How To Remove The Waste Of Non-utilizing Talent During Downtime
Non-utilization of talent is one of the eight wastes of downtime in lean manufacturing. it can best be described as a waste of waiting and has severe implications on factory efficiency. When an application goes down for maintenance, it can bottleneck a process from phasing into the next stage. Non-utilizing talent can be caused by numerous factors: production lines being on hold or managers improperly positioning their talent. Regardless of the causes, non-utilization can be prevented when management strategically assigns tasks to their team. The non-utilization of talent is a common phenomenon that often goes unnoticed. If you feel as though your company is not performing to your standards, you should ask yourself the questions listed below. Each question will allow you to consider what areas can be improved to enhance your manufacturing productivity. Utilizing your talent to its fullest potential will yield cost savings and can be a major ROI in manufacturing.
This post will go over how to remove the waste of non-utilizing talent of the production line during downtime to improve factory efficiency.

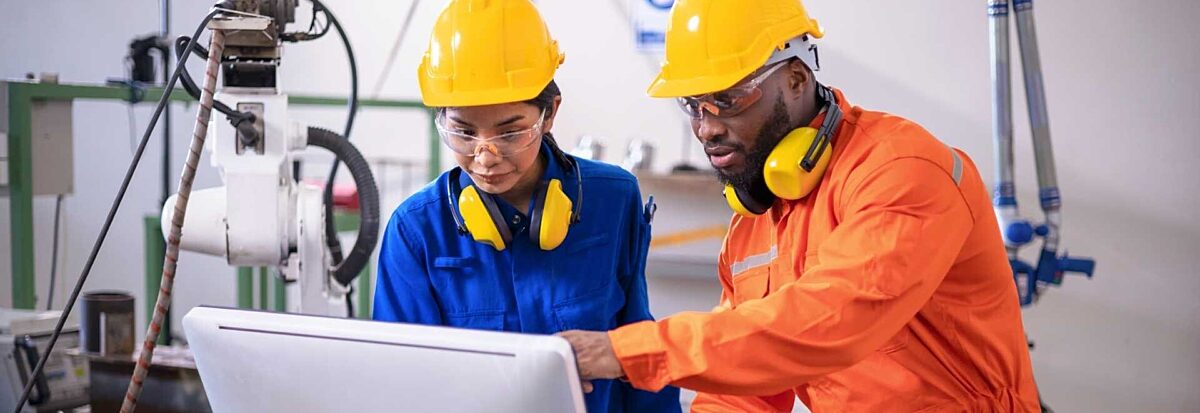
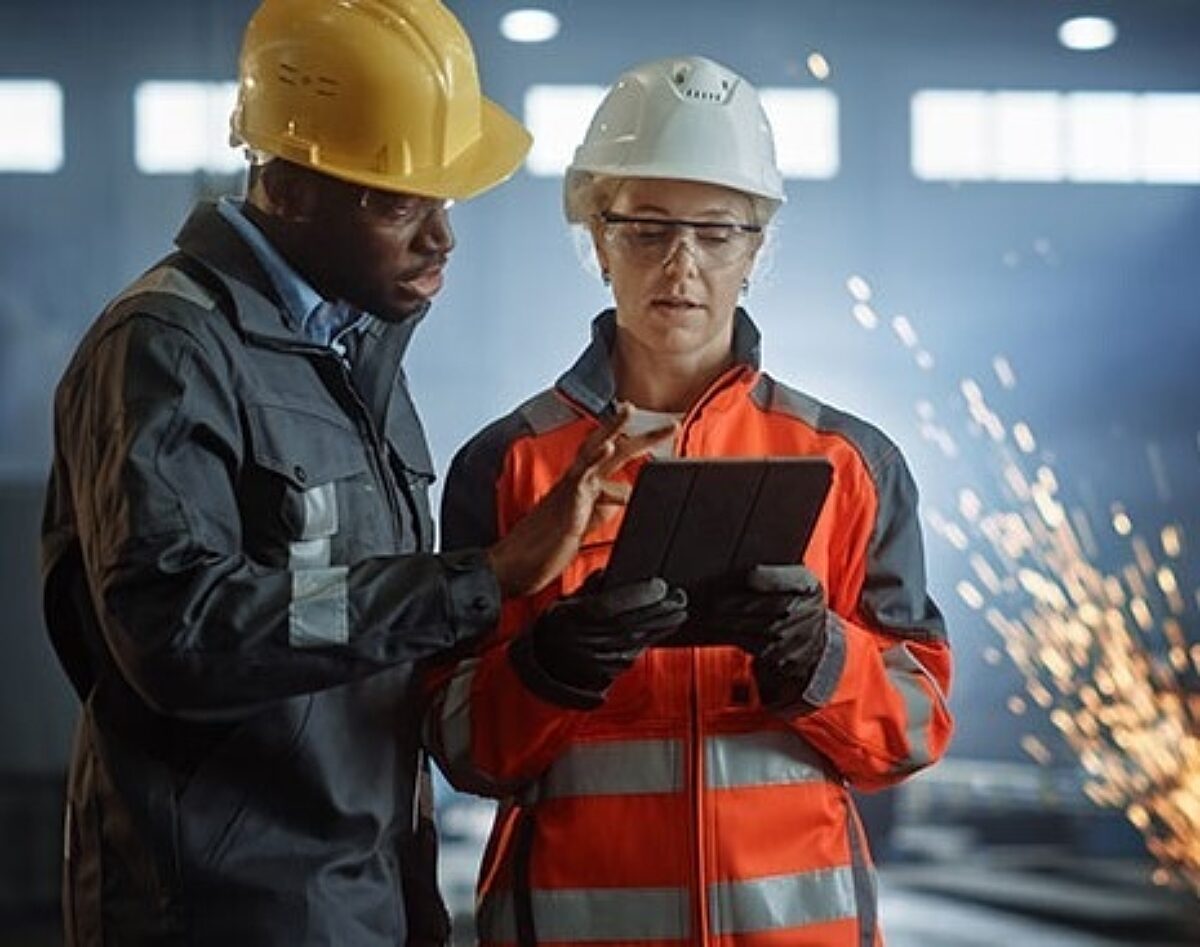
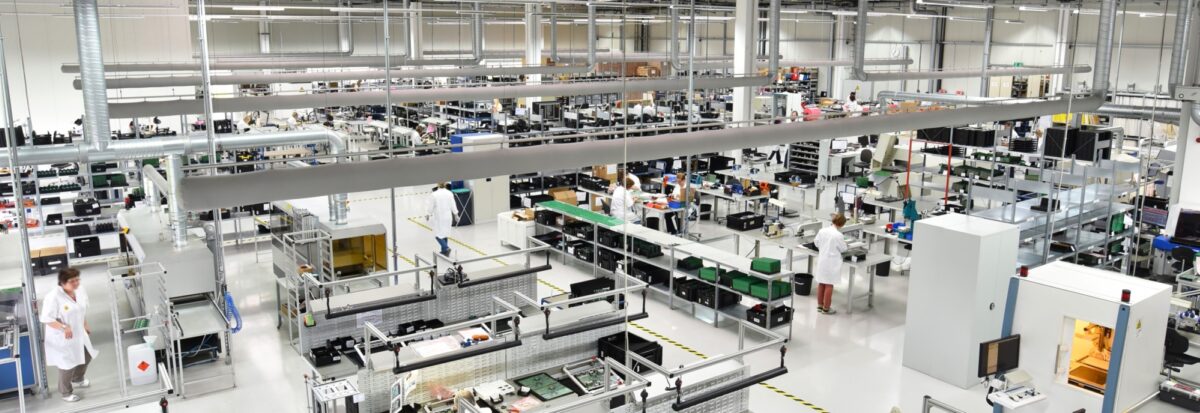
Are Your Employees Receiving Appropriate Training?
Employees are only as good as how well the management trains them. For example, sending a new employee off to watch 300+ industry videos and then throwing them to the wolves expecting them to do a task to get by is not only inadequate training, but it also shows a severe flaw in management’s leadership. Training must be objective to ensure effectiveness. Objective training enables employees to act and be productive right away. Improved training will lead to downtime reduction. Investing in employee training is considered an ROI in manufacturing. Appropriate and accurate training can also lead to a reduction in damage and injuries. Although there will be costs upfront to improve training, there will also be clear improvements in manufacturing efficiency in the long run.
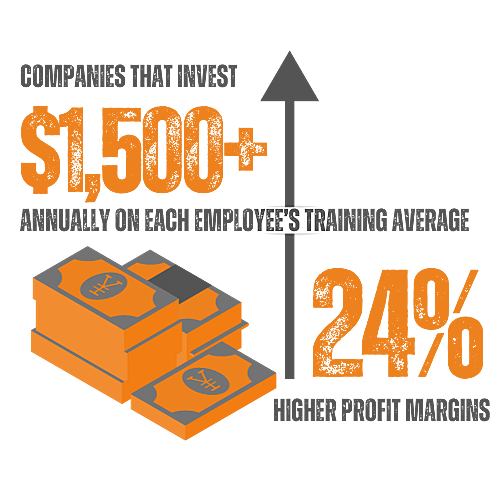
Does Your Company Practice Clear Communication?
A very simple solution to improve the utilization of your staff is to implement a clear path to communication between management and your employees. Clear communication is beneficial to the success of your company and the attitudes of your talent. When management can effectively assign tasks to workers there will be a reduction in downtime, and it will improve manufacturing efficiency. A direct line of communication is essential to saving time and costs. Not only can clear communication limit costs, but it can improve your working staff’s motivation. It is common knowledge that employees that enjoy who and what they are working for are more likely to work harder. This principle may seem simple; however, it is relentlessly overlooked when systems are put into place. If you and your company prioritize clear communication a respectful relationship between the company and those working for it will be formed. Once motivation is driven from your talent, you will immediately notice an improvement in utilization and factory efficiency.
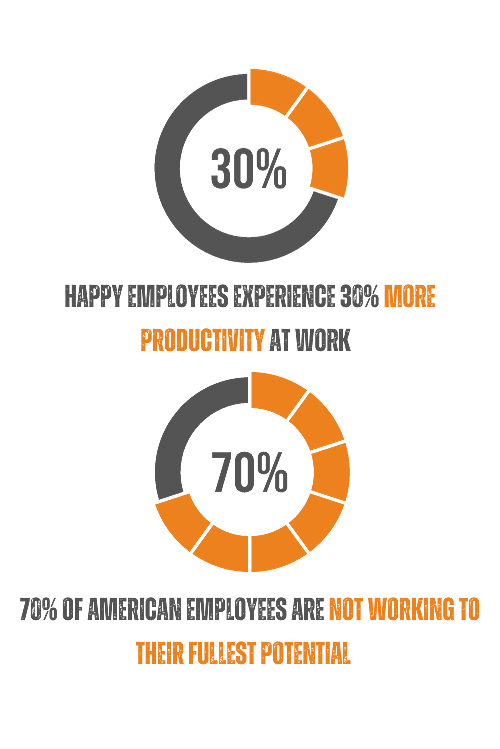
Do You Limit an "Order of Command" Design?
Most common in manufacturing facilities, an order of command design is implemented where subordinates report to a supervisor. Although this company construct appears to establish clear communication through a hierarchal system, it can be detrimental to utilization. This system can cause a lack of talent recognition since supervisors overseeing company operations are not directly acknowledging the faculty running their facilities. Since the higher-ups are not focusing on which employees may be useful in other positions, they are not using all their staff to their fullest potential. If your company does operate on an order of command system, you may want to consider adjusting it so that supervisors are consistently evaluating and determining where in the manufacturing process each employee would be most suitable. By maximizing the positioning of your employees, you will yield improvements in manufacturing efficiency, which would be a ROI in manufacturing.

Are Performance Reviews Being Consistently Used?
To limit non-utilization successful companies have implemented a performance management system, most often guided by performance reviews. By conducting consistent reviews employers can define clear goals and consistently evaluate their talent. Reviews allow employees to feel seen and rewarded for their hard work and management can identify performance issues early on. Performance reviews will lead to a reduction in down time since it will allow management to place employees in suitable roles and limit lean manufacturing wastes. Clear goals will be communicated on a consistent basis which will improve factory efficiency.
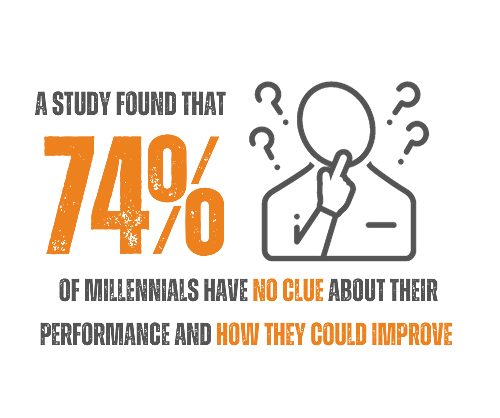
Conclusion
Directing talent to do busy work is not a good use of downtime. When a manager utilizes an employee’s skill set to better a manufacturing process, everyone benefits. Utilization is a key component to a successful company, maximizing utilization improves manufacturing efficiency. If your company is looking for ways to improve in these areas, focusing on the non-utilization of your talent is a great place to start. If you are interested in other easy ways to upgrade your manufacturing facility beyond utilization, browse our website of premium casters. Caster Connection has a wide selection of wheels and casters which can be tailored to your company’s warehouse or distribution needs. Establishing a World Class Manufacturing culture is a team effort and Caster Connection is here to assist you along the way.
Interested in learning more about our offerings that can help improve your company’s efficiency and utilization? Send us a message today and we'll get you in touch with one of our Regional Solutions representatives.