SUMMARY & ANALYSIS OF THE OSU SRI STUDY: IMPROVEMENT OF PUSH/PULL FORCE ESTIMATES USING A SINGLE-AXIS GAUGE
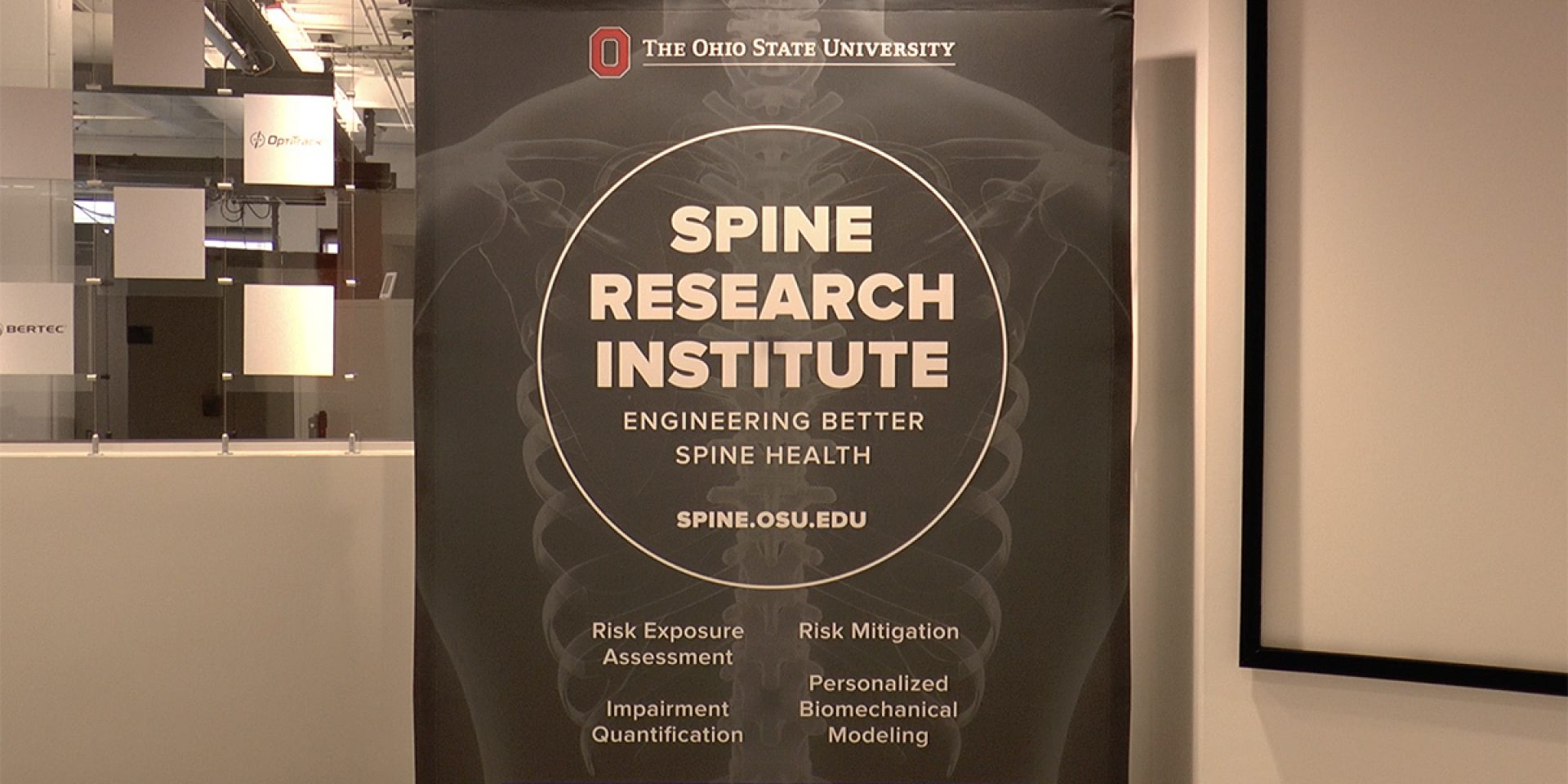
One of the primary aims of improving ergonomics in material handling is to prevent injury to the lower back. Since injuries to the back cost companies billions of dollars each year and cause pain and suffering for thousands of employees, companies need a reliable way to improve ergonomics in their facilities.
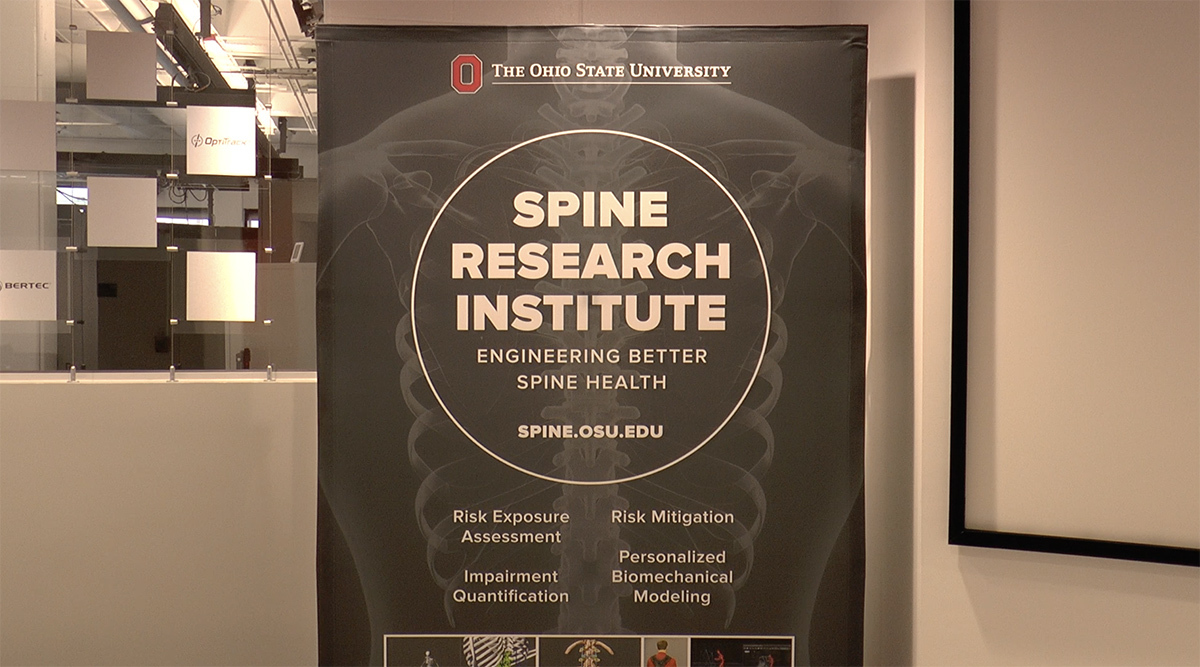
Improving equipment, specifically casters, to decrease push/pull can significantly improve ergonomic initiatives. However, in order to verify that push/pull has improved, practitioners need a reliable way to measure push/pull forces.
For this reason, Caster Connection collaborated in a study with The OSU SRI (Ohio State University Spine Research Institute) within the CDMI (Center for Disruptive Musculoskeletal Innovations), which is funded and supported by the NSF (National Science Foundation). The study was conducted within the Spine Research Institute’s laboratory over a period of 10 months. The results of this study reveal that many practitioners are more than likely putting workers at risk for a lower back injury because of non-real-world measurements.
PERFORMING THE STUDY
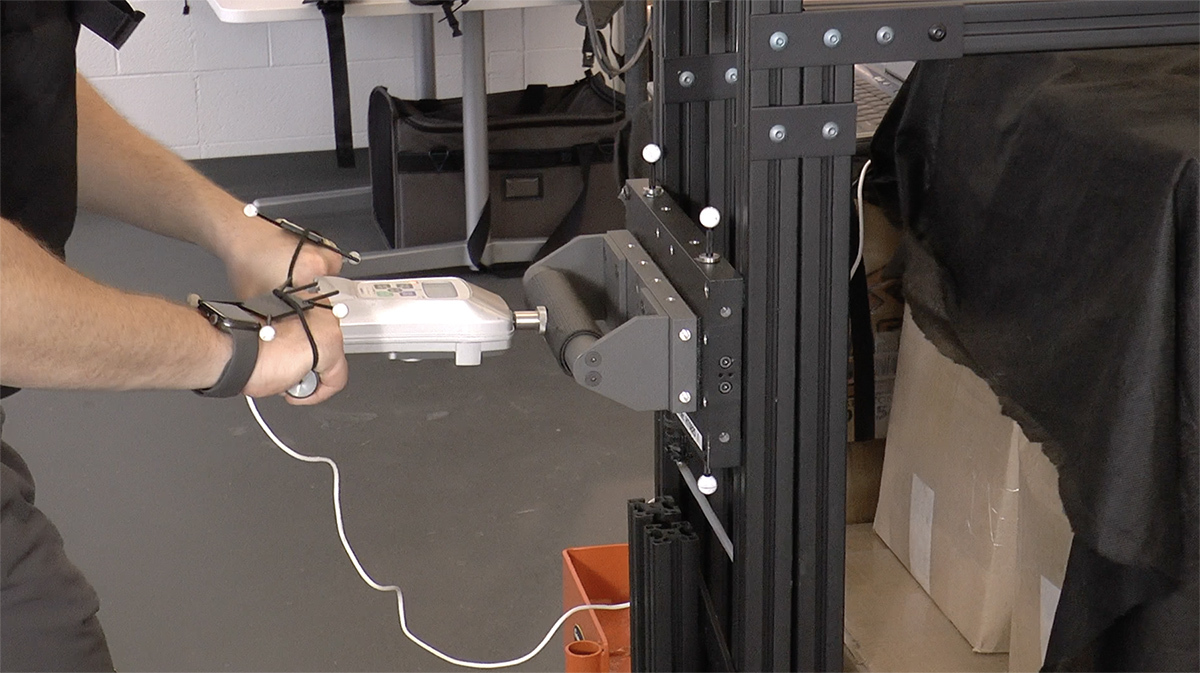
In the study, volunteers pushed, pulled, and turned (while pushing) a manual materials handling cart outfitted with four CC Apex caster wheels combined with four CC Alpha kingpinless rigs. The study employed two main forms of force measurement, a three-dimensional hand transducer (the gold standard of push/pull measurement) and a single-axis force gauge (the most common measurement tool in industry). Push/pull forces were recorded simultaneously from both the three-dimensional hand transducer and the single-axis gauge for two separate cart weights and three separate paces (slow, fast, and self-selected). Slow and fast paces were based on variations of the current best-practices described by the International Organization for Standardization (ISO), while the self-selected speed allowed volunteers to move the cart at the speed and acceleration that felt most comfortable to them. The self-selected pace was also measured without the single-axis force gauge (using the three-dimensional hand transducer only), so as to record push/pull forces that most closely resemble actual push/pull forces workers would encounter within industry.
BASIC RESULTS FROM THE STUDY
As shown in the graphic below, push/pull forces recorded for the “fast” pace with a single-axis gauge most closely matched push/pull forces recorded for the self-selected pace without a gauge. In other words, the fast pace most closely equated to the forces that employees within industry would actually encounter. Another takeaway is that future research is needed to improve push/pull force measurements when turning.
The following graphic information was taken from a report produced by the OSU SRI and the CDMI.
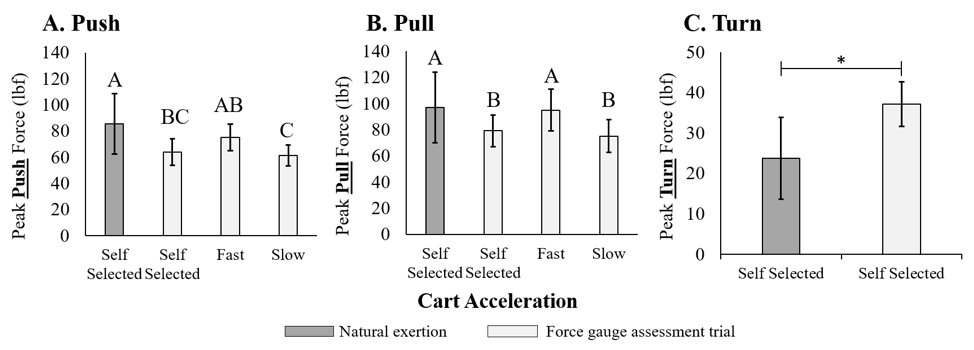
Magnitude of peak hand force estimates separated by assessment type and cart acceleration for (A) pushing, (B) pulling, and (C) turning exertions. Letters above groups denote post-hoc Tukey results, where groups not connected by the same letter differ significantly from one another. * represents a statistically significant difference p<0.05.
ANALYSIS OF THE STUDY AND IMPLICATIONS FOR INDUSTRY
The study revealed two primary implications for industry. First, the study revealed that practitioners can indeed use a single-axis force gauge with relative accuracy when compared to a three-dimensional hand transducer. That means that industry can continue to use a single-axis force gauge, but only under certain conditions and when using specific guidelines, namely making sure that the practitioner applies force as close to the horizontal as possible.
The second primary result, as mentioned above, was that when practitioners moved at the fast pace, their results most closely resembled subjects moving a cart at a self-selected pace without the gauge, which should be the push/pull force most equating to that which occurs within material handling facilities.
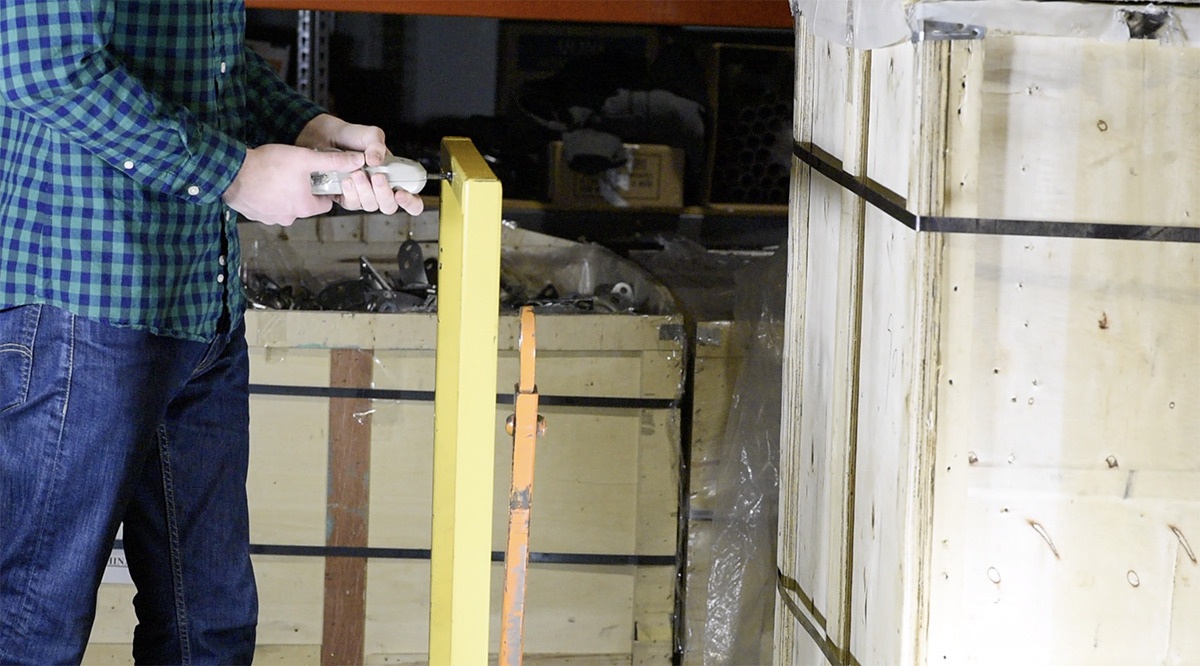
This has some further implications for industry. Namely, because the study showed variance in push/pull measurements based on acceleration and speed, force measurements done in industry facilities with a single-axis gauge may underestimate injury risk to the lower back. This is because the current push/pull testing standard (ISO 11228-2) calls for push/pull forces to be recorded at a slower pace than what was tested in the OSU SRI study. That is, while the current ISO standard successfully records differences between casters or other factors surrounding cart design, it may not accurately assess the push/pull forces exerted in a natural setting and application.
The fast pace tested in this study (1 m in 3 seconds, 0.5 m/s sustained) conducted with the gauge most closely resembles push/pull forces occurring in a natural environment, i.e., self-selected without the gauge. Therefore, practitioners should consider using this faster pace in their push/pull testing moving forward. This is the major implication of this study.
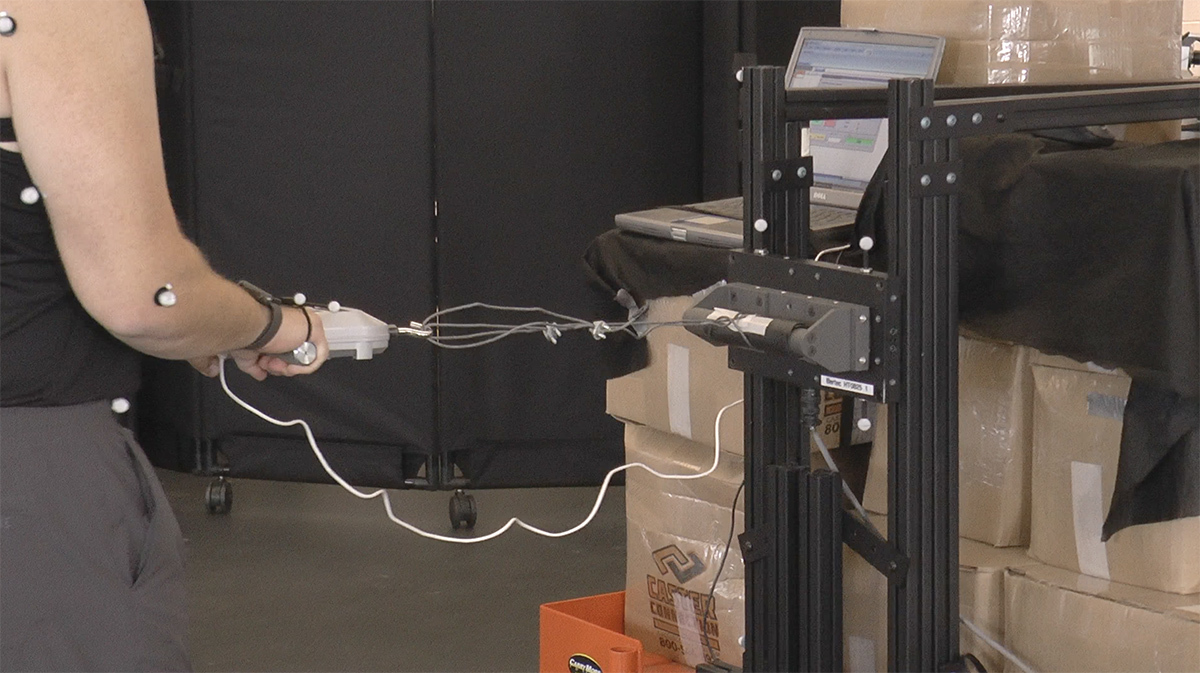
A minor result of this study was to highlight the tremendous need for studies of turning while measuring with a force gauge. Results from this study showed an extreme inconsistency when turning was measured with the single-axis force gauge. At this point in time, there is no perfect standard for measuring turning forces measured with a single-axis force gauge, and therefore, it is difficult to understand the ergonomic risks associated with turning.
The study also pointed to the fact that practitioners must test for both pushing and pulling (as shown above). These two activities do not necessarily produce the same results, so it is in the best interest of those involved in push/pull measurement to perform testing for both of these movements.
INDUSTRY PROBLEMS CONNECTED TO THIS STUDY
This study highlights the need for consistent testing at a faster initial and sustained acceleration/velocity in order to match push/pull force measurements from a single-axis force gauge to push/pull exertions that workers encounter within industry. The pace recommended in the study (1 m in 3 seconds, 0.5 m/s sustained) is faster than that suggested in ISO 11228-2.
In addition to this, the study conclusively demonstrates that a practitioner can obtain widely different force measurements for the same cart weight by simply varying the initial and sustained acceleration/velocity. It may be tempting from an industry perspective to conduct multiple tests internally (at whatever rates of acceleration/velocity are expedient or traditional) to get favorable push/pull measurements, but these forces may not approximate those forces actually encountered by the individuals pushing/pulling that cart in their job role.
While ISO has established a standard by which all companies can compare products, many companies are not adhering to any established standard. In this way, practitioners are verifiably assessing neither injury risk nor a consistent comparable push/pull force. Following the recommendations provided in this study will accomplish both of these, but this may change a company’s historical measurement results and therefore may alter established push/pull force benchmarks within a company.
USING THE DATA FROM THIS STUDY
This study affects two main aspects of a business’ operations and ergonomic initiatives: comparing equipment, for example casters, and assessing injury risk to employees. As stated above, a company can use the acceleration/velocity guidelines provided in this study in order to be the most accurate on both counts.
Another option is to maintain historical measurements, which a company may have taken over years, or perhaps decades, by continuing to use a company’s current measurement standards/approach in order to compare casters or other equipment to these historical measurements. This is done with the understanding that there is often extreme inconsistency from business to business in their own measurement approach.
However, at no point should these numbers (taken from testing with ISO or a company’s traditional push/pull standards) be used to assess injury risk to employees. Strictly adhering to the standards provided in this CDMI study, which is the most advanced and nuanced push/pull measuring study to date, will allow a company to better gauge injury risk and therefore best protect its valued employees.