Caster Solutions for Concrete Manufacturing and Handling
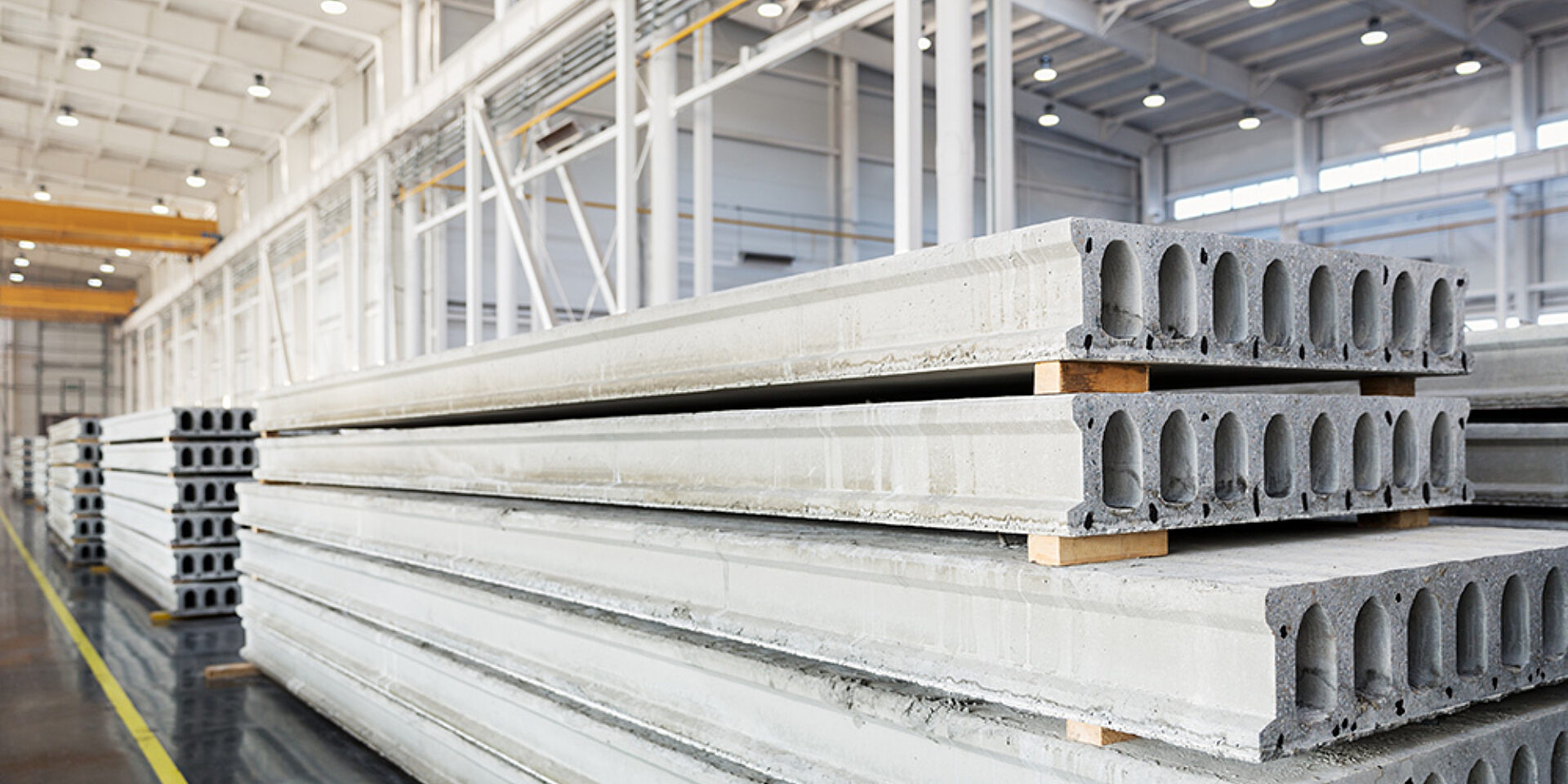
Concrete doesn’t wait. Once it’s mixed, the clock starts ticking. Forms must be poured, staged, cured, and moved—often in environments where dust chokes bearings, weight stresses every joint, and debris grinds down equipment.
So what keeps these brutal workflows moving?
Casters.
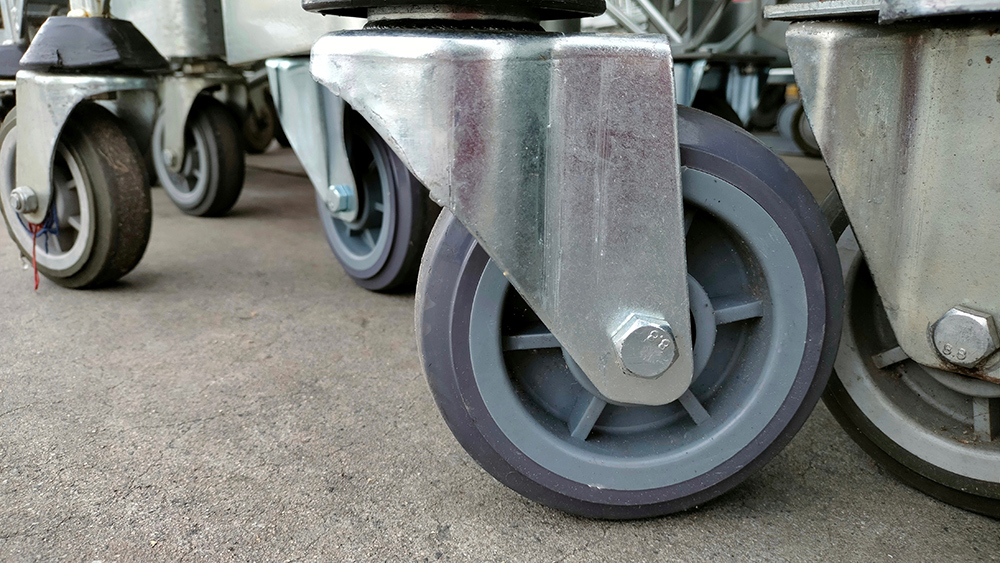
The right caster system can mean the difference between on-time delivery and dangerous delays. In concrete manufacturing and handling, you don’t just need mobility—you need mobility that’s built to survive.
Let’s break down how purpose-built casters help teams move fast, stay safe, and protect their investment in even the harshest conditions.
The Brutality of Concrete Environments
Concrete manufacturing isn’t just tough on people—it’s punishing on equipment. Every inch of the facility or job site is a potential hazard for caster systems: sharp debris underfoot, unforgiving loads, relentless motion, and constant exposure to water and corrosive chemicals. In these environments, average casters don’t stand a chance. To survive, your mobility solution has to be engineered for extremes.
Dust, Debris, and Damage
Concrete production is a war zone—for equipment, at least. Grit, crushed aggregate, and rebar offcuts coat the floor. That dust works its way into exposed bearings and soft treads, grinding down wheel performance and shortening lifespan.
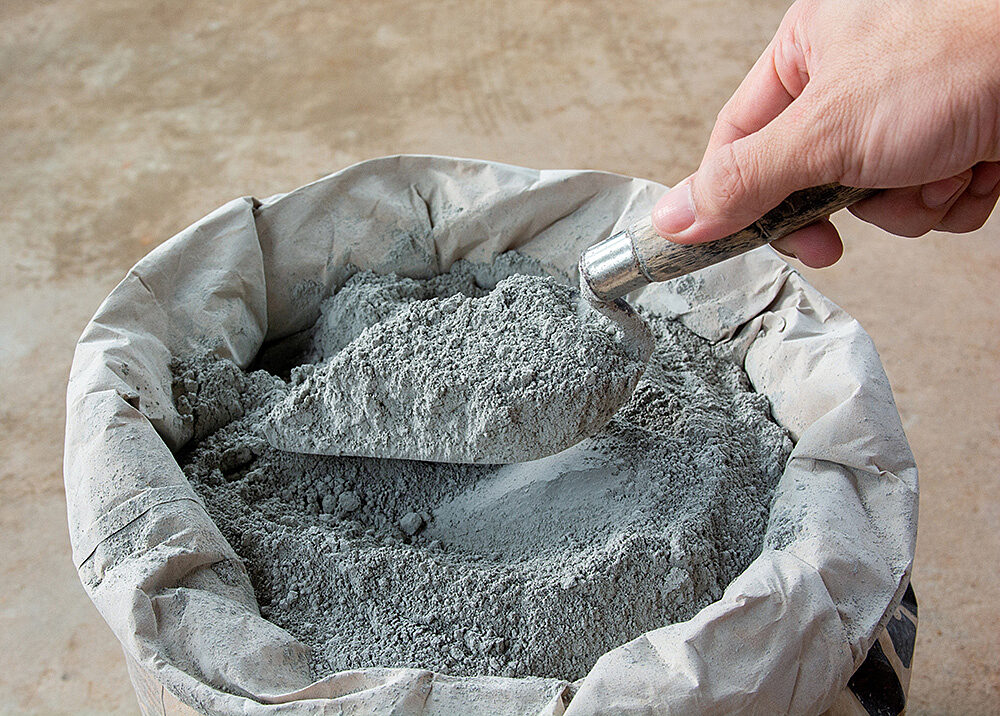
Extreme Weight
Even a small form filled with wet concrete can weigh hundreds of pounds. Precast slabs, wall panels, or barriers easily cross the 1,000+ lb. mark. If your casters can’t take that pressure, you’re headed for failure.
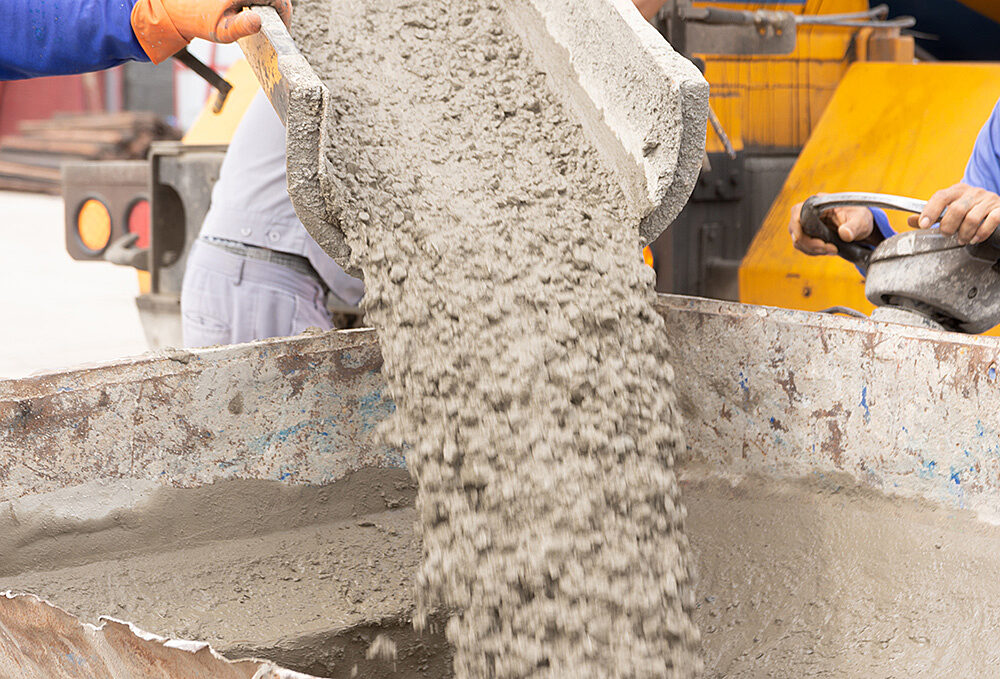
Repetitive Impact and Movement
Between staging, pouring, curing, and finishing, forms and slabs may be moved multiple times. The surface underneath may be cracked, uneven, or littered with debris. Each pass adds stress to the caster rig.
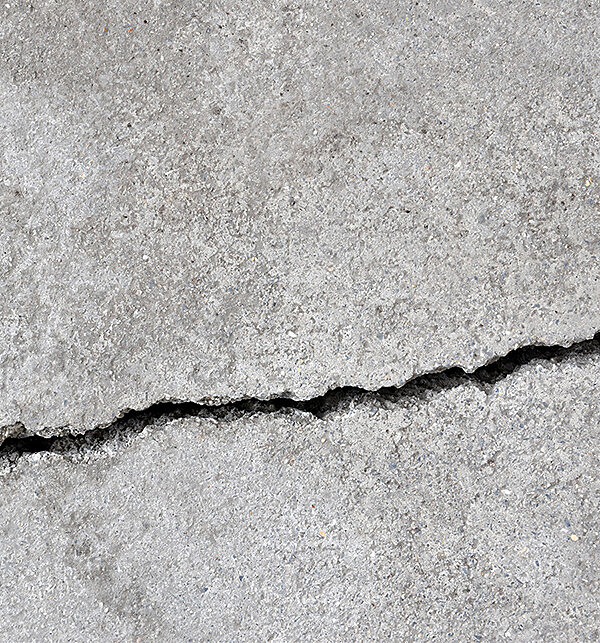
Moisture and Corrosive Exposure
Water, curing compounds, and jobsite chemicals increase wear on metals and rubber. If your caster isn’t sealed and protected, you’ll be replacing it long before the next job is done.
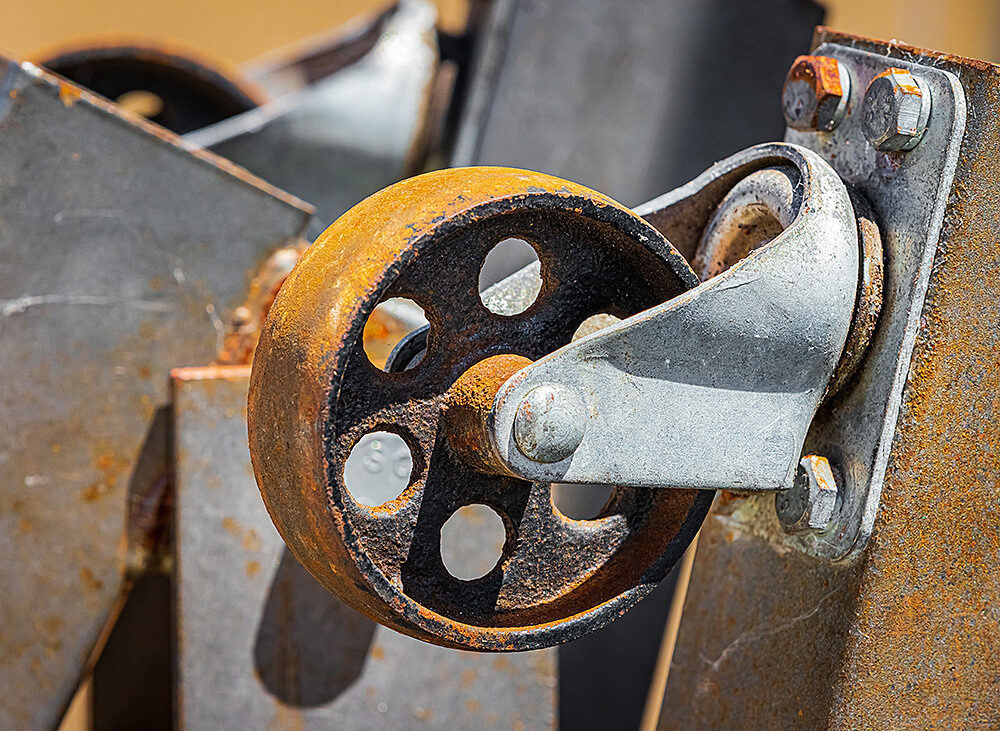
How Casters Power Concrete Production
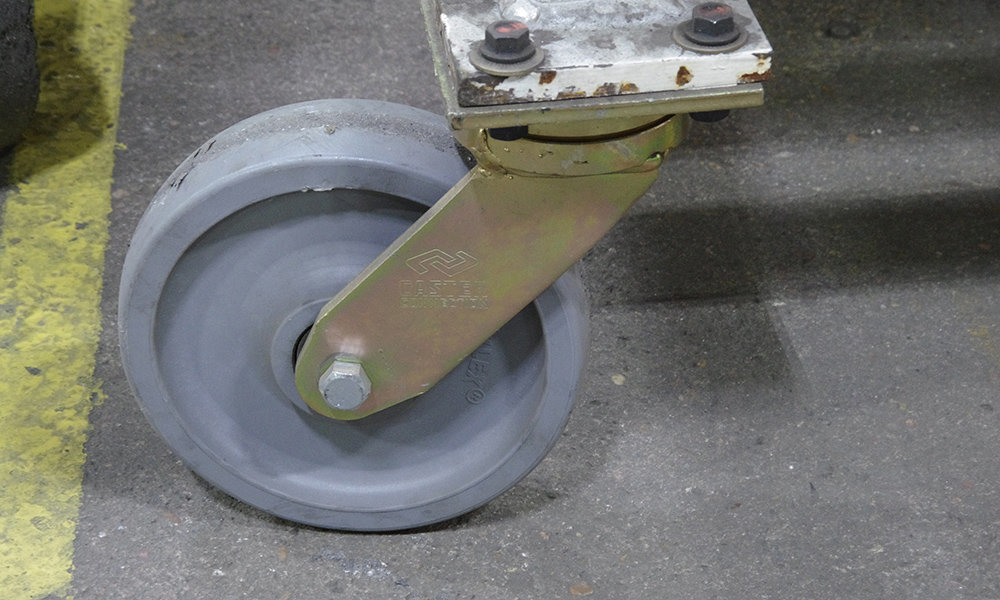
Mobility is mission critical in concrete production. Whether you're inside a precast facility or out on the job site, the ability to move forms, molds, and panels safely and efficiently can make or break your schedule. Casters turn heavy, rigid equipment into agile, responsive tools. They help eliminate bottlenecks, reduce physical strain, and keep workflows on pace from the first pour to the final install.
In the Precast Facility
Heavy-duty casters transform mold carts, tilt tables, and staging racks into mobile, flexible stations:
-
No need for forklifts at every turn
-
Smoother workflow with fewer equipment breakdowns
Workers move forms efficiently between batching, pouring, curing, and finishing zones—cutting downtime and increasing safety.
On the Job Site
For slab and panel movement during install:
-
Casters navigate uneven terrain
-
Allow precise alignment with crane lifts
-
Enable staging for inspection and touch-ups
The result: improved speed and control in environments where every minute counts.
Caster Features That Survive Concrete's Toughest Demands
Not all casters are built for the chaos of concrete work. To perform in environments filled with weight, grit, moisture, and movement, caster systems must combine strength, durability, and intelligent design. The right features not only keep equipment rolling but also prevent failures that lead to delays, injuries, or damaged product. Here are the essential qualities that set high-performance casters apart in concrete manufacturing and handling.
1. Heavy-Duty Load Ratings
Don’t gamble with under-rated wheels. Casters for concrete work must handle multi-ton loads without cracking, flattening, or shifting under stress. Forged rigs and reinforced plates are your best friend here.
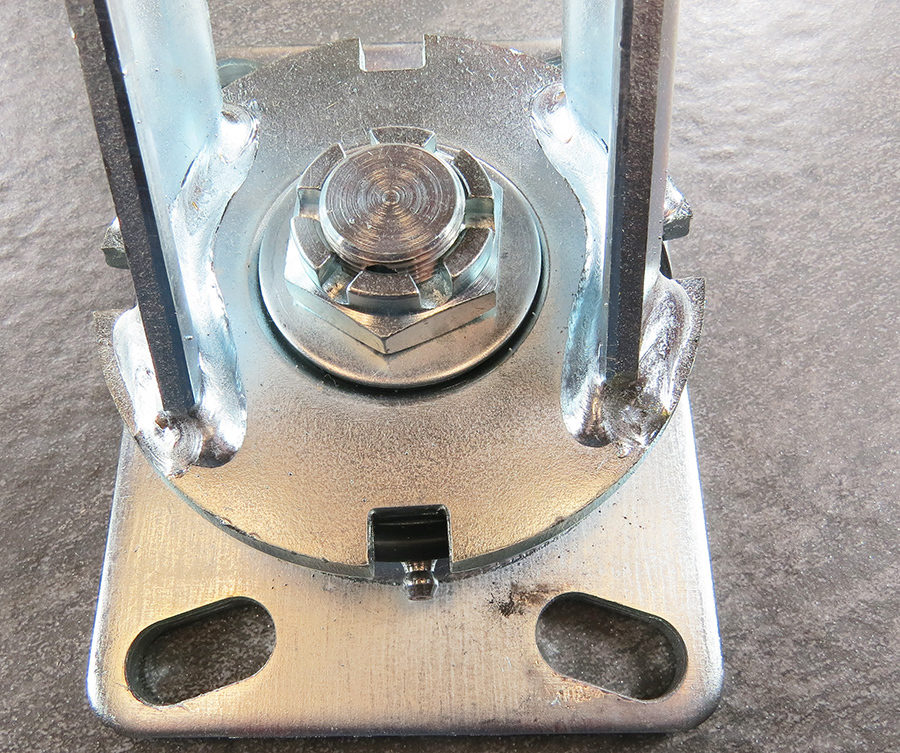
2. Abrasion-Resistant Treads
Standard rubber wheels wear fast on rough surfaces. Look for polyurethane or high-performance elastomer treads that can survive grit, steel rebar, and broken concrete underfoot.
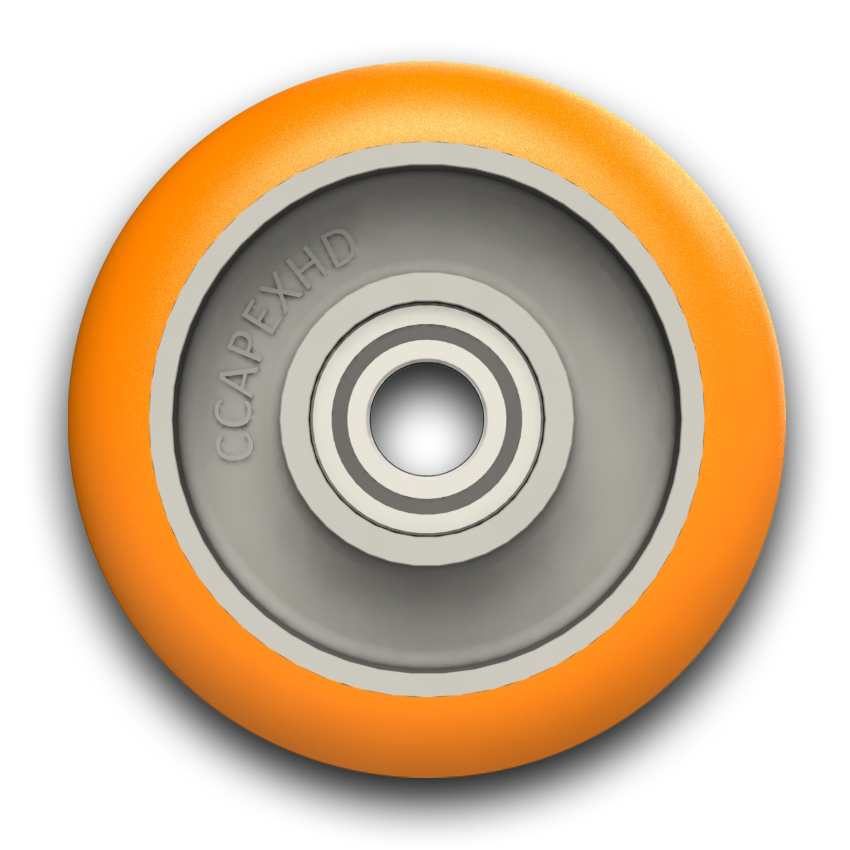
3. Sealed Bearings and Enclosed Rigs
Dust kills bearings. A sealed design protects internal movement mechanisms, reducing maintenance and dramatically extending caster life.
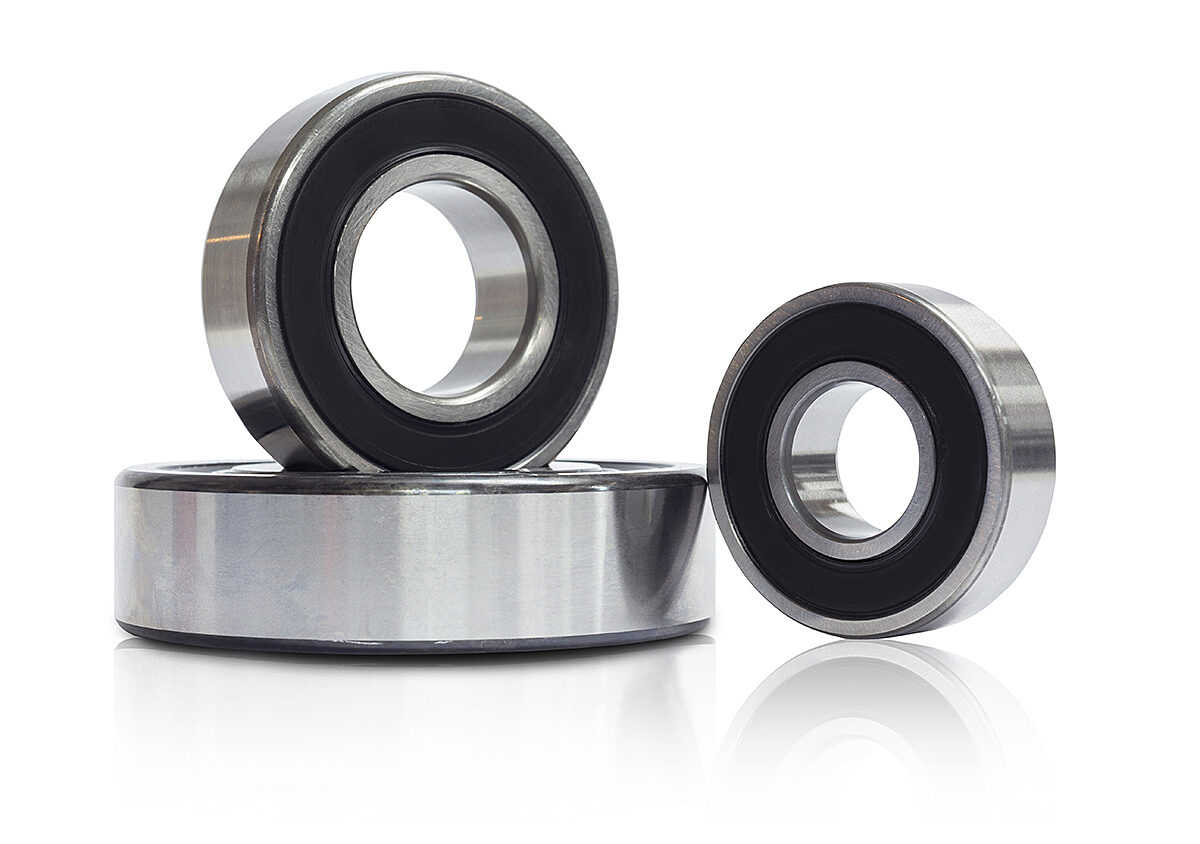
4. Corrosion-Resistant Materials
Zinc-plated, powder-coated, or stainless steel options prevent breakdown from wet curing areas, outdoor sites, or chemical exposure.
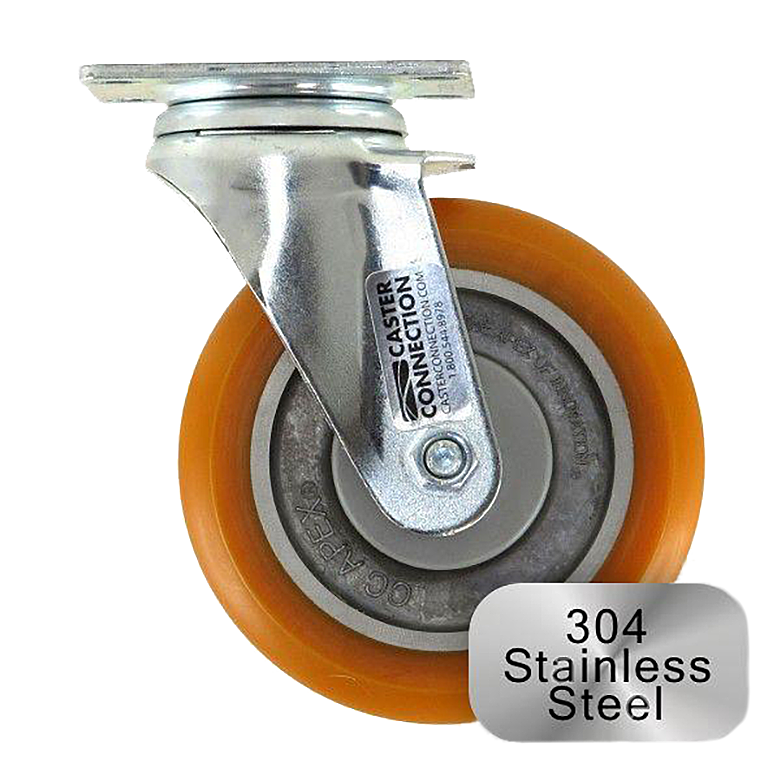
5. Shock and Vibration Dampening
Fresh pours are sensitive. Curing slabs are brittle. Shock-absorbing casters reduce cracks and protect panel integrity, which is especially important when staging finished surfaces for inspection or install.
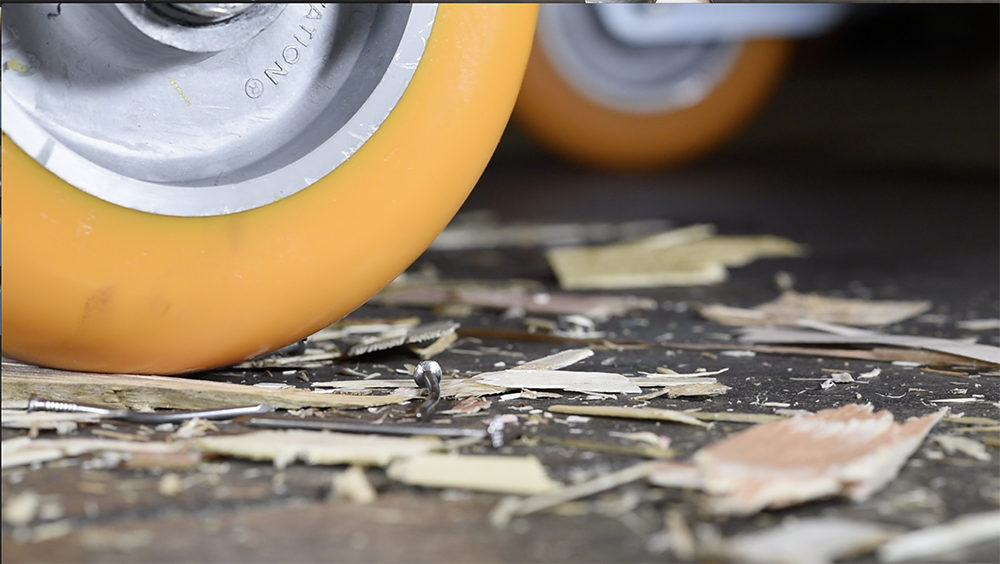
Braking and Stability Under Pressure
Concrete doesn’t just need to move. It also needs to stay still when it counts. A shifting mold, rolling slab cart, or runaway panel platform can ruin a pour or injure a worker.
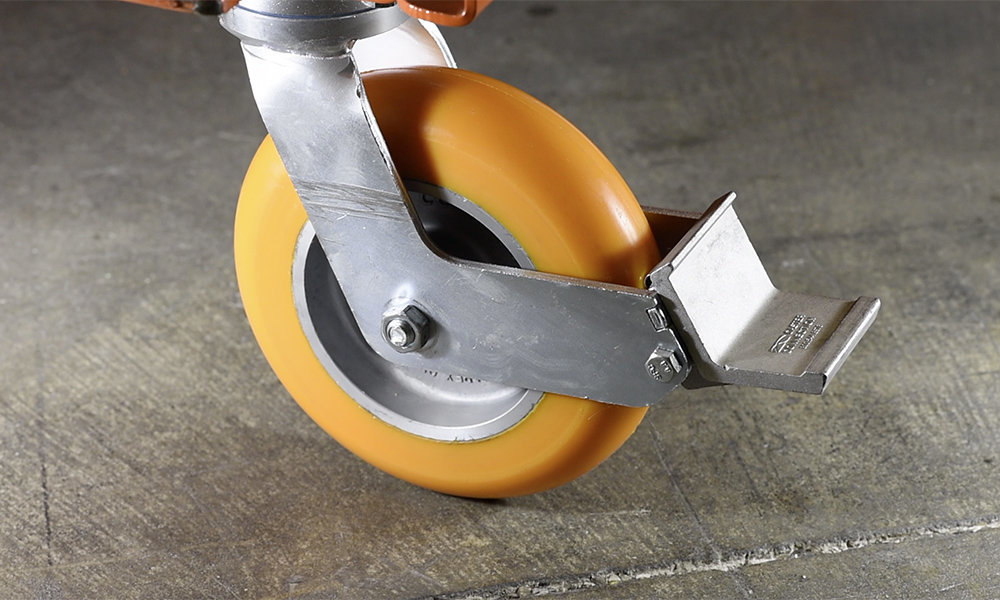
Here’s how the right brakes make the difference:
-
Total-Lock Brakes
Lock both the wheel and the swivel with one mechanism. These are ideal for slab carts or staging racks that must remain stationary under load, even on uneven surfaces. -
Floor Locks
Create firm ground contact to stabilize mobile platforms during pouring, curing, or inspection. These are essential in areas where movement is not acceptable, even if it's minimal. -
Deadman Brakes
Automatically engage when a cart or structure is unattended. These fail-safe systems prevent rollaways if a worker lets go during transport.
In a high-pressure environment, braking systems are not optional features. They are essential safety tools.
What to Look for in Casters for Concrete Applications
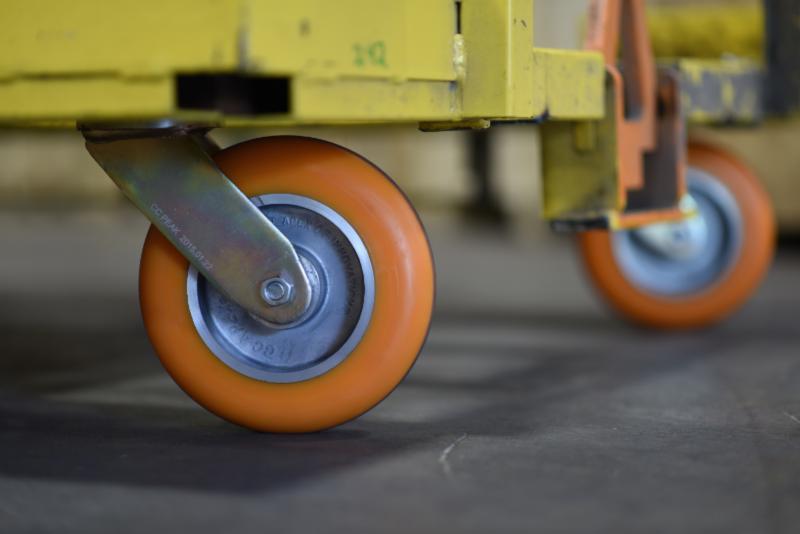
Choosing the right caster isn't just about mobility. It’s about protecting workers, maintaining productivity, and ensuring that your equipment survives the demands of concrete work. Whether you're managing a precast facility or overseeing on-site installations, your caster selection can make a significant impact on efficiency and safety.
Here’s a quick checklist for concrete producers, prefab operators, and site supervisors:
- Load rating that exceeds your heaviest filled forms or slabs
-
Abrasion-resistant tread that can withstand concrete grit and debris
-
Sealed bearings and enclosed rigs to block dust and extend lifespan
-
Corrosion protection such as zinc plating, powder coating, or stainless steel
-
Shock absorption to protect delicate or curing slabs
-
Reliable braking options including total-lock, floor lock, and deadman brakes
-
Large wheel diameter to handle uneven or debris-covered surfaces
Real-World Example: Durability That Delivers
A precast concrete plant specializing in tilt-wall panels and highway barriers was experiencing constant caster failures. Wheels were jamming, bearings were seizing, and carts were dragging across the floor. The resulting downtime was cutting into production, and slabs were being damaged before they could be shipped.
After upgrading to heavy-duty polyurethane casters with sealed bearings and integrated floor locks, the team saw immediate improvement:
-
Caster failures dropped by 70 percent
-
Panel staging times were reduced by 30 percent
-
Caster replacements went from monthly to once per quarter
The change saved tens of thousands of dollars in lost time, damaged products, and replacement costs. It also improved morale on the production floor.
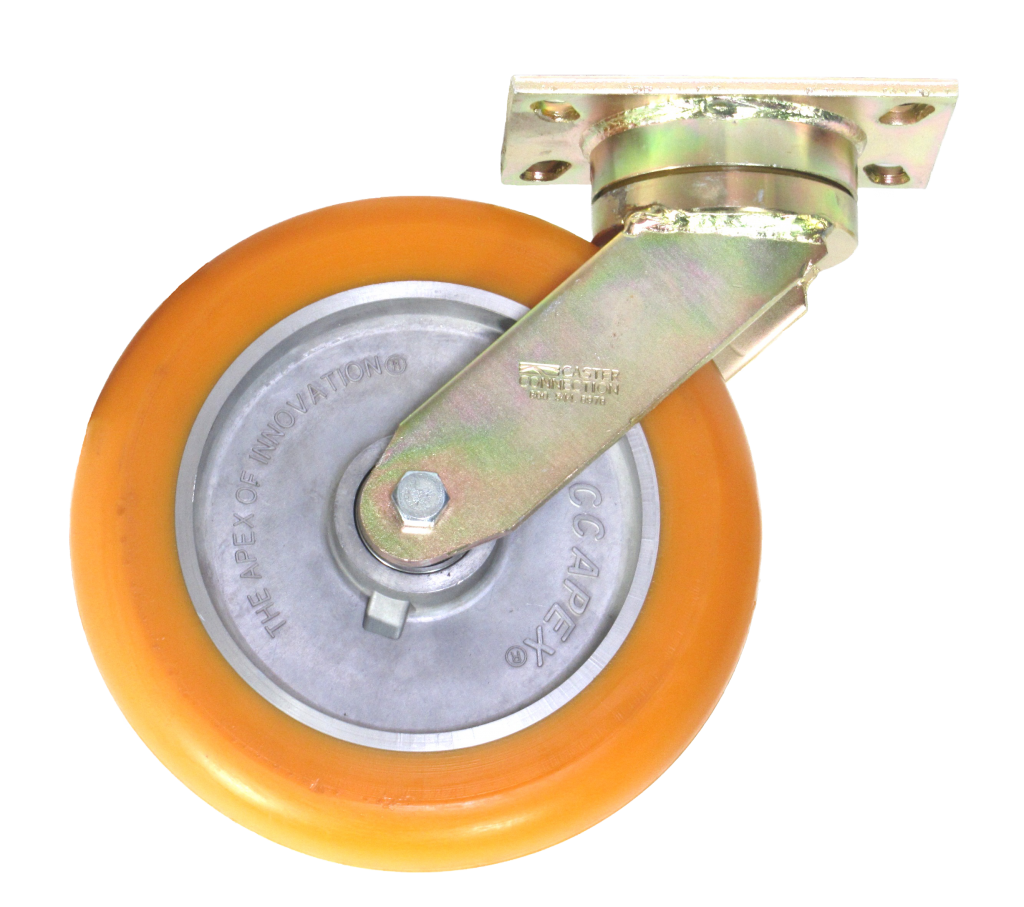
Ready To Upgrade Your Concrete Handling Equipment?
Caster Connection offers caster solutions built for the tough demands of concrete work and its demanding schedules. If you're ready to outfit your carts, forms, or racks with casters that reduce maintenance and boost performance, we've got you covered.
SKU: CC-1010-800200-40-T2
ALT-SKU: CCAPEX-8R-TP2
-
- Overall Height
- 9-1/2"
- Wt. Capacity
- 1,200 lbs.
- Wheel Width
- 2"
- Wheel Diameter
- 8"
SKU: CC-1210-800200-40-T2
ALT-SKU: CCAPEX-8S-TP2
-
- Overall Height
- 9-1/2"
- Wt. Capacity
- 1,200 lbs.
- Wheel Width
- 2"
- Wheel Diameter
- 8"
SKU: CC-1212-300125-40-T4
ALT-SKU: CCAPEX-325-G-S
-
- Overall Height
- 4-1/4"
- Wt. Capacity
- 400 lbs.
- Wheel Width
- 1-1/4"
- Wheel Diameter
- 3"
4" Solid Steel V-Groove Rigid Caster
SKU: 4-82-DIV
-
- Overall Height
- 5-5/8"
- Wt. Capacity
- 1,250 lbs.
- Wheel Width
- 1-13/16"
- Wheel Diameter
- 4"
3" Low-Profile Nylon Swivel Caster
SKU: P10S-NG030K-P
-
- Overall Height
- 3.9375"
- Wt. Capacity
- 660 lbs.
- Wheel Width
- 1-9/16"
- Wheel Diameter
- 3"
Save More With Tiered Pricing
Whether you're replacing a few wheels or outfitting a full production line, we offer volume discounts on many of our Caster Connection brand products. You'll get better value as your order size grows. Shop casters with tiered pricing available or contact us to get personalized guidance and pricing.
Keep Concrete Projects Rolling Smoothly
Concrete is one of the most durable materials on Earth. But the process of making and handling it is tough on tools, workers, and timelines. If your casters aren’t built to survive those conditions, they’ll fail quickly and throw off your entire schedule.
The right caster solution makes concrete handling safer, faster, and more reliable.
Whether you’re pouring barriers in a prefab facility or staging panels on site for installation, trust the wheels that are built to take the pressure and keep moving forward.
Ready to move your heaviest loads with confidence?
Start your Caster Needs Evaluation today.
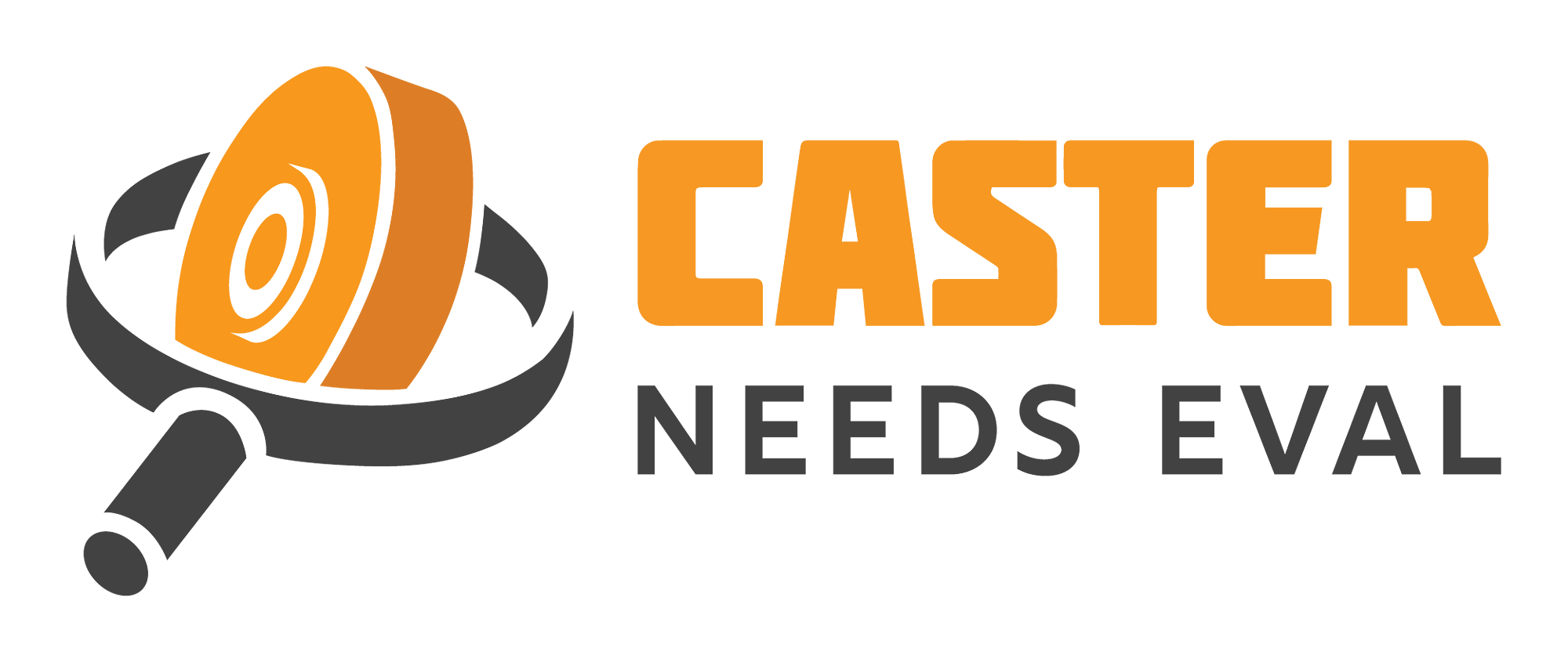