The Hidden Costs of Caster Failure On Construction Sites
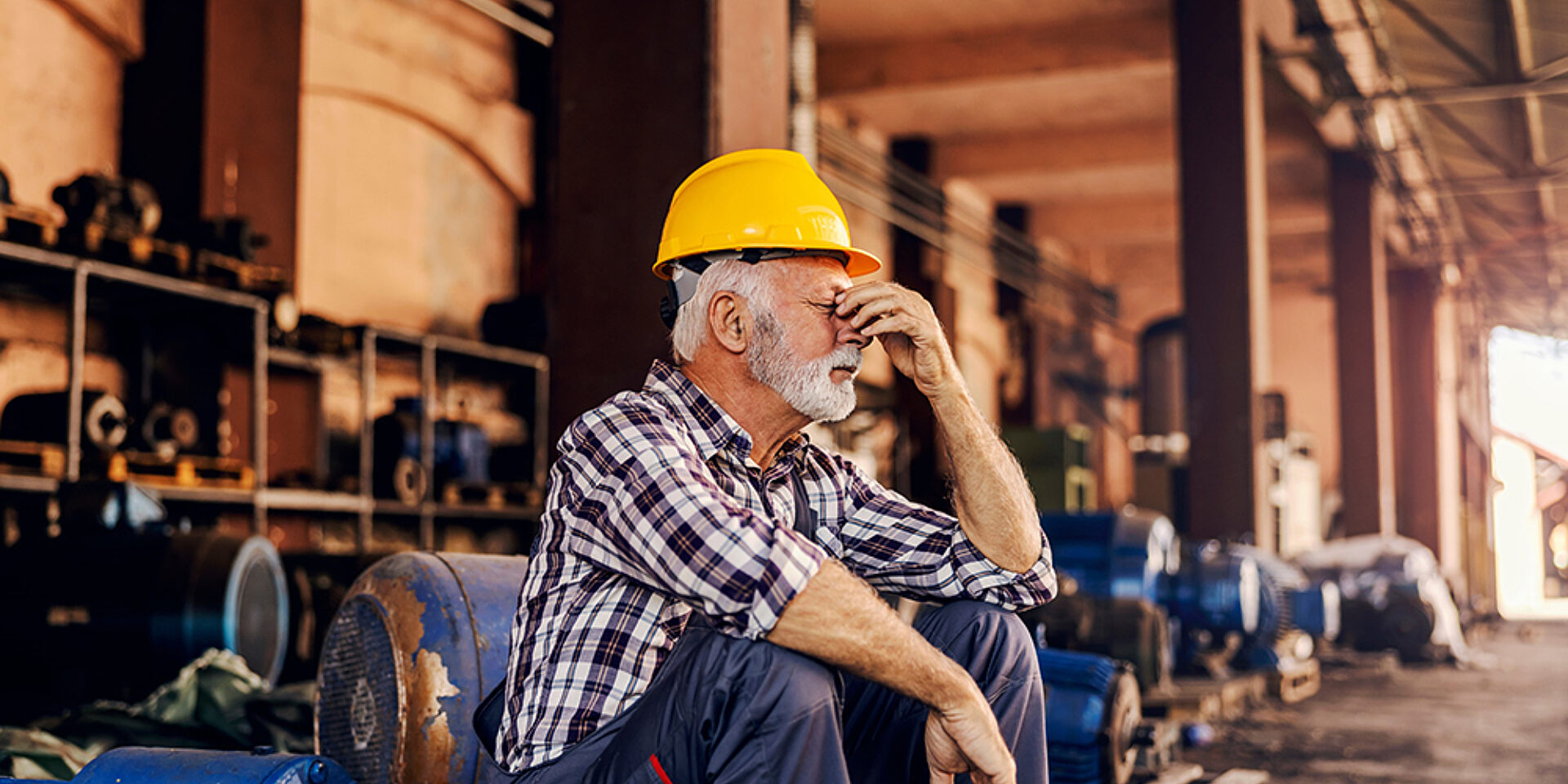
Every minute of construction downtime can cost hundreds, or even thousands, of dollars. In fact, studies show that downtime can average $300 to over $500 per minute in some sectors. With so much at stake, project managers, site supervisors, and procurement teams face mounting pressure to keep operations running smoothly and on schedule.
While much attention is often paid to big-ticket equipment and material costs, one small component is frequently overlooked: the caster. These humble wheels power the movement of materials, equipment, and structures across construction sites. When they fail, the consequences can be severe for both timelines and budgets.
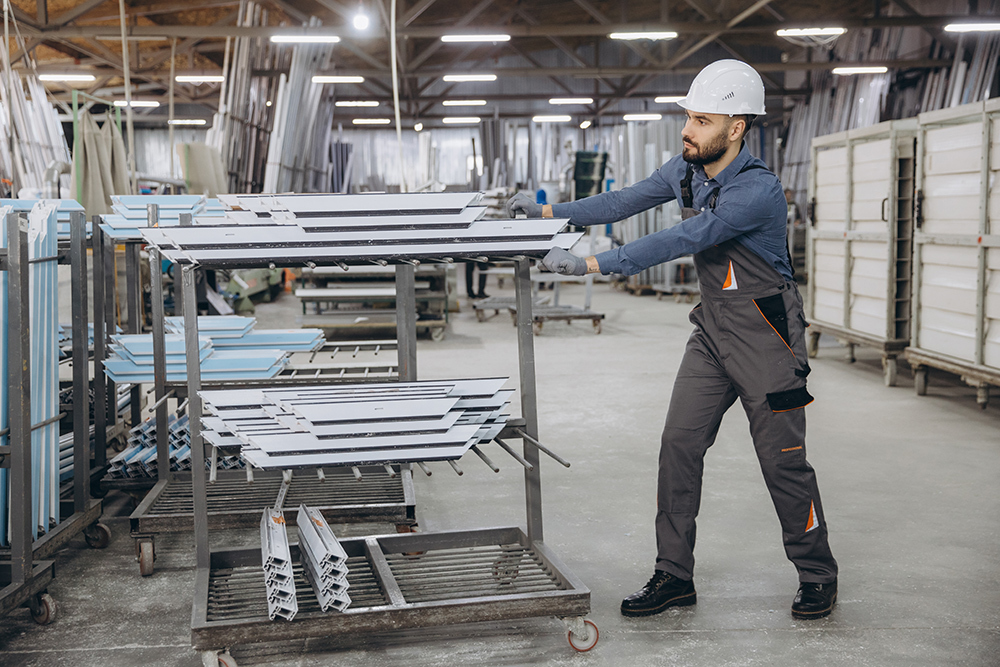
In this blog, we’ll explore the true cost of downtime, how high-quality casters help prevent it, and why a small investment in better mobility solutions can deliver a strong return.
The True Cost of Downtime in Construction
Downtime on a construction site drains resources, damages reputations, and threatens the success of the entire project. While some interruptions are unavoidable, many can be traced back to preventable issues. Understanding the full impact of downtime is the first step in creating a more resilient, efficient job site.
Downtime is Expensive
Downtime is more than an inconvenience. It is a costly risk that can derail even the best-planned projects. Some of the most significant hidden costs include:

Labor Costs
Crews waiting around still need to be paid, driving up labor budgets without any progress.

Equipment Rental Overruns
Delays extend the need for rented machinery, which can quickly escalate costs.

Delayed Project Penalties or Lost Incentives
Many contracts include penalties for late delivery or bonuses for early completion. These financial outcomes are lost when schedules slip.

Damage to Reputation and Future Opportunities
Repeated delays can hurt a company’s reputation, making it harder to win future bids.
Common Causes of Downtime
In the construction industry, time is money. When operations are interrupted, even briefly, the effects can ripple through the entire project. Downtime reduces productivity, drives up labor costs, and puts deadlines at risk. Some causes are easy to anticipate, while others, like overlooked equipment components, can catch teams off guard. Understanding these common sources of downtime is the first step toward preventing them.

Material Handling Delays
Projects slow down when materials are not delivered to the right place at the right time.

Equipment Failures
Small but essential components such as casters and wheels can fail under stress and bring work to a stop.

Injury-Related Work Stoppages
Injuries resulting from manual handling or faulty equipment can lead to complete shutdowns while teams address the incident.
The Hidden Cause of Construction Delays
In many cases, it is not the large equipment failures that cause the most disruption. Instead, it is the small, easily overlooked issues that bring work to a halt. A broken caster, for example, can immobilize scaffolding, delay the movement of materials, or damage expensive components during transport. These seemingly minor problems can create ripple effects that disrupt entire workflows and extend downtime far beyond the original incident. Addressing these hidden vulnerabilities is essential to maintaining job site efficiency.
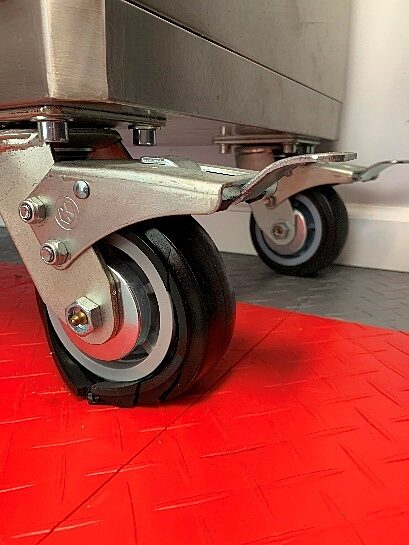
The Role of Casters in Construction Mobility
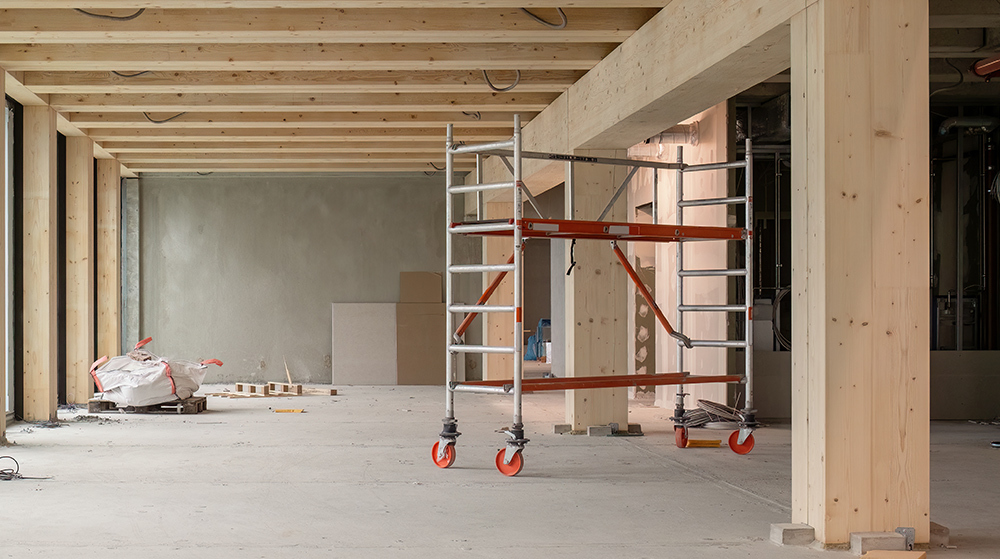
Casters play a vital role in keeping construction operations moving. They enable the safe, efficient transport of materials and support the mobility of key equipment throughout the job site. Their impact extends far beyond convenience—they directly influence productivity, safety, and cost control.
Casters support essential movement by:
-
Transporting heavy materials such as stone panels, concrete forms, prefabricated sections, and glass installations
-
Staging and repositioning mobile equipment including scaffolding, modular work platforms, and heavy-duty carts
When this movement is interrupted, job site efficiency drops, and delays begin to stack up.
When Casters Fail, Everything Slows Down
Even a single caster failure can create a domino effect that disrupts workflow. Materials may become stuck and inaccessible, slowing down staging and installation. Skilled workers are often pulled away from their tasks to troubleshoot or manually move equipment. At the same time, the risk of damaging fragile or high-value materials increases, which adds to the overall cost of the delay.

Why High-Quality Casters Matter
Investing in high-performance casters offers clear advantages for construction environments:

Superior Load Capacity
Quality casters can handle heavier loads without breaking down or compromising safety.

Resistance to Harsh Conditions
Durable designs withstand exposure to dust, debris, moisture, and rough terrain.

Longer Lifespan and Fewer Maintenance Needs
Fewer breakdowns and replacements reduce both downtime and operational costs.
Reliable casters help crews stay focused, protect valuable materials, and maintain steady progress across every phase of construction.
Why Caster Quality is a Smart Investment
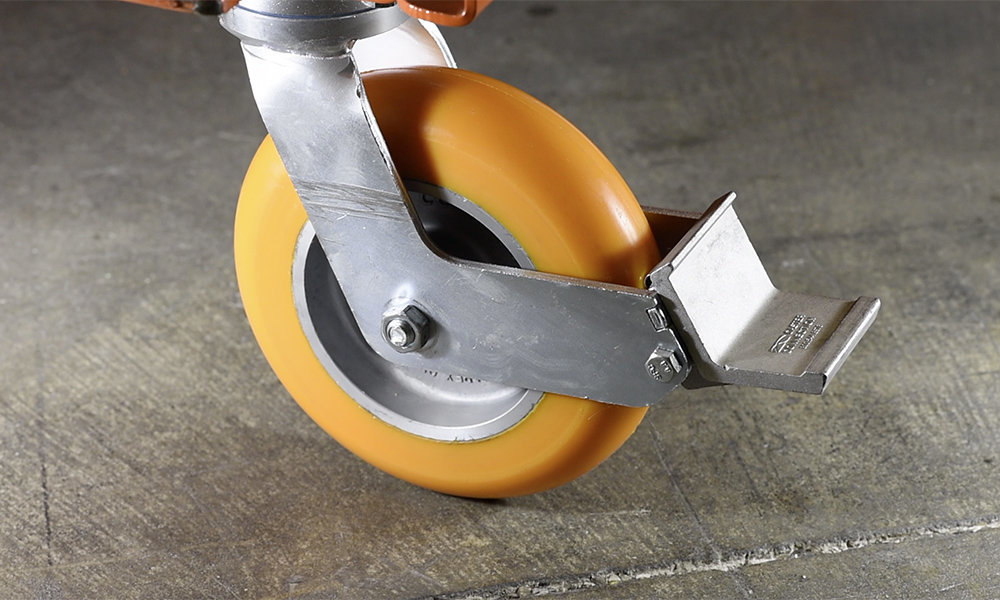
It can be tempting to cut costs on small components like casters, especially when managing a large construction budget. However, the true value of a caster should be measured not by its price tag, but by its performance over time. High-quality casters contribute to fewer delays, safer work conditions, and fewer maintenance demands. These benefits directly translate into financial savings and long-term gains for the entire project.
Upfront Cost vs. Lifecycle Value
Although premium casters may have a slightly higher initial cost, they deliver long-term value by:
-
Reducing the number of replacements needed
-
Minimizing downtime caused by equipment failures
-
Lowering ongoing maintenance expenses
-
Supporting consistent performance throughout multiple project phases
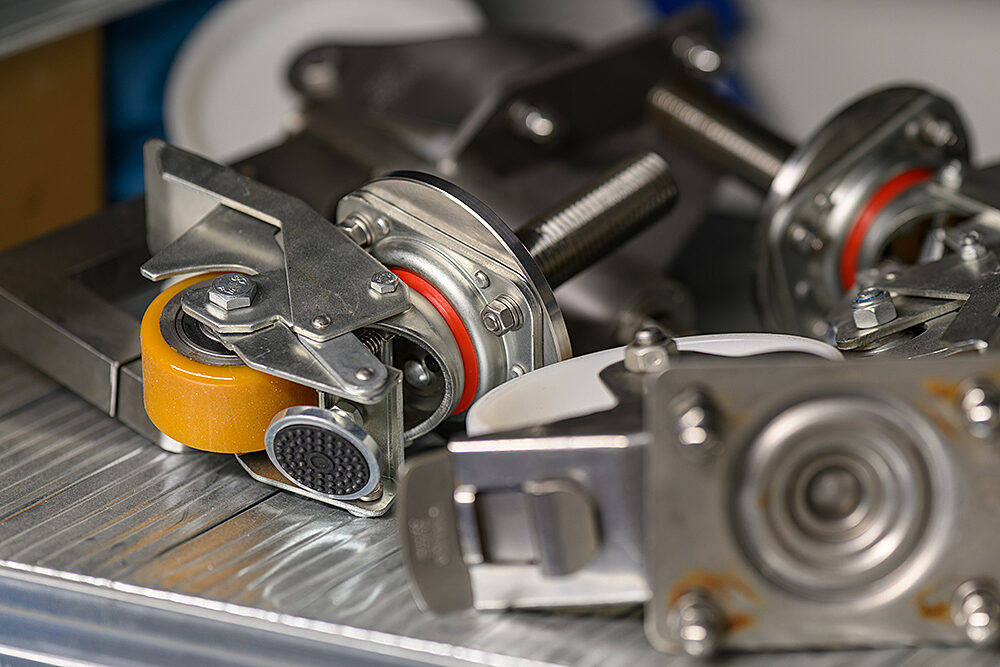
How A Single Caster Failure Can Cost Thousands
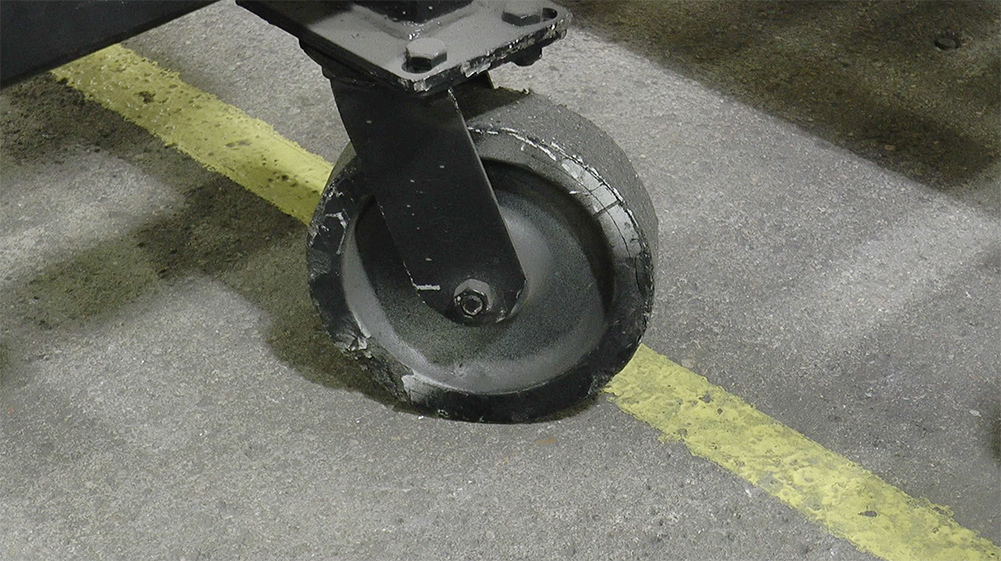
Consider a simple example. If a single caster failure halts the movement of scaffolding for just one hour, the costs can add up quickly:
-
A 10-person crew earning $50 per hour sits idle, resulting in $500 in lost labor
-
Equipment rental overages may add another $200 or more
-
Delays can disrupt multiple project timelines, leading to thousands of dollars in lost productivity
In comparison, investing a few hundred dollars more per unit in high-performance casters can help avoid these disruptions and save tens of thousands of dollars over the course of a project.
Additional ROI Factors
Beyond direct cost savings, high-quality casters contribute to:

Reduced Injury Claims
Ergonomic movement reduces strain and lowers the risk of worker injury, which helps decrease insurance and compensation costs.

Better Material Protection
Reliable casters help prevent damage to valuable items such as glass panels, stonework, or prefabricated units.

Improved Client Satisfaction
Fewer delays and smoother workflows lead to faster project completion and stronger relationships with clients.
What Features to Prioritize for Construction Success
Not every caster is built for the rigors of a construction site. Dust, debris, uneven surfaces, and heavy loads create a harsh environment where low-quality components can quickly fail. To ensure performance, safety, and longevity, it's essential to select casters designed specifically for construction demands. Focusing on the right features can make a significant difference in operational efficiency and cost control.
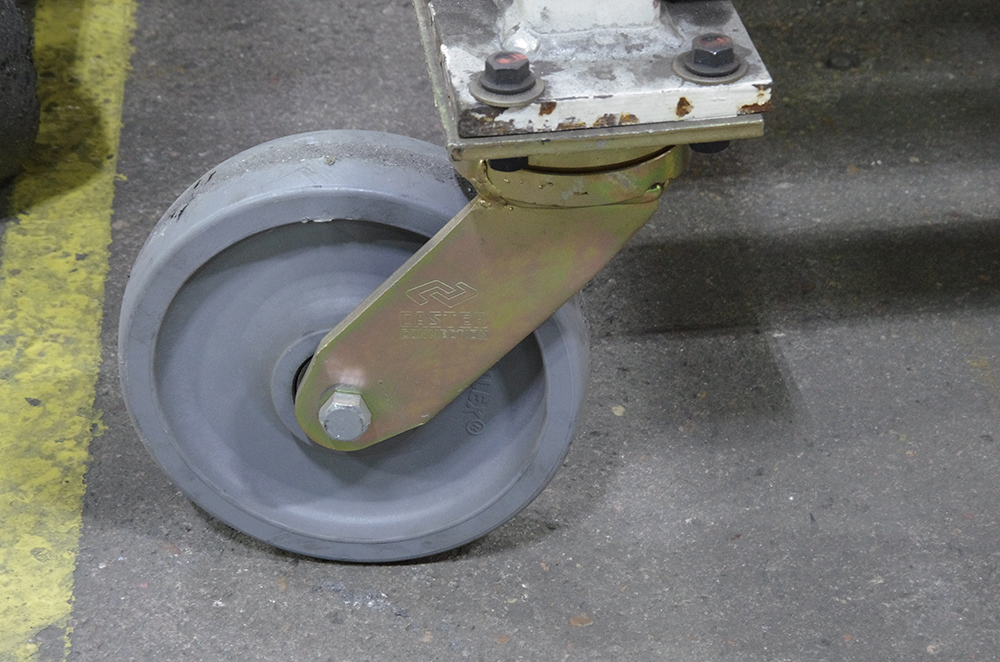
When evaluating caster options, prioritize the following:
-
Load Capacity and Stability: Casters must be rated for the maximum weight they will carry to prevent failure and maintain balance during movement.
-
Shock Absorption: Look for casters that can cushion vibrations and impacts to protect fragile or high-value materials during transport.
-
Corrosion and Weather Resistance: Outdoor and rugged job sites expose casters to moisture and debris, so choose materials that resist rust and deterioration.
-
Ease of Braking and Locking: Quick, reliable braking systems help secure mobile structures and improve job site safety.
-
Maintenance Simplicity: Select designs that allow for fast servicing, easy cleaning, and quick part replacement to minimize downtime.
-
Surface Adaptability: Wheels should roll smoothly over rough, uneven, or debris-covered surfaces to maintain mobility across varied terrain.
Quick Tip: Choosing heavy-duty polyurethane or steel wheels with sealed bearings can significantly increase caster longevity and performance in construction environments.
Real-World Results from Smarter Caster Selection
Improved caster performance translates directly into better job site efficiency, fewer delays, and stronger project outcomes.
One construction company specializing in prefabricated modular housing saw dramatic improvements after upgrading to CC Apex HD heavy-duty casters.
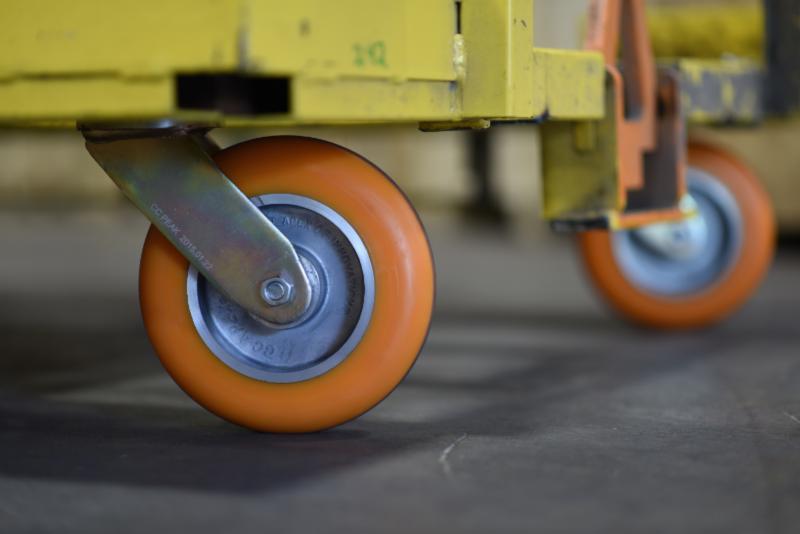
Before the switch, the company faced frequent slowdowns during material staging. Moving fragile prefabricated units was time-consuming, and the risk of damage during transport was high. After implementing the new caster solution, the firm reported a 30 percent reduction in downtime related to material handling.
The benefits were immediate. Staging processes became smoother and faster, fragile components arrived at their destination in better condition, and overall crew productivity improved—all without the need to increase labor.
This success highlights a key insight: quality casters do more than support weight. They support progress, reduce friction in daily operations, and help construction teams stay on schedule with less waste and fewer setbacks.
Casters Are Key
Downtime is a silent threat to construction profitability. Even the smallest delays can create pressure on budgets, extend timelines, and disrupt carefully planned workflows.
Casters, although often overlooked, play a critical role in maintaining safe, efficient, and reliable movement on the job site. Choosing high-quality caster solutions is not just about making equipment easier to move. It is a strategic decision that helps protect your schedule, your materials, your team, and your reputation.
If your goal is to keep projects moving forward without unnecessary setbacks, every detail matters. The right caster investment can help you stay on track, avoid costly disruptions, and finish strong.
Stop letting small failures cause big problems. Talk to a Caster Expert today and protect your project timeline.
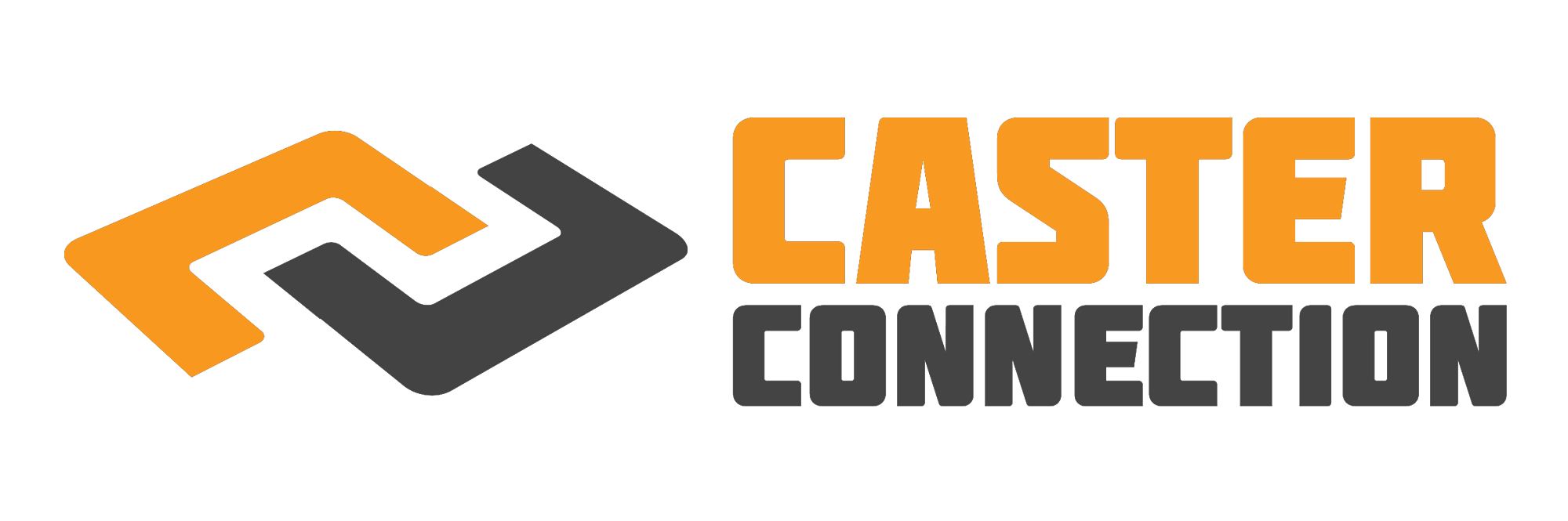