How To Remove Waste Of Overproduction
Poor forecasting can cause this. Producing items beyond the customer's requested amount are incredibly wasteful. Some of the related costs associated with overproduction are:
- Poorly utilizing extra workers to fulfill orders
- Using up spare parts and raw materials
- Using up pallets and skids
Overproduction also affects other types of downtime waste like:
- Waiting - Related to a batch and queue process of a large quantity order
- Not-Utilizing Talent - Failure to harness the potential and efficiency of human capital
- Transporting - Unneeded finished goods are taking up needed space of the distribution center
- Inventory - Overstock of items and using up raw parts and materials to fulfill order demands
- Motion Waste - Workers are busy putting together products that no one ordered
- Excess Processing - Large batch processing might require filling out extra paperwork
Learn more about the 8 Waste Types of Downtime here.
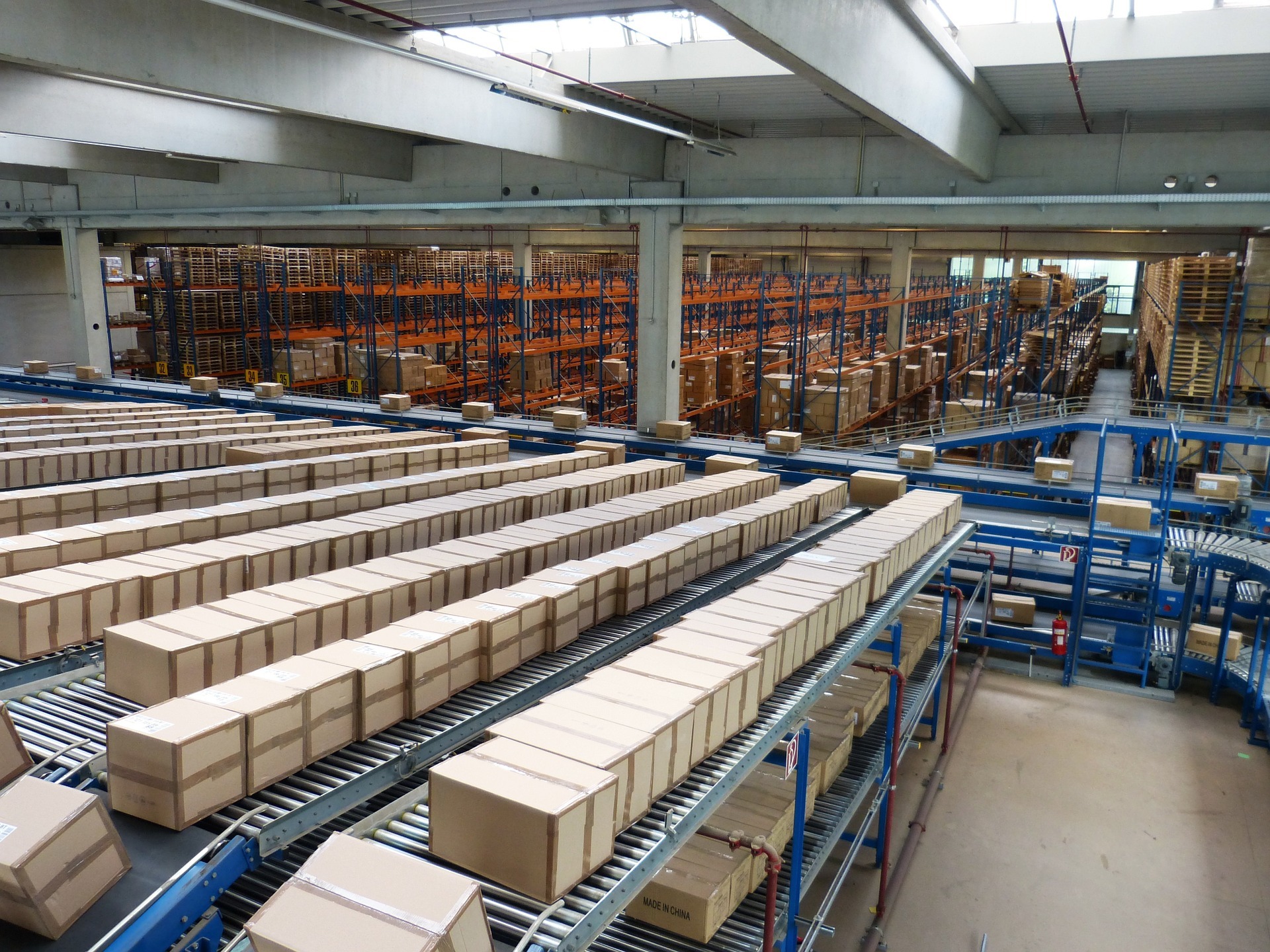
The best starting point to avoid overproduction is to employ the “pull method.” The pull method is demand-centric and will require proper forecasting to ensure that waste does not happen within the workplace or production line. The effectiveness of the pull production is to manage the minimum number of pieces ready for withdrawal. Doing so will ensure that overproduction never occurs, and the overstock piles of inventory will not exist.
From what we’ve learned, overproduction is a waste of downtime that is preventable. Failure to keep overproduction from happening will set off a chain reaction that will affect the other types of downtime. Overproduction will take up a lot of time and resources to manage. If you are interested in how to remove other waste of downtime, you can learn how to remove the waste of defects here.