Adapting to Tariffs and Supply Chain Shifts in Material Handling
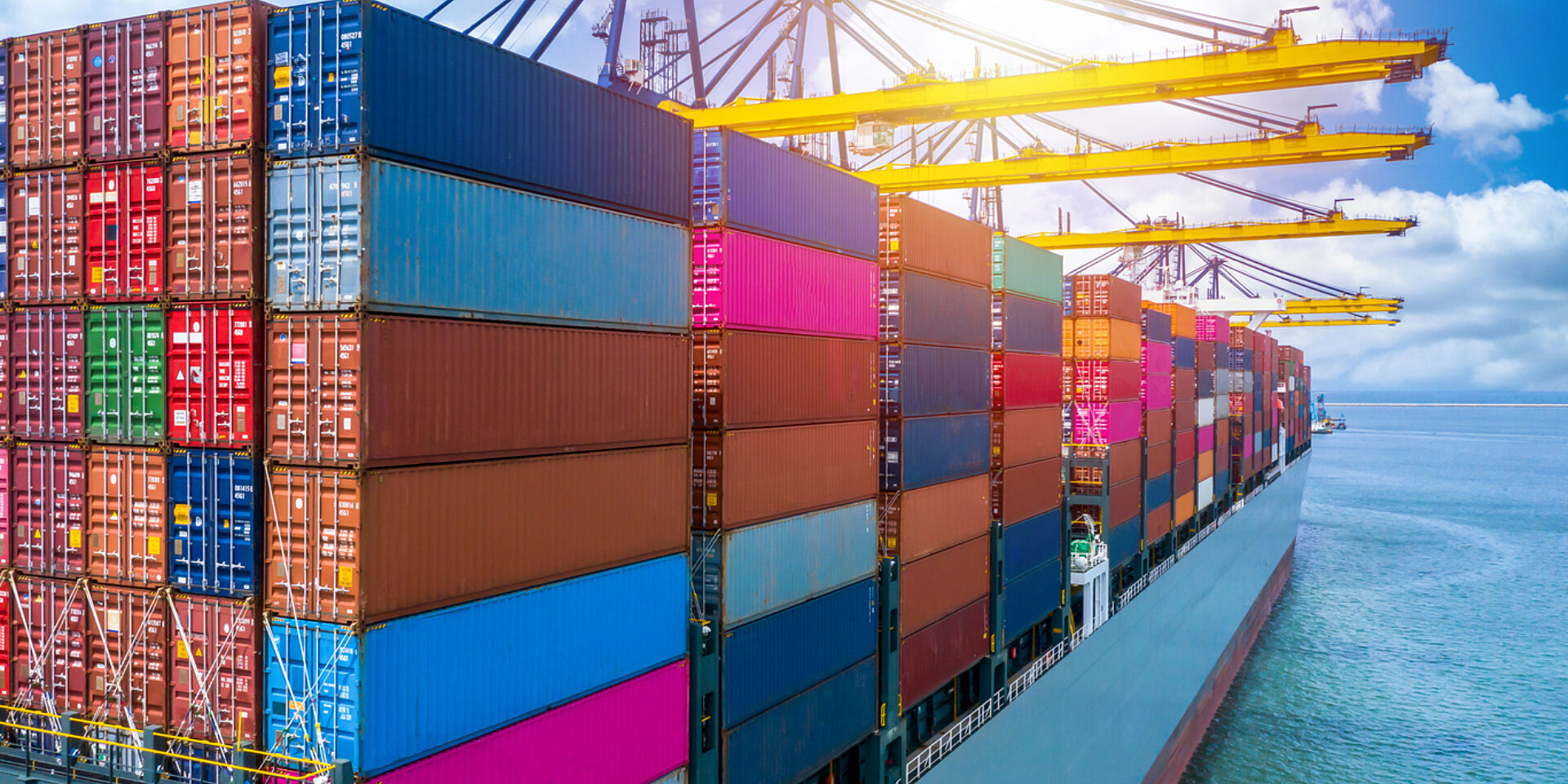
Material handling is the backbone of any successful operation in manufacturing, logistics, and distribution. But with ongoing supply chain disruptions, rising tariffs, and unpredictable material costs, the rules are changing fast.
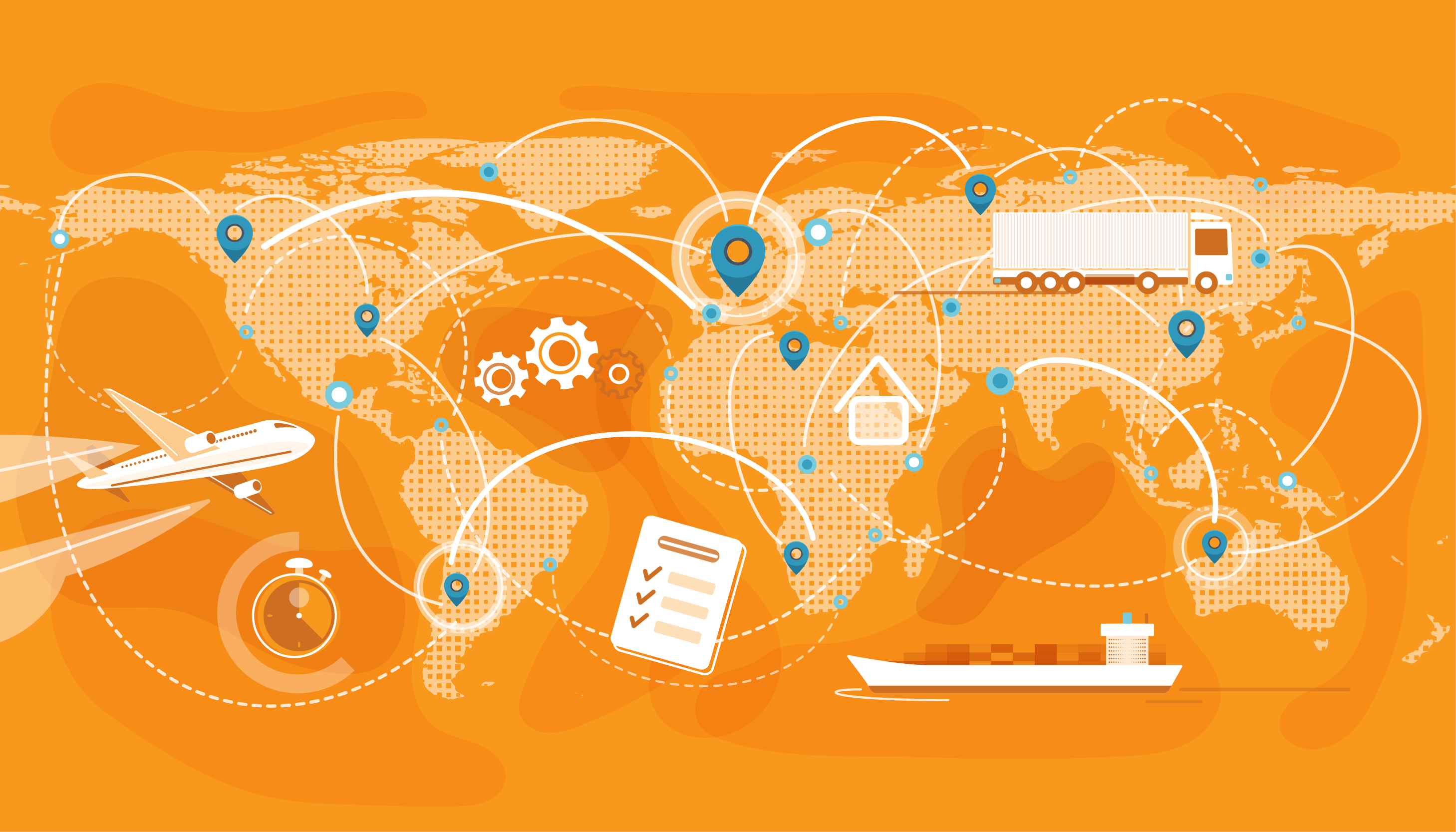
Today’s environment requires more than speed and efficiency. It demands flexibility, resilience, and smarter decision making at every level. In this blog, we’ll take a closer look at what’s driving the change and how forward-thinking teams are adapting.
What's Driving Change in Material Handling?
The material handling landscape is being reshaped by a combination of global, economic, and workforce pressures. Here are the key forces behind the shift.
Steel Tariffs and Raw Material Volatility
Ongoing tariffs and rising metal costs have made pricing unpredictable. Core materials like steel now fluctuate sharply, affecting everything from caster rigs to storage racks. This makes long-term budgeting and procurement planning far more difficult.
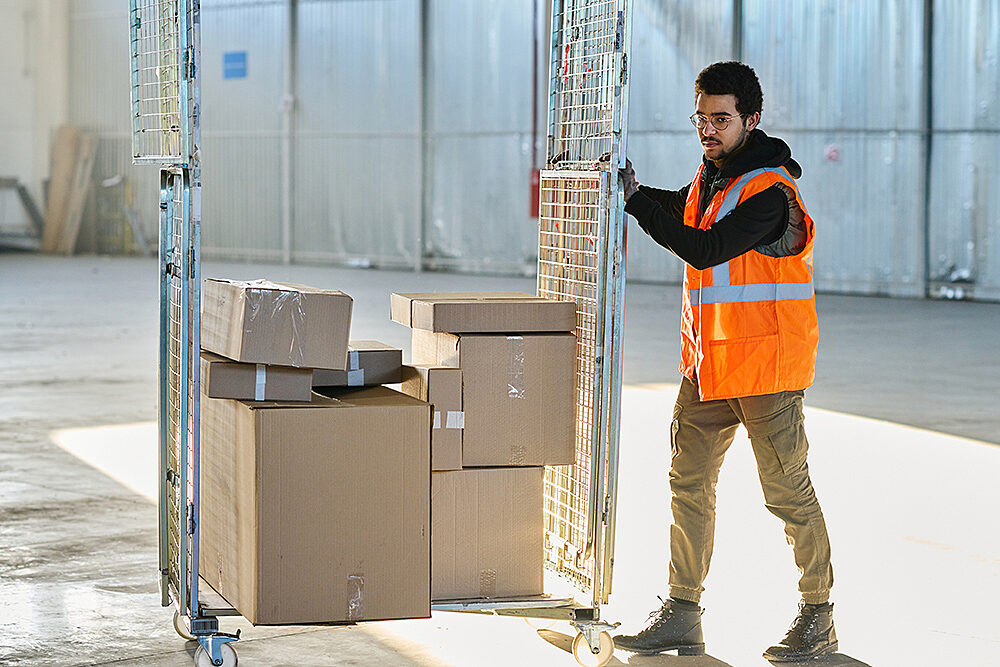
Supply Chain Delays and Disruptions
Shipping slowdowns and component shortages have made advanced planning critical. When previously common parts suddenly go out of stock, operations are forced to deal with delays, downtime, and the scramble to find alternatives.
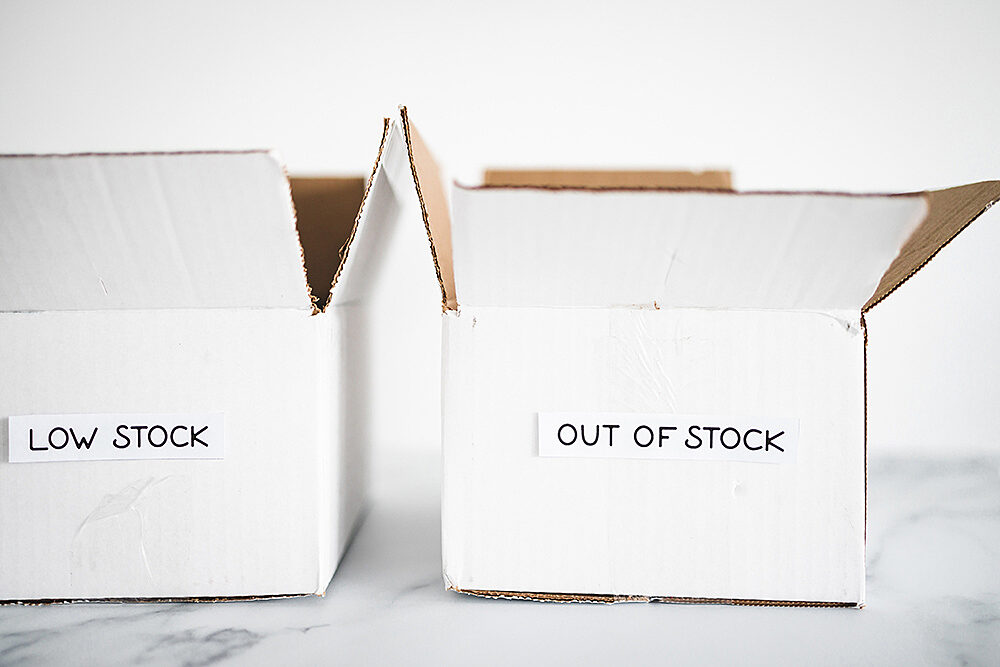
Labor Shortages and Increased Safety Demands
With fewer workers available and a growing focus on safety, businesses are rethinking how their equipment supports smaller teams. There’s a rising demand for ergonomic tools and maintenance-free solutions that reduce physical strain and staffing needs.
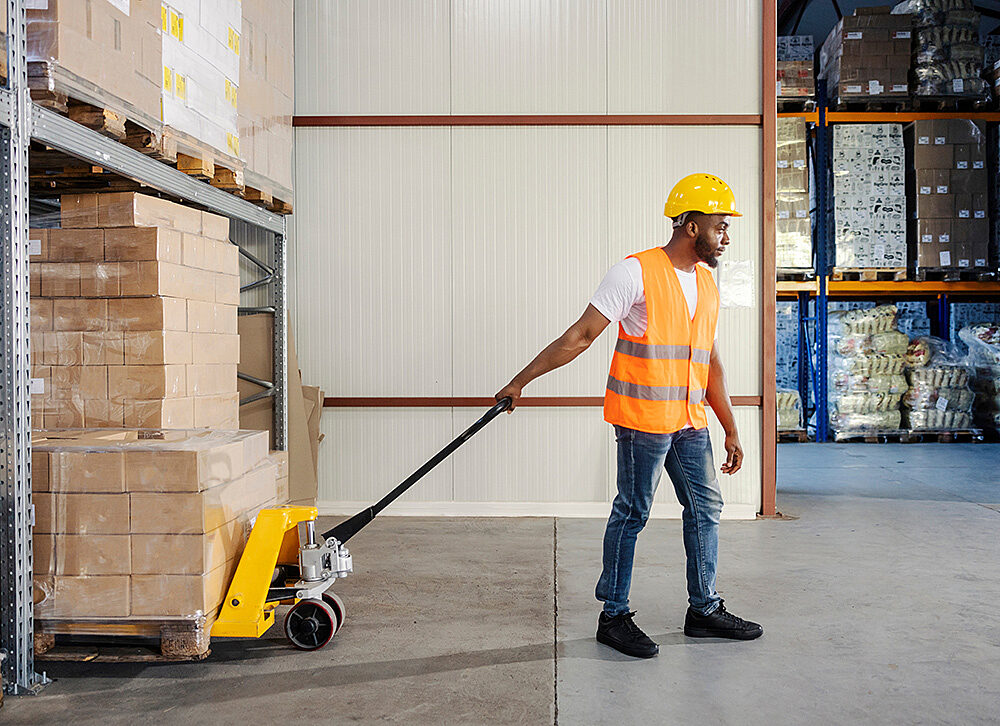
A Need for Flexibility and Scalability
The ability to pivot quickly is now a competitive advantage. From modular carts to mobile shelving, material handling equipment must be able to adapt to changing workflows, facility layouts, and operational priorities.
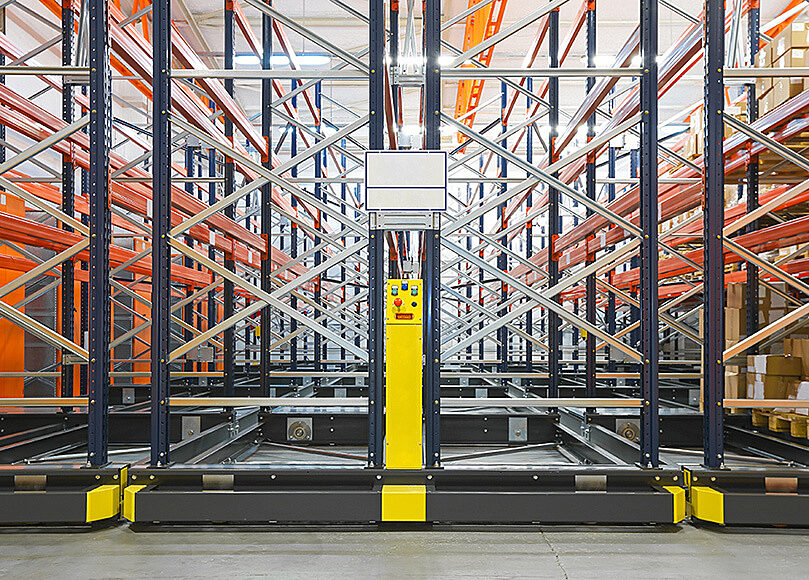
How Industry Leaders Are Responding
Teams that are thriving despite today’s challenges are doing more than just adjusting—they’re rethinking their approach altogether. Here’s how.
Revamping Procurement Strategy

Longer-term price agreements, larger volume orders, and closer partnerships with vendors are helping companies stay ahead of volatility. Bulk purchasing and price locking are becoming standard tactics.
Investing in Long-Term Value
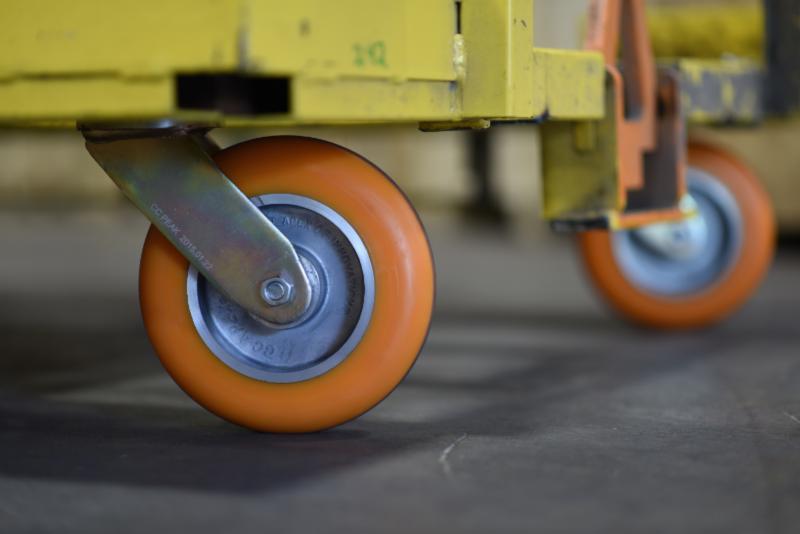
Instead of choosing the cheapest equipment, smart buyers are evaluating total cost of ownership. Durable, low-maintenance components like high-performance casters reduce downtime and extend replacement cycles.
Shifting Toward Maintenance-Free and Automated Solutions
As labor becomes harder to find, demand is growing for products that reduce manual input. Maintenance-free casters, for example, support automation and eliminate lubrication schedules, saving time and labor costs over the long term.
Prioritizing Sourcing Resilience
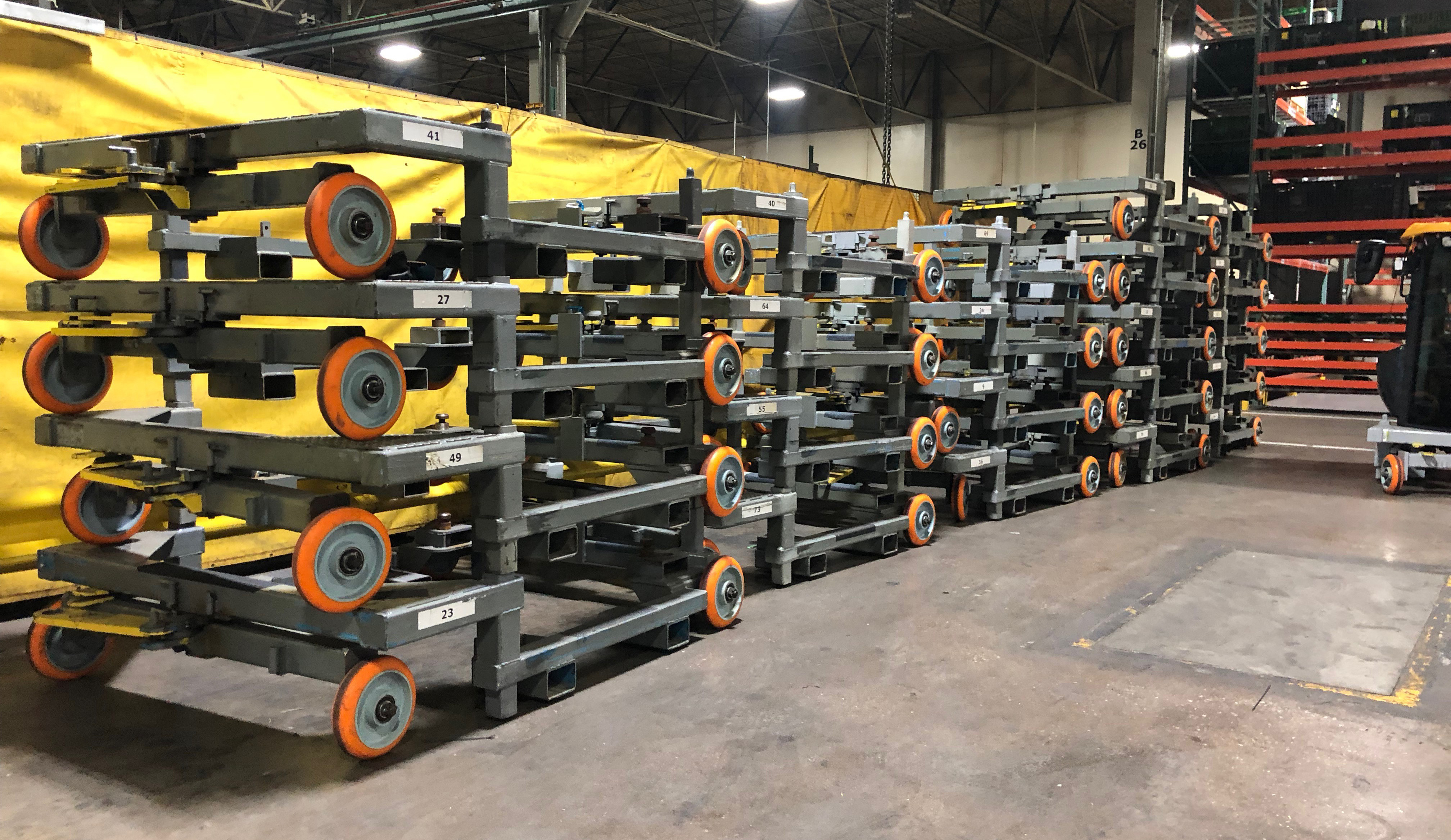
Working with partners who offer domestic sourcing, faster lead times, and proactive service is no longer optional. Companies like Caster Connection help reduce uncertainty with dependable product availability and responsive support.
Where Material Handling is Headed Next
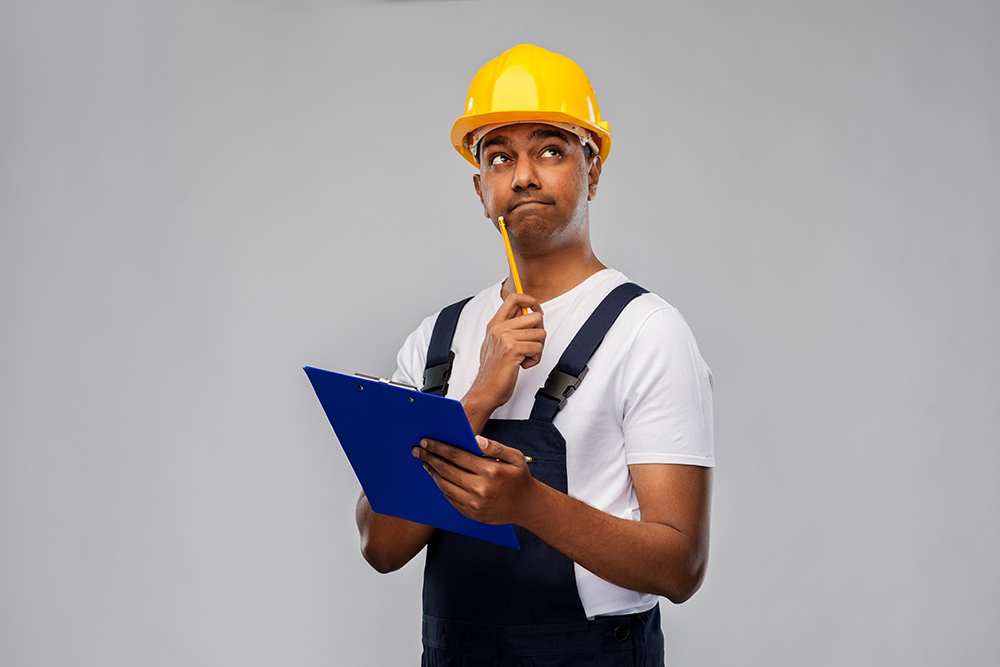
The challenges facing manufacturing and logistics today are accelerating innovation across the board. Companies that want to stay competitive are paying attention to the trends shaping the next generation of material handling—because those trends are already here. The key is not just knowing what’s coming, but planning for how to respond.
Autonomous Mobility
More operations are deploying automated guided vehicles (AGVs) and autonomous mobile robots (AMRs) to handle repetitive, high-volume tasks. This shift is increasing the demand for casters that work seamlessly with guided systems and support consistent, low-resistance movement.
Predictive Intelligence
Digital twin modeling and predictive maintenance tools are helping facilities monitor wear, forecast failures, and plan repairs with greater precision. Casters and components that integrate into smarter maintenance ecosystems are gaining traction.
Ergonomic Investment
As labor shortages continue, ergonomic improvements are no longer optional. From low-resistance casters to maintenance-free solutions, businesses are investing in equipment that protects workers and reduces injury-related downtime.
Sustainable Design Priorities
More companies are choosing equipment that lasts longer, reduces waste, and meets environmental goals. This includes recyclable materials, modular components, and products built for longevity over disposability.
Operational Visibility and Uptime
Real-time tracking, system-wide performance monitoring, and equipment standardization are becoming essential. Downtime is more expensive than ever, and every component needs to support uninterrupted performance.
Resilience is the New Competitive Edge
The companies that will thrive in this new environment are the ones willing to adapt. That means embracing flexible systems, investing in durable components, and working with partners who understand how the landscape is changing. Even something as small as a caster can make a measurable difference when you're working to reduce downtime, control costs, and keep operations running smoothly.
If you're navigating supply chain challenges or rethinking your procurement strategy, we’re here to help. Our team can recommend durable, future-ready caster solutions built to support your goals today and into the future. You can start by booking a Caster Needs Evaluation, exploring material handling solutions, or talking with one of our specialists about your current setup.
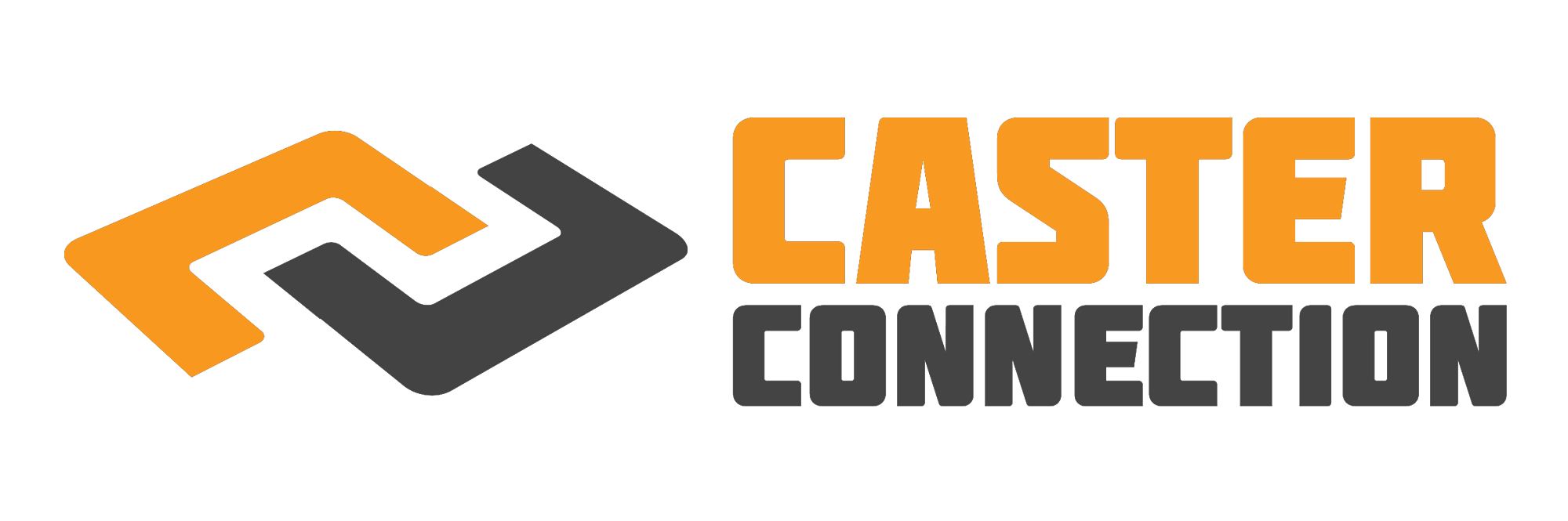