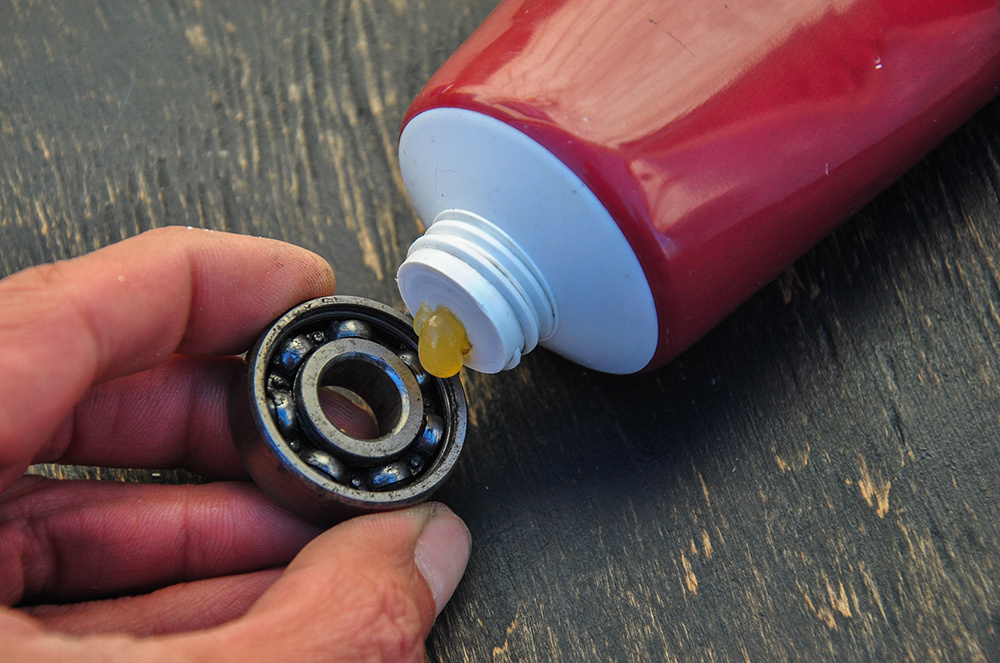
Create a service schedule that defines how often each piece of equipment should be inspected, cleaned, lubricated, or tested. Break the schedule into time-based intervals, such as:
-
Daily or weekly for basic visual checks, fluid levels, and air pressure readings
-
Monthly for deeper inspections, including caster condition, belt tension, brake function, and frame wear
-
Quarterly or semi-annual for more intensive tasks like filter replacements, bearing changes, alignment checks, and load testing
Assign responsibilities for each interval. In some cases, operators can handle routine checks, while skilled technicians perform scheduled servicing and replacements.
Step 3: Include Mobile Equipment and Carts
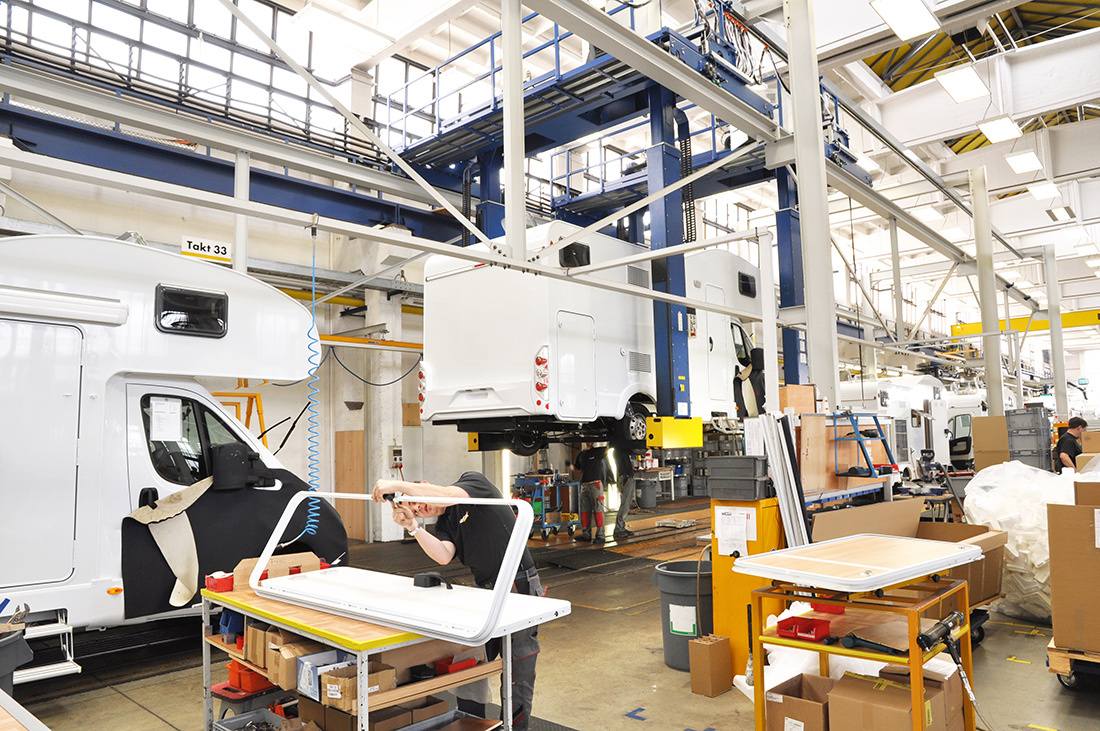
Mobile equipment is often overlooked in maintenance plans, but it can have a major impact on safety and productivity. Carts, racks, and mobile workstations move frequently throughout the facility and are subject to continuous wear from floor transitions, debris, and weight shifts.
Here are a few important items to inspect:
-
Casters for tread wear, flat spotting, cracked wheels, or loose rigs
-
Brakes and locks to ensure carts stay securely in place when needed
-
Welded frames and hardware for cracks, corrosion, or signs of fatigue
Caster failure is one of the most preventable causes of slowdowns on the floor. High-quality polyurethane casters, such as the CC Apex, CC Apex HD, or CC Stout HD from Caster Connection, can extend service life, reduce push/pull force, and help prevent costly floor damage. These products are ideal for RV plants that move heavy loads across varying surfaces.
Step 4: Track Maintenance Activity and Service History
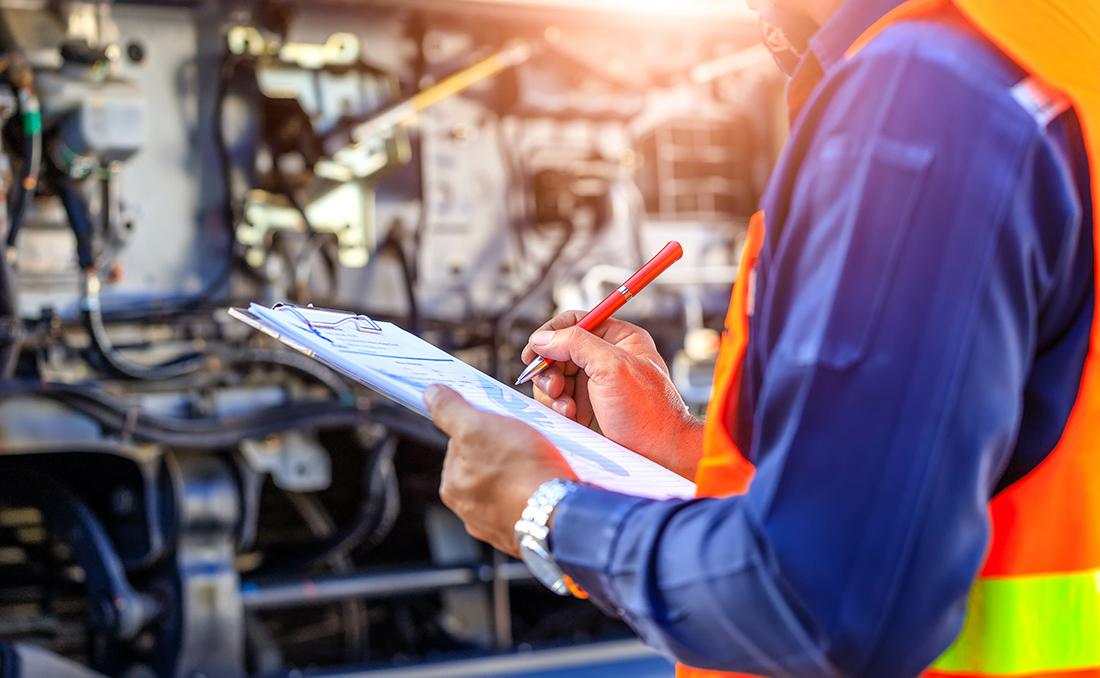
Without documentation, maintenance routines can be forgotten or duplicated. A simple tracking system can keep your plan on track and make audits easier. Your system should include:
-
Equipment name or ID
-
Date of last service
-
Summary of tasks completed or parts replaced
-
Technician name
-
Next scheduled check or service
Facilities with larger teams may benefit from a CMMS (computerized maintenance management system), which automates alerts and stores records digitally. This makes it easier to spot recurring failures or review compliance.
Step 5: Keep Spare Parts and Replacement Components in Stock
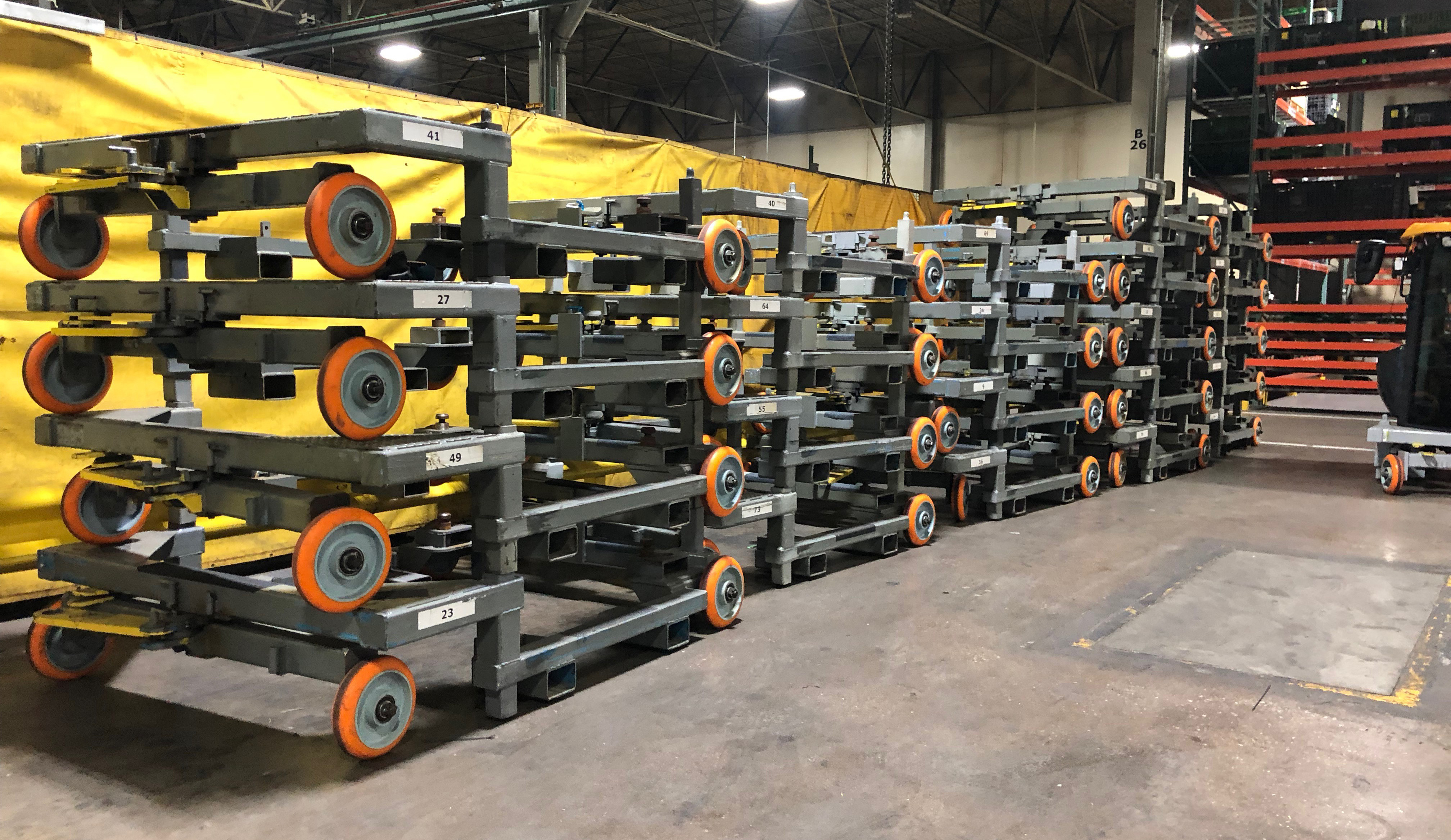
Preventive maintenance is more effective when you have the right parts on hand. Delays in replacement parts can turn a short repair into a multi-day issue. Keep a designated inventory of critical components, including:
-
Casters and wheels for carts and fixtures
-
Bearings, seals, and belts
-
Electrical fuses, sensors, and contactors
-
Lubricants and fasteners
-
Air hoses and quick-connect fittings
Caster Connection can help you standardize your caster inventory across departments and develop a stocking strategy. This helps reduce downtime and ensures fast turnaround when equipment needs attention.
A Plan That Pays for Itself
A preventive maintenance plan helps avoid emergencies, supports worker safety, and reduces long-term operating costs. When done consistently, it builds a stronger, more resilient production line and ensures your equipment is always ready for the job.
If carts or casters are part of your current challenges, Caster Connection can help. Our team provides detailed caster evaluations and tailored recommendations that match your workflow, load requirements, and facility layout.
Contact us today to schedule an Caster Needs Evaluation or build a stocking plan that supports your maintenance goals.
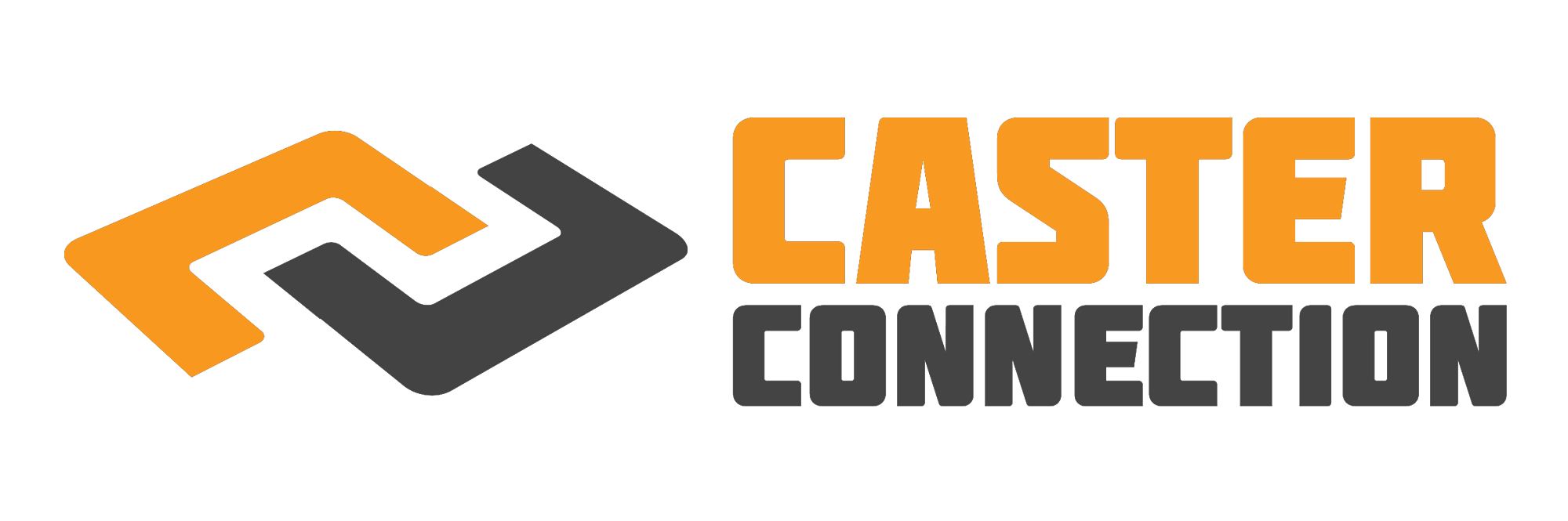