Material Handling Automation Is on the Rise
Material handling automation has become increasingly important in recent years as companies strive to improve efficiency and productivity while minimizing the risk of workplace injuries. By implementing automated systems for material handling, companies can reduce costs, improve safety, and increase output.
In this blog post, we'll take a closer look at material handling automation and its benefits.
If you are looking for more comprehensive information, including videos, case studies, a white paper, caster recommendations and more, visit our Material Handling and Automation resource library
What is Material Handling Automation?
Material handling automation refers to the use of technology to automate the movement, storage, and retrieval of materials in a warehouse or manufacturing environment. This can include conveyor systems, automated guided vehicles (AVGs), automated storage and retrieval systems (AS/RS), robotic systems, and other advanced technologies.
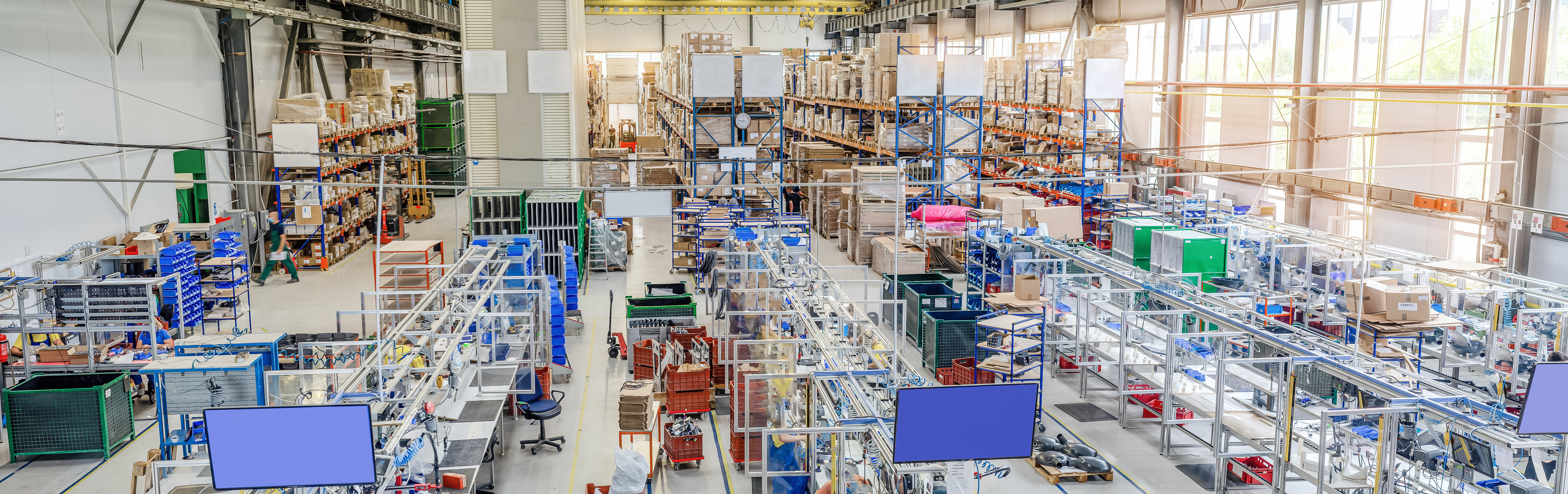
Benefits of Material Handling Automation:
There are many benefits to implementing material handling automation in your facility, including:
1. Improved Efficiency: By automating material handling processes, you can reduce the time and labor required to move materials around your facility. This can lead to increased productivity and output.
2. Cost Savings: Automation can help reduce costs associated with labor, energy, and equipment maintenance. In addition, automated systems can help minimize the risk of workplace injuries, which can result in lower insurance premiums and workers' compensation claims.
3. Improved Accuracy: Automated systems can be programmed to accurately track and move materials, reducing the risk of errors and damage to products.
4. Increased Flexibility: With material handling automation, you can easily adjust your operations to meet changing demands or production schedules. Automated systems can be programmed to handle a wide variety of materials and can be customized to meet your specific needs.
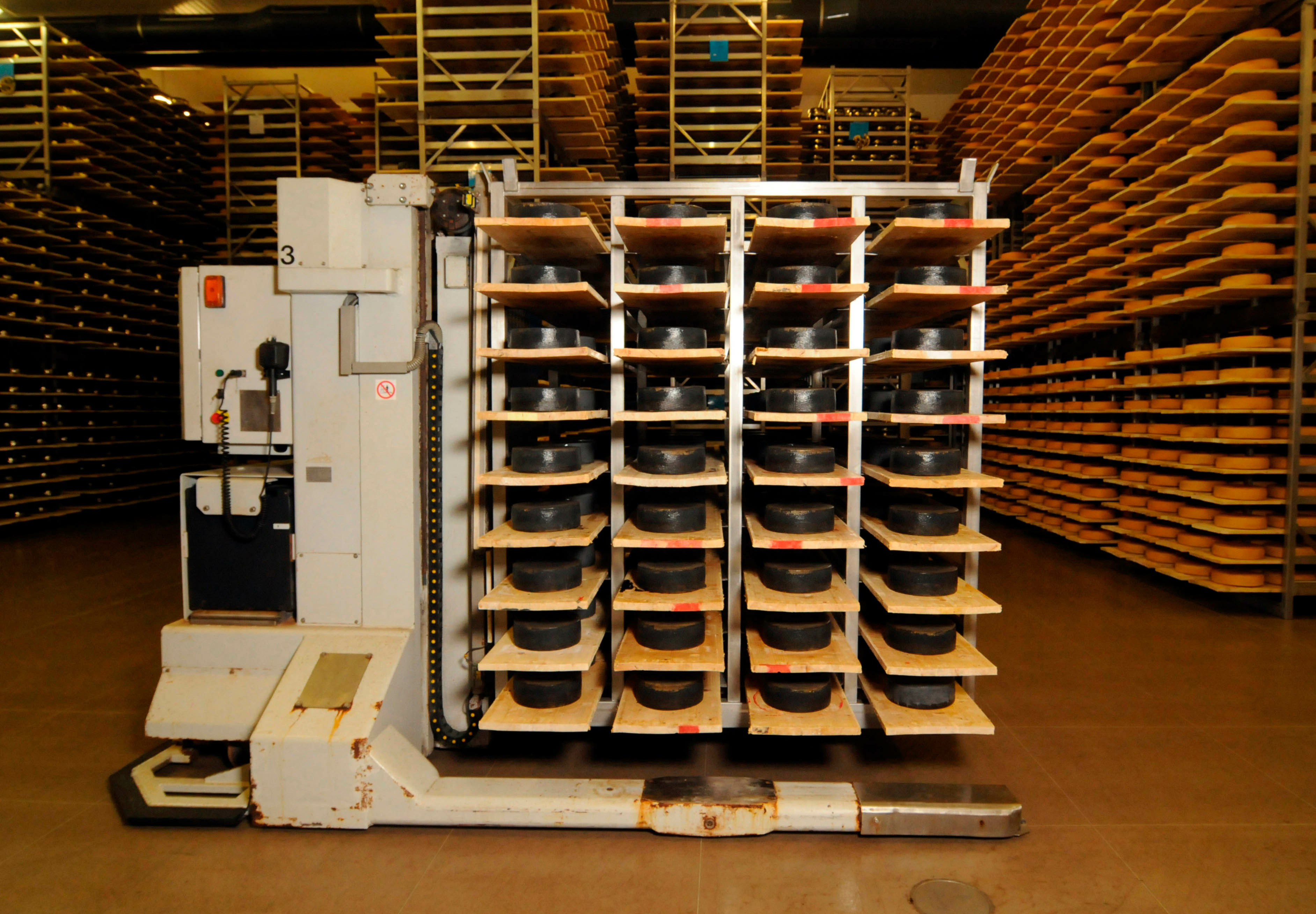
Types of Material Handling Automation:
There are several types of material handling automation systems, each with its own unique advantages and applications:
1. Automated Guided Vehicles (AGVs), Automated Guided Carts (AGCs), and Automated Guided Robots (AGRs): AGVs, AGCs, and AGRs are autonomous vehicles or robots that are guided by embedded sensors or markers on the floor. They can navigate predetermined paths or respond to real-time inputs to transport materials within a facility. AGVs are typically used for transporting pallets or containers, while AGCs are designed for smaller loads, and AGRs combine robotic capabilities with autonomous navigation.
2. Conveyor Systems: Conveyor systems use belts, rollers, or other mechanisms to move materials from one location to another. They can be used for both horizontal and vertical transportation of materials.
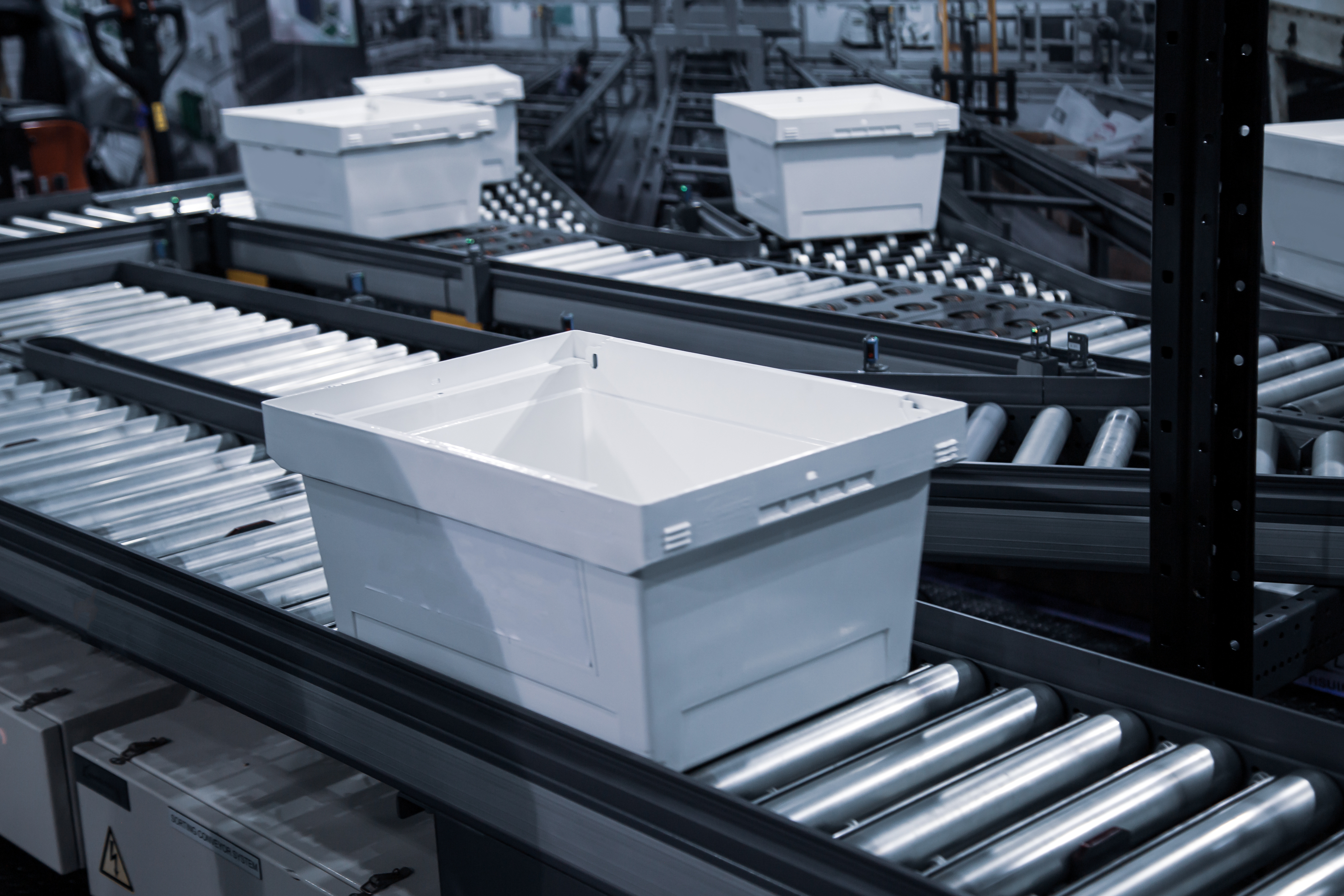
3. Automated Storage and Retrieval Systems (AS/RS): AS/RS systems use automated cranes or shuttles to store and retrieve materials from high-density storage racks. These systems can maximize storage capacity while minimizing the required space.
4. Robotic Systems: Robotic systems use advanced sensors and programming to automate the movement of materials. They can be used for tasks such as palletizing, depalletizing, and order picking.
Conclusion:
Material handling automation has become an essential component of modern warehouse and manufacturing operations. By implementing automated systems for material handling, companies can improve efficiency, reduce costs, and increase output. With a variety of systems available, it's important to choose the right automation solution for your specific needs. Contact a trusted provider like Caster Connection to learn more about how material handling automation can benefit your business.