Material Handling Flexibility for an Auto Parts Maker
When purchasing casters and wheels, the quality of the sellers’ client service is often as important of a factor as the quality of the products being purchased. A manufacturer of automotive parts and accessories found that although the casters they were using on their Automated Guided Vehicles worked sufficiently, the supplier they ordered from was struggling to deliver their product in an efficient manner. The supplier required a 20-week lead time, and because the wheels were custom made, they were also expensive.
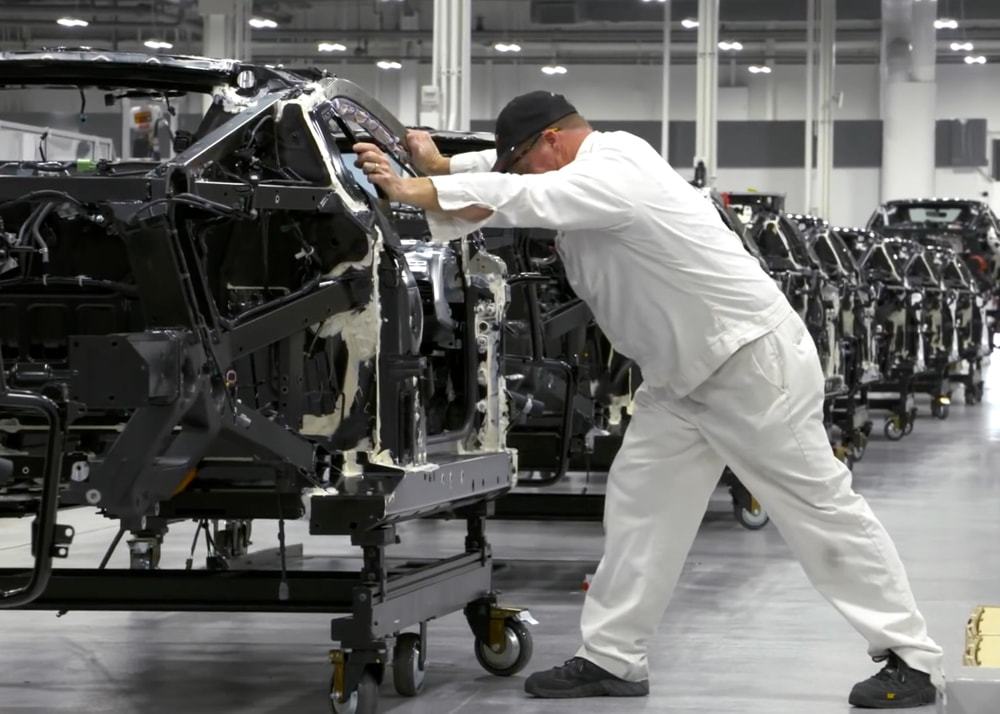
Because they were unhappy with their lead time and pricing, the automotive manufacturer reached out to Caster Connection for help. One of Caster Connection’s Regional Solutions Managers (RSM) was sent to investigate the problem and find a solution for the client’s needs. Our RSM quickly thought of two solutions for the frustrated company:
- First, we had the wheels that the client currently had in use retreaded with high-grade polyurethane. This cut their costs in half and was a quick fix to the 20-week lead time.
- Second, Caster Connection contacted a new manufacturer to have new wheels made to their exact specifications. This was a difficult task because the AGV’s use sensors on the floor to determine their path. These sensors are very sensitive to the height of the wheels in use, so the wheels had to be precisely the same size.
By manufacturing new wheels for the company, Caster Connection was able to reduce the 20-week lead time to only 4 weeks, and cut the cost of the wheel by $100. When it comes to getting the right solution for your material handling problems, no one can beat the experience of Caster Connection and our trusted experts.
WANT TO BE OUR NEXT SUCCESS STORY? LET'S TALK!
Get Rolling with Caster Connection →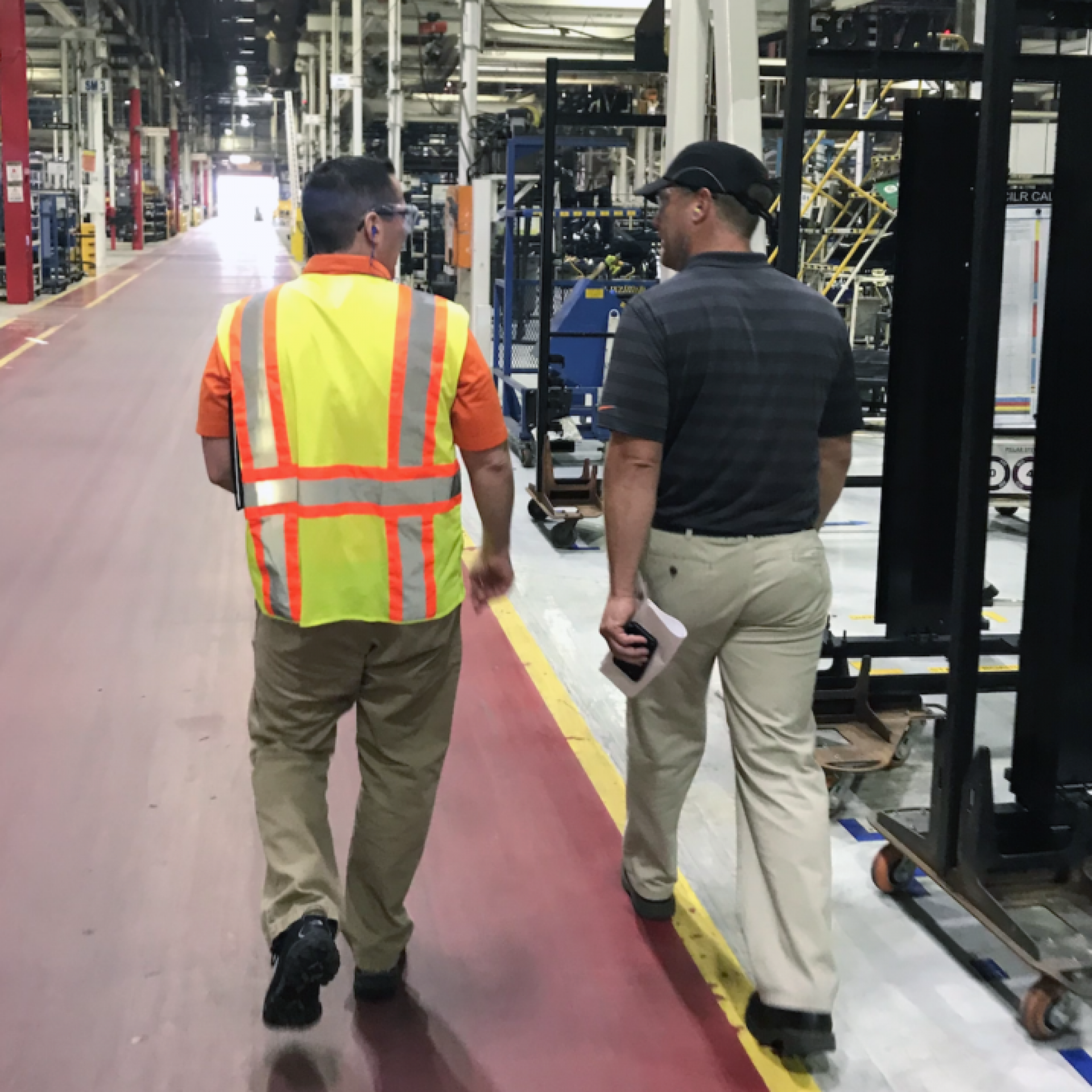