Conductive and Dissipative Casters: Two Different Solutions for Static Discharge
In many industrial, technology-centric, or sensitive environments, static electricity is a major problem, particularly when moving products on carts that have casters. Companies combat this problem with specially designed caster wheels. Caster experts use the terms “conductive” or “electrostatic dissipative” caster wheels to describe casters that diminish or eradicate static electricity in different ways.
The Challenge of Static Electricity
As your carts move around your facility on casters, they generate static electricity. If there is no path for this electricity to dissipate, the carts retain this static electricity. When this electricity transfers from one thing to another, from a cart to an associate, for example, this is called electrostatic discharge.
This electrostatic discharge can damage valuable electrical components. It can also ignite gases and affect clean rooms and medical areas by causing dust particles to cling together, which prevents the dust particles from entering filtration systems. Static-eliminating caster wheels will prevent these risks and protect your team members from unnecessary shocks.
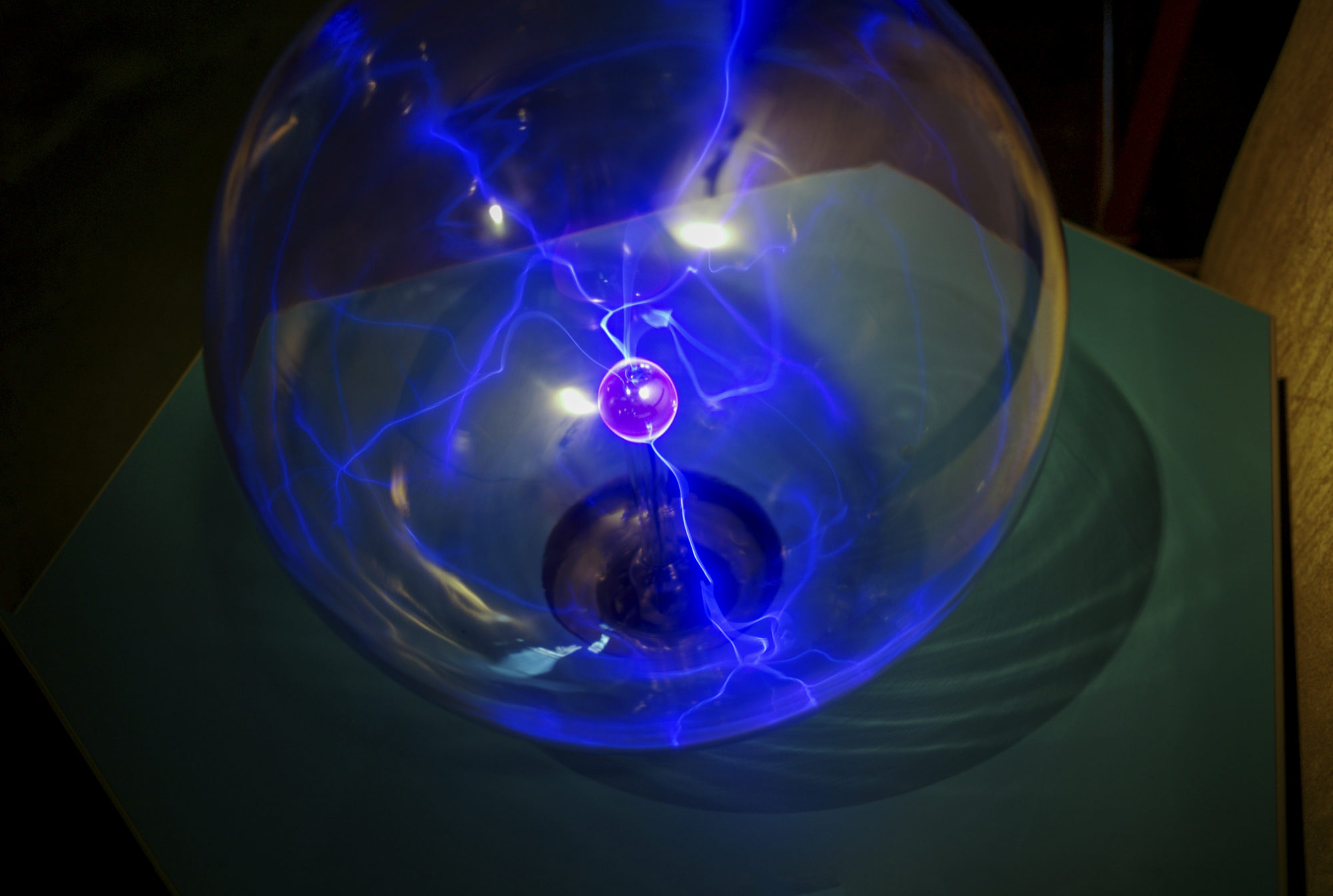
Two types of static-eliminating caster wheels
It is important for you to understand the specific strengths and limitations of each type of static-eliminating caster wheel. Static-eliminating wheels come in two different types: conductive and electrostatic dissipative.
In layman's terms, the main difference between conductive and electrostatic dissipative wheels is the speed at which electron charges flow through the caster tread.
A conductive wheel, which has a lower resistance to ohms, means the charge will quickly dissipate through the wheel tread. Conductive caster wheels offer the highest protection for electrical environments.
An electrostatic dissipative wheel has a higher resistance, so the current of electrons moves slower through the tread, in a more controlled manner. Electrostatic dissipative caster wheels provide enough protection for most applications and also give you the flexibility to use casters that are highly versatile for many industrial applications.
So if an end user needs a quick flow due to high sensitivity of the application, they may choose a conductive wheel whereas other end users do not need that kind of flow of electrons, so an electrostatic dissipative wheel is the better option for them.
Conductive Caster Wheels
Conductive caster wheels, such as the Blickle 50mm Electrically-Conductive TPR Swivel Caster, are made from conductive material, that is, material that conducts electricity from the wheel into the floor. These wheels are manufactured from materials that have low resistance to electrical flow, such as rubber or polyurethane, in many sizes and load ratings.
Conductive caster wheels have a surface resistivity of equal to or greater than 10^3 ohms, but less than 10^5 ohms. They offer the best protection against electrostatic discharge.
Advantages
- Offer the highest protection against electrostatic discharge
- Excellent shock absorption (soft ride)
- Quiet ride
Disadvantages
- High cost
- Not suitable for clean rooms
- Possibly long lead times
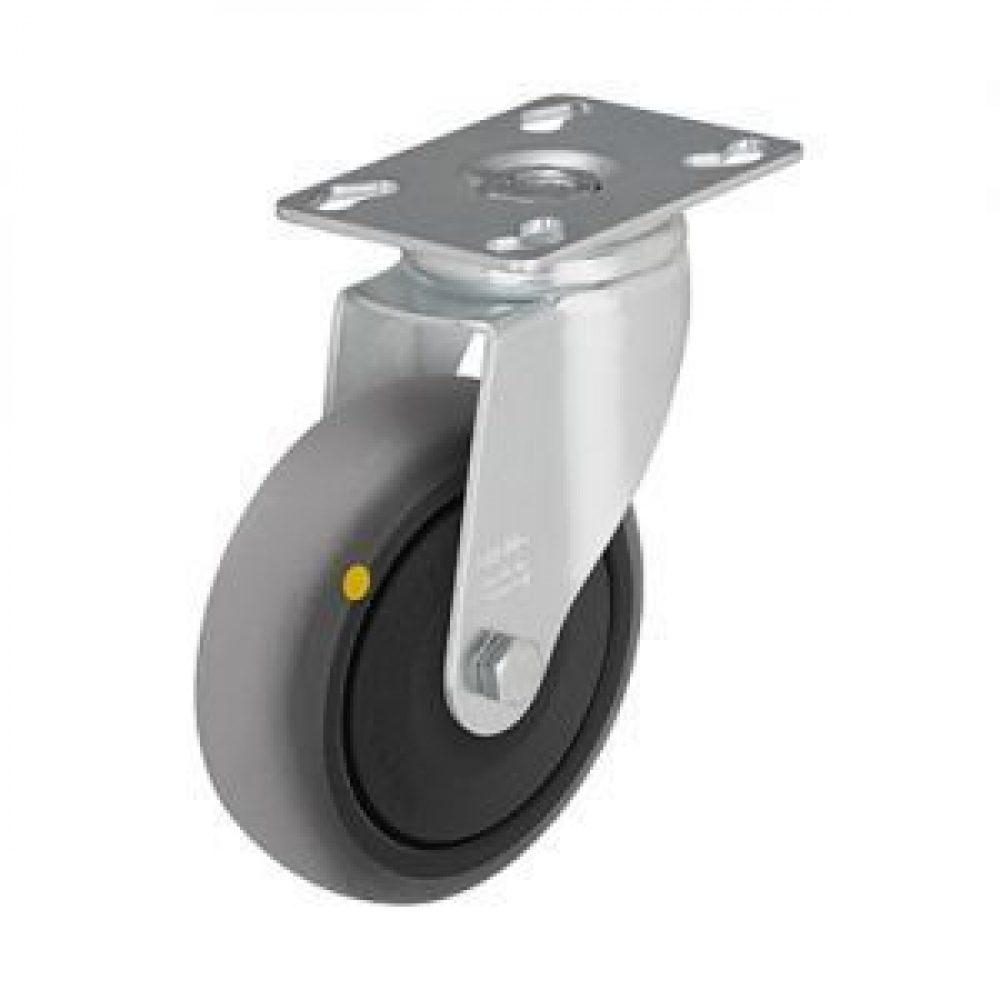
Electrostatic Dissipative Caster Wheels
Electrostatic dissipative caster wheels, such as the CC Apex ESD, are made from material that conducts electricity, but not as efficiently as conductive materials do. A chemical compound is added to the tread compound to make the tread - polyurethane or rubber - electrostatic dissipative. The static dissipative material has medium resistance to electrical flow.
Electrostatic dissipative caster wheels have a surface resistance of > 105 < 1012 Ohms. They offer the next-best level of protection against electrostatic discharge (after conductive caster wheels).
Advantages
- Good protection against electrostatic discharge
- Medium shock absorption
- Quiet ride
- More cost effective
- Readily available
Disadvantages
- Do not offer the highest protection against electrostatic discharge
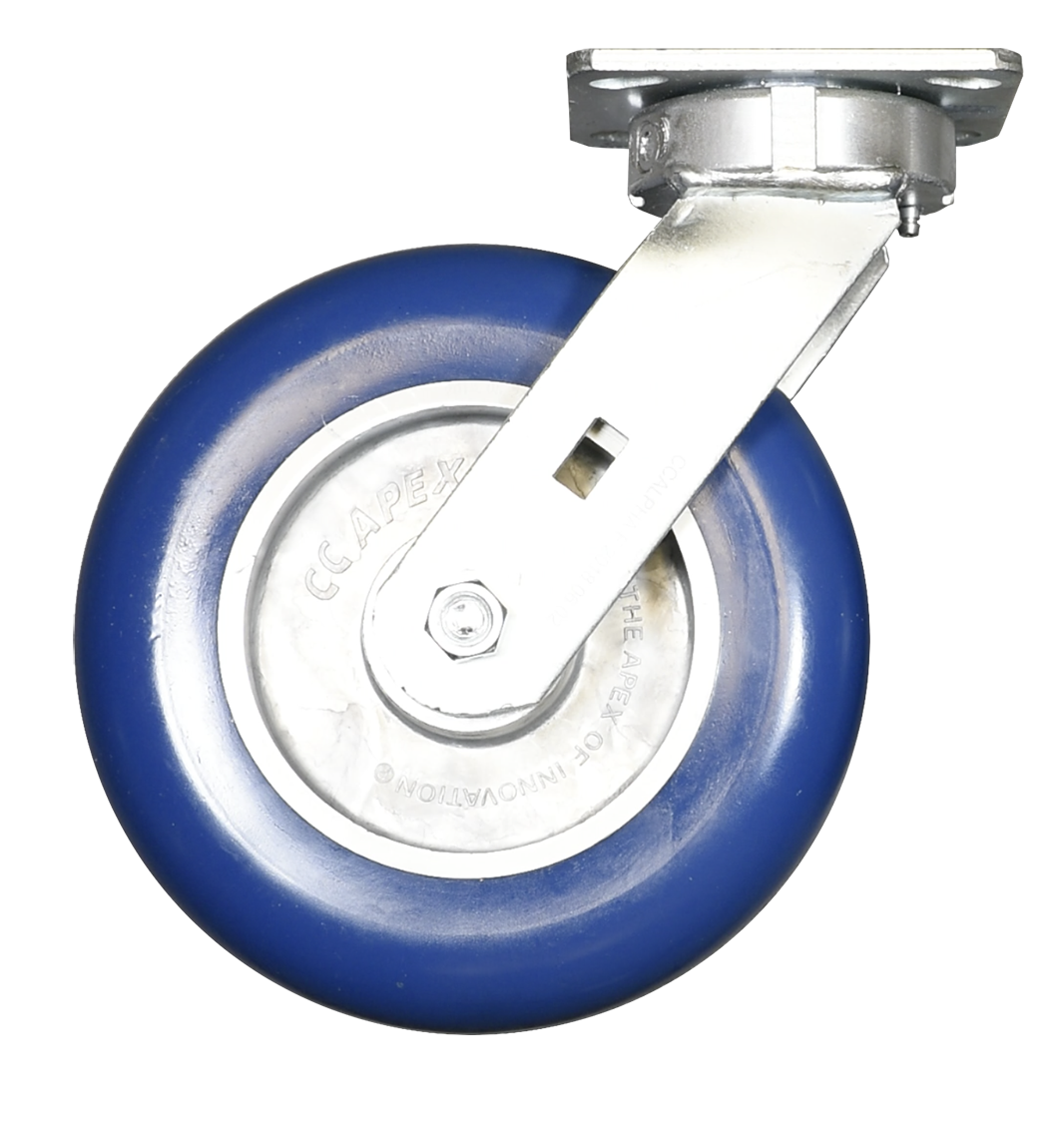
Conductive vs. Electrostatic Dissipative Caster Comparison
|
Conductive Caster Wheels |
Electrostatic Dissipative Caster Wheels |
Electrostatic Discharge Protection |
Best |
Excellent |
Surface Resistivity |
> 103 < 105 Ohms |
> 105 < 1012 Ohms |
Material |
Neoprene Rubber, Polyurethane |
Polyurethane |
Shock Absorption |
Excellent |
Good |
Quiet Ride? |
Yes |
Yes |
Mark Floors? |
Yes, No (Poly) |
No |
Suitable for clean rooms? |
No |
Yes |
Shelf life |
High |
High |
Conclusion
To prevent static electricity, you really have two options: conductive and electrostatic dissipative. Besides these specific strengths, conductive casters are on average more expensive and because they are used more rarely, they normally have a lead time from 8 to 10 weeks, so if you need casters quickly, electrostatic dissipative caster wheels are a better option in most cases. What it comes down to is options. Make your decision based on your specific situation and environment.
If you'd like someone to partner with you to make sure you have the perfect ESD caster, get in touch with an expert at Caster Connection. We will help you make the choice that fits your unique situation and budget.