How To Remove The Waste Of Waiting From Downtime
Waiting is a non-value added activity that cuts into a company’s cost of time and resources. Non-value added activities prevent products from reaching a complete state. Waiting is a category of downtime waste where workers may find themselves waiting for parts inspection to perform a required task, waiting for materials to be delivered to a work area, waiting for a machine to finish its cycle or waiting for information from a supervisor. This post will teach you how to remove the waste of waiting from downtime.
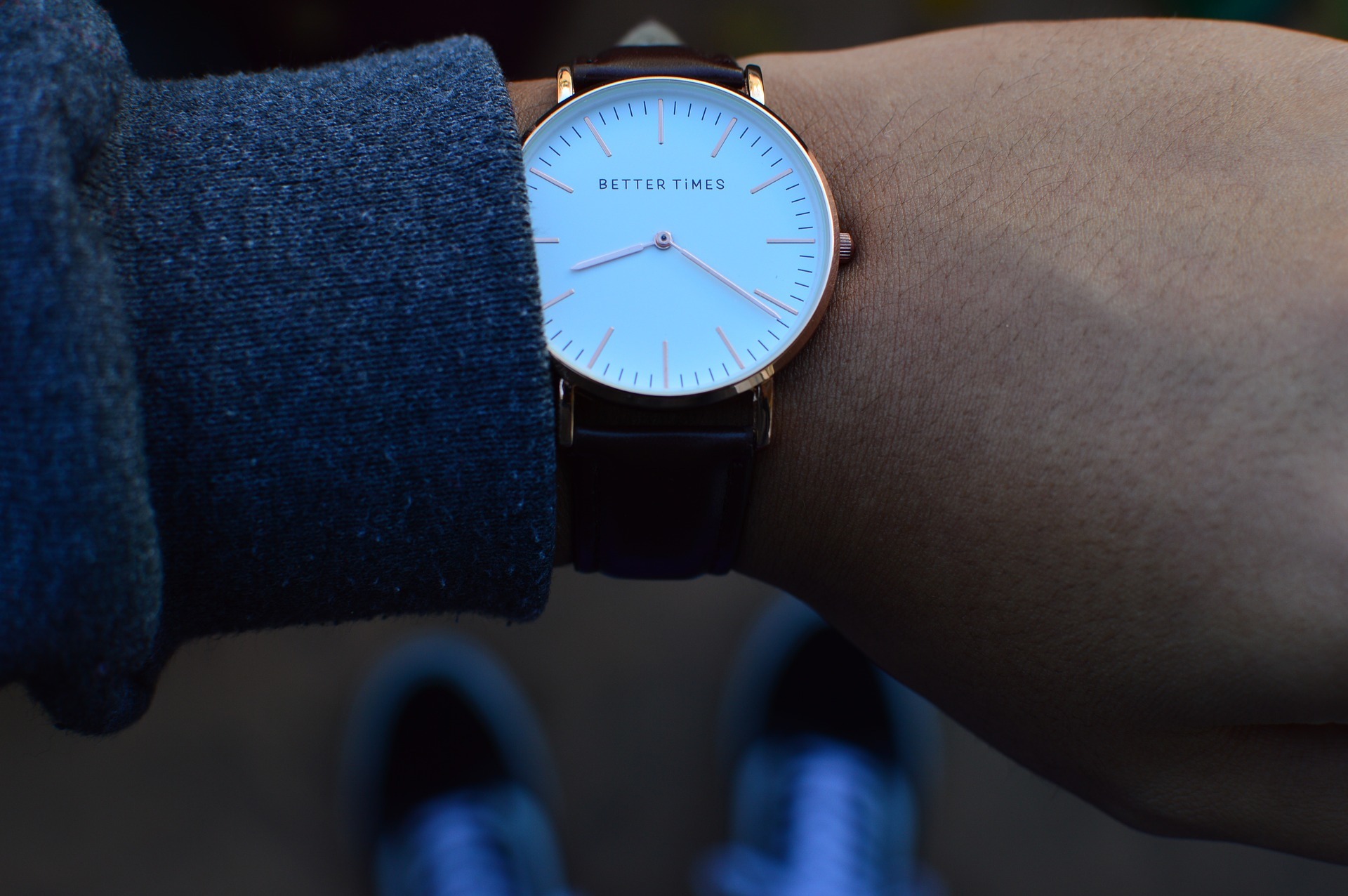
Unplanned equipment downtime is an excellent example that demonstrates the waste of waiting. Whenever products are not moving along the production line or the product is not processed into the next phase of production, the waste of waiting happens. Waiting is apparent when a company is paying for workers to stand idle and the products’ lead-time are not meeting client's expectations.
To further illustrate the point, a towline of a production line is towing cargo weighing 3000 pounds, traveling 5 miles per hour. The towline is running on four 8” x 2” thermoplastic rubber (TPR) caster wheels and one of the TPR caster wheels fail under the weight of the 3000-pound cargo. The towline is now inoperable to fulfill a required task that sets off a chain reaction that makes other processes of the production line stand idle. Due to the unplanned equipment downtime, the production flow has now come to a screeching halt – delaying the production schedule.
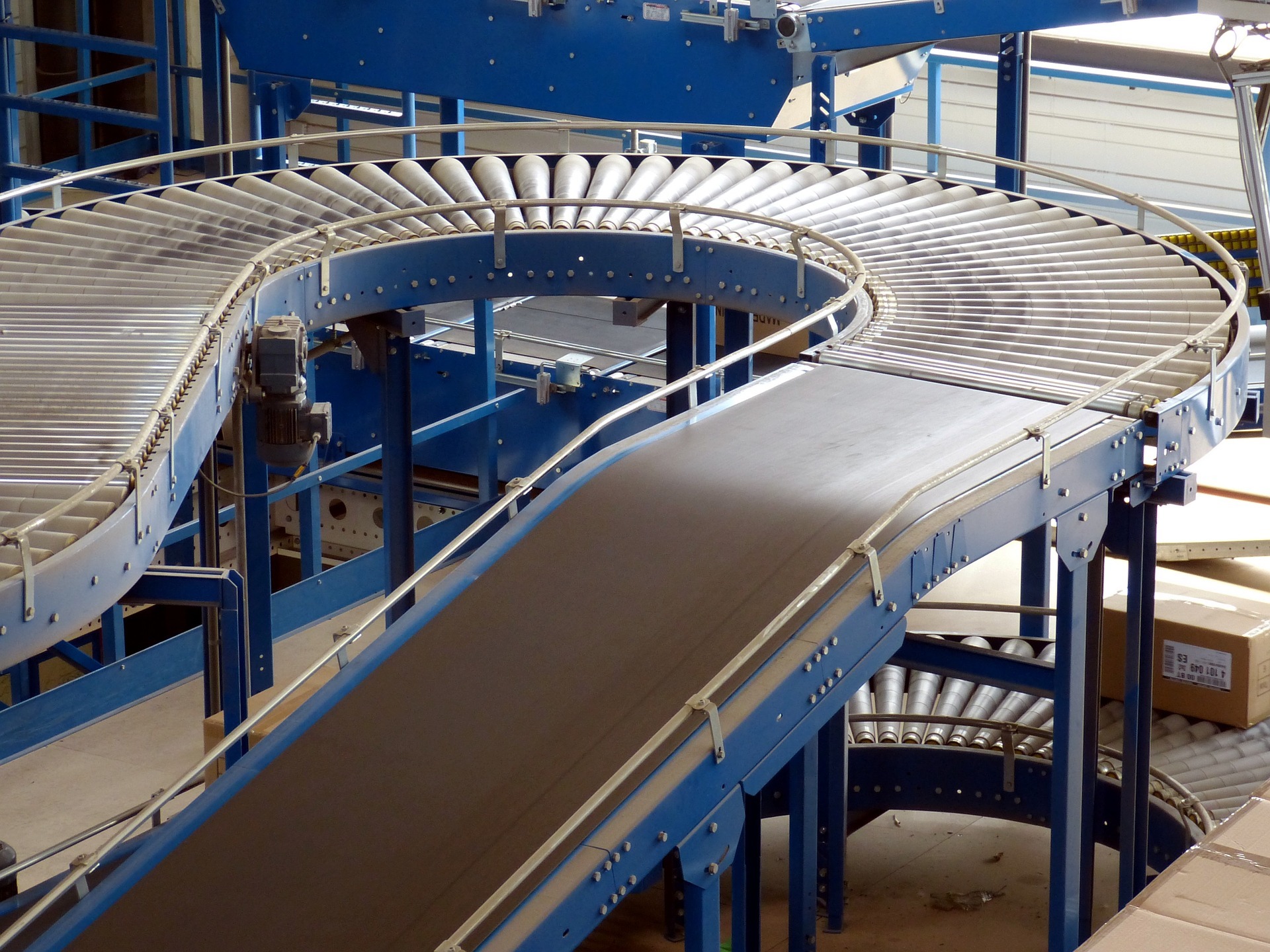
An employee, in charge of maintenance, will have to tend to the unexpected equipment downtime and will most likely replace it with a spare 8” x 2” thermoplastic rubber caster wheel from the tool crib, which will fail again. In this scenario, replacing the faulty caster wheel with the same thermoplastic rubber caster wheel is not going to do the towing application any service because, the fact of the matter is thermoplastic rubber caster wheels are poor options to use for towing applications.
The only way a worker would know this beforehand is by exercising preventative maintenance. If a company would have chosen the right solution the first time, they would not be in a predicament mentioned in the scenario. If the operations manager of the company reached out to one of Caster Connection's Regional Solutions Managers (RSM), they would have learned why thermoplastic rubber caster wheels are not qualified for towing applications.
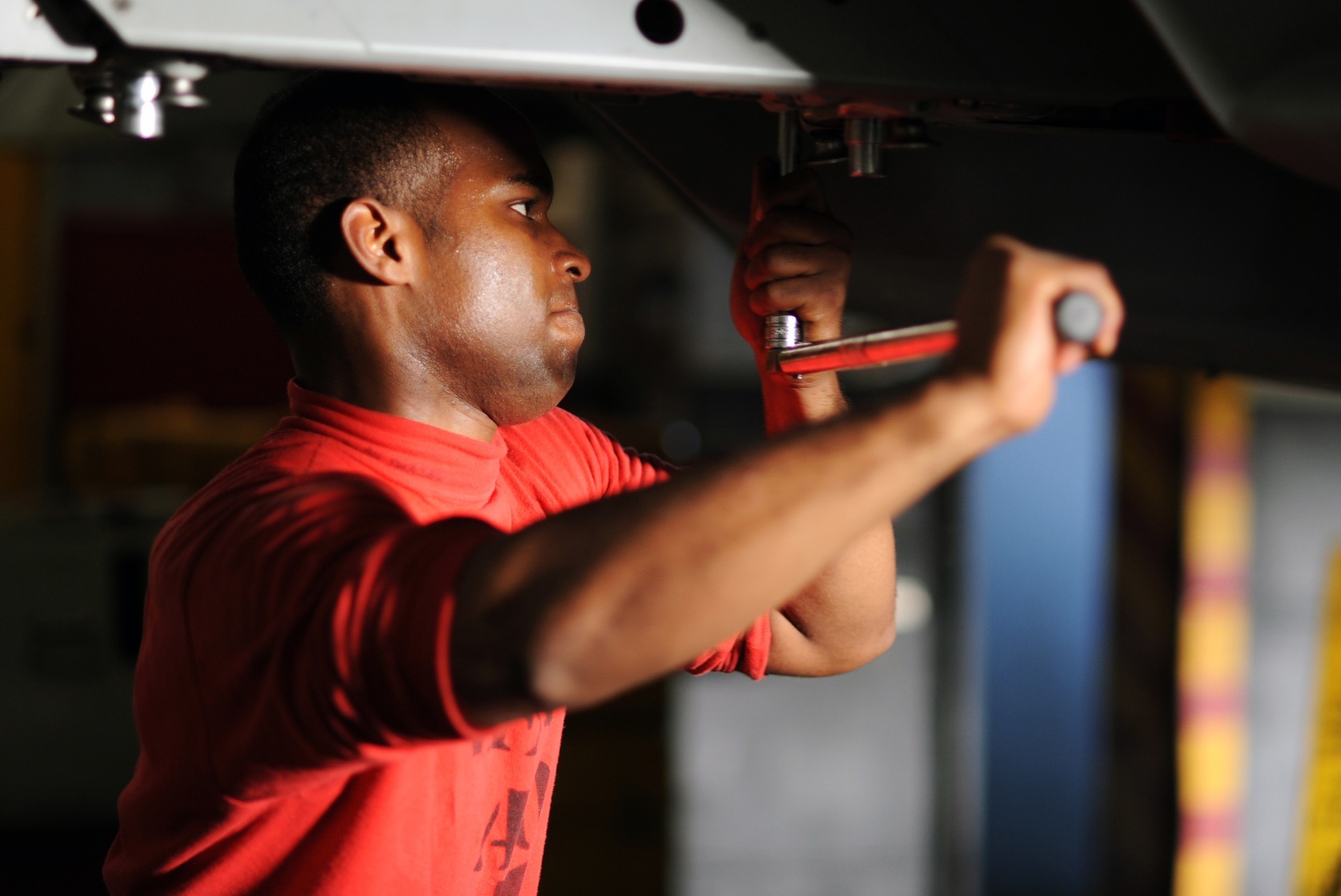
Thermoplastic rubber caster wheels have a lower load capacity rating, will pick up debris, and cannot handle heat – due to revolutions per minute. The rubber tread of the TPR caster wheel will run hot during long, active use and the tread of the TPR will de-bond from the caster wheel’s core, making it inoperative for a towing application. Had the operations manager spoke with a Caster Connection RSM and learned about the flaws of TPR caster wheels early on, the operations manager may have opted for a solution that is qualified for the company’s production line’s needs, like choosing the CC Apex.
Unlike the TPR caster wheels, the CC Apex was designed to handle the rigors of a towing application. In the scenario, the towline was outfitted with four 8” x 2” TPR casters. One 8” x 2” TPR caster has a 600-pound load capacity, whereas, an 8” x 2” CC Apex has a 1200-pound load capacity. The energy stored into the CC Apex’s polyurethane rejects debris and the aluminum core of the CC Apex will not overheat and bog down movement. Learn more about the CC Apex here.
Taking everything into account, if the operations manager of the scenario chose the right solution for the company’s towline application - the first time - the company’s production line would not have suffered through the downtime of waiting. Waiting is a non-value added activity that takes away from the company’s cost of time and other valuable resources. By exercising preventative maintenance beforehand, the towline equipment may have continued to be operable and the waste of waiting may not have occurred. Do not wait for things to go wrong to practice preventative maintenance, contact one of our RSMs to find out how to choose the right caster solution for your application. Get it right the first time.