Why Choosing the Right Load Capacity Matters When Steel Costs Are Rising
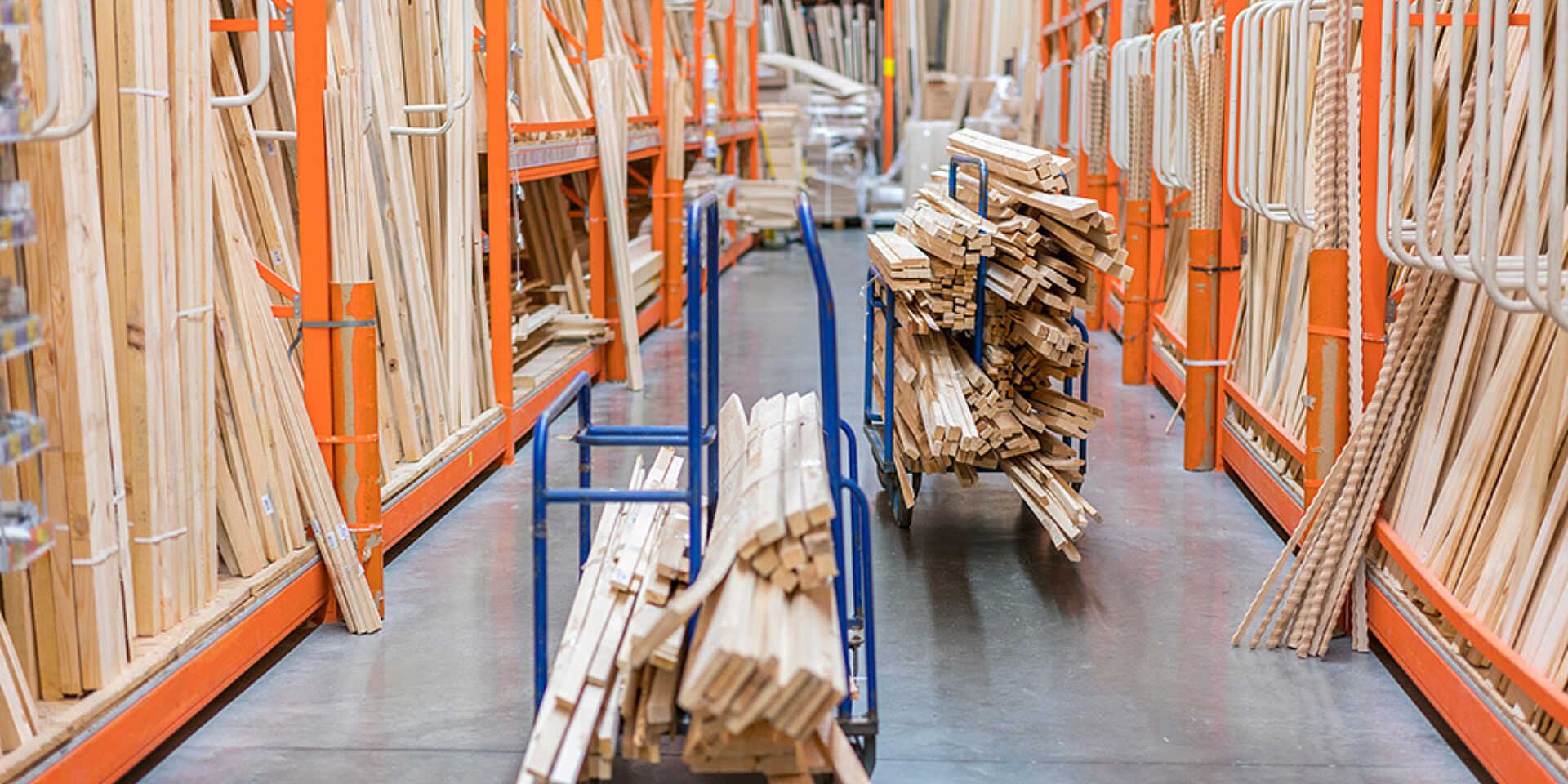
Steel prices are climbing, and operations teams are under pressure to stretch every dollar. While it might seem safer to choose the most heavy-duty caster available, overspecifying your equipment can actually cost you more in materials, labor, and efficiency.
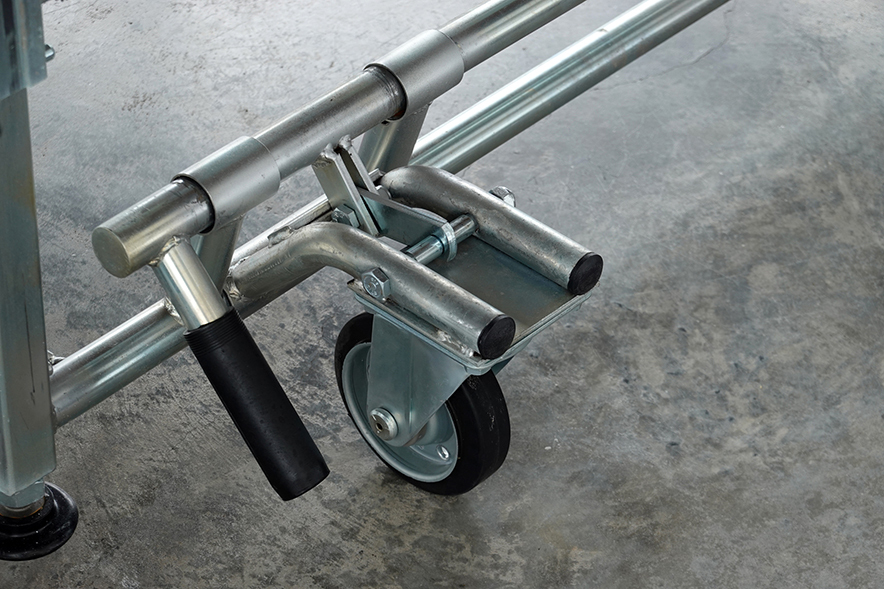
At Caster Connection, we focus on precision. Choosing a caster that’s too strong for the job wastes steel, inflates costs, and adds unnecessary strain to your operation. In this blog, we’ll explain what load capacity optimization really means, why it matters now, and how getting it right can help you reduce costs without sacrificing performance or safety.
Why the Right Load Capacity is Important
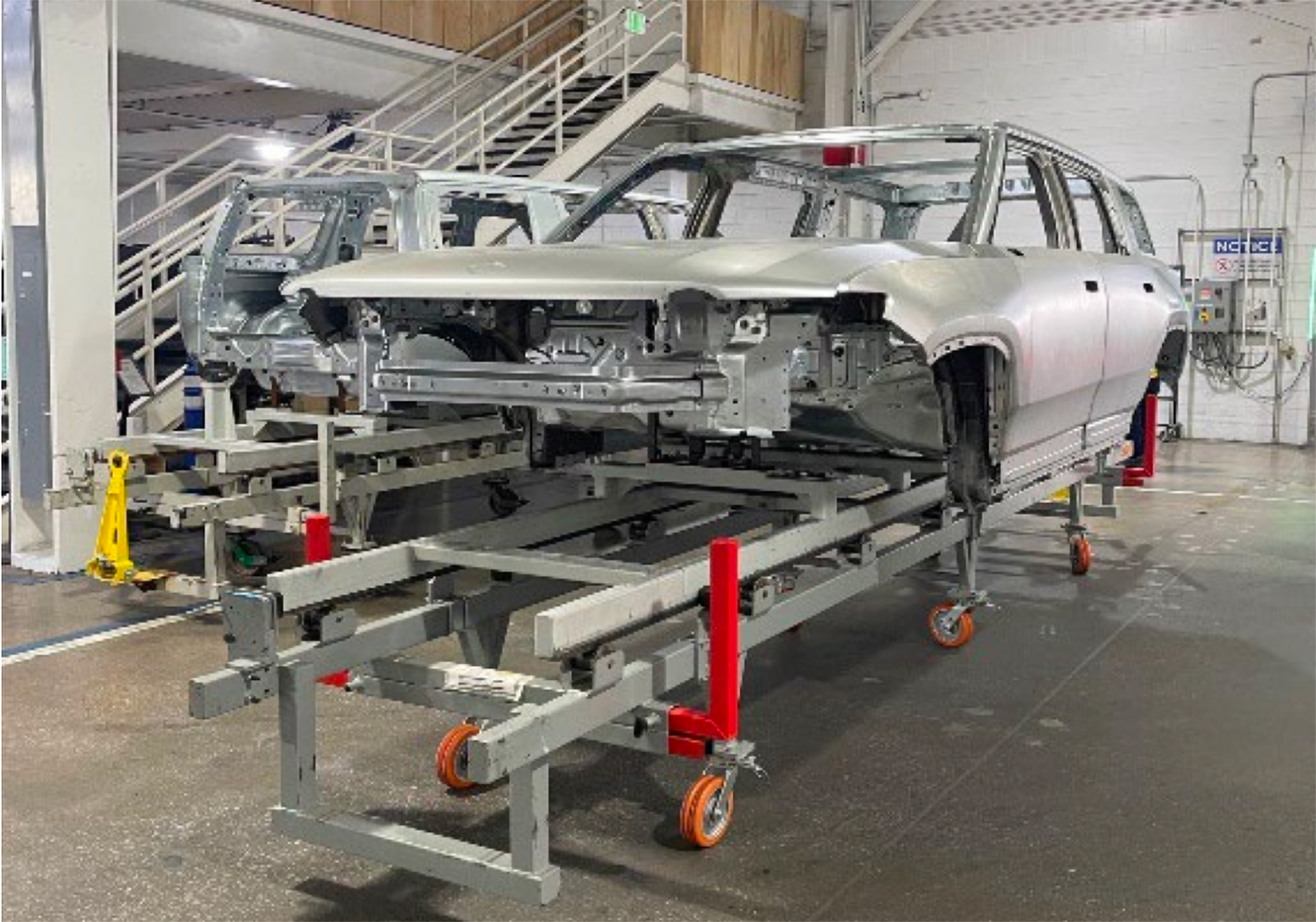
Choosing the right load capacity means selecting a caster that supports your application’s weight requirements without adding unnecessary bulk or cost. It’s about covering your equipment’s full load requirements without overshooting the safety margin and inflating spend.
Casters are rated to carry specific weight ranges:
-
Light-duty: 100 to 300 pounds
-
Medium-duty: 300 to 1,200 pounds
-
Heavy-duty: 1,200 to 5,000 pounds or more
Specifying a caster with more load bearing capacity than needed often results in higher steel usage, increased rolling resistance, and inflated costs. The goal isn’t the biggest caster. It’s the most efficient one for the job.
Why Overspecifying Casters Adds Unnecessary Costs
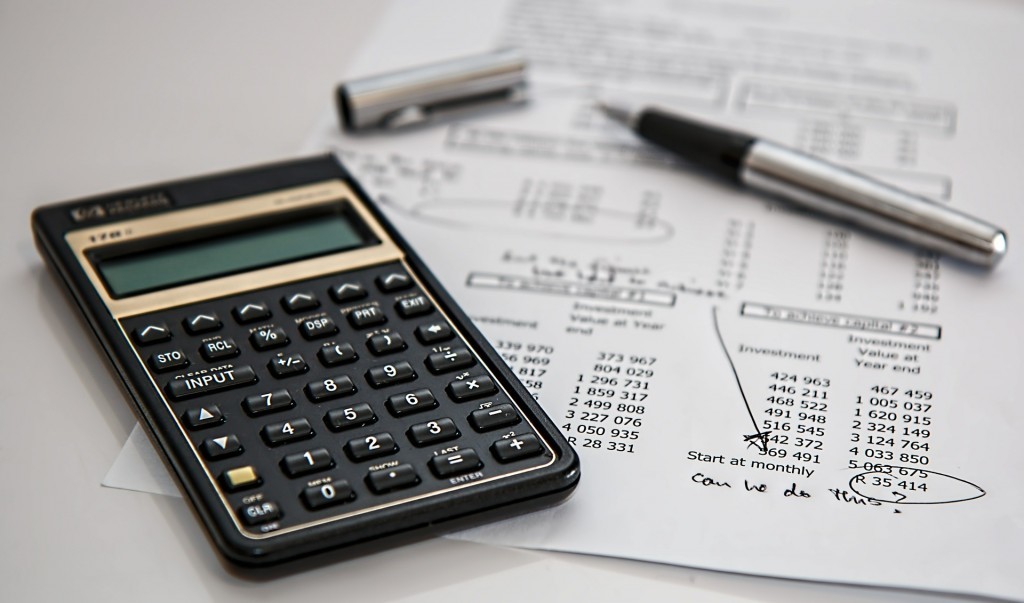
Choosing a caster with more capacity than your application requires might seem like a safe move, but it often leads to wasted materials, higher ergonomic strain, and added complexity. Overspecification doesn’t just increase upfront costs — it affects how your equipment performs and how efficiently your operation runs.
Higher Material Usage Means Higher Cost
Heavy-duty casters require more steel, thicker rigs, and stronger wheels. These materials drive up price, especially when multiplied across hundreds of carts or equipment.
More Rolling Resistance
Bigger casters aren’t always easier to move. Added weight and overbuilt components increase push and pull effort, slowing workflows and increasing the risk of ergonomic injuries.
Inventory Complications
Using oversized casters where they’re not needed leads to more SKUs and more complexity in procurement and maintenance. Streamlining caster specs improves stocking and simplifies replacements.
How to Right-Size Caster Load Capacity
Specifying the correct load capacity starts with understanding how your casters are actually used. It’s not enough to rely on general duty classifications or assumptions about safety buffers. By calculating the load each caster supports and accounting for real-world conditions, you can choose the most efficient and cost-effective option for the job.
1. Know Your Load Per Caster
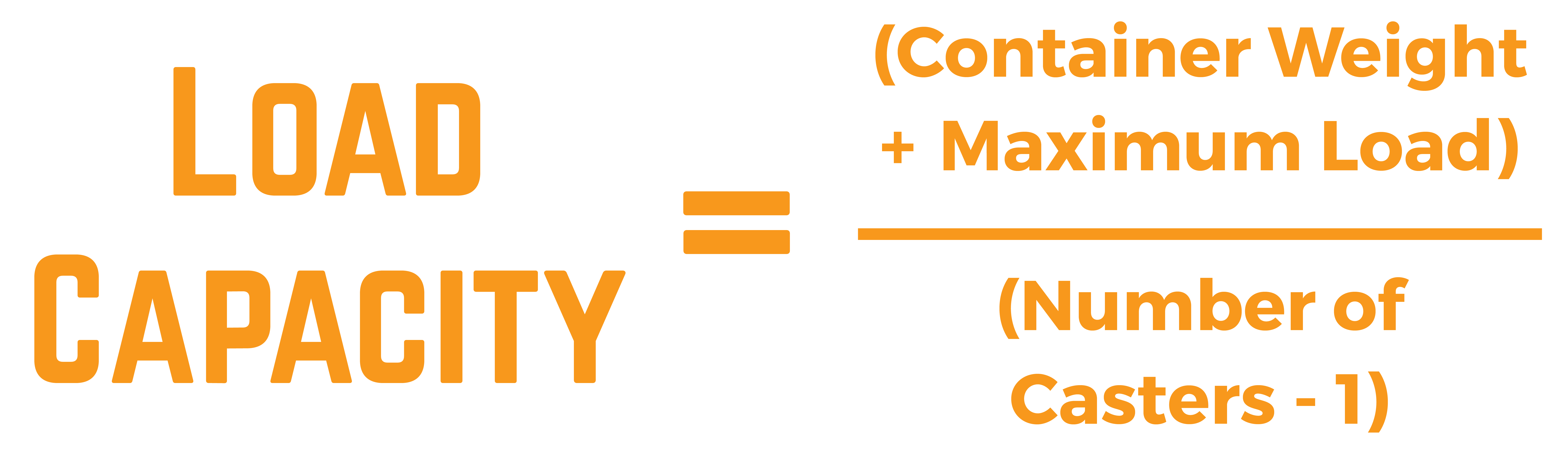
To calculate required capacity, add the weight of your equipment to the maximum load it will carry, then divide that total by the number of casters minus one. This gives you the minimum load rating each caster should support, with a built-in safety margin to prevent overload.
2. Consider the Application Environment
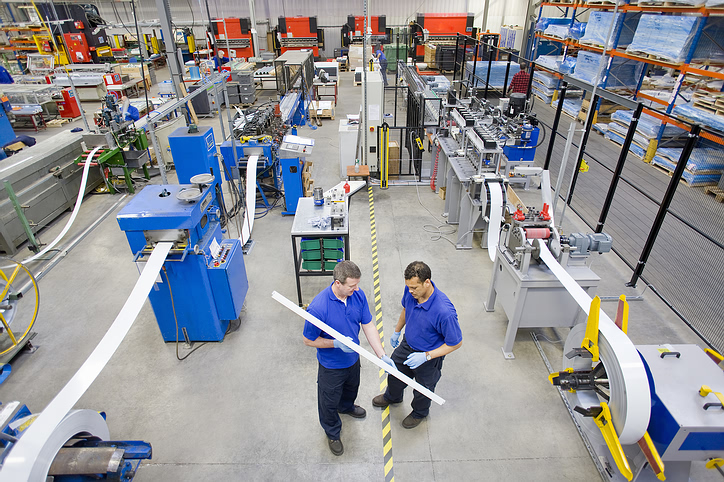
Will carts be in constant use or moved occasionally? Are they powered by AGVs or pushed manually? What’s the condition of the floor? These factors help determine how much capacity you really need.
3. Choose the Right Product Line

Caster Connection offers a range of solutions to match load needs with ergonomic performance:
-
CC Apex: Ideal for light to medium loads, with smooth rolling and reduced push/pull force
-
CC Apex HD: Built for medium to heavy loads while preserving ergonomic benefits
-
CC Stout: Designed for high-impact environments and heavy loads with minimal maintenance
-
CC Nexus: A modular caster system for AGVs and AMRs that reduces battery draw and allows flexible load tuning across applications
Case Study: Cutting Cost Without Compromising Performance
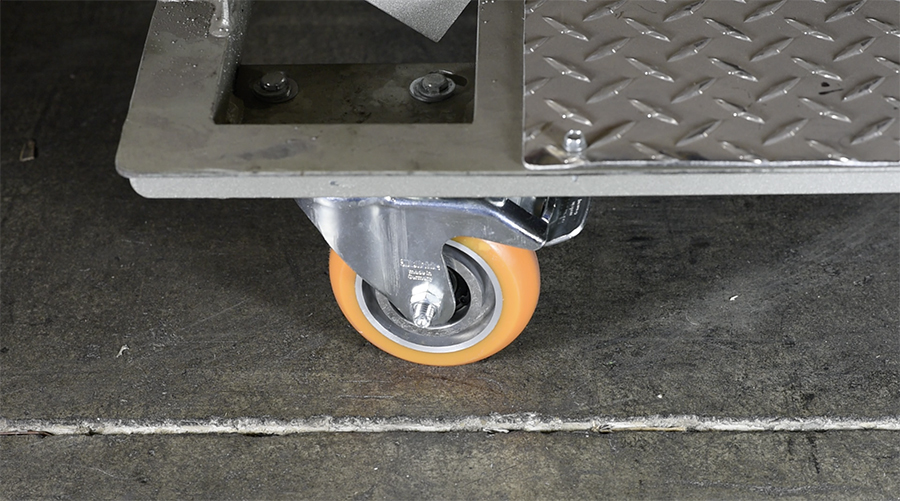
A warehousing operation was using 2,000 lb-rated casters on carts carrying only 600 lbs. After a Caster Needs Evaluation, we recommended switching to CC Apex casters rated at 900 lbs—more than enough for their actual load.
Results:
-
28% savings on caster cost
-
Better rolling performance and less operator strain
-
Faster lead times and improved inventory flexibility
Precision Pays Off
In a high-cost market, overspending on raw materials doesn’t just stretch your budget. It slows down your entire operation. Choosing casters with the right load capacity helps reduce waste, improve ergonomics, and boost efficiency across your facility.
If you're not sure whether your current spec is working for you, we can help. Schedule a Caster Needs Evaluation, speak with a Caster Nerd, or explore our Caster Education page.
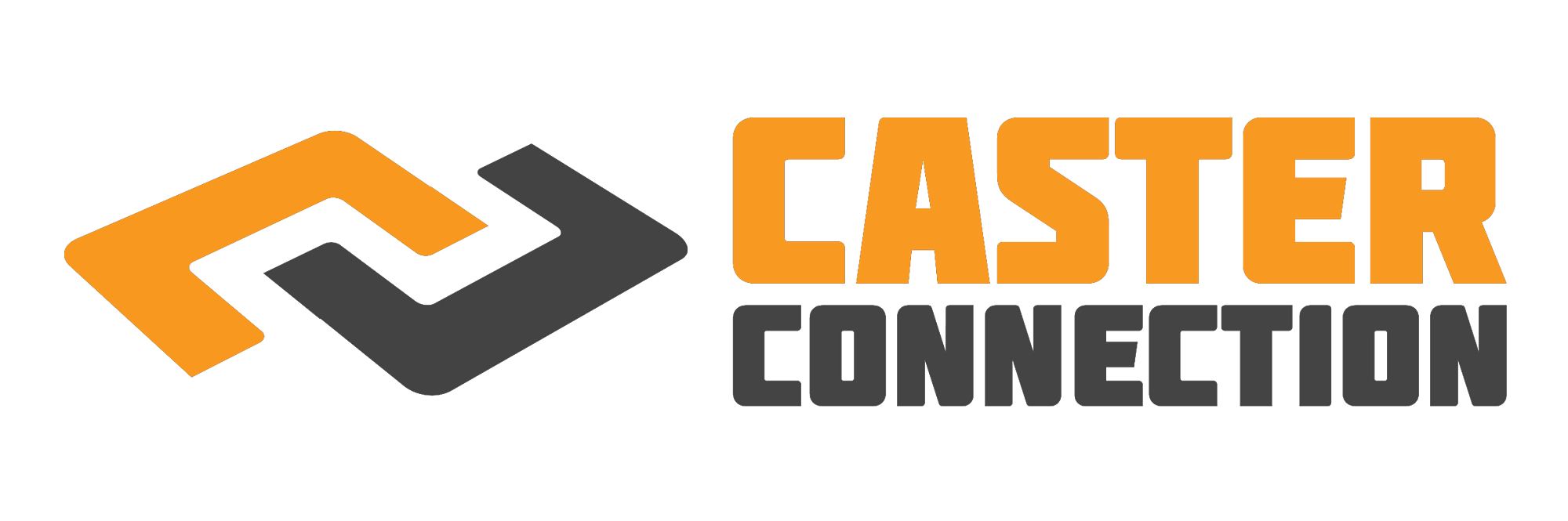