8 Waste Types Of Downtime
"Lean manufacturing" or lean production, often simply "lean", is a systematic method for the elimination of waste ("Muda") within a manufacturing system." Before deciding on your application's solution to run lean, you need to understand the 8 waste types of downtime.
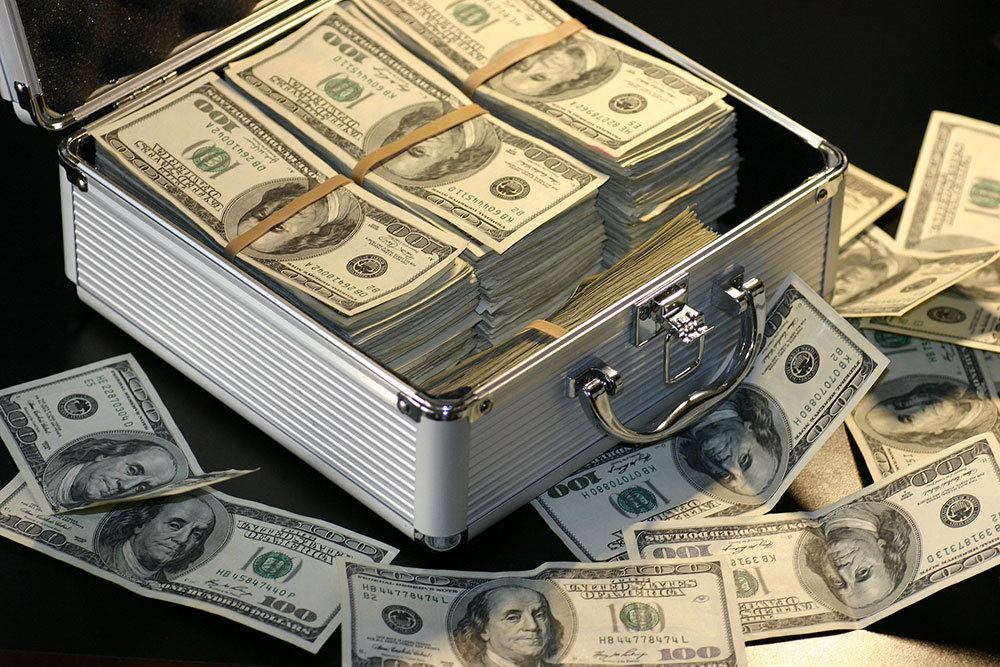
The 8 waste types of downtime are:
- Defects
- Overproduction
- Waiting
- Not-Utilizing Talent
- Transporting
- Inventory
- Motion Waste
- Excess Processing
Defects are a great example as to why it is imperative to choose the right product the first time. Improper deployment of tools, poor specifications, and poor quality can require a lot of time and money to resolve an issue.
Overproduction is when a company produces more products than the market demands. Overproduction is one of the largest types of waste that contribute to increased inventory holding cost, labor, and facility cost.
Waiting involves a delay of the production flow process. Delay can happen through unplanned downtime, which can occur through malfunctioning of poor quality materials, waiting on appropriate materials to complete a task, or unbalanced workload that can bottleneck the workflow.
Not-Utilizing Talent takes place when personnel is idle while waiting for a process to be completed by another staff member or process, or when they are not utilized effectively based on their knowledge or skill-set.
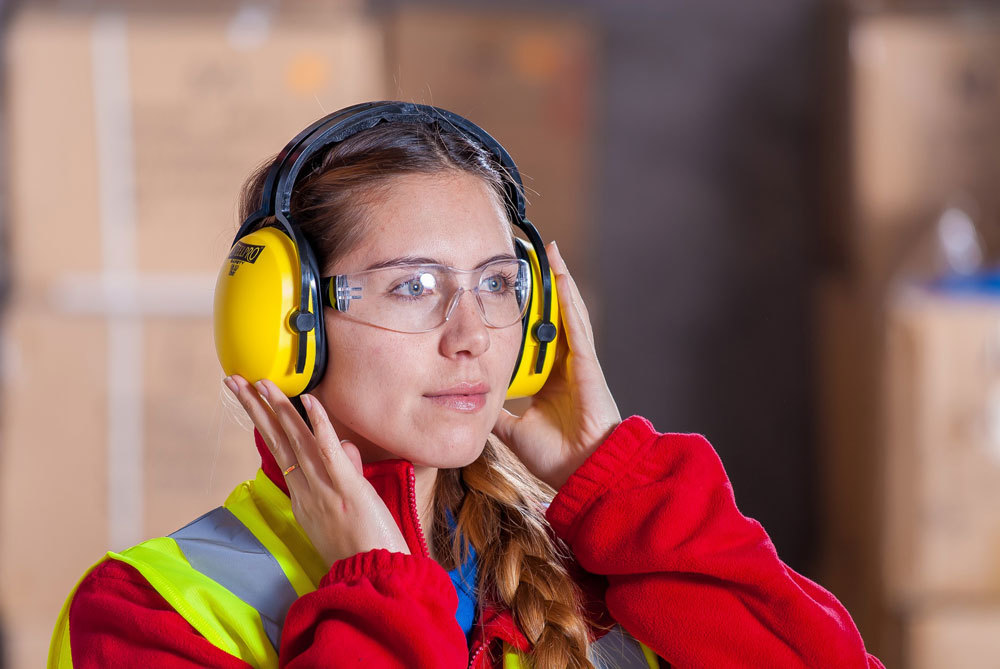
Transporting materials through long or complicated routes between operations can exponentially increase handling costs. Learn more in our article, Forklift-free Initiative: Using Casters To Pull Towards Lean.
Inventory Excess increases manufacturing costs by consuming extra floor space required to maintain excess inventory, and the people obligated to handle it. Lean manufacturing works off of a pull system that produces product at a time when customers need it. Doing so will not put a company in a predicament of trying to figure out how to sell the excess product when there is no demand for it.
Motion Waste is excess movement that can put workers’ safety at risk, possibly resulting in overexertion injuries. Overexertion injuries can cause a significant reduction in employees' productivity. Employing a new hire will cost time and money to properly train the new employee to make up for the delay. Also, reassigning an existing employee to cover the injured employee’s position does not alleviate the fact that the workforce is still down a person. Learn more about employee safety from our Ergonomic Casters Education section.
Excess Processing happens when operation depends on surplus labor because of poor maintenance, excess operational capability for production requirements and/or fulfilling redundant processes that stand in the employees’ way of being optimally productive.
Caster Connection upholds World Class Manufacturing principles and stresses the importance of choosing the right product the first time, which will help to avoid a host of problems from downtime.
Contact us for assistance to help you find the right mobility solution to any of your problems with downtime.
HAVE MORE QUESTIONS? LET'S TALK!
Get Rolling with Caster Connection →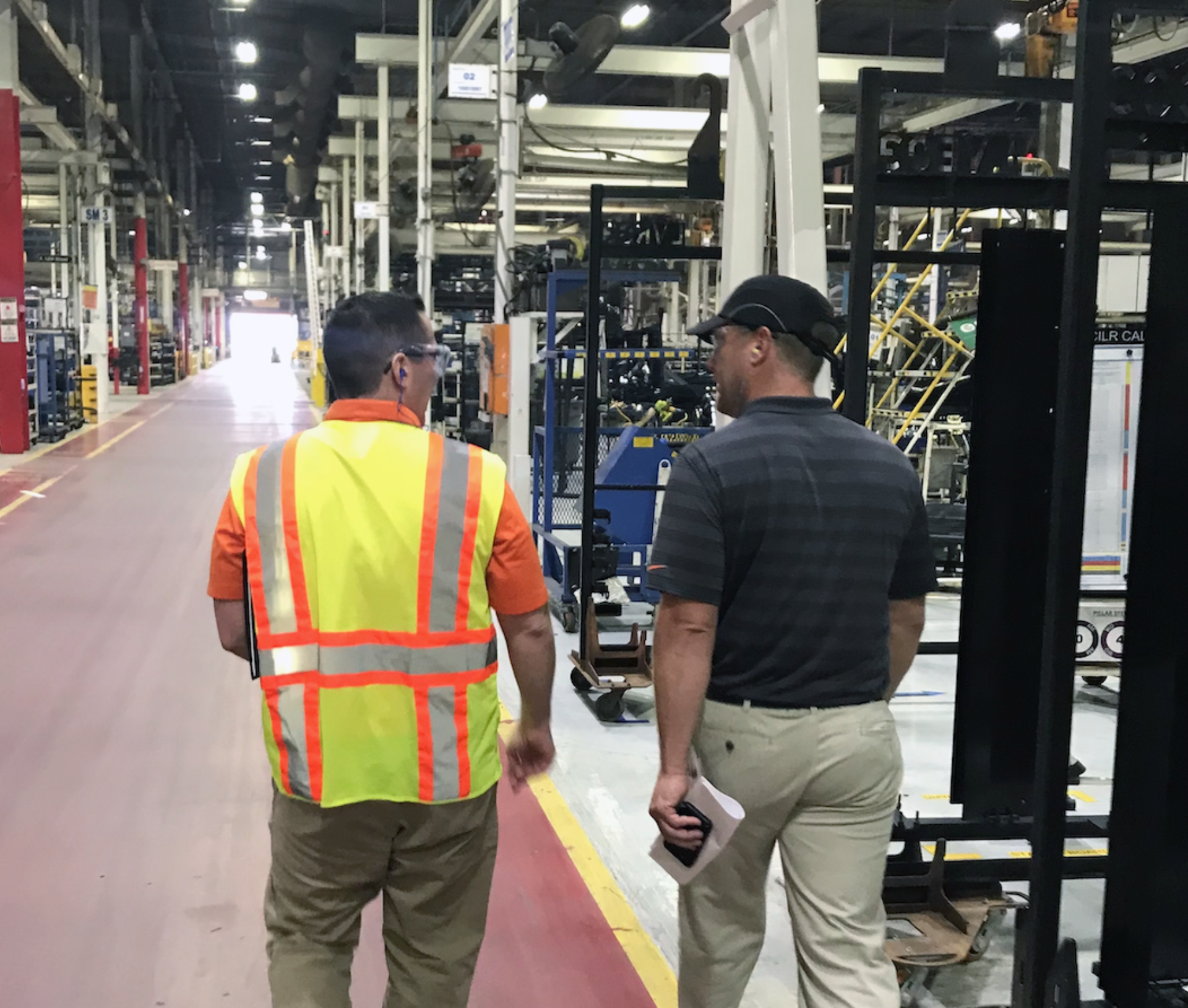