Going Forklift-Free: How Automation Is Transforming Material Handling Operations
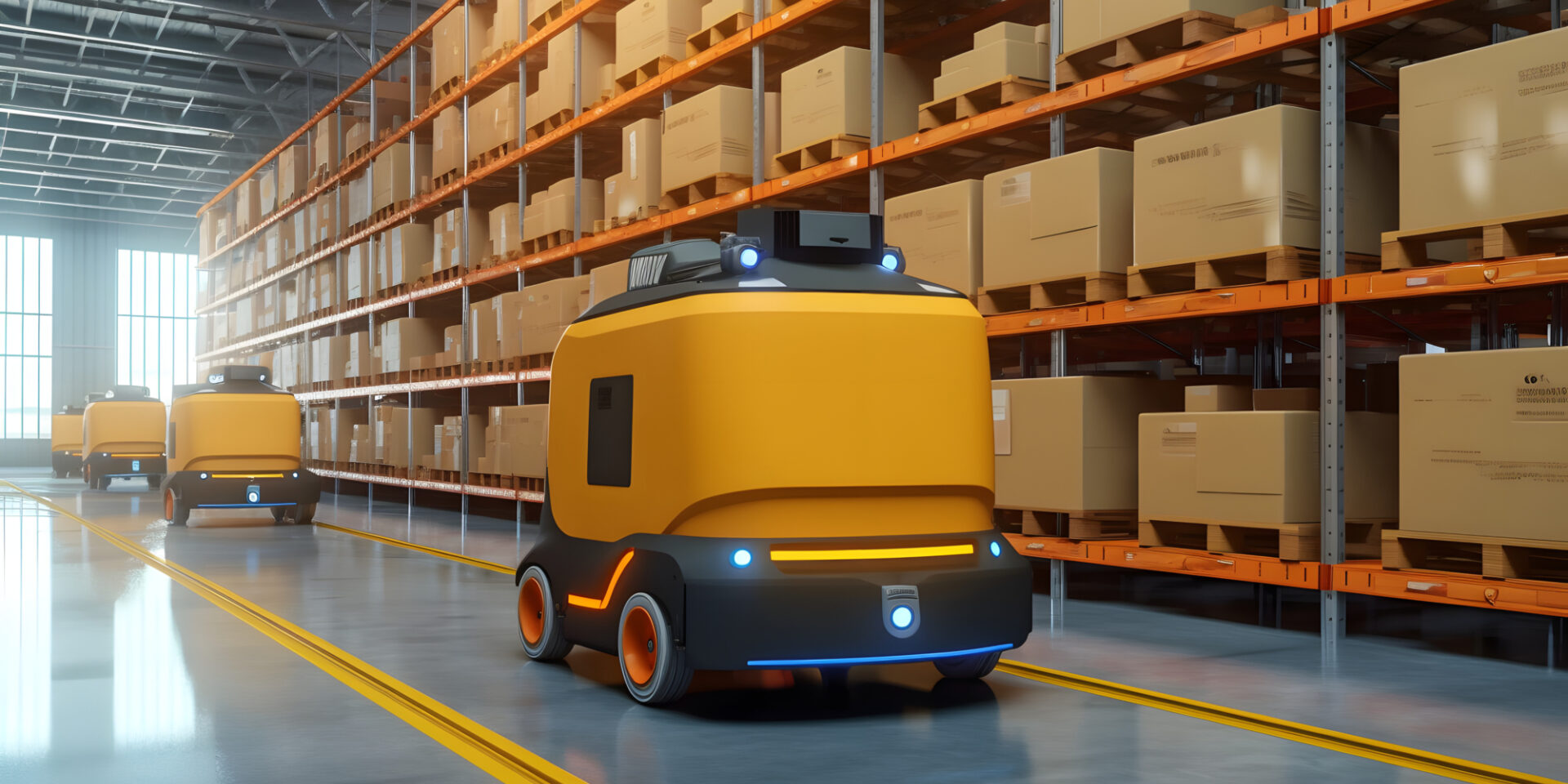
Forklifts have been an integral part of the material handling and manufacturing industries for years. Built into the fabric of many companies’ operations, the powerful industrial trucks provided an alternative way to transport materials around facilities. However, companies quickly noticed that forklifts came with indisputable safety concerns for operators, pedestrians, and goods. Aiming to address these concerns, many companies have moved towards automated solutions, following the forklift-free initiative. Before we jump into what the forklift-free initiative is and how it’s benefitting the material handling and manufacturing industries, let’s look at the problem.
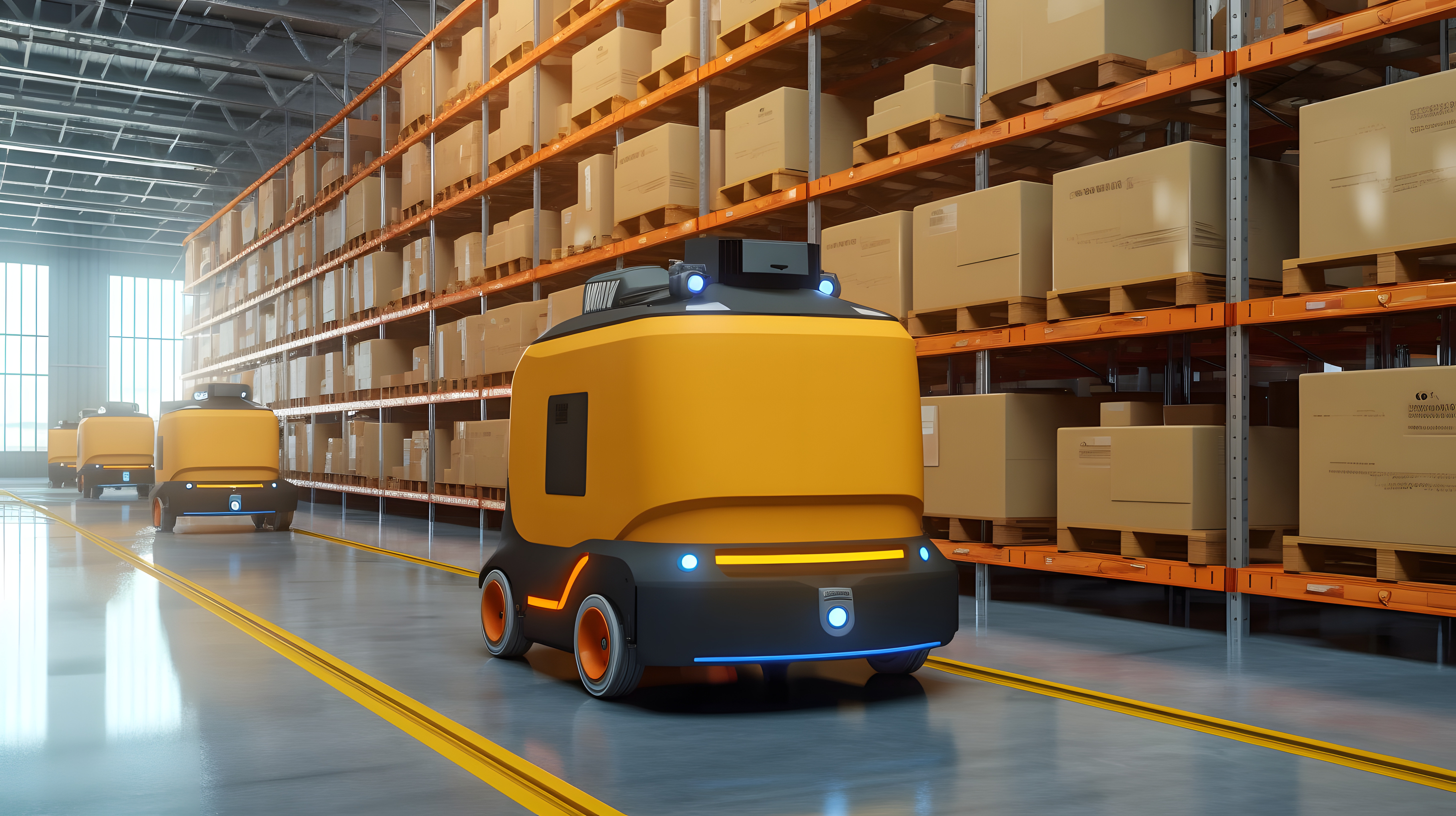
Reasons Behind the Forklift-Free Initiative
The convenience that forklifts offer is hard to deny, providing a reliable means of transporting heavy loads. However, they come with a set of risks and challenges that cannot be overlooked.
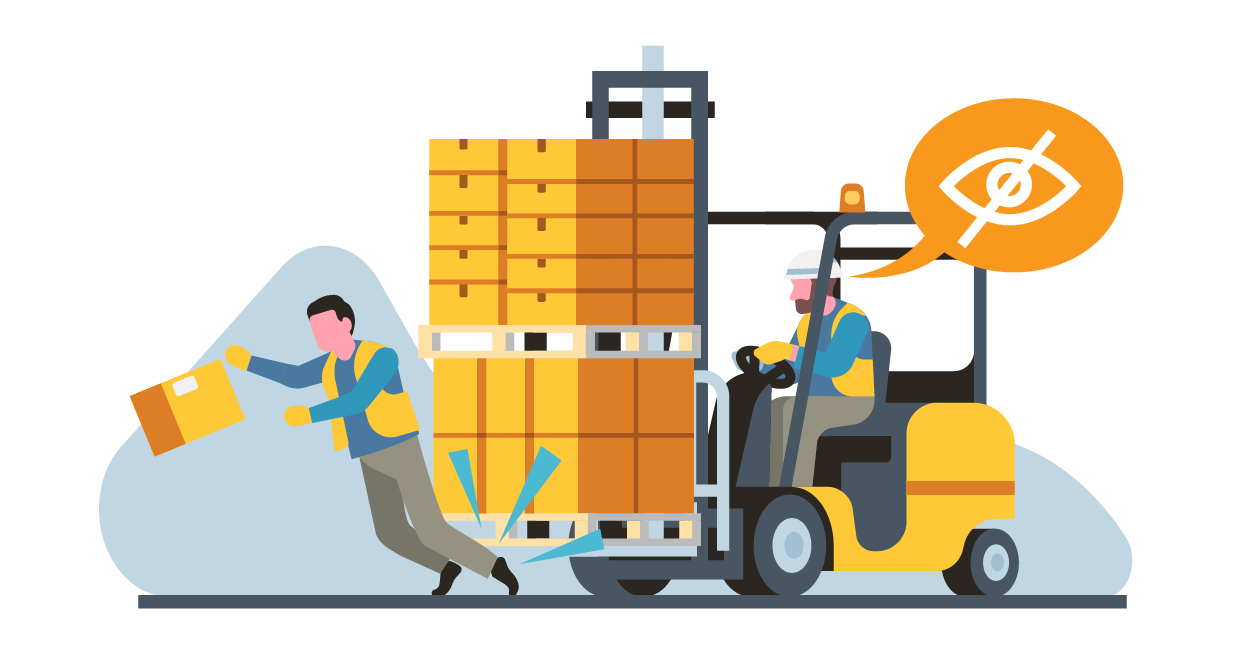
Safety Concerns
Forklifts are involved in many workplace accidents each year. OSHA estimates that there are almost 100,000 accidents annually in the United States alone. 100 of these accidents result in death, 34,900 cause life-threatening injuries, and 61,800 causes non-serious injuries. Common reasons for accidents include collisions, tip-overs, falling loads, and emissions poisoning from internal combustion forklifts.
Forklifts can also drop and destroy valuable goods, products, and materials, which puts workers at greater risk and causes product loss. The Council of Supply Chain Management Professionals reported in 2017 that the annual cost of damaged and unsaleable product was nearly $15 billion. TT Club reports that collisions caused by handling equipment, such as forklifts and lift trucks, are the second most common cause of freight damage and inventory loss, accounting for almost 13.6 percent of all claims.
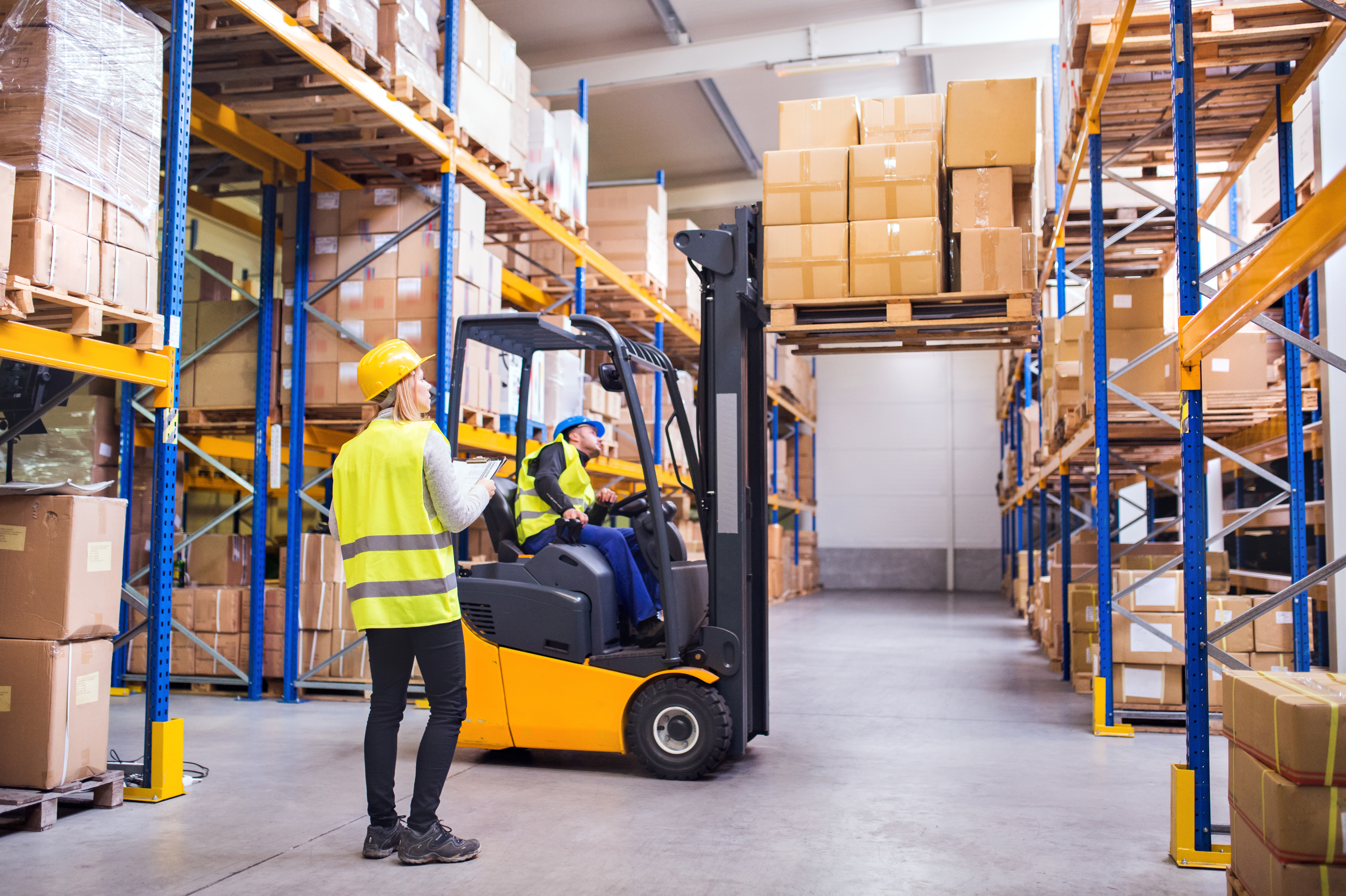
Operational Limitations
Forklifts require skilled employees to operate them, increasing workforce requirements and costs. The average cost of a forklift operator is $20/hour, according to the U.S. Bureau of Labor Statistics. Also, because they require frequent maintenance, forklift usage can cause excessive downtime, production schedule disruptions, and reduced overall efficiency. Common forklift maintenance issues include mast problems, steering problems, and starting problems. Unfortunately, these issues can be difficult to troubleshoot, often leading to further problems down the road.
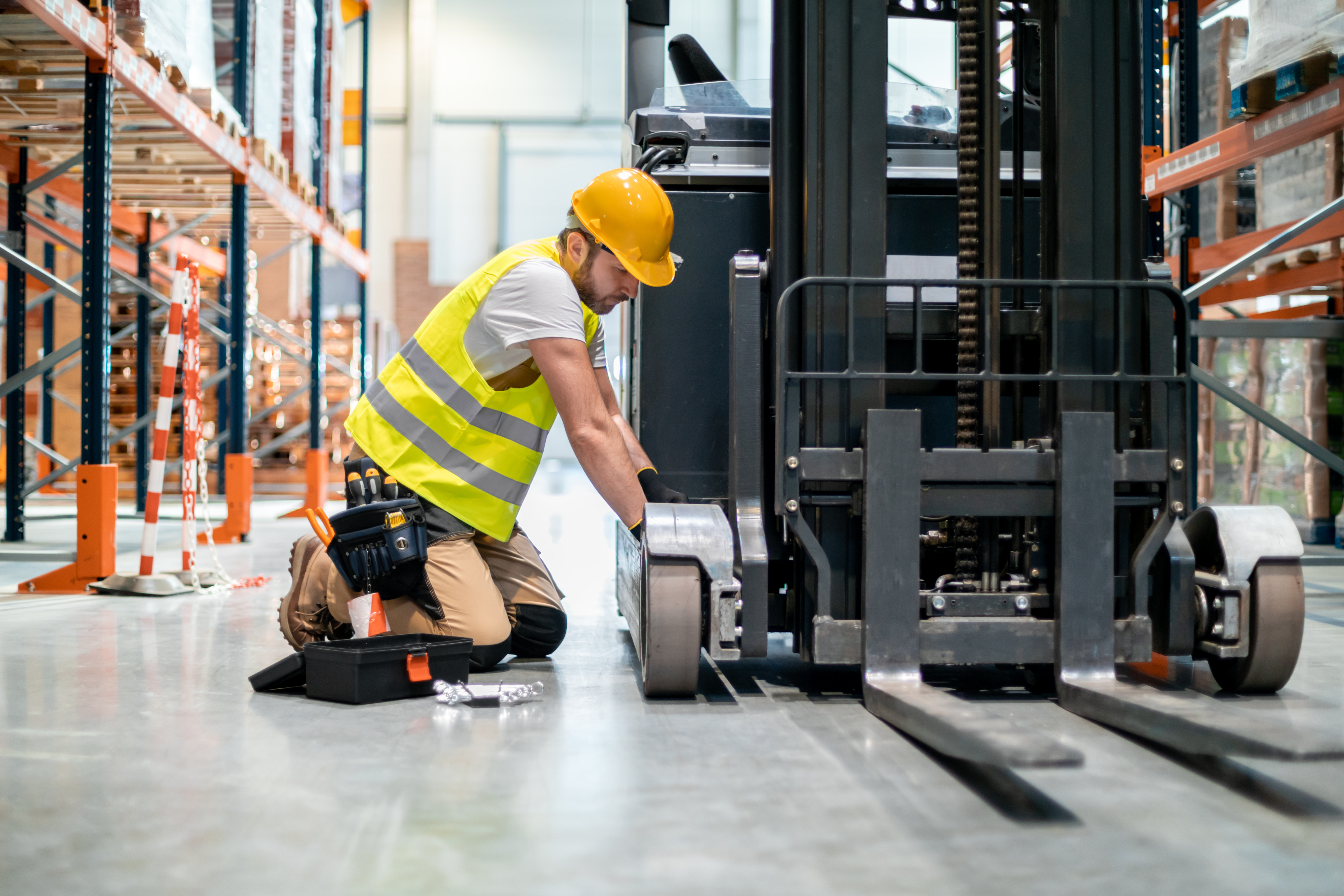
Environmental Impact
Traditional forklifts, especially those powered by internal combustion engines, contribute to greenhouse gas emissions and noise pollution. Additionally, they are less energy-efficient than their electric counterparts, which can be powered by renewable energy sources. Another point of contention regarding the environment is the forklift’s risk of fuel spill and leaks. ICE forklift fuel spills and leaks can contaminate soil and water sources, especially when preventative maintenance is underprioritized. Proper disposal of these fuels is crucial to the prevention of environmental damage.
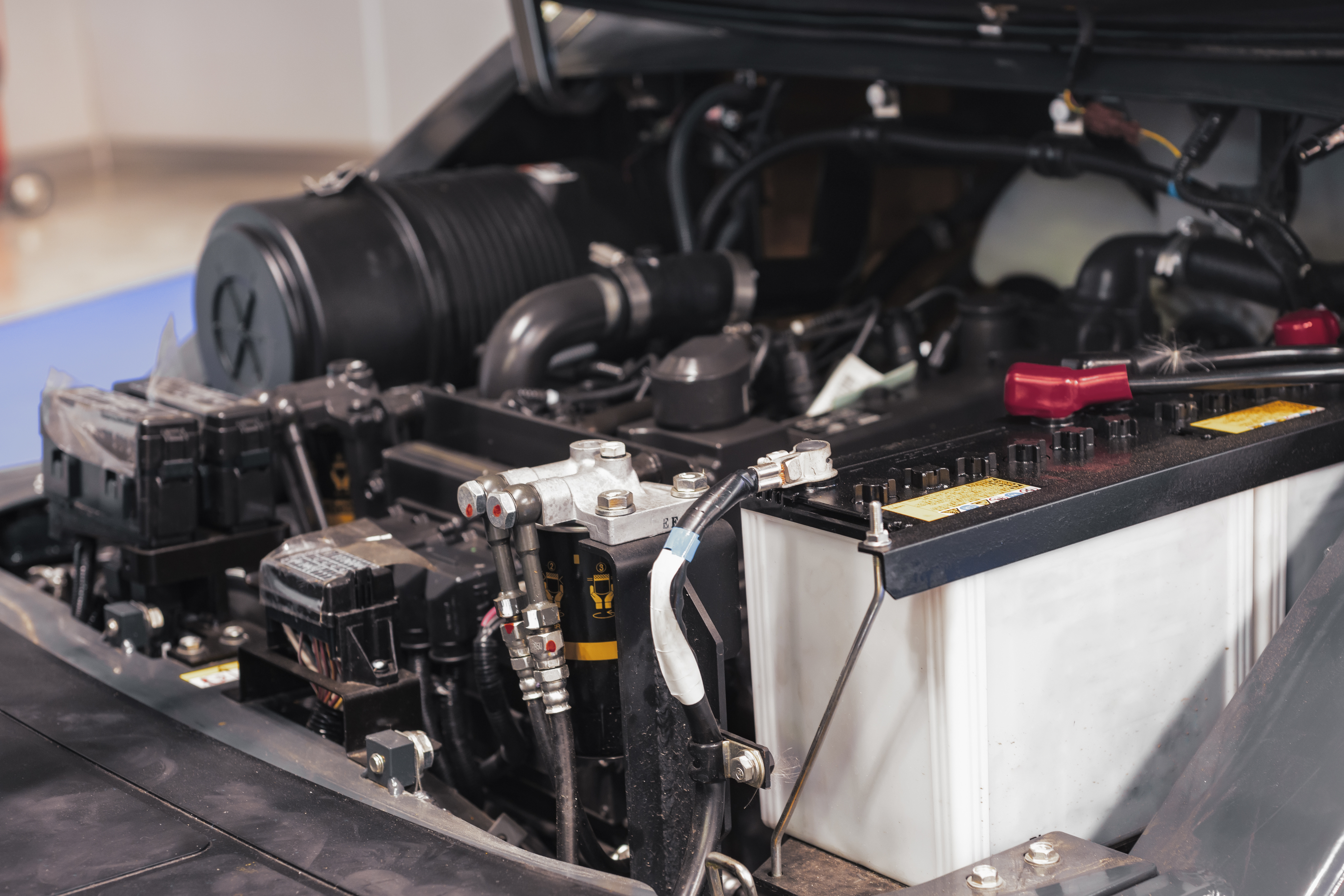
Introducing the Forklift-Free Initiative
Recognizing these challenges, many companies are adopting forklift-free solutions to enhance safety, efficiency, and sustainability. This initiative aims to correct limitations brought on by forklift usage and provide a plan for implementing forklift alternatives. Here are some alternatives that are driving change in the manufacturing and material handling industries:
Automated Guided Vehicles (AGVs)
AGVs are autonomous robots designed to transport materials without human intervention. Equipped with sensors and navigation systems, they can move loads along predefined paths. AGVs come in a variety of sizes, making them suitable for a diverse range of applications and load capacities.
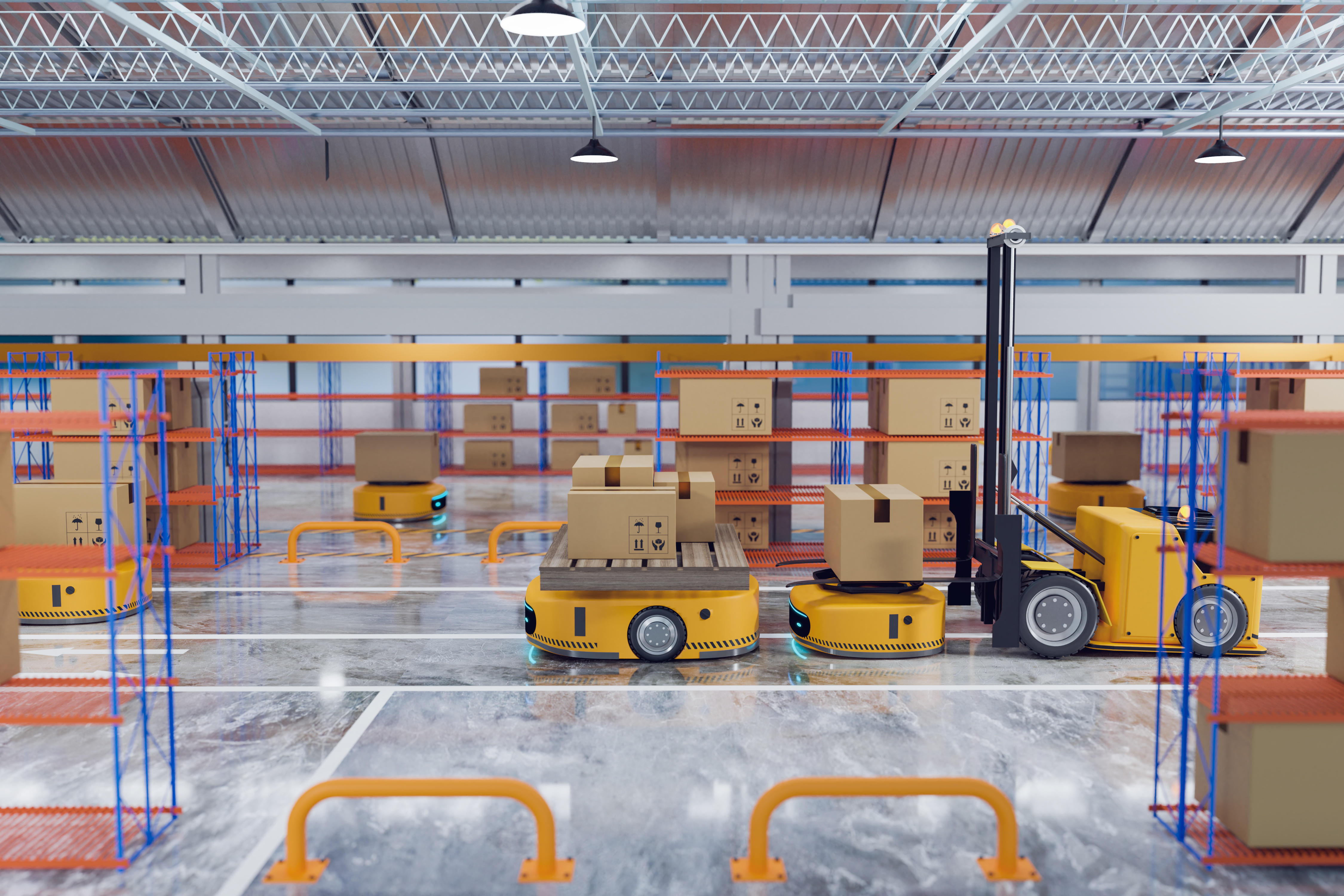
Autonomous Mobile Robots (AMRs)
Unlike AGVs, AMRs can navigate dynamic environments using real-time data. They are ideal for complex warehouse layouts and can adapt to changes without requiring extensive reprogramming.

Conveyor Systems
Conveyors offer a reliable means of moving goods over short to medium distances within a facility. They can be customized to handle various load sizes and types, and they integrate well with other automated systems.
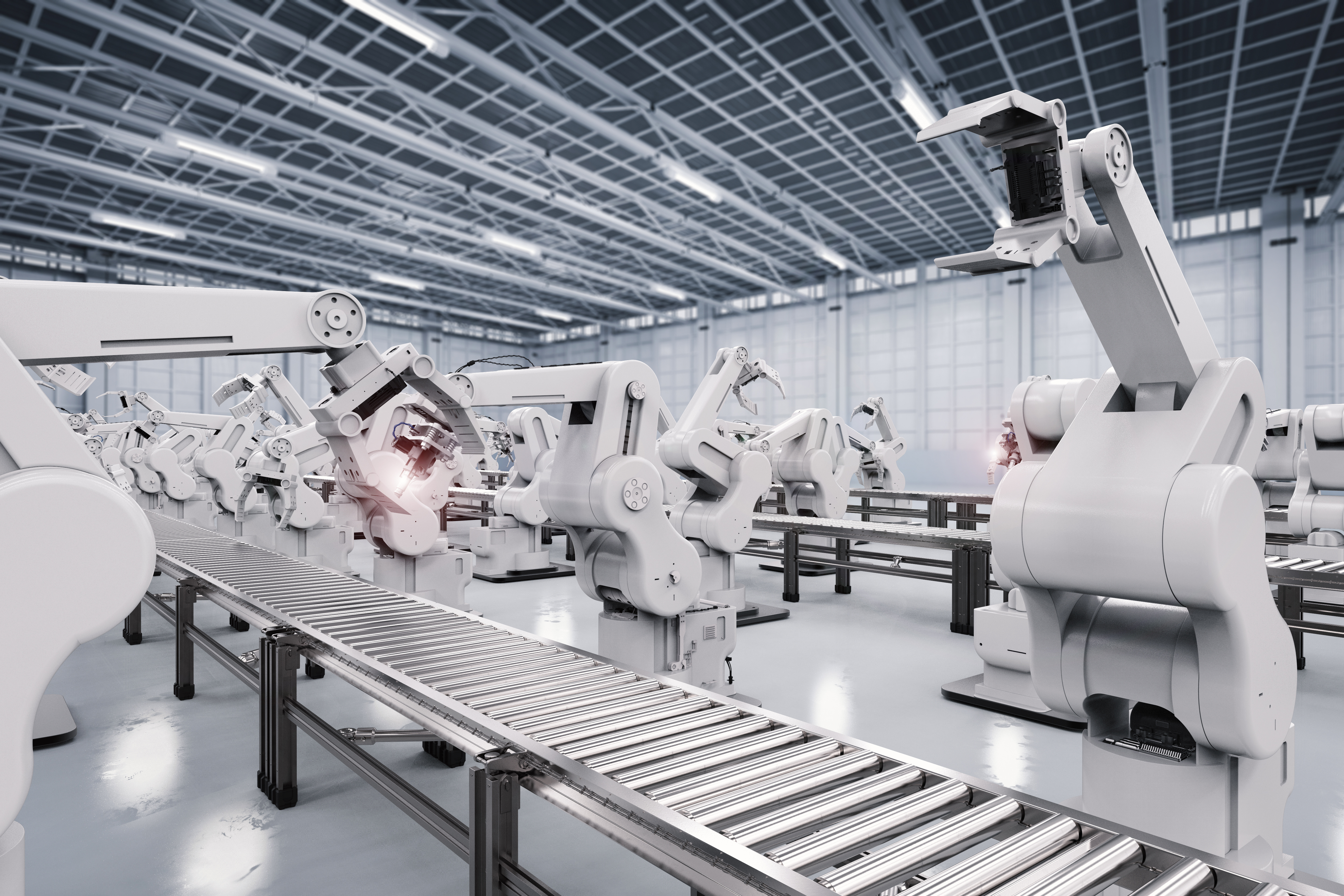
Carts and Dollies
For short-distance transport, carts and dollies equipped with high-quality casters provide a simple yet effective solution. Though they require manual operation, these tools provide a safe, convenient alternative to forklifts.
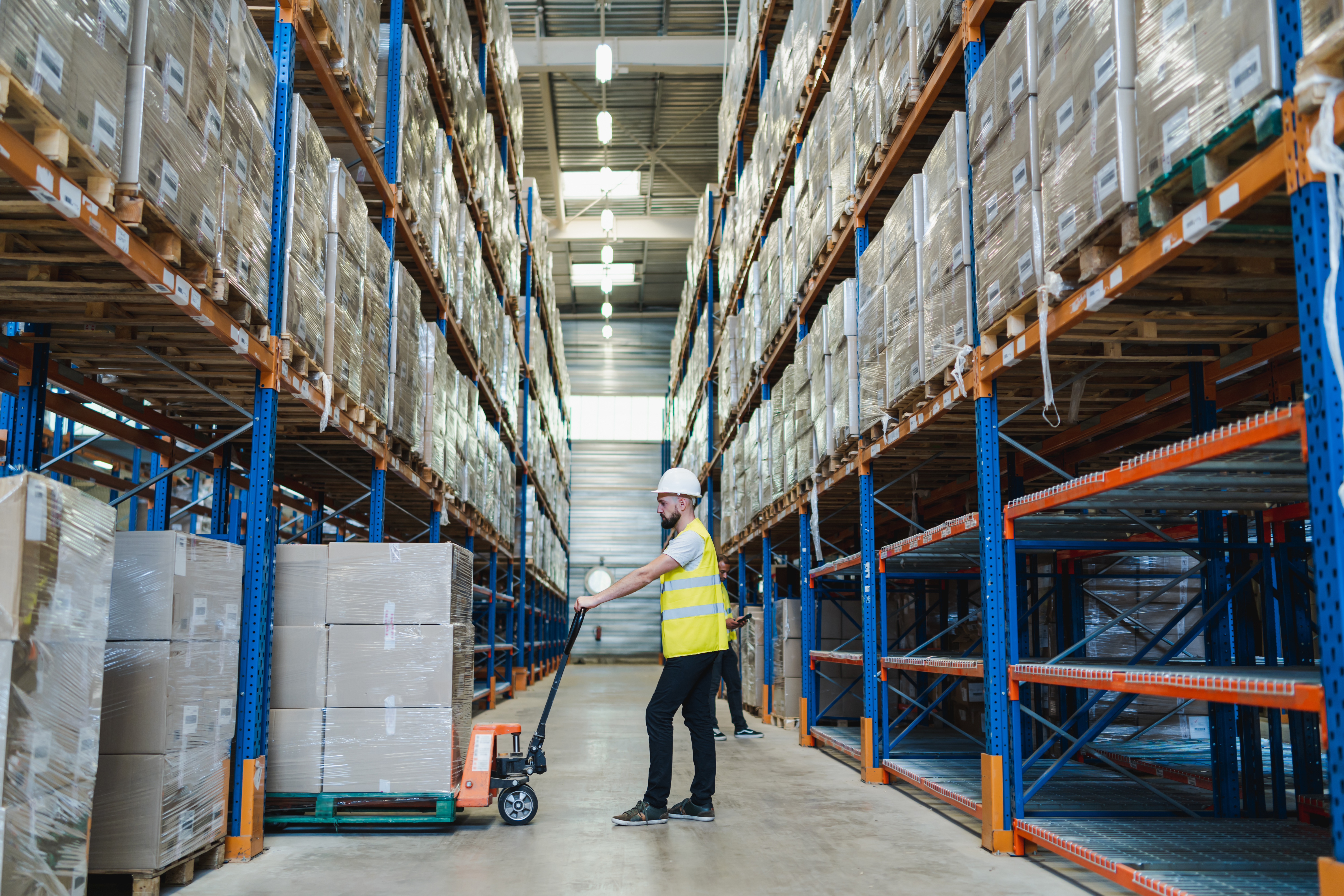
Implementing A Forklift-Free Strategy
Making the switch to a forklift-free operation requires careful planning. Here are some steps you should consider when deciding to go forklift-free.
1. Assess Your Current Operations
Conduct a thorough analysis of your processes to determine where forklifts are most used and determine the feasibility of alternative solutions. Collect detailed data, such as the types of goods transported, the weight and dimensions of loads, the frequency and distance of trips, and the layout of the facility. This will help you make an informed decision about the most appropriate forklift-free solution to implement without compromising productivity.
2. Evaluate Your Alternatives
Research and evaluate the various forklift-free options available. Determine which alternative solutions are most compatible with your current infrastructure and systems and assess what costs would be required for their implementation. For instance, AGVs might be ideal for long distance transport within a warehouse, while conveyor systems could be more effective for fixed, repetitive movements.
3. Invest In Training
Ensure that your employees are adequately trained to operate new equipment and understand the benefits of the forklift-free initiative. Safety protocols and best practices should be prioritized, such as performing regular equipment inspections, to prevent accidents and injuries.
4. Gradually Transition to A Forklift-Free Operation
Before you begin replacing all your forklifts with alternative solutions, run a pilot project to test the effectiveness of them. Gather feedback, make necessary adjustments, and gradually phase forklifts out of the rest of your facility. Collecting data is extremely important at this step, to ensure that your alternatives are meeting performance goals.
5. Monitor and Optimize
Continue to monitor the performance of the new systems and make data-driven decisions to further improve your operations. Regular training for staff and equipment maintenance and updates will help ensure long-term success. Be sure to keep your keep your automated vehicles up to date with the best casters and wheels.
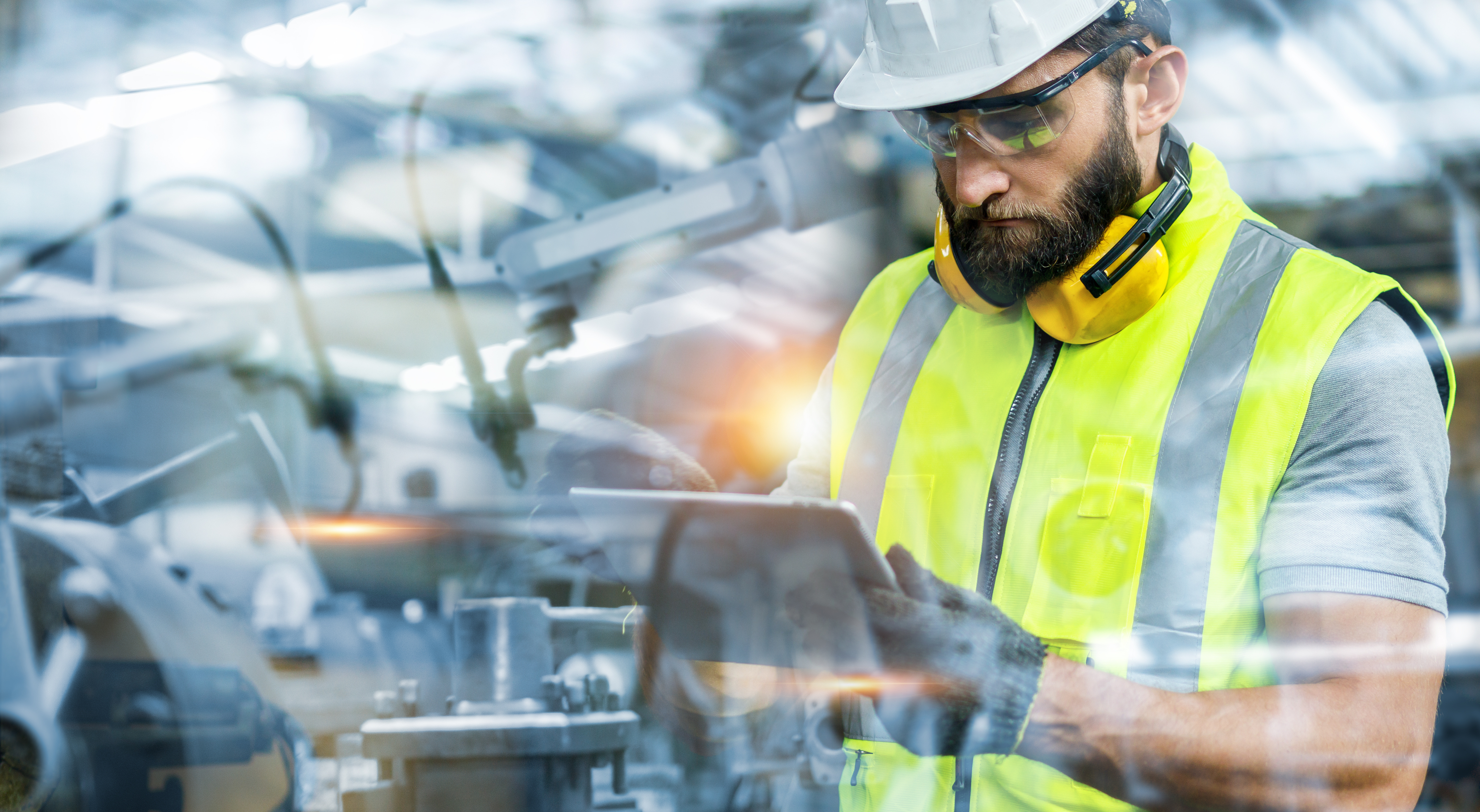
Creating A Path to A Safer, More Efficient, and Sustainable Future
The forklift-free initiative is paving the way for material handling facilities to move towards safer, more efficient, and more sustainable operations. By embracing innovative automated solutions, such as AGVs, AMRs, and conveyor systems, companies can transform their systems and gain an advantage in a competitive landscape. As a leading provider of industrial casters, we are committed to supporting this transformation with solutions that enhance mobility and performance.
Interested in finding more information on automation and how it can help you enhance safety and productivity? Contact a trusted provider, like Caster Connection for expert advice and guidance on what mobility solutions to use with your automated vehicles.
Want To Catch Up on What Else Is Happening in Industrial Automation?
Download Our Free Whitepaper →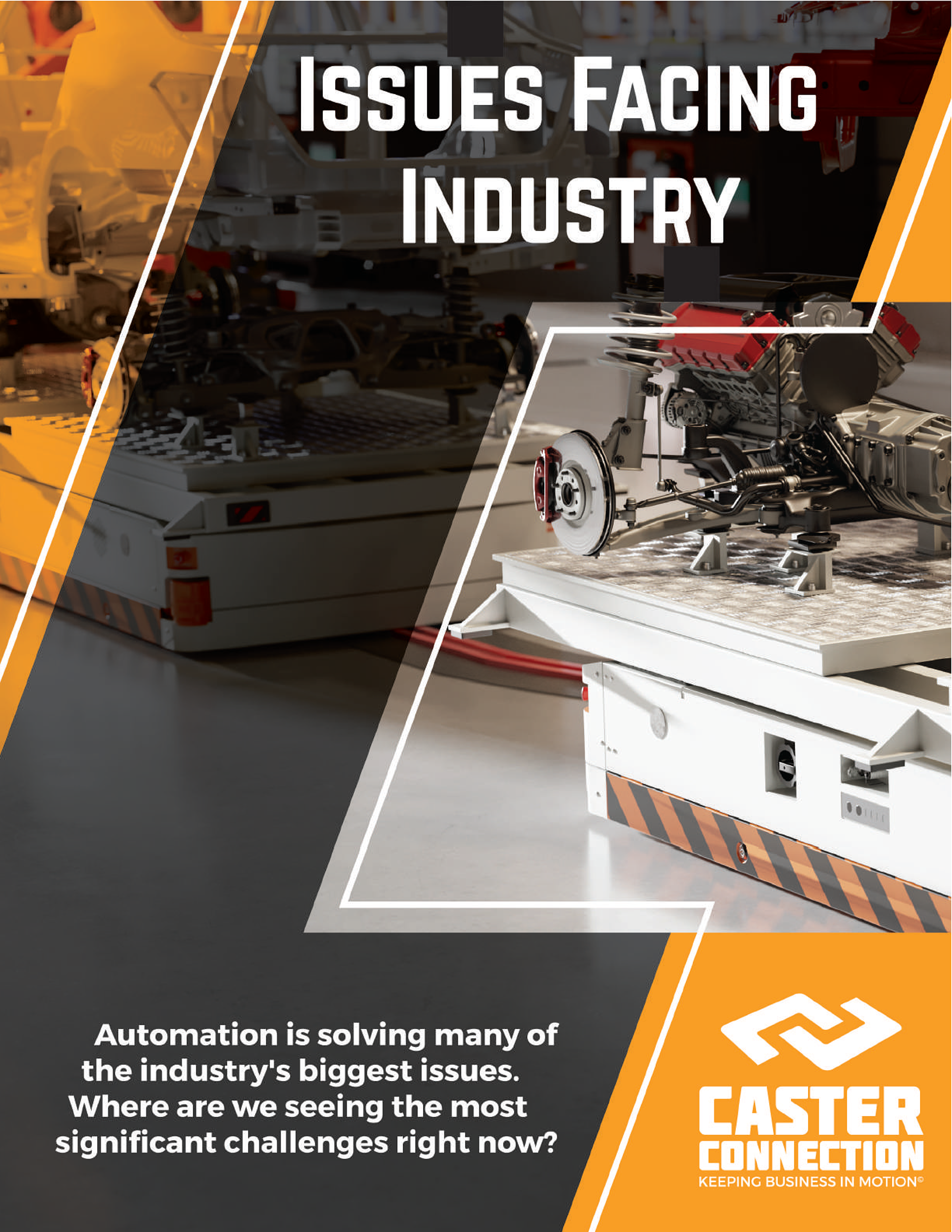