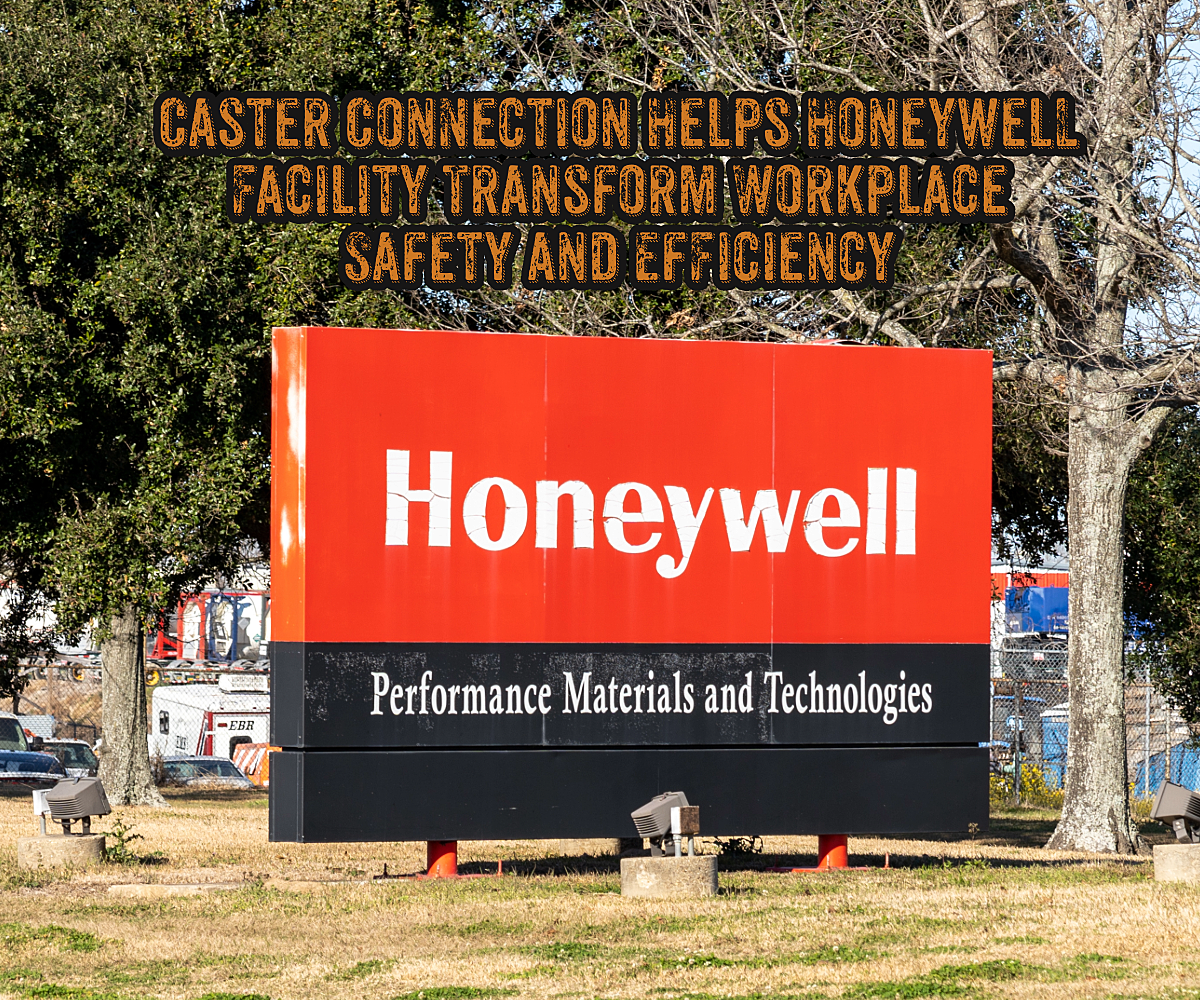

Background:
Honeywell is a leading engineering and manufacturing conglomerate producing cutting-edge technologies across numerous industries. The focus of this case study is a Honeywell facility in Virginia that produces high tensile strength fiber that is pound-for-pound, fifteen times stronger than steel. This facility faced a significant challenge in its production process because this fiber, though incredibly strong, had a propensity to get caught in the wheels of its buggies and carts, leading to injuries and downtime. Seeking a solution, Honeywell turned to Caster Connection, an innovative caster and wheel solutions provider.
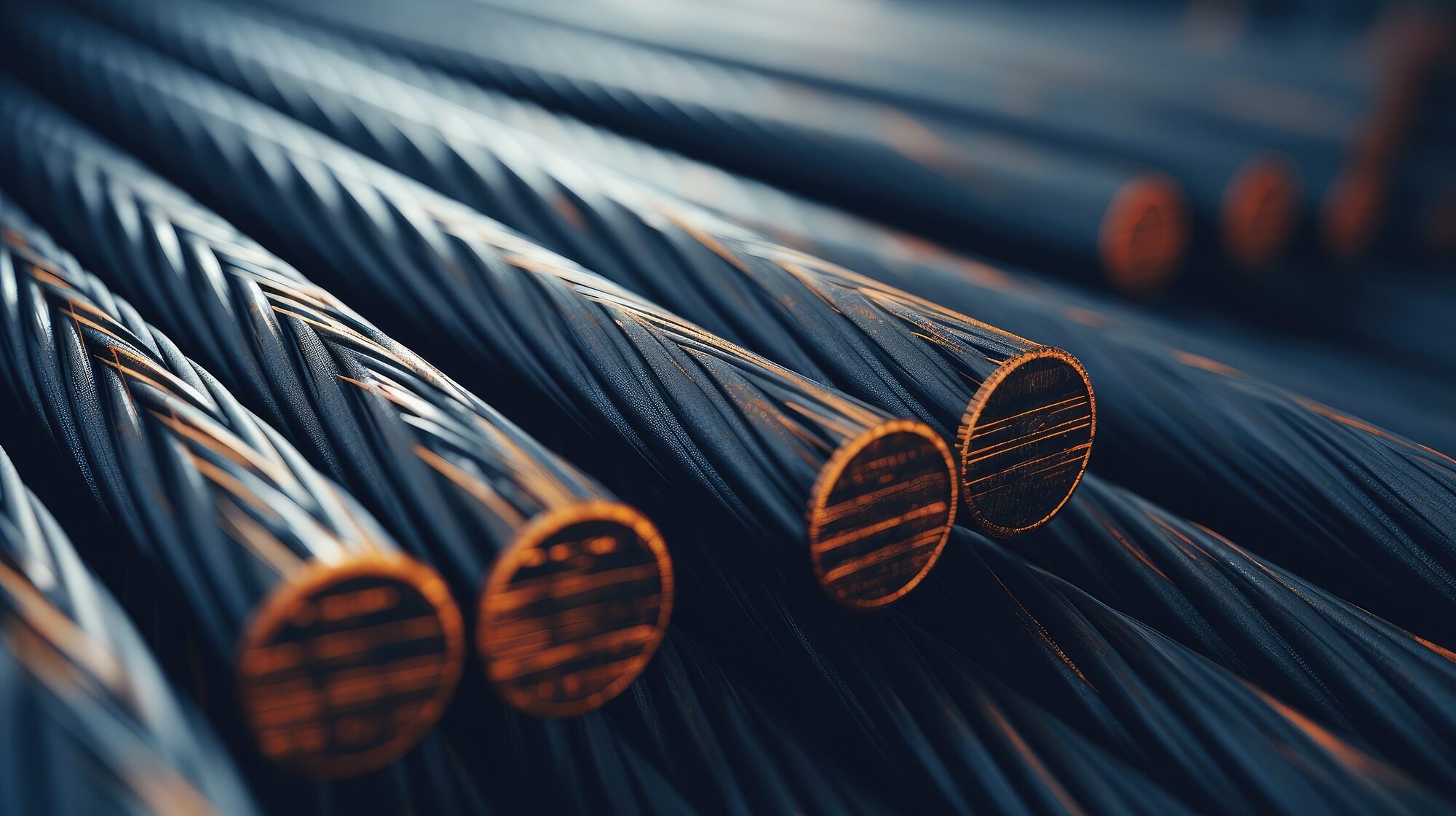

The Problem:
While vital for a variety of industrial-strength products, ballistic armor, and medical devices, Honeywell’s high tensile strength fiber created operational challenges. At the time, this facility used flat-tread, higher durometer wheels on carts and buggies used throughout the facility that tended to accumulate debris because of their more rigid material lacked rebound resilience. Their larger surface area combined with their inability to dispel debris was becoming a liability because bits of string fiber would accumulate on the factory floor and get entangled in the wheels of their buggies and carts. These entanglements were leading to safety hazards, injuries, and operational downtime. Because this string fiber is so strong, once it seized a wheel on one of these carts, it would take hours to untangle and cut away.

Caster Connection’s Solution:
While on a conference call with another Honeywell facility, Patrick Thompson (Maintenance Supervisor/Planner) and Richard Edens (Maintenance Planner) received a recommendation to reach out to Caster Connection from another Honeywell employee who was familiar with our expertise. After receiving the recommendation and reaching out, Thompson and Edens were connected with Brett Russell, a Regional Solutions Manager with Caster Connection. Upon hearing about the facility's pain points and what they were looking for, Brett Russell provided Thompson and Edens with free samples of our 8-inch CC Apex casters.
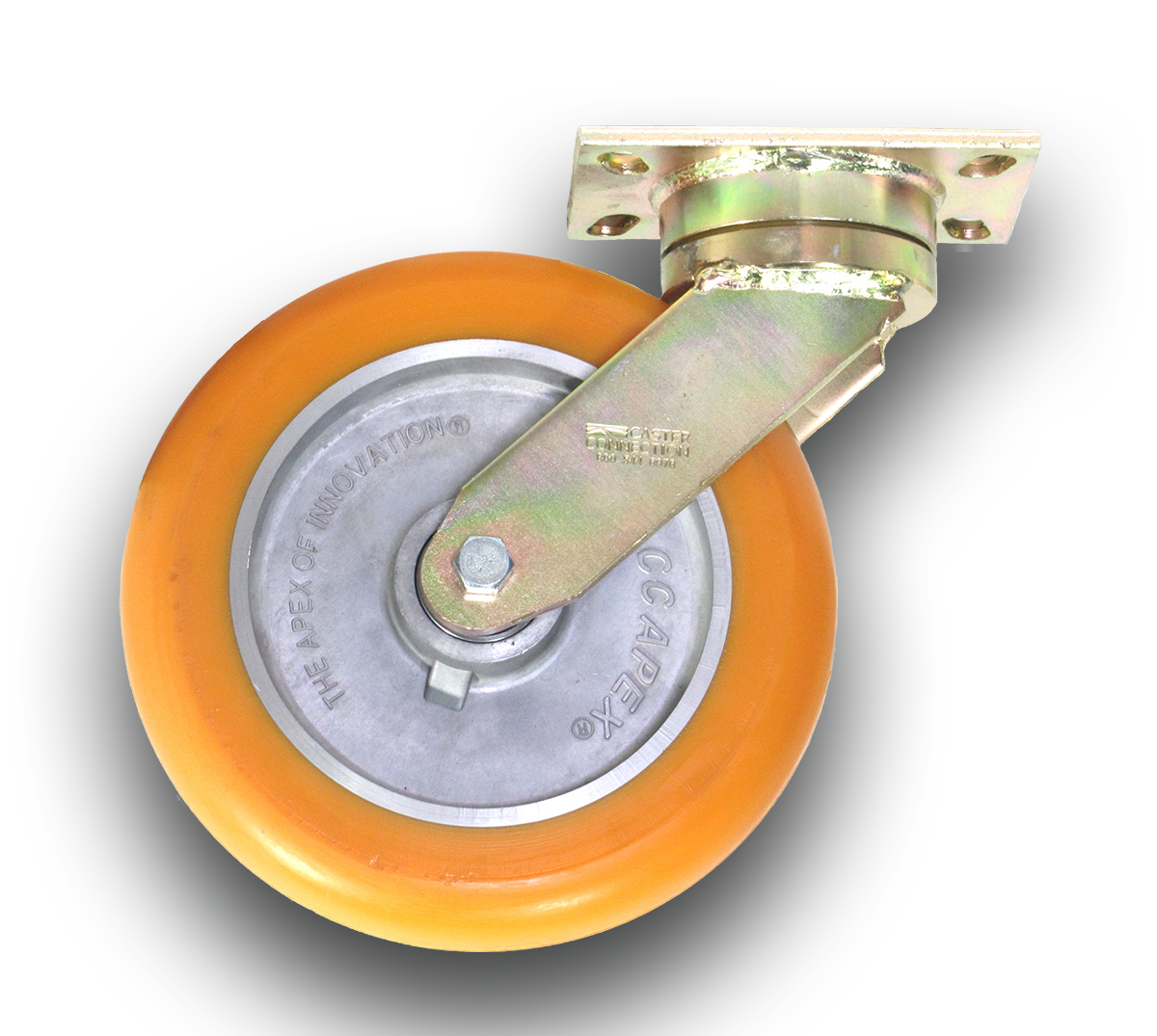

Implementation and Results:
The Honeywell facility tested the CC Apex wheels and found that they significantly reduced string accumulation, improving both safety and productivity. They systematically replaced the existing wheels on their buggies with CC Apex wheels, eliminating injuries related to the entangled string issue. Since then, the team began the year-long process of upgrading all their carts and buggies with CC Apex wheels.
This Honeywell facility plans to continue implementing CC Apex wheels on various buggies based on their specific needs. They also intend to standardize wheel sizes to simplify inventory management and ensure seamless replacements when needed.

Benefits:
1. Enhanced Safety—Reduced string accumulation significantly reduced the risk of injuries associated with moving buggies.
2. Increased Productivity—Operational downtime due to wheel maintenance was minimized, leading to increased productivity.
3. Cost Savings—The CC Apex wheels’ durability meant fewer replacements, leading to cost savings in the long run.
4. Innovative Solution—The introduction of bow tie pins, suggested by Honeywell and supported by Caster Connection, further streamlined wheel maintenance, enhancing overall efficiency.

Conclusion:
Caster Connection’s tailored solution resolved this facility's safety concerns and improved its operational efficiency. The collaborative approach between Honeywell and Caster Connection and innovative ideas like the bow tie pins exemplify how strategic partnerships can lead to transformative outcomes in industrial settings. Honeywell’s experience showcases the importance of understanding a client’s unique challenges and providing customized solutions to drive positive change in the workplace.
Work for Honeywell? Discover how Caster Connection can help your facility?
Infinite Opportunities Await
Get Rolling with a Caster Connection Solutions Expert →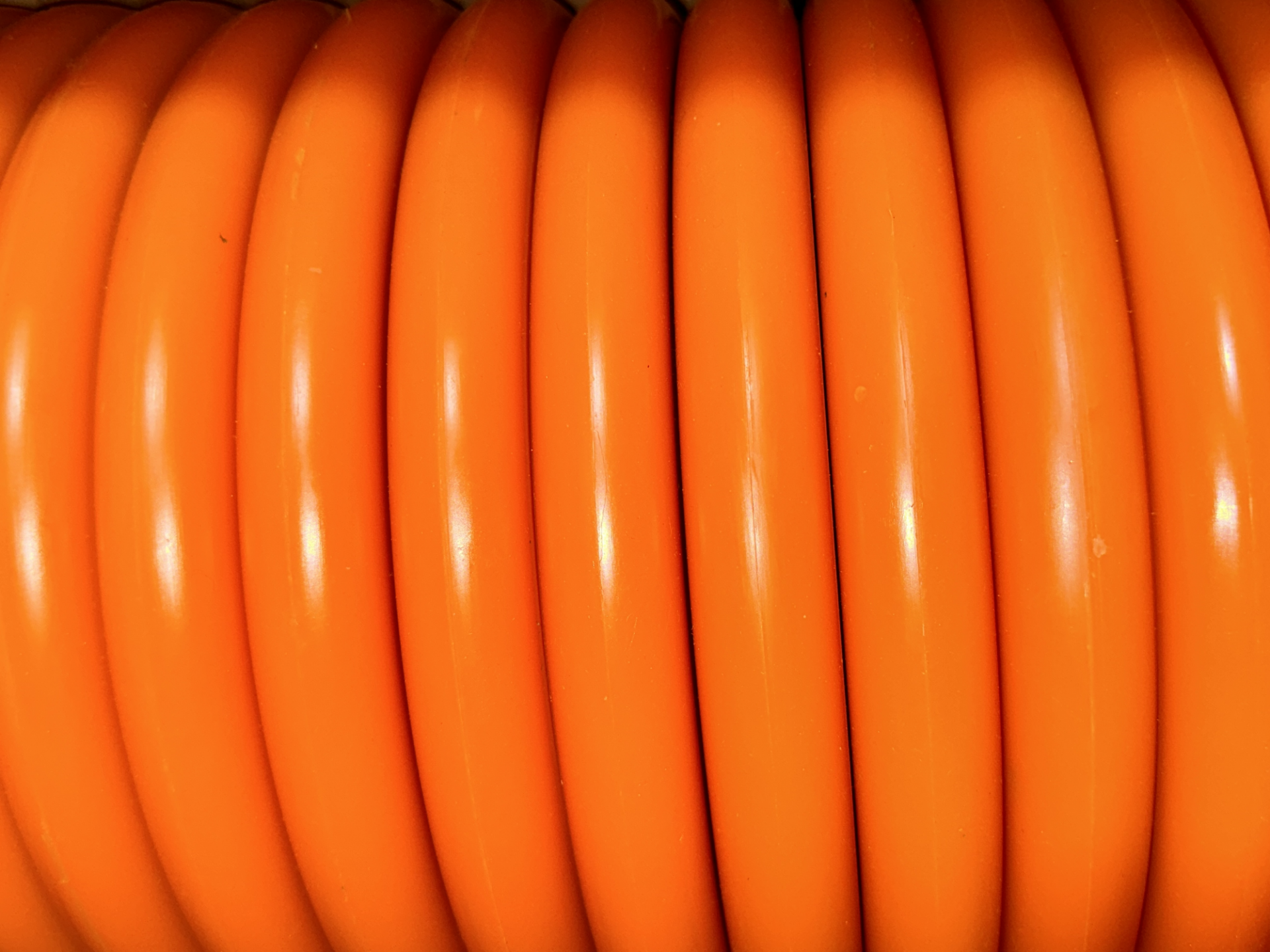