How Bad Casters Cause Downtime in Material Handling
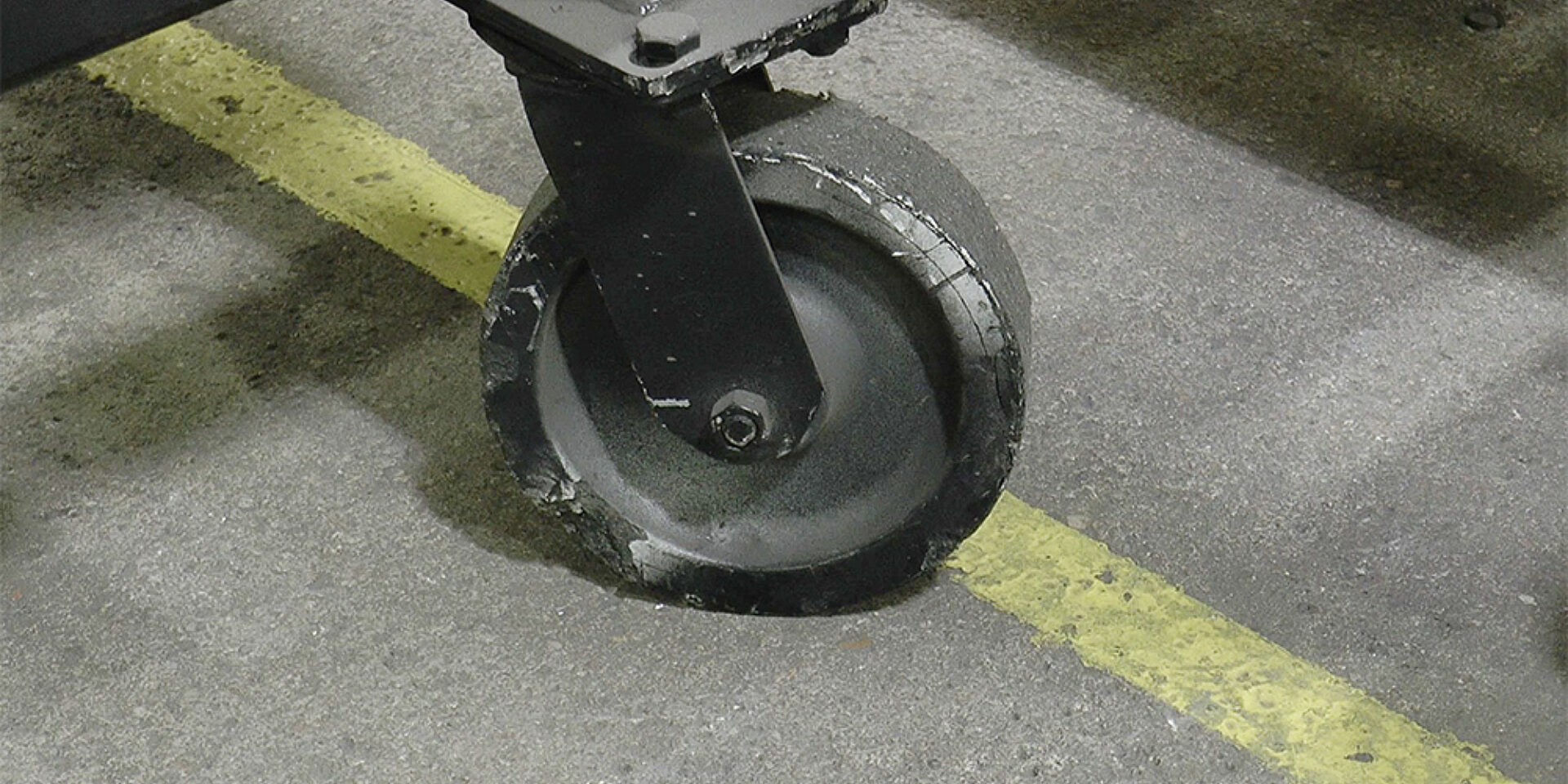
In fast-moving manufacturing and industrial environments, downtime doesn’t just slow you down. It compounds across the operation. Missed deadlines, idle labor, damaged equipment, and safety incidents all pile up quickly. And while most facilities focus on optimizing machinery and software, many overlook one of the most preventable sources of disruption: casters.
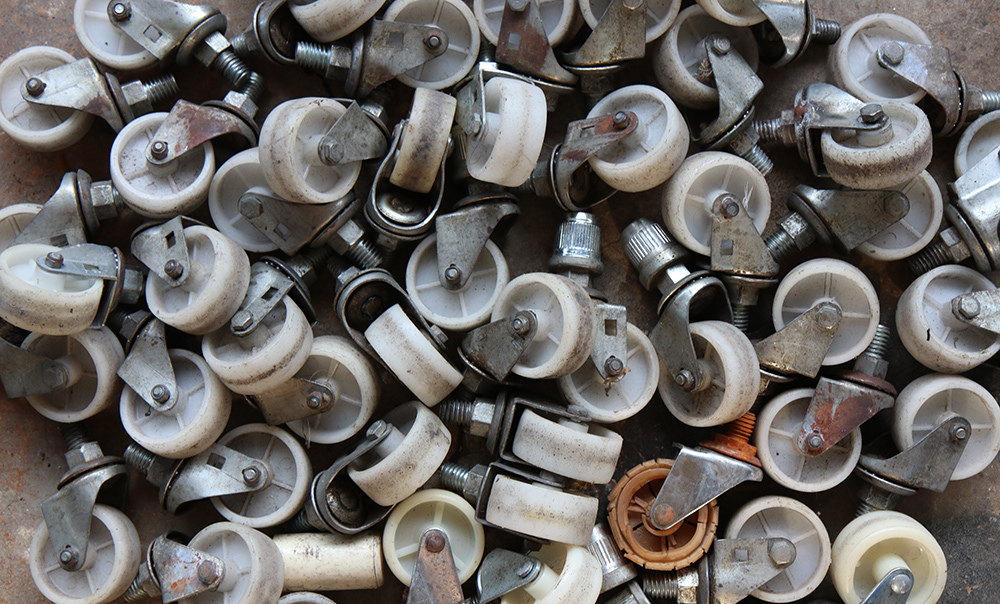
If your casters aren’t moving, neither is your team. This blog explores how mobility breakdowns impact productivity and what you can do to stop them before they start.
What Downtime is Really Costing You
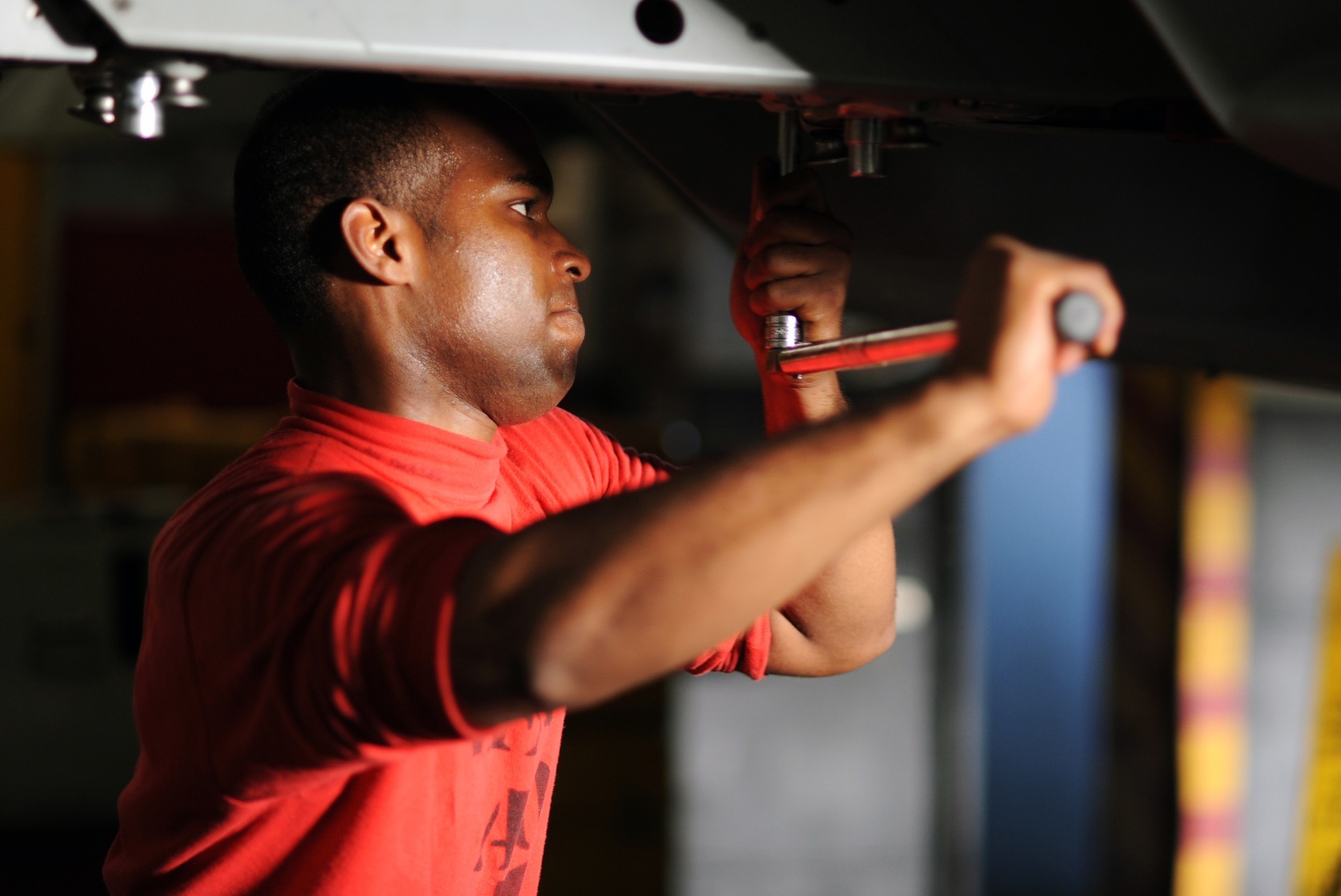
Downtime doesn’t always show up as a line item, but it drains your operation in ways that are easy to miss and hard to recover from. Every delay caused by mobility issues triggers a ripple effect. It slows output, exhausts teams, increases damage risk, and compromises safety. And most of the time, it’s completely preventable.
- Lost Production Time: When carts or equipment can’t move efficiently, workflows stall. Pulling carts offline to replace casters can delay an entire line.
- Labor Inefficiency: Workers are forced to compensate for poor mobility, leading to slower output, higher fatigue, and mounting frustration.
- Equipment and Floor Damage: Dragging unstable carts can damage components, tools, and facility floors. This leads to additional repair and replacement costs that eat into your maintenance budget and slow production.
- Increased Injury Risk: Difficult-to-maneuver carts raise the likelihood of musculoskeletal injuries and workers’ comp claims.
Why Caster Performance is Critical
Casters might not be the flashiest part of your operation, but they are one of the most influential. When mobility breaks down, everything from safety to throughput is affected. High-performing casters don't just roll better. They help your people, processes, and equipment operate as intended.
Casters Are the Foundation of Material Movement
Every process that depends on moving product—whether it's picking, staging, packing, or assembly—relies on carts that move easily. One worn-out or underperforming caster can jam an entire workflow, delay output, or put strain on adjacent teams trying to compensate.
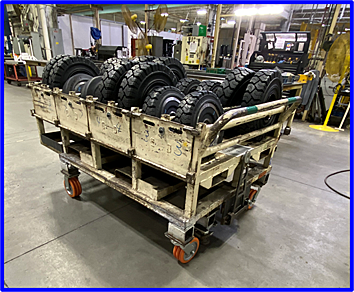
Poor Ergonomics Slows Everything Down
Casters that drag, resist, or wobble require more effort to push and steer. That extra resistance leads to fatigue, slows down cycle times, and increases the risk of injuries. Over time, this results in lower throughput, missed targets, and more physical strain on your team.
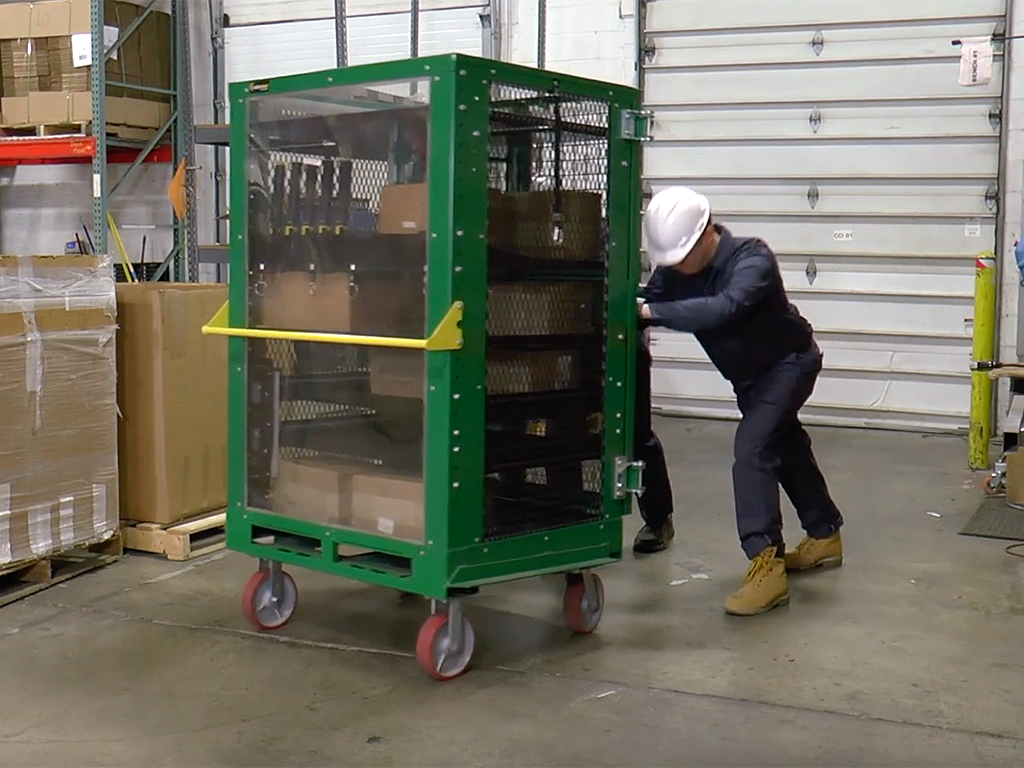
Low-Quality Casters Drain Maintenance Resources
Budget casters often fail early, especially in high-use environments. That leads to more service calls, more replacement cycles, and more unscheduled downtime. Every repair pulls time and attention away from higher-priority tasks and increases operational costs.
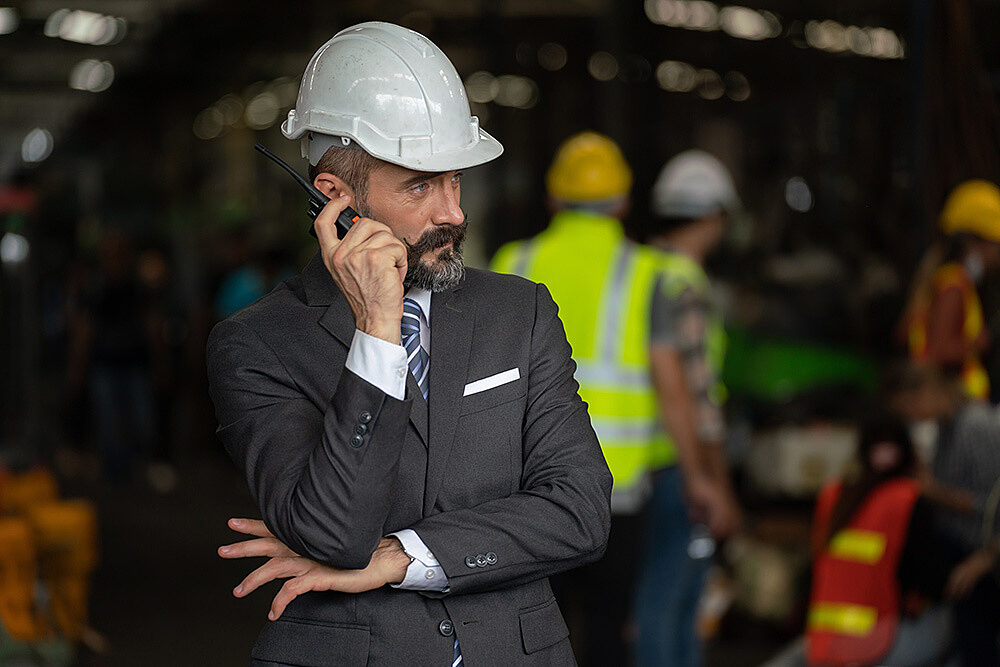
Common Causes of Caster-Related Downtime
Not all caster problems are random. Here are the most frequent culprits:

Overloaded Casters
Choosing a caster that can't support the load will lead to early failure.

Mismatched Materials and Floor Conditions
Hard wheels on soft floors, or vice versa, result in poor performance, damaged flooring, and faster wear.

Bearing Failure from Poor Maintenance
When swivel sections aren’t kept clean and lubricated, bearings can seize, making carts harder to move and more likely to fail under load.

Low-Quality Components
Budget casters break down quickly and can’t keep up with daily operational demands.
How to Prevent Downtime and Improve Mobility
Most caster-related delays can be avoided with the right strategy. That starts with selecting the right equipment, keeping it in working order, and identifying small issues before they become big problems. These four steps can help you eliminate mobility bottlenecks and keep your operation moving.
1. Choose the Right Casters for Your Application
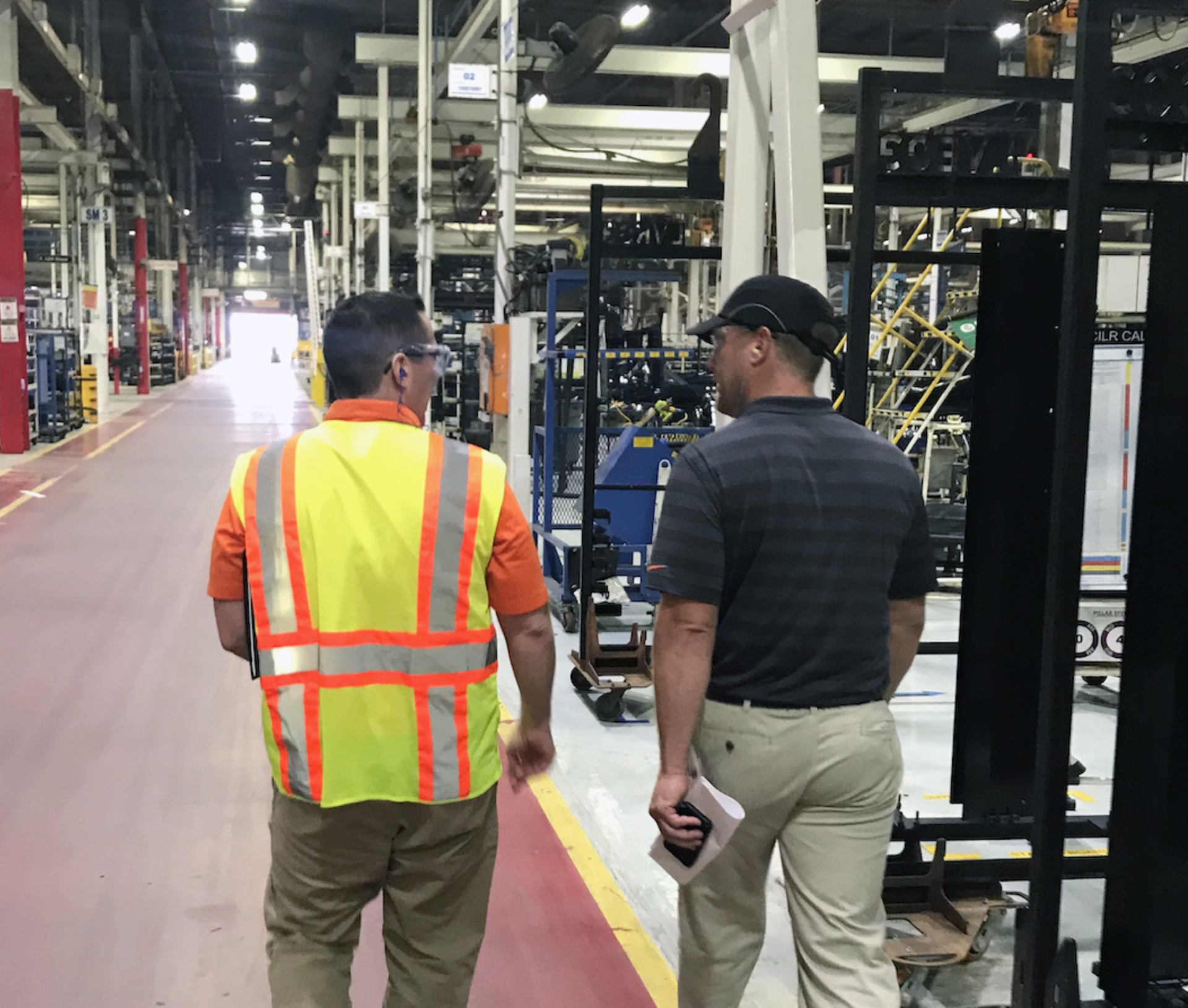
Work with a caster expert to match the right product to your floor conditions, load weight, movement frequency, and environmental hazards.
2 Upgrade to High-Performance Casters
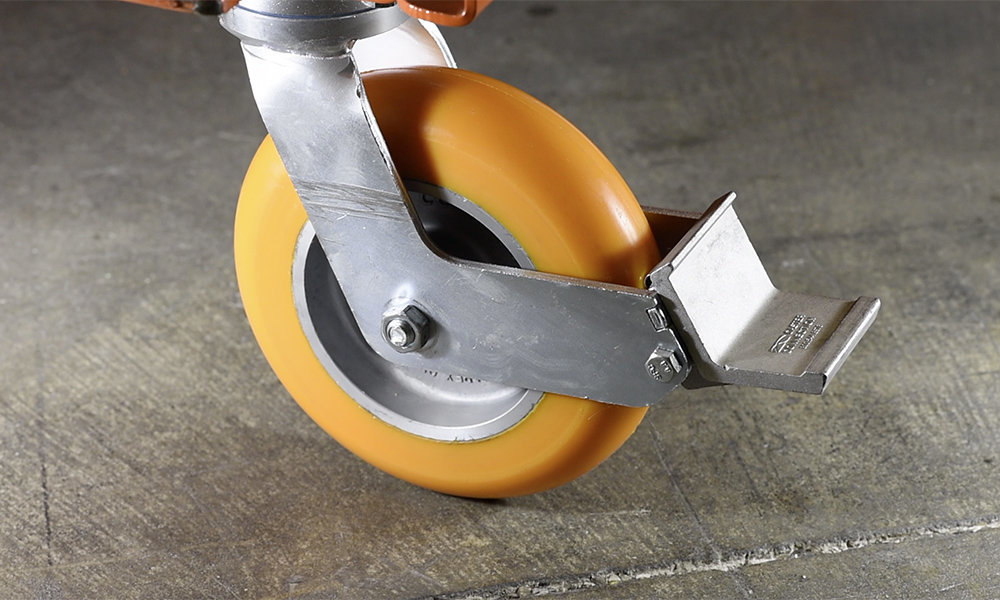
Caster Connection’s CC Apex and CC Stout are built to deliver long-lasting performance with low rolling resistance and high impact tolerance.
3. Implement Preventative Maintenance or Go Maintenance-Free
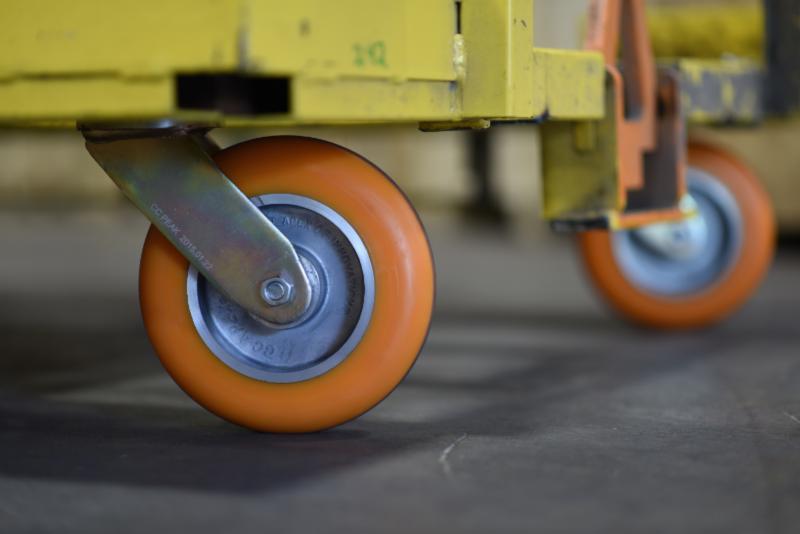
Establish a caster inspection schedule or switch to sealed, maintenance-free casters like the CC Peak to reduce labor and increase uptime.
4. Schedule A Caster Needs Evaluation
Let Caster Connection audit your carts and mobility systems to identify risks, inefficiencies, and areas for improvement.
Real-World Impact: One Bad Caster, One Big Delay
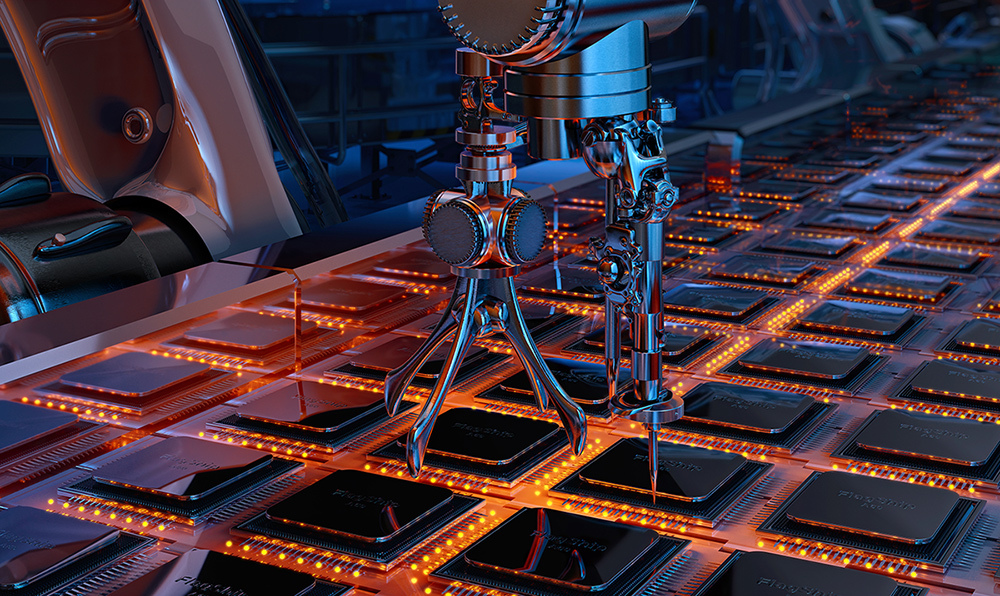
A global electronics manufacturer faced frequent line stoppages caused by failing casters on carts carrying sensitive components. After upgrading to sealed precision-bearing casters matched to the actual load requirements, the company saw:
-
80 percent reduction in caster-related delays
-
Shorter takt times on key production lines
-
Fewer ergonomic complaints from operators
Don't Let Small Wheels Create Big Problems
When your mobility breaks down, so does everything else. Casters directly affect productivity, safety, and operational costs—but they’re also one of the easiest places to make measurable improvements. With the right caster strategy, you can eliminate preventable delays and keep your operation moving smoothly.
If you're ready to identify weak points in your mobility system, we’re here to help. Start by booking a Caster Needs Evaluation, exploring high-performance caster options, or talking to a mobility expert about your current challenges.
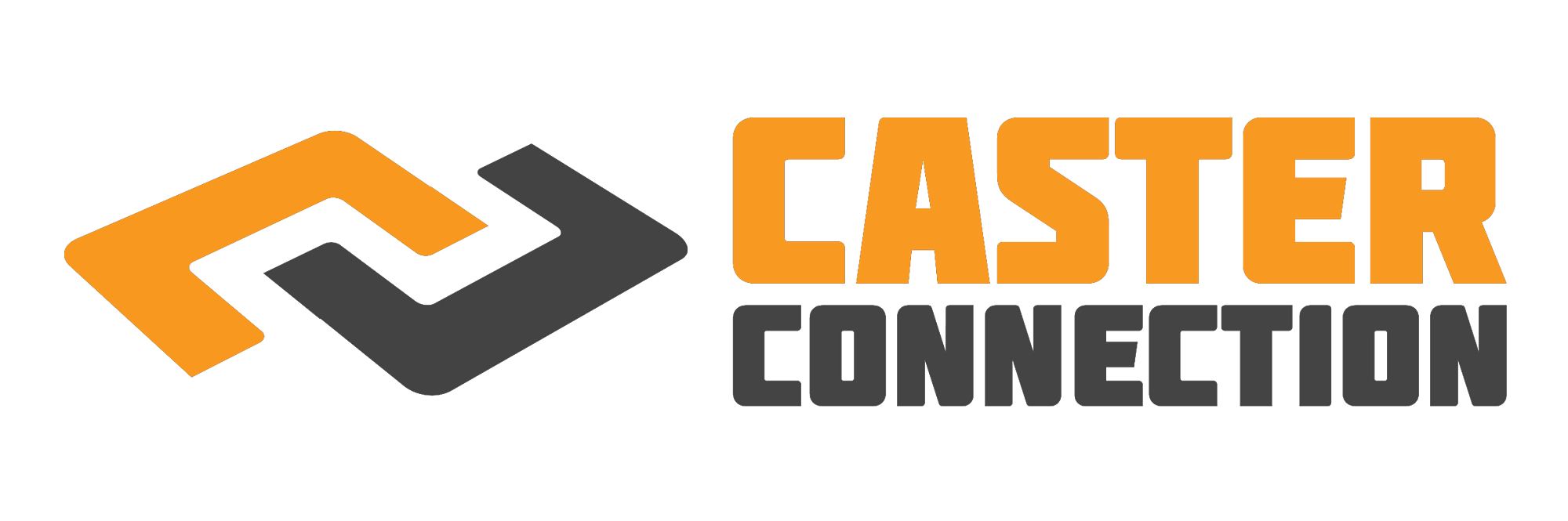