Most Advanced Manufacturing Facility In The World
Judging by the “Tesla Motors” video published by Wired, the Tesla Factory appears to be the cleanest, most cutting-edge, and advanced manufacturing facility to date. The Tesla Factory is a great representation of smart manufacturing and how technological advancements can be implemented to achieve successful digital manufacturing.
WHAT IS THE NUMMI PLANT?
NUMMI (New United Motor Manufacturing, Inc.) was an automobile manufacturing company jointly owned by General Motors and Toyota from 1984 until 2010. The size of the NUMMI plant stretches out to 5.3 million of square footage and with the latest buzz of the Tesla Factory’s expansion, it is looking to double that size to accommodate 14,000 workers and make room for activities. The NUMMI plant utilizes advanced manufacturing technology to enhance their Tesla production process.
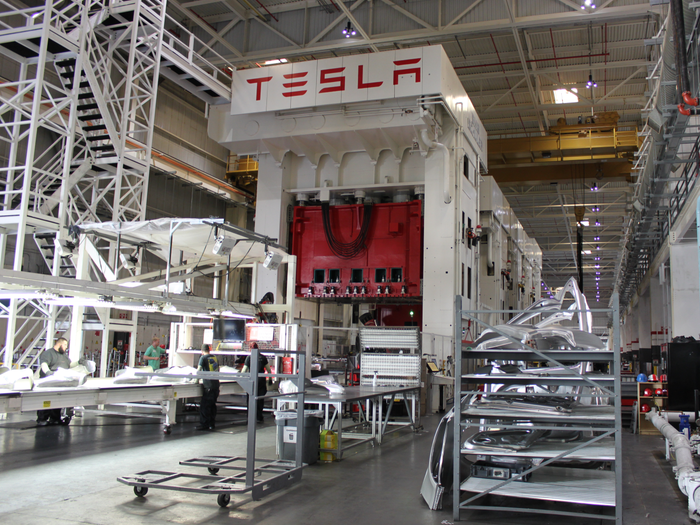
APPLICABLE MATHEMATICS
Let's put the size of the Tesla Factory to scale. A regulation-sized NFL football field is 360 feet long and 160 feet wide. Using the Length x Width rule: 360 (Length) x 160 (Width) = 57,600 square feet. If you take 5,300,000 square feet and divide it by 57,600, the size of the Tesla Factory is equivalent to 92 football fields. As shown in the “Tesla Motors” video by Wired, there is working evidence that caster wheels are used to help transport heavy items within the 5.3 million square foot space. This post will go over some of the ways that casters are used along with advanced manufacturing technology to improve electric vehicle (EV) manufacturing efficiency.
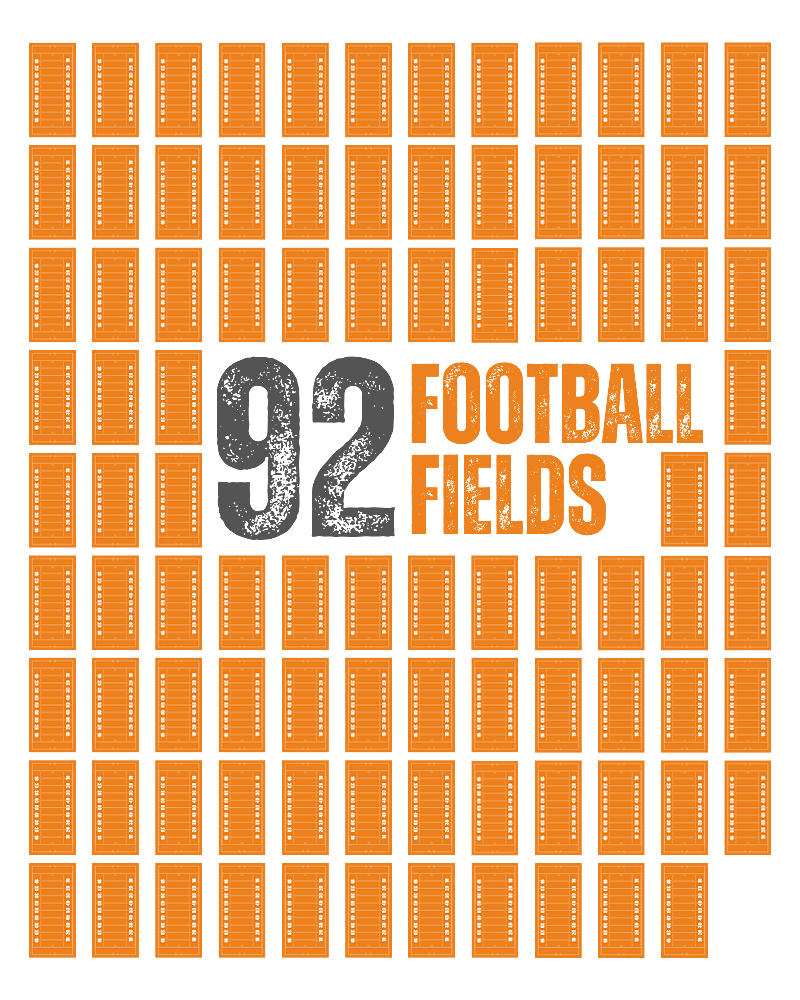
1. MANUFACTURING CLEANLINESS
Cleanliness and safety go hand-in-hand. As seen in the photo above, black markings are placed on the floor to indicate the tool cart’s proper location when not in use. The tool cart is kept at arm’s length when needed, and with the help of caster wheels, the tool cart can easily maneuver around a factory worker’s workflow. Cleanliness is the first step to automation in manufacturing and yields successful Tesla manufacturing processes.
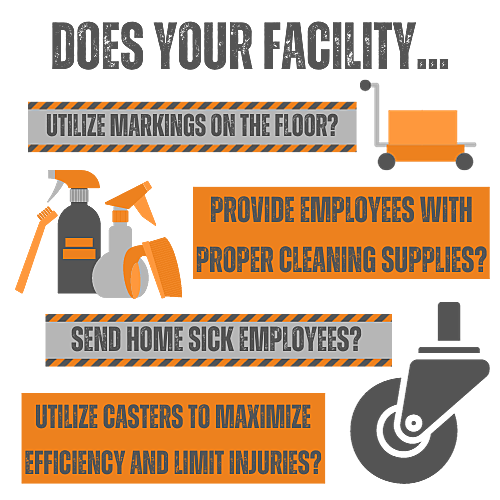
2. PULLING THE WEIGHT
To anyone not familiar with a tugger and cart system, a tugger is a cart for material handling in which the average tugger can handle a total weight load of 10,000 pounds. To help transport the frame of a Tesla car on over to the next stage of assembly, the tugger will require the proper caster wheel to ALSO handle to the tugger cart’s carrying capacity. This is just one of the numerous examples of caster solutions for EV production lines and what makes the NUMMI plant the most advanced manufacturing facility.
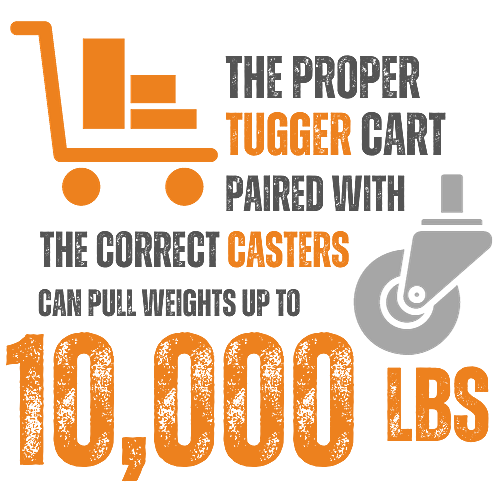
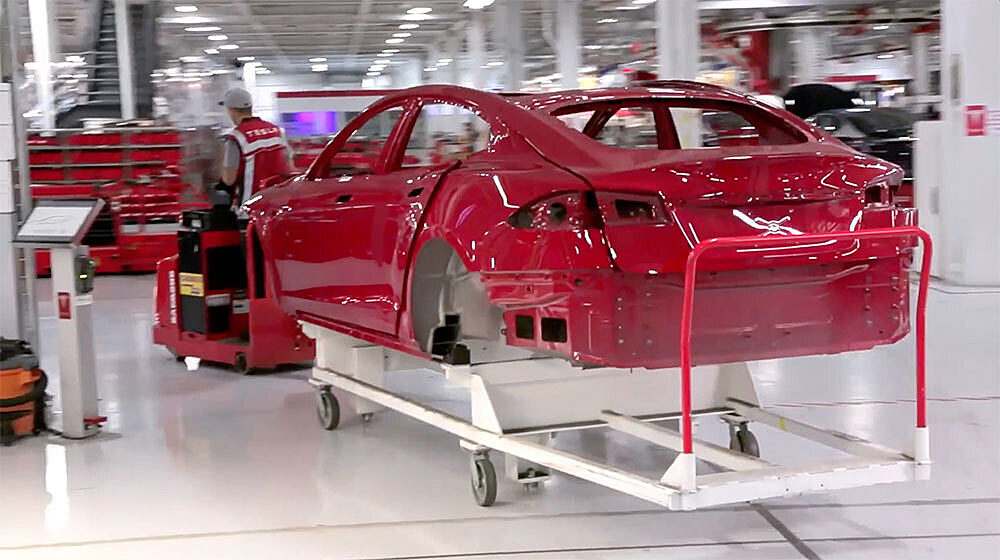
Referencing our “Selecting The Right Caster” page - the gross weight of truck/dolly/[cart] should be divided by the number of casters/wheels on which weight is distributed. There is the possibility that all 4 caster wheels will not have complete contact to the floor on a 4-caster/cart setup, therefore the carrying weight of the cart should be divided by 3 to ensure that your caster wheels can provide more than enough support.
For instance, if you were to take a 15,000-pound cart and divide it by 3, each caster you intend to install onto the cart should support a weight load of 5,000 pounds per caster. Doing so will create a safety allowance of 33% that will keep your employees safe and will protect the product that is being transported.
If you would like to know about the best caster for heavy weight loads, contact any one of our Regional Solutions Managers.
3. DROP OFF AND PICK UP
Using a tugger cart to transport the frame of the Tesla S from one stage of assembly onto the next stage can help a worker from overexerting their bodies from pulling the frame themselves. The utilization of casters for EV manufacturing improves overall plant efficiency and is an example of how the NUMMI plant has advanced manufacturing technology.
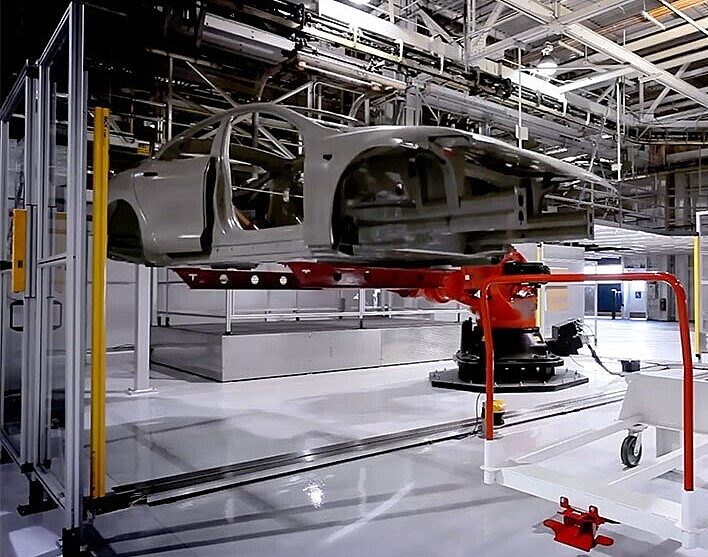
4. LIGHT UP THE DETAILS
After being fully assembled, a thorough run-through of the car is necessary to confirm that it is spotless. In EV manufacturing nothing’s better than having a mobile lighting system that a worker can configure based on their needs. The constant checking for accuracy also reduces the plant’s waste and is one of the facilities many sustainable manufacturing practices.
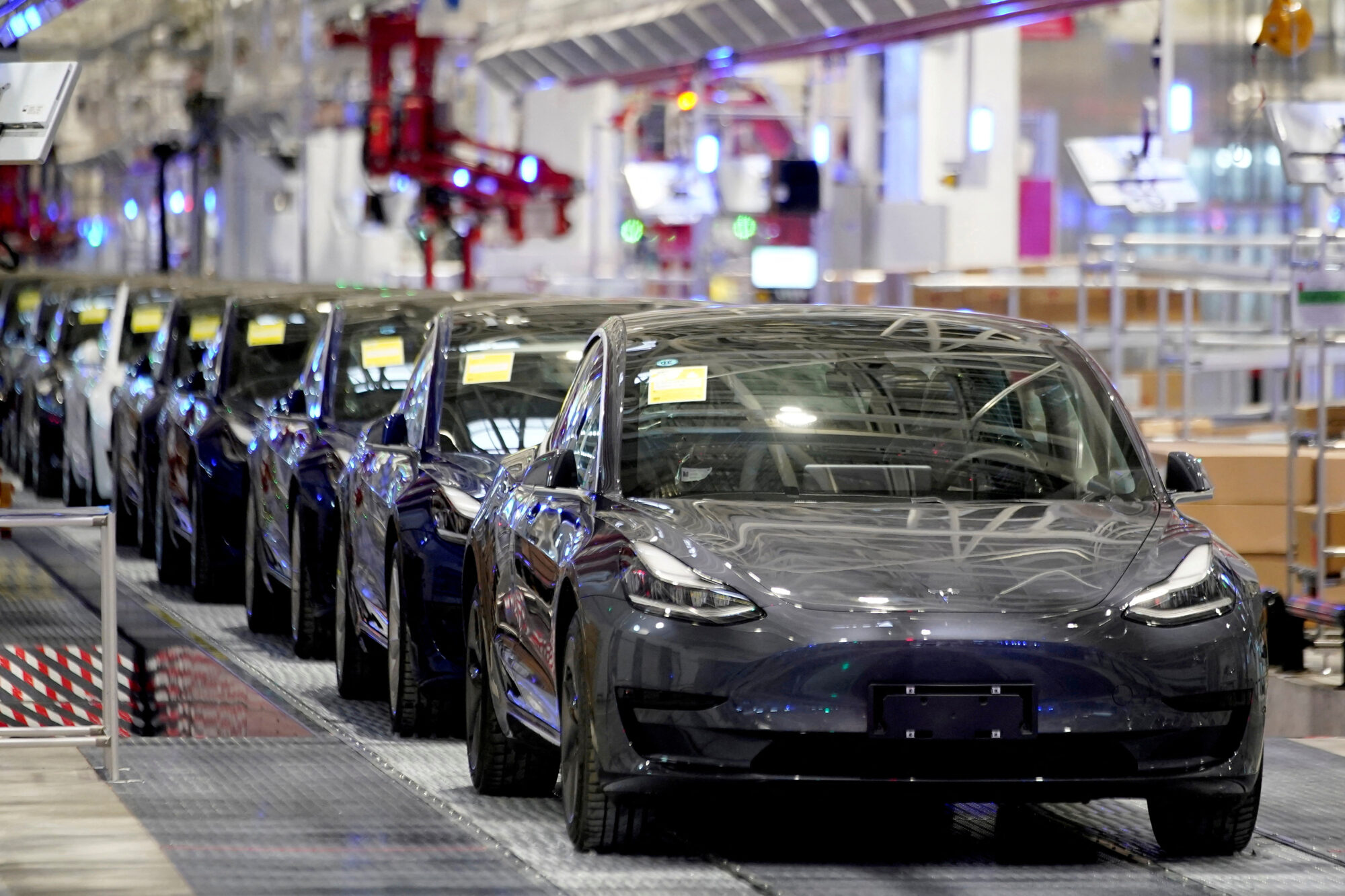
5. PUSH IT TO THE LIMIT
Tuggers are not going to set up the carts without the assistance of human labor. As far as we know, machines do not feel pain the same way humans do. So, if a 90 to 300-pound worker has to push or pull a 10,000-pound cart manually, be sure that the casters are capable of lowering push/pull resistance to prevent injuries. Using lean manufacturing principles it is easy to conclude that the non-utilization of employees is one of the many wastes and plant’s should utilize casters in order to prevent injuries and non-utilization.
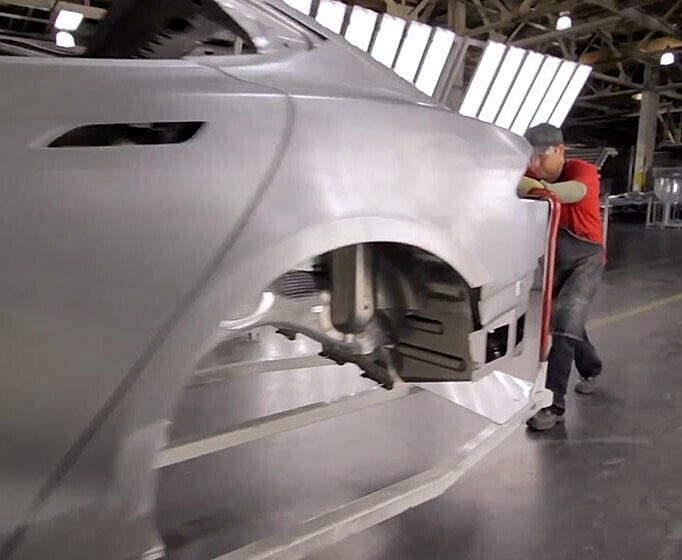
CONCLUSION
The Tesla manufacturing plant is currently working with a space equaled to 92 football fields. At the time of this writing, Tesla is working with new plans of expanding the 5.3 million square feet of space into 10.6 million square feet to accommodate 14,000 workers and more activities.
10.6 million square feet divided by 14,000 employees will amount to 757 square feet of working space per employee. 750 square feet is about the size of a modest two bedroom, one bathroom apartment. If an employee has to maneuver heavy duty product around a 750 square foot space - all day, every day - a reliable cart with dependable casters should be installed to help take the load off.
If you're interested in learning about the best casters for your application or needs, contact us to begin working with one of our expert Regional Solutions Managers.
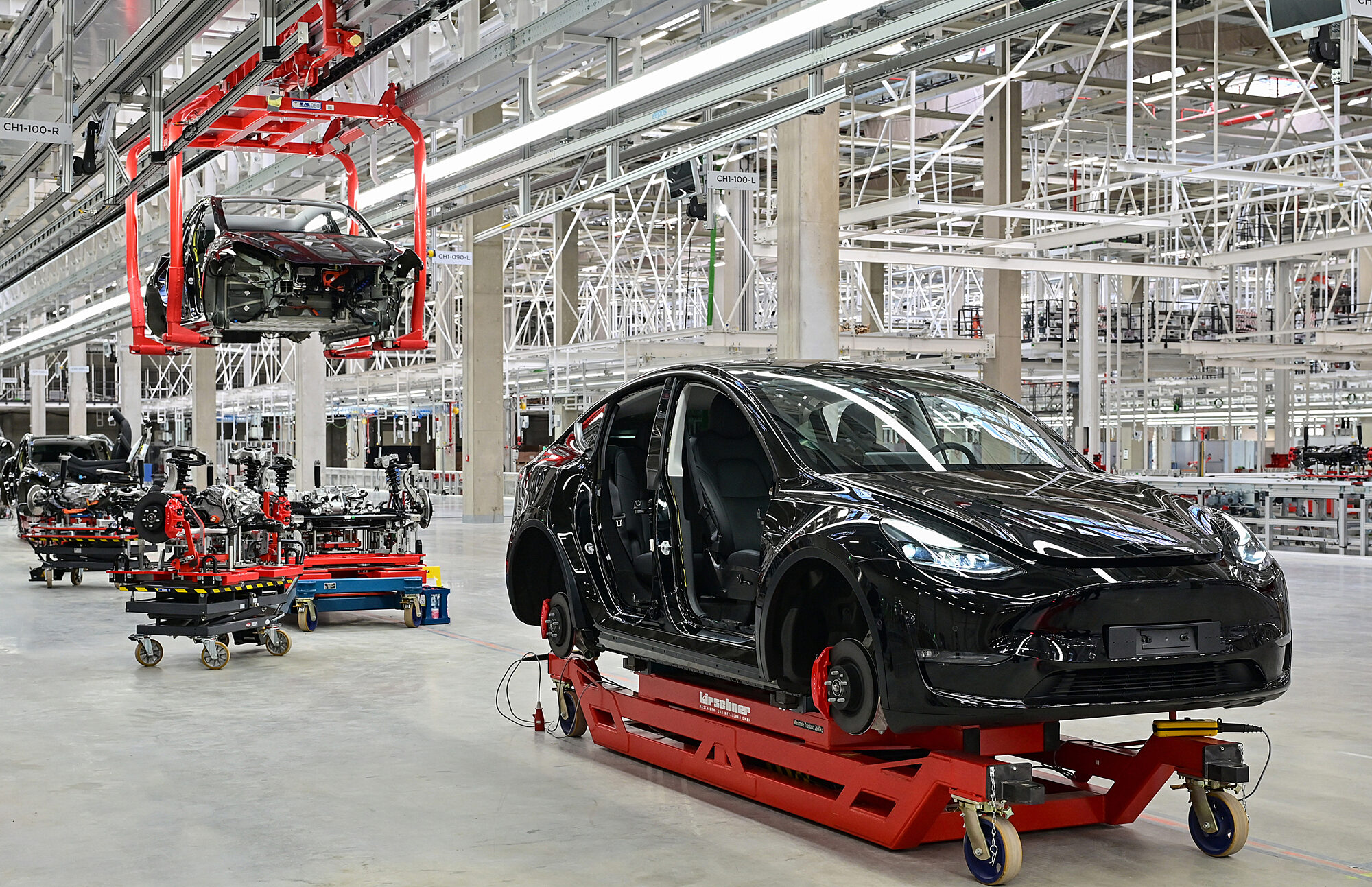