Navigating Aerospace Material Handling Challenges Amid Rising Costs
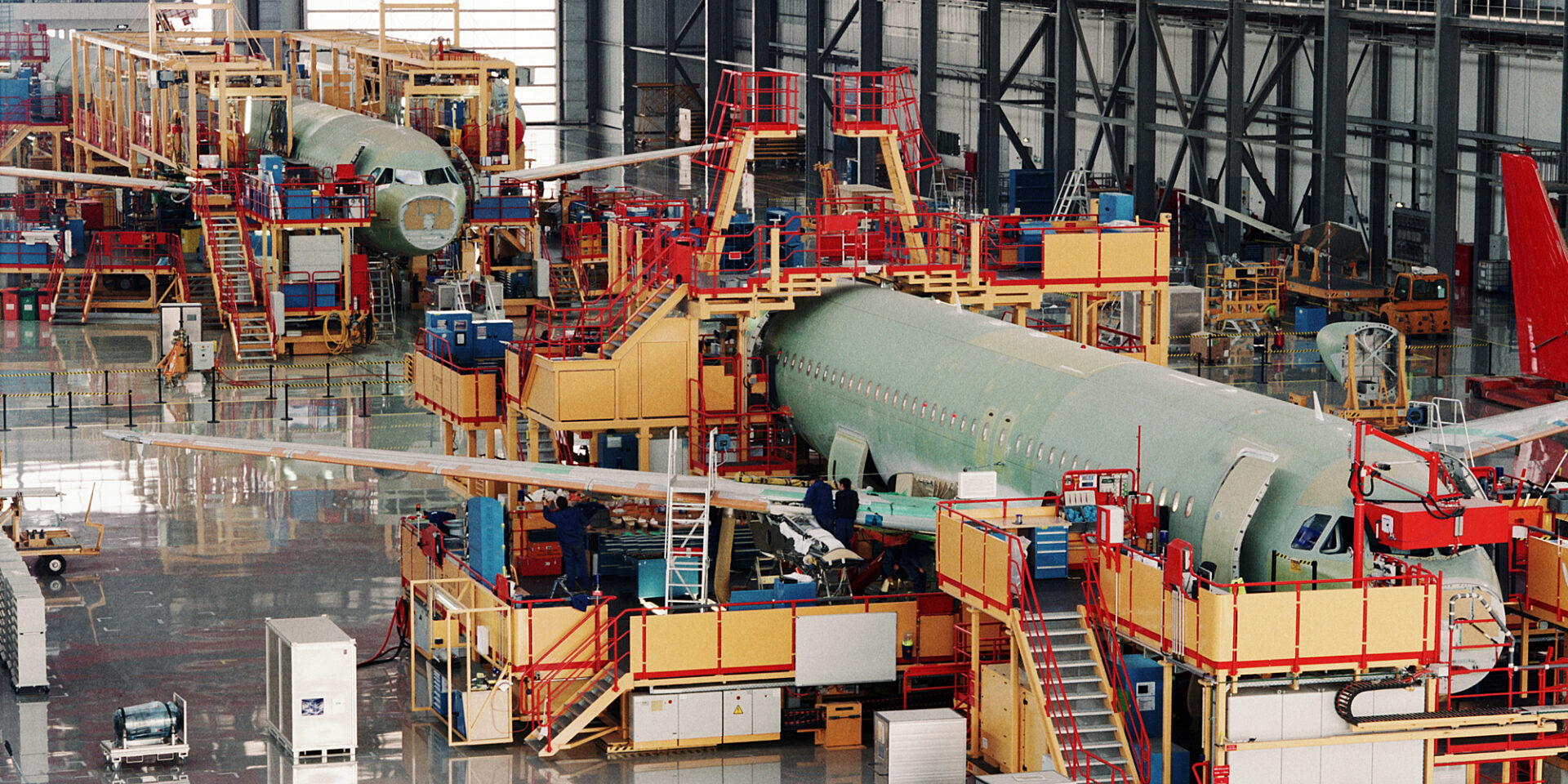
Aerospace manufacturing demands precision, consistency, and control. These qualities are becoming harder to maintain in a volatile market shaped by rising steel costs, supply chain disruptions, and mounting production pressures. As budgets tighten, aerospace operations must find smarter ways to protect productivity and safety without compromising quality.
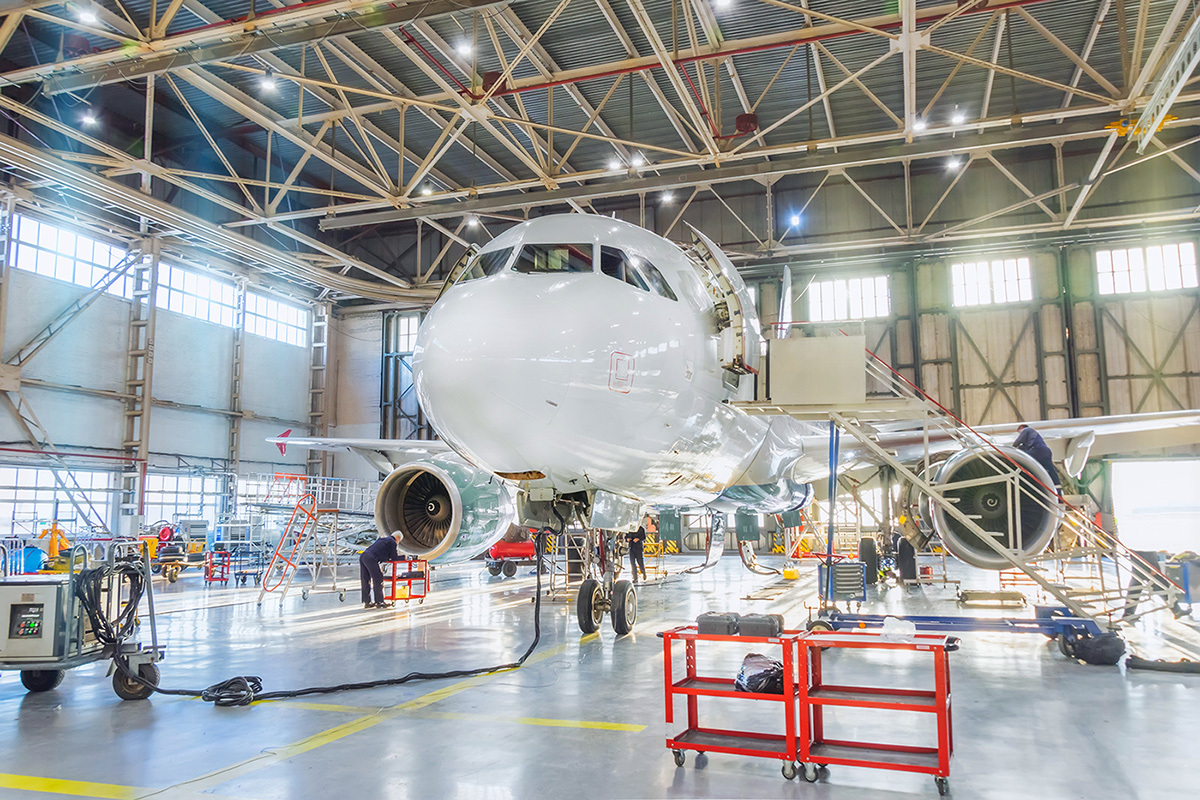
One solution that often gets overlooked? Premium casters. In this blog, we’ll break down the material handling challenges unique to aerospace manufacturing and show how the right caster solutions can help you maintain performance and control costs.
The High-Stakes Nature of Aerospace Material Handling
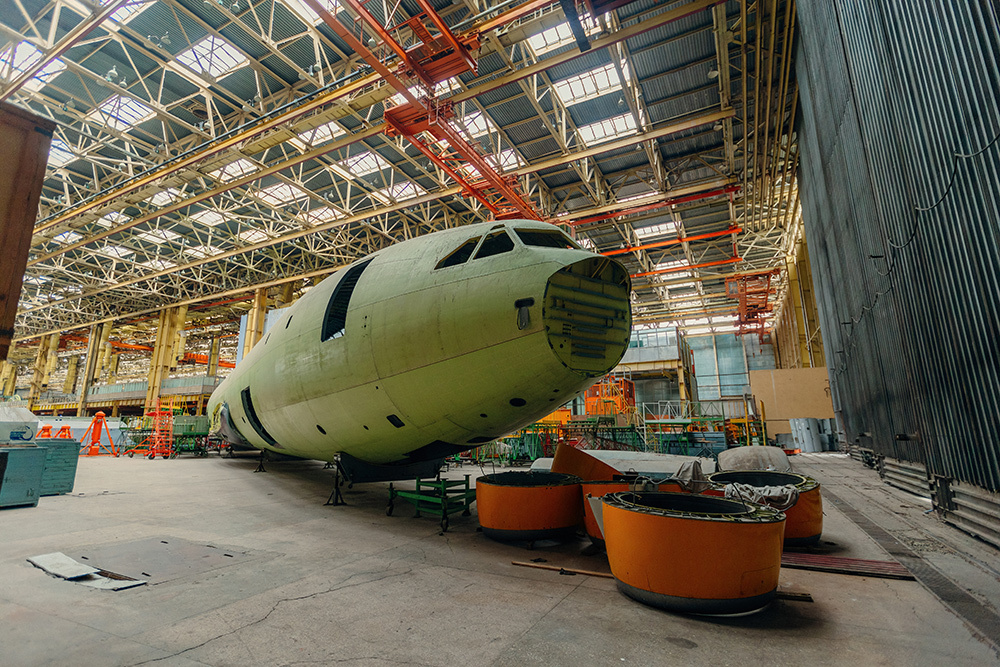
Aerospace manufacturing demands an exceptional level of control at every stage of production. From transporting sensitive components to maneuvering complex assemblies through tight floor layouts, material handling is deeply tied to product quality, worker safety, and operational efficiency.
The equipment used in these environments must do more than move items from point A to point B. It must prevent damage, maintain accuracy, and support repeatable, ergonomic workflows. Effective material handling solutions help:
-
Prevent costly damage to high-value parts
-
Reduce shock and vibration that compromise precision
-
Maintain consistent tracking and controlled movement
-
Minimize operator strain in repetitive or high-force tasks
Casters may seem like a small detail, but their performance has outsized consequences. A single failure can disrupt production, delay assembly schedules, or lead to costly rework. In aerospace, where stakes are high and tolerances are tight, the right mobility solution is essential to keep operations running on time and to spec.
Key Challenges Facing Aerospace Manufacturers
Aerospace manufacturers operate in an environment where precision, safety, and efficiency are non-negotiable. But rising costs and evolving production demands are creating new pressure points on the shop floor. These are three of the most common mobility-related challenges impacting aerospace material handling today.
1. Rising Steel and Raw Material Costs
The cost of steel continues to rise due to tariffs, supply chain instability, and increased global demand. Many facilities rely on heavy-duty casters that use more steel than necessary, assuming it’s the safer option. But when multiplied across hundreds of carts and fixtures, these overbuilt components add significant material costs without delivering additional value.
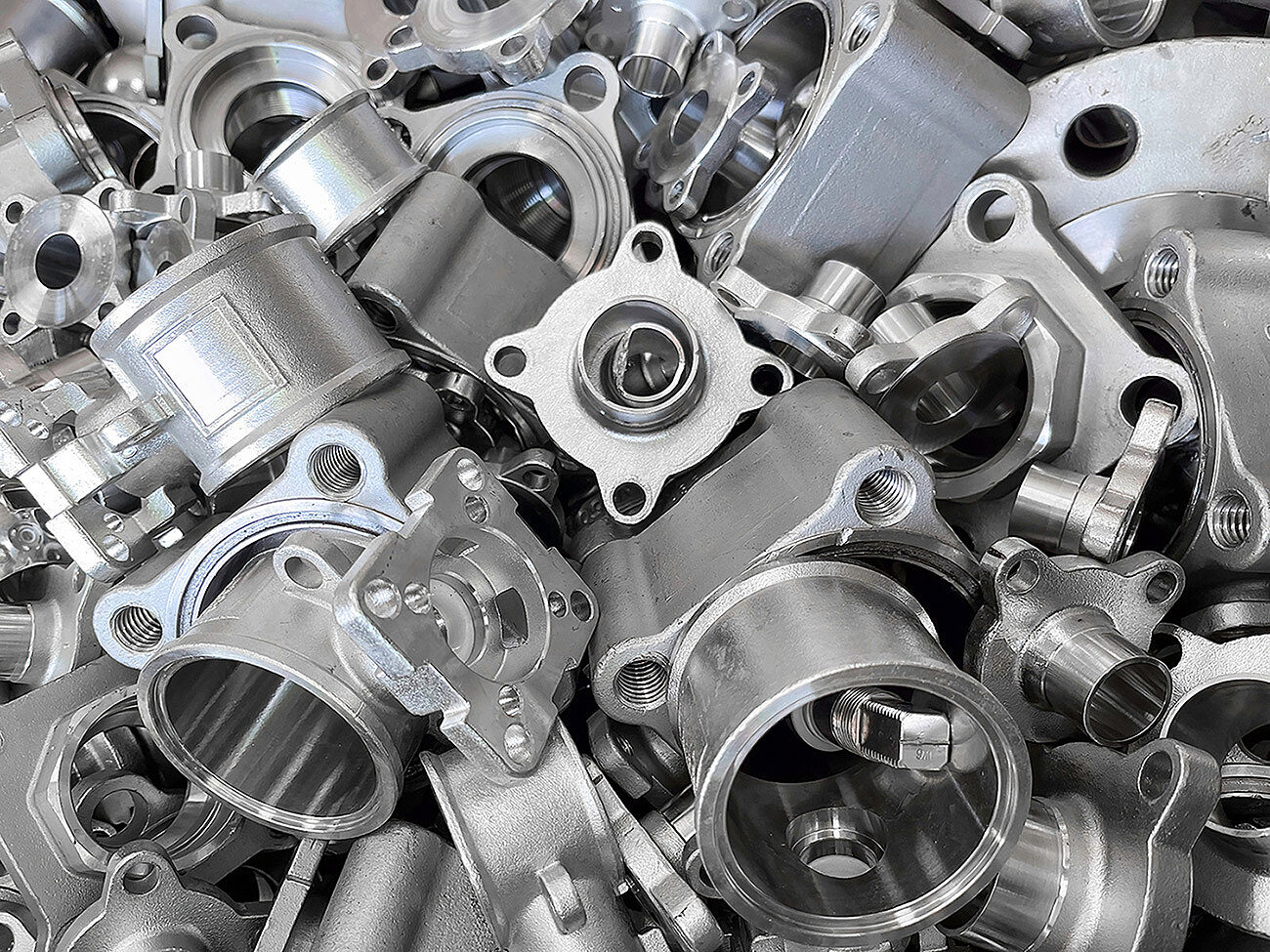
2. Tight Tolerances and Handling Sensitivity
Aerospace components require smooth, controlled movement to avoid vibration, misalignment, or impact during transit. Casters that drag, bind, or track inconsistently can disrupt sub-assembly workflows and lead to expensive rework. They also increase strain on operators, especially in high-repetition tasks, raising injury risk and slowing throughput.
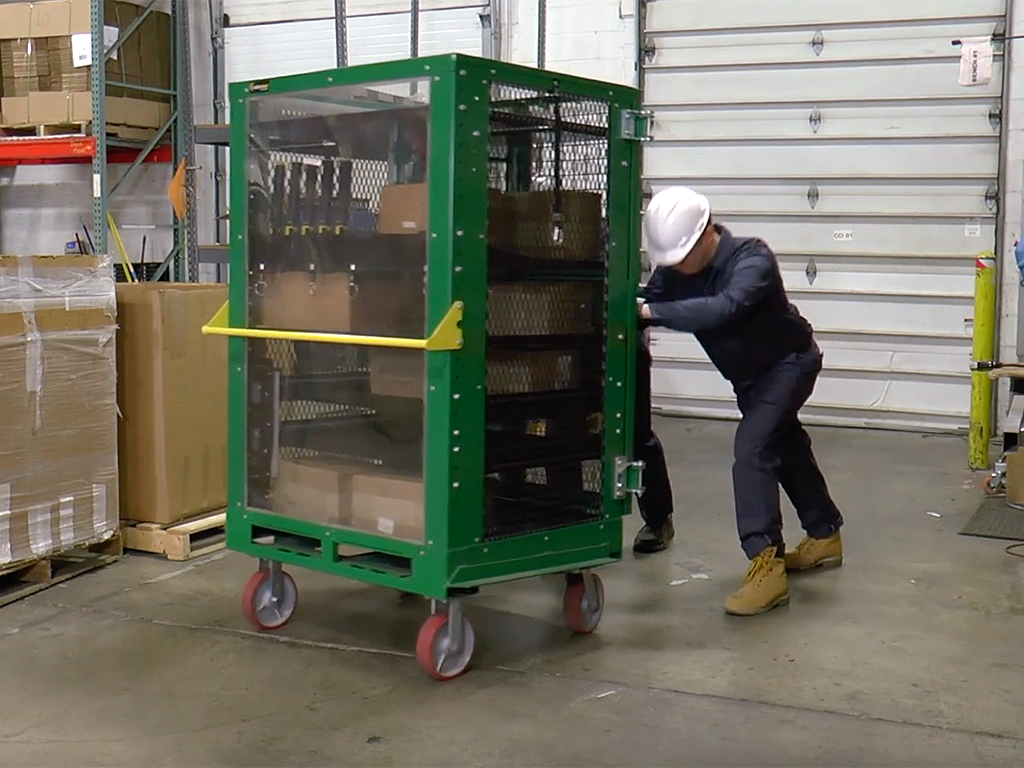
3. Space Constraints and Complex Layouts
Lean aerospace facilities often operate in constrained environments with narrow aisles, sharp turns, and specialized equipment zones. Casters that don’t match the layout can cause carts to drift, snag, or resist movement, which slows operations and increases the risk of collisions or floor damage. Precision mobility is essential for maintaining flow and safety.
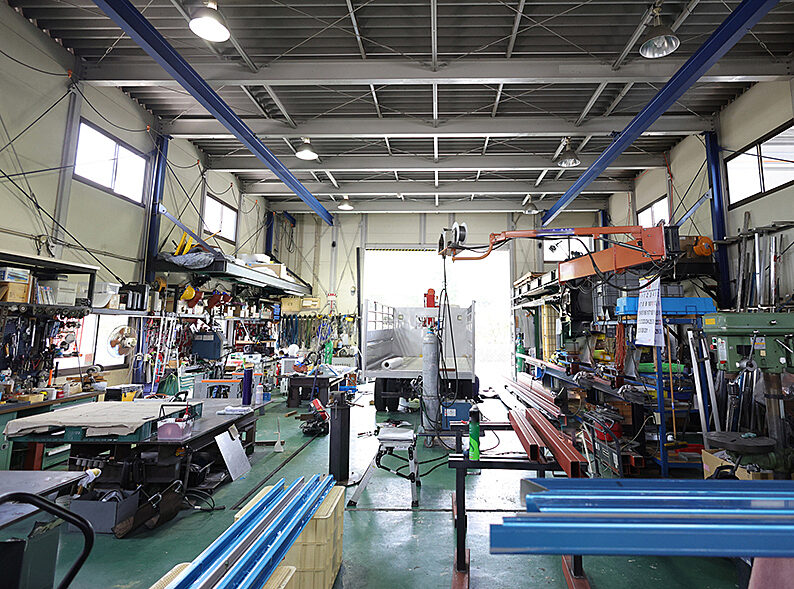
How Premium Casters Solve Aerospace Pain Points
Aerospace environments demand more from every component, and casters are no exception. When failure isn’t an option, premium caster solutions help manufacturers maintain precision, reduce disruptions, and protect high-value parts. Below are three ways advanced caster design addresses common aerospace material handling challenges.
1. Long-Term Durability
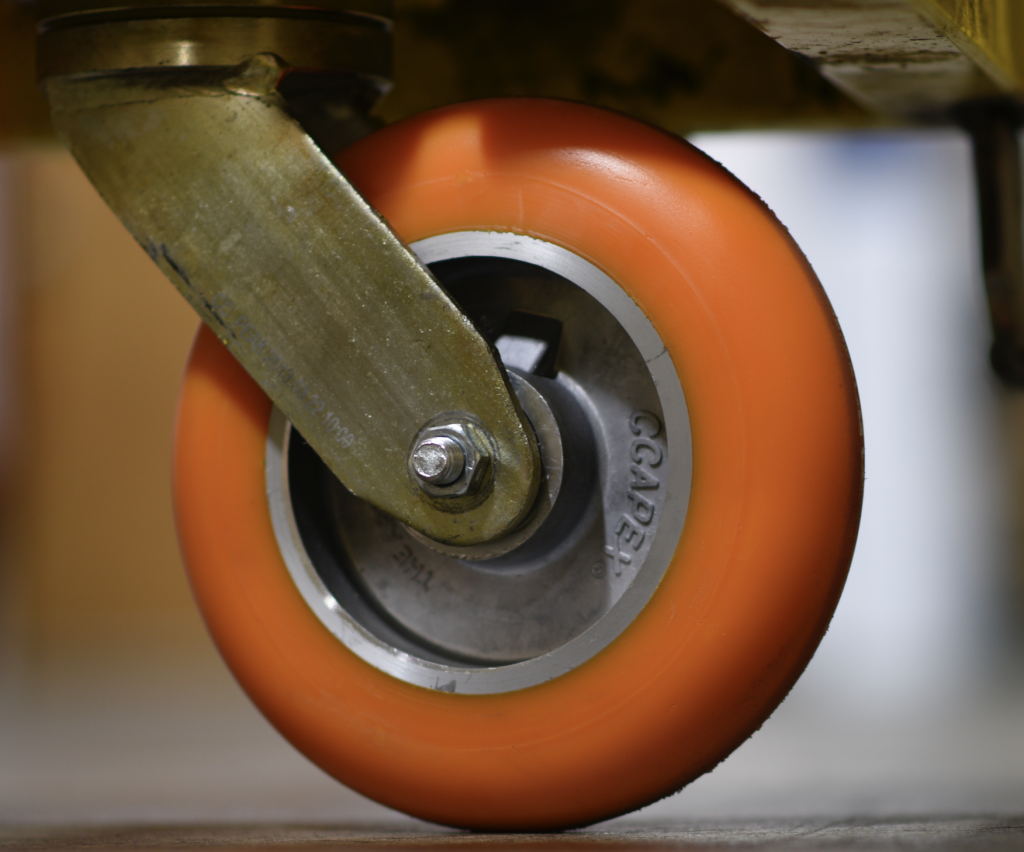
Casters like the CC Apex and CC Stout are engineered specifically for high-use aerospace environments, where performance and consistency are critical. Their durable construction reduces the need for frequent replacements, minimizes downtime across production cycles, and ensures smoother, more reliable handling even under continuous load and movement.
2. Ergonomic, Controlled Mobility
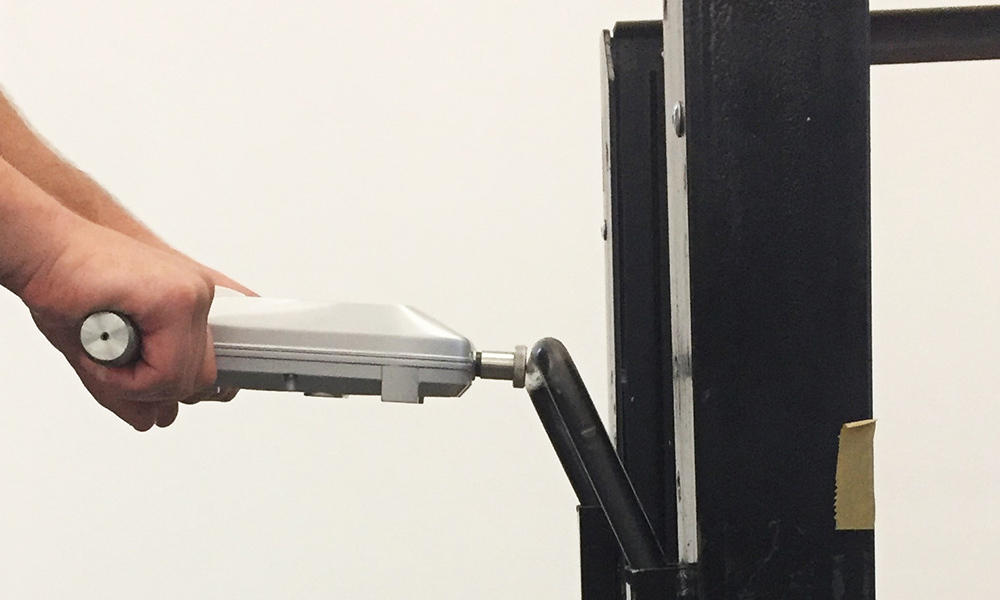
Premium casters with sealed precision bearings and polyurethane treads help achieve stable, quiet movement across epoxy, concrete, and other industrial floor types. This controlled mobility not only protects delicate payloads from vibration and shock, but also reduces operator fatigue, improves safety, and enhances maneuverability in tight, complex workspaces.
3. Application-Specific Solutions
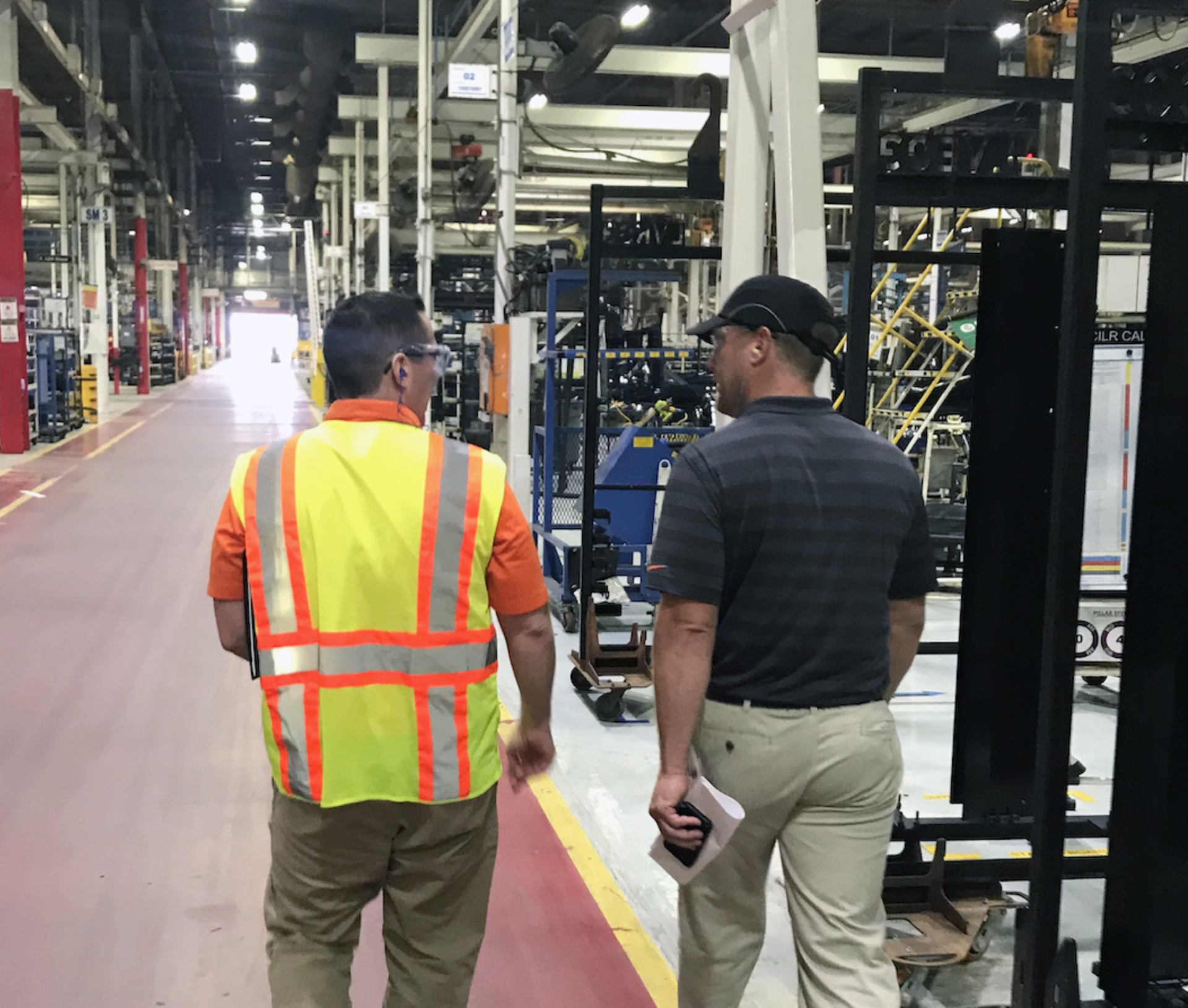
Aerospace operations rely on a wide range of carts, racks, and fixtures, each with its own load requirements and mobility demands. Our team works directly with manufacturers to specify the right caster for each application, taking into account factors like duty cycle, floor conditions, turning radius, and ergonomic goals. This tailored approach ensures every caster supports both the equipment and the workflow it’s built for.
Case Study: Reducing Downtime by 45%
An aerospace facility was facing repeated caster failures on carts transporting jet engine parts. After a Caster Needs Evaluation, they transitioned to heavy-duty polyurethane casters with sealed bearings and optimized tread width.
Results:
-
45% reduction in downtime related to caster failure
-
Improved safety and smoother handling
-
Longer caster life with lower total maintenance and procurement costs
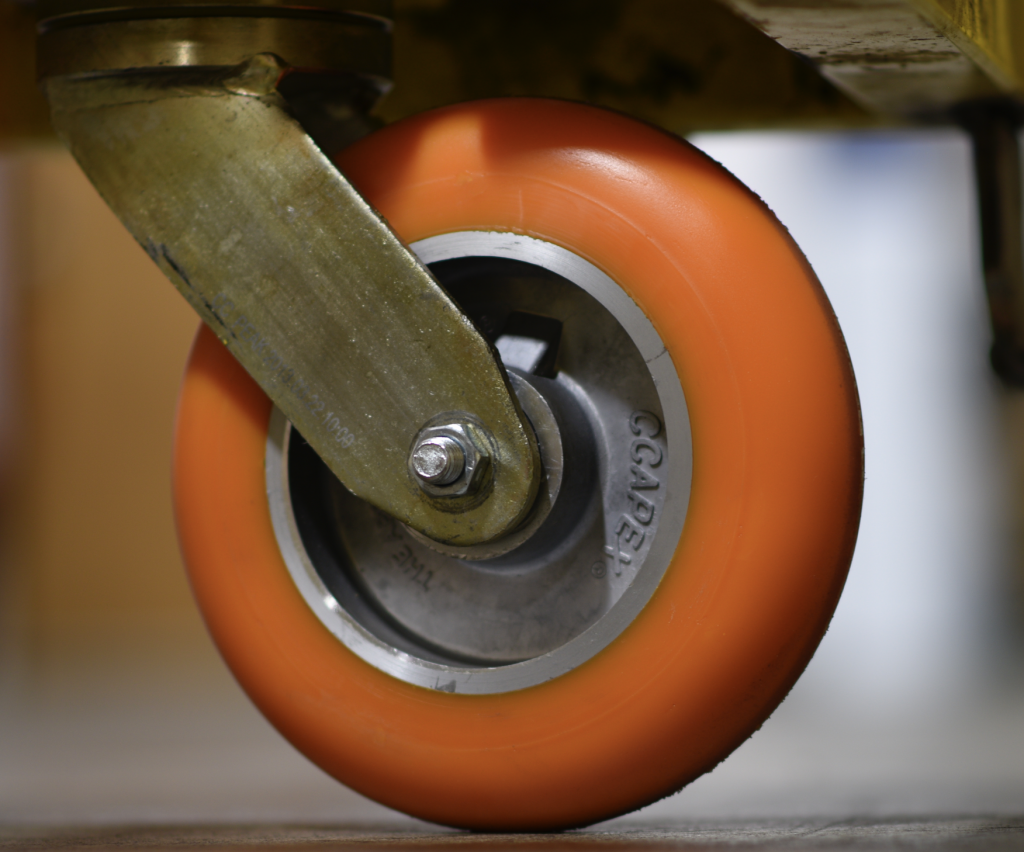
Elevate Performance Without Increasing Cost
In aerospace, there’s no room for wasted time or tolerance for unreliable equipment. As costs rise and expectations grow, premium casters offer a simple, scalable way to protect productivity, support precision, and reduce long-term expense.
If you're ready to assess your caster setup, we’re here to help. Schedule a Caster Needs Evaluation, explore aerospace-ready solutions, or connect with a specialist to build a plan tailored to your goals.
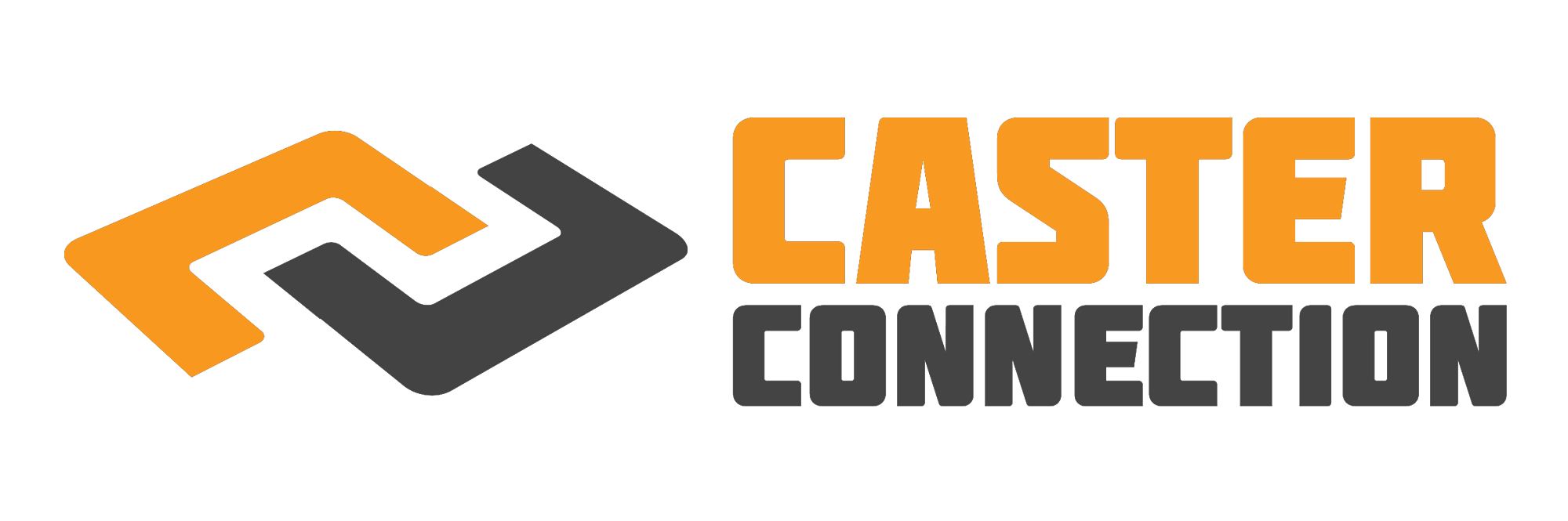