5 Ways Reliable Casters Help Minimize Downtime in Aerospace Manufacturing
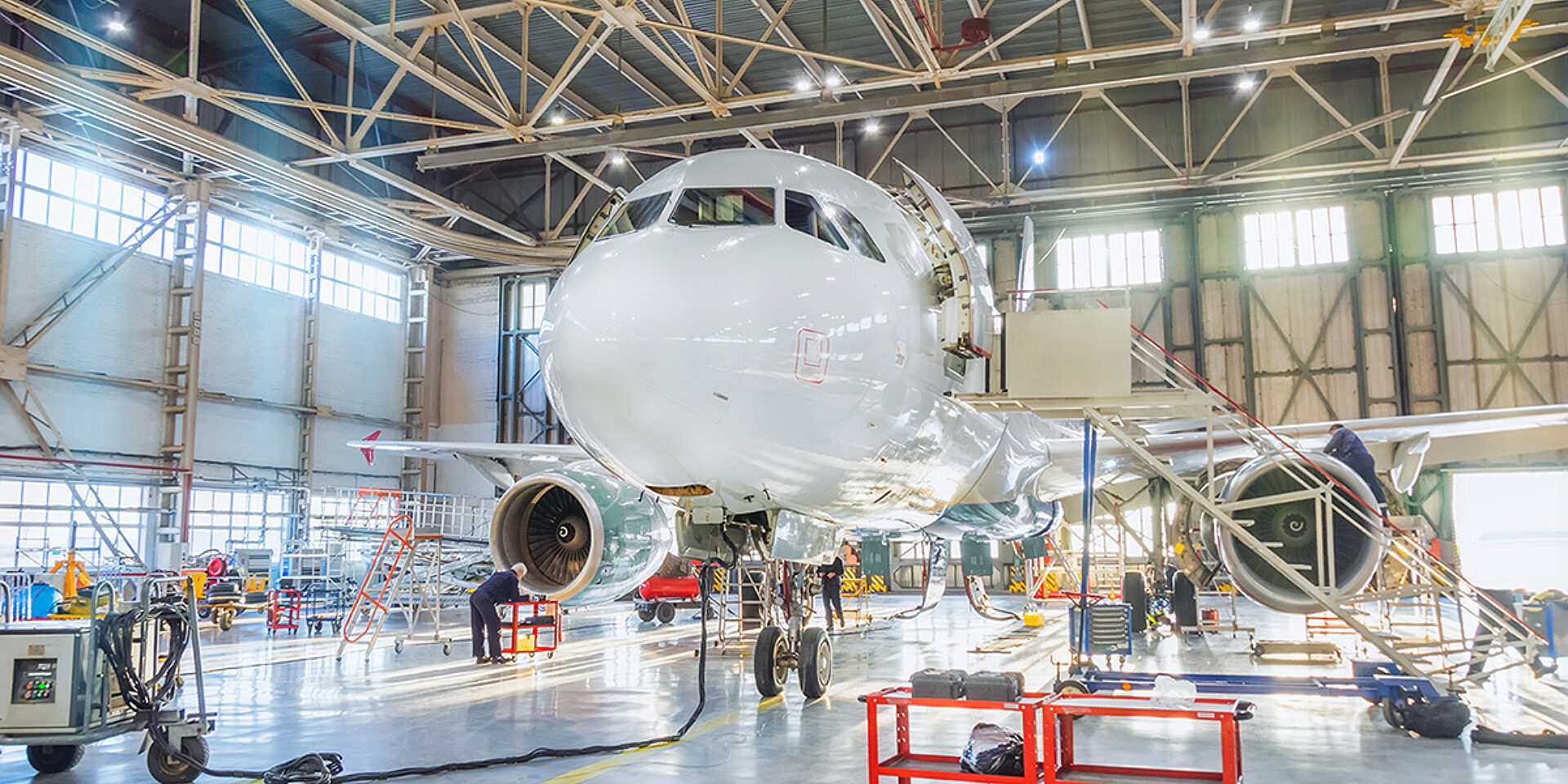
In aerospace manufacturing, where precision is key and workflow interruptions can be costly, the role of reliable casters often goes unnoticed. However, choosing the right casters is critical to minimizing downtime and keeping workflows running without error. Here are five actionable ways that reliable casters help reduce downtime in aerospace manufacturing environments.
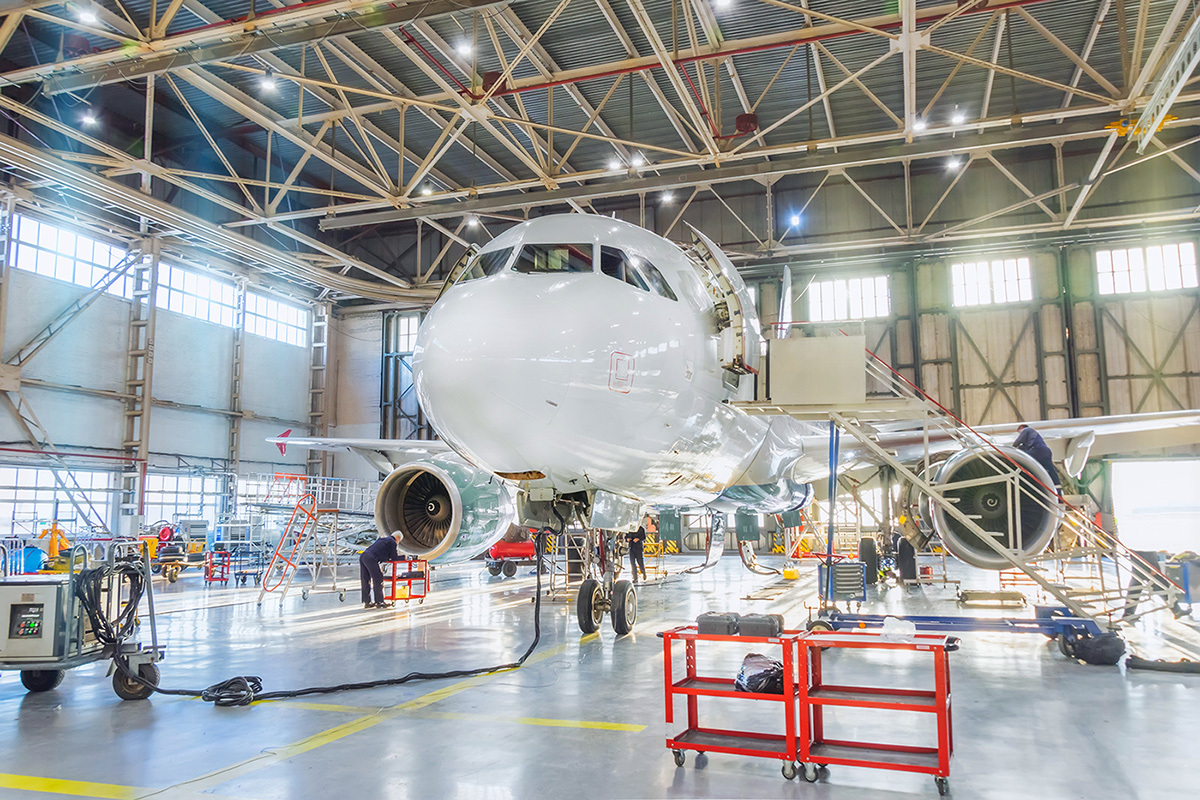
1. Maintaining High Standards in Cleanroom Environments
Subpar casters can leave behind debris or create unnecessary friction, leading to delays in critical cleanroom processes. High-quality casters are designed with non-marking materials that won’t shed particles, ensuring safe transfer of sensitive equipment. Investing in cleanroom-specific casters minimizes the need for frequent maintenance and cleaning, keeping your production line moving.
Actionable Tip
Opt for casters made of non-shedding, easy-to-clean materials to avoid contaminating cleanroom environments, which helps reduce downtime associated with repairs or equipment cleaning.

2. Load-Bearing Efficiency for Heavy-Duty Components
Aerospace manufacturing requires the transport of heavy machinery and components, and inferior casters can lead to load-bearing failures that halt operations. Heavy-duty casters built to withstand increased loads reduce the risk of breakdowns and ensure your equipment moves safely and efficiently without causing costly stoppages.
Actionable Tip
Ensure that casters are rated for the load capacity you need and regularly inspect them for signs of wear to avoid unexpected equipment failure.
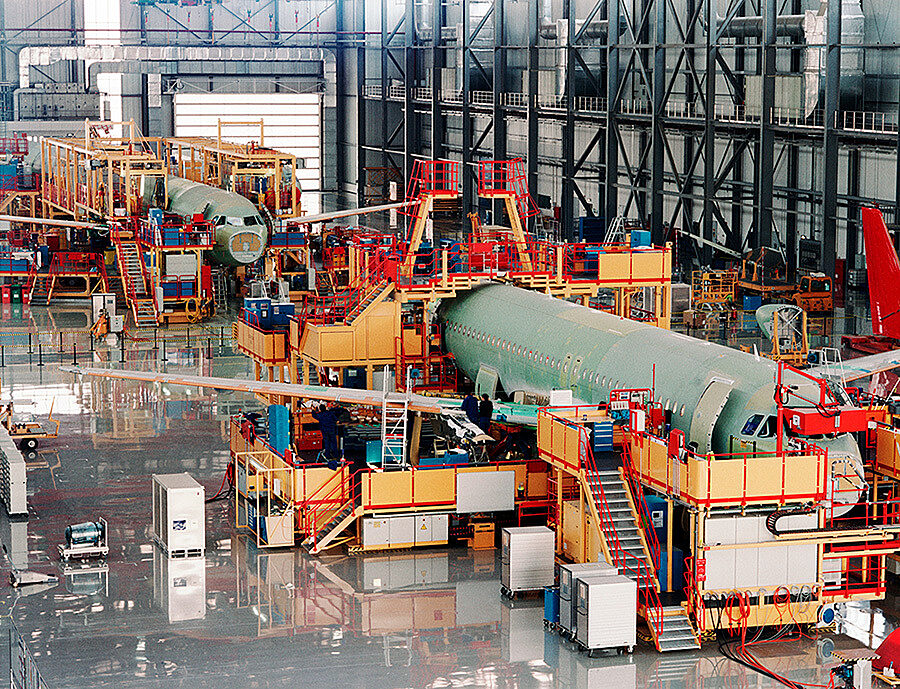
3. Reduced Maintenance With Longer-Lasting Materials
Casters made from inferior materials wear out quickly, requiring frequent replacement or repairs, which can lead to downtime. Investing in casters built with durable materials, such as polyurethane or rubber, increases longevity and minimizes the need for constant upkeep, allowing teams to stay focused on production.
Actionable Tip
Choose casters with abrasion-resistant treads that can withstand constant movement across different surfaces, reducing the need for frequent replacements and maintenance.
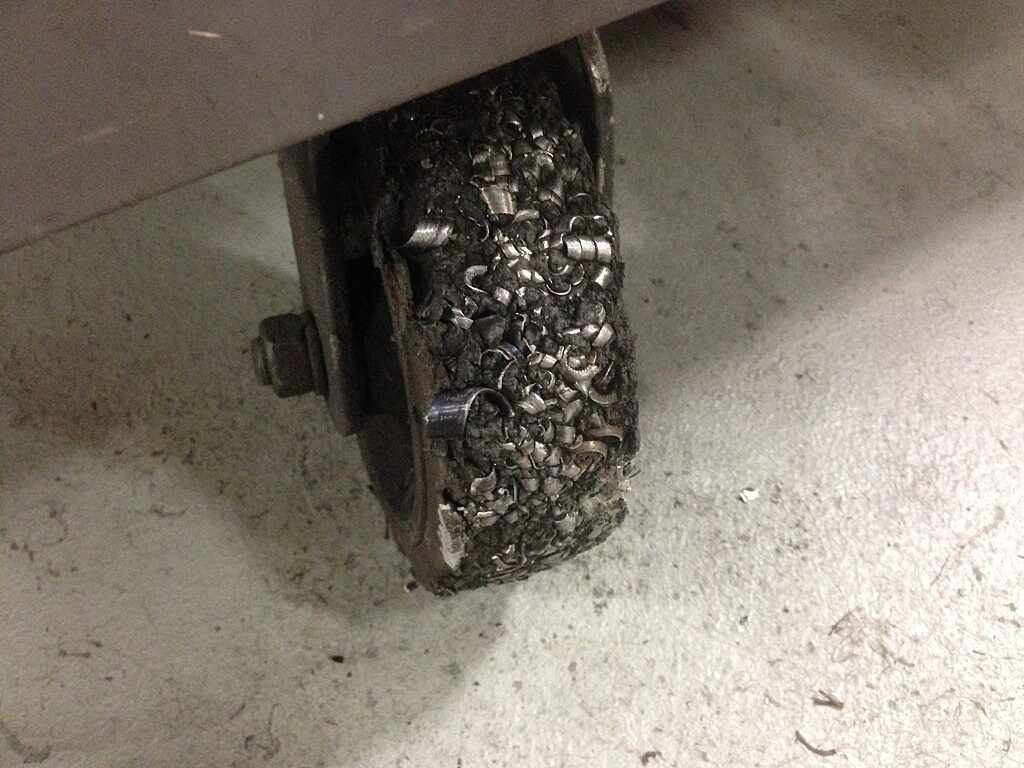
4. Ergonomic Design Prevents Operator Fatigue
In aerospace manufacturing, the ergonomics of your equipment directly impact worker productivity. Poor-quality casters often require excessive force to move equipment, leading to operator fatigue and slower production times. Rebound-resilient casters help reduce rolling resistance and prevent putting excessive strain on workers. This leaves production employees with more energy and higher morale, contributing to increased workflow efficiency.
Actionable Tip
Implement ergonomic casters that reduce push/pull force requirements, keeping workers energized and preventing unnecessary slowdowns in the production process.
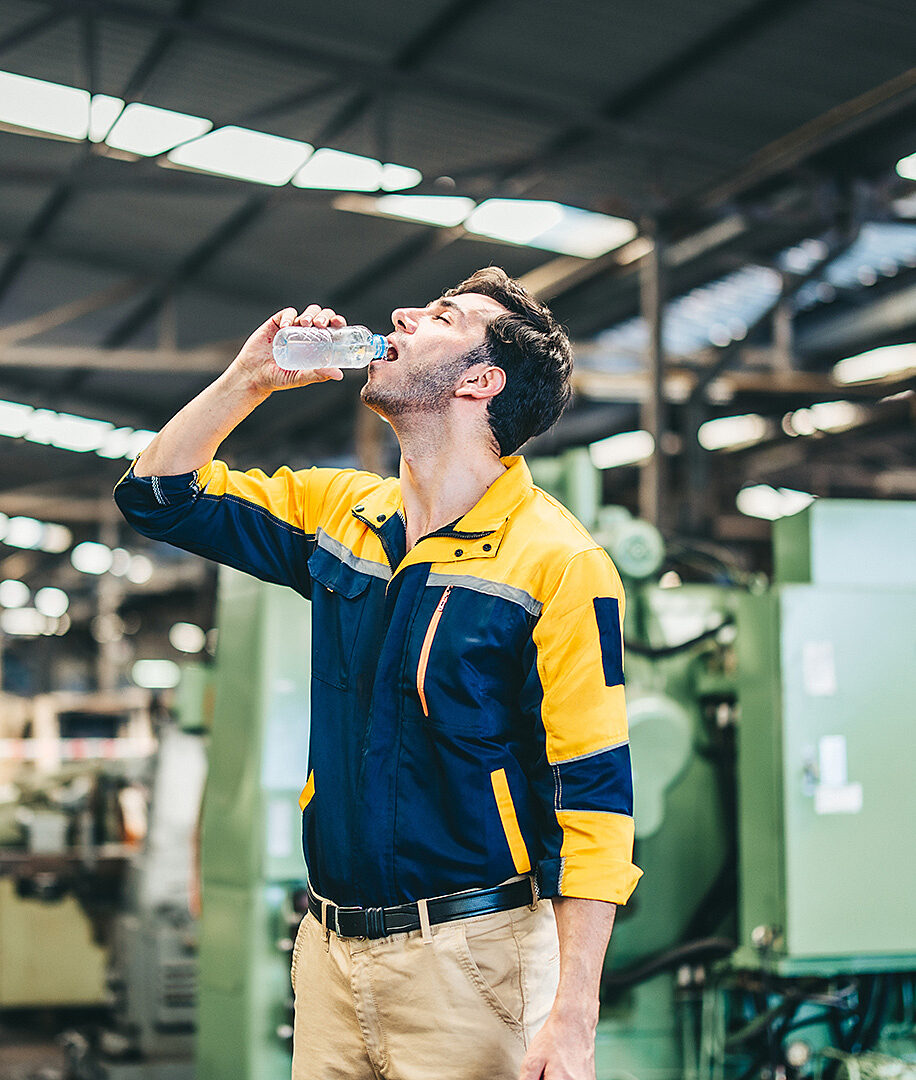
5. Increased Control for High-Accuracy Tasks
Many aerospace manufacturing tasks demand precise movement of equipment within tight spaces. Casters that don’t offer good swivel or directional control can lead to workflow interruptions and cause delays in high-accuracy operations. Reliable casters with high-quality swivel rigs allow for optimal maneuverability and easy navigation through tight spaces, preventing collisions or workflow disruptions.
Actionable Tip
Invest in casters with 360-degree swivel capabilities and precision steering to maintain the high accuracy required in aerospace manufacturing environments.
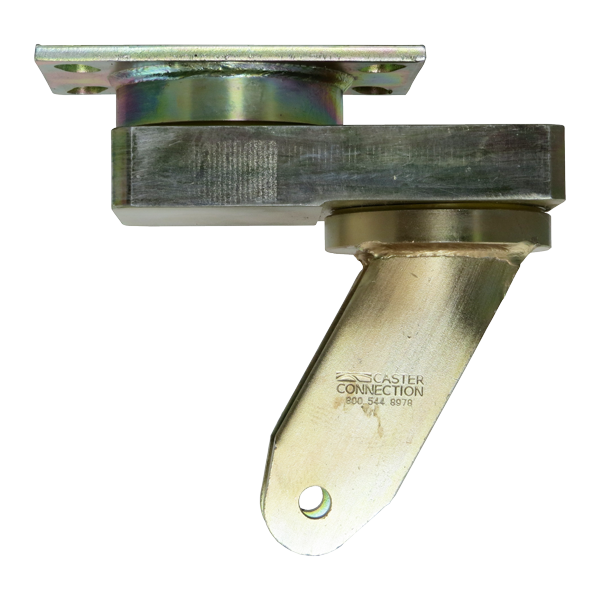
Shop Swivel Casters for Aerospace Manufacturing
6" CC Apex Kingpinless Swivel Caster
SKU: CC-2110-600200-40-T1
ALT-SKU: CCAPEX-6S-KP
-
- Overall Height
- 7-1/2"
- Wt. Capacity
- 1,000 lbs.
- Wheel Width
- 2"
- Wheel Diameter
- 6"
6" CC Peak Maintenance-Free Swivel CC Apex Caster
SKU: CC-3110-600200-40-T1
ALT-SKU: CCAPEX-6S-EMF
-
- Overall Height
- 7-1/2"
- Wt. Capacity
- 1,000 lbs.
- Wheel Width
- 2"
- Wheel Diameter
- 6"
6" CC Peak Maintenance-Free Swivel CC Apex Caster w/ Extended Swivel Lead
SKU: CC-3210-600200-40-T1
ALT-SKU: CCAPEX-6S-EMF-EXT
-
- Overall Height
- 7-1/2"
- Wt. Capacity
- 1,000 lbs.
- Wheel Width
- 2"
- Wheel Diameter
- 6"
6" Stainless Steel CC Apex Kingpinless Swivel Caster
SKU: DC-S510-600200-45-T1
ALT-SKU: CCAPEX-6S-SS-KP
-
- Overall Height
- 7-1/2"
- Wt. Capacity
- 1,000 lbs.
- Wheel Width
- 2"
- Wheel Diameter
- 6"
6" CC Apex ESD Kingpinless Swivel Caster w/ Built in Brake
SKU: CC-2111-600200-40-T1-BIB
ALT-SKU: CCAPEX-ESD-6S-KP-BIB
-
- Overall Height
- 7-1/2"
- Wt. Capacity
- 1,000 lbs.
- Wheel Width
- 2"
- Wheel Diameter
- 6"
8" CC Axis Dual-Swivel Maintenance-Free CC Apex ESD Caster
SKU: CC-7111-800200-40-T2
ALT-SKU: CCAPEX-ESD-8S-AXIS
-
- Overall Height
- 11-1/2"
- Wt. Capacity
- 1,200 lbs.
- Wheel Width
- 2"
- Wheel Diameter
- 8"
6" CC Apex ESD Dual-Wheel Kingpinless Swivel Caster
SKU: DC-D111-600200-40-T2
ALT-SKU: CCAPEX-ESD-6S-KP-DUAL-TP2-OH4
-
- Overall Height
- 8"
- Wt. Capacity
- 1,800 lbs.
- Wheel Width
- 2"
- Wheel Diameter
- 6"
8" CC Nexus Kingpinless Swivel Caster with Built-In Brake - 4" X 4-1/2" top plate
SKU: CC-2115-800200-40-T1-BIB
-
- Overall Height
- 9-1/2"
- Wt. Capacity
- 1,750 lbs.
- Wheel Width
- 2"
- Wheel Diameter
- 8"
8" CC Nexus Heavy Duty Kingpinless Swivel Caster - 4-1/2" X 6-1/4" top plate
SKU: CC-6115-800300-40-T2
-
- Overall Height
- 10-1/8"
- Wt. Capacity
- 2,625 lbs.
- Wheel Width
- 3"
- Wheel Diameter
- 8"
8" CC Nexus Kingpinless Outrigger-Style Swivel Caster - 4" X 4-1/2" top plate
SKU: CC-2315-800200-40-T1-RG
-
- Overall Height
- 10-1/8"
- Wt. Capacity
- 2,000 lbs.
- Wheel Width
- 2"
- Wheel Diameter
- 8"
6" Stainless Steel Thermoplastic Rubber Swivel Caster
SKU: 6-81SS-220GF
-
- Overall Height
- 7-1/2"
- Wt. Capacity
- 500 lbs.
- Wheel Width
- 2"
- Wheel Diameter
- 6"
Simplify Your Manufacturing Workflow With the Right Casters
Looking for a way to make material handling easier in your aerospace facility? Chat with us to talk mobility solutions, request a quote, or use our PartSolutions tool to access and download 3D and 2D CAD files of our casters and wheels.
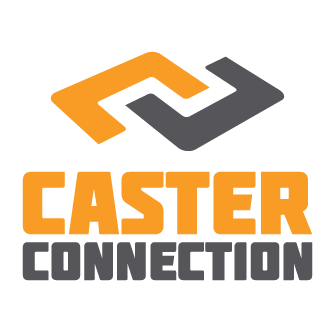