Tier 1 Automotive Manufacturer Sees Ergonomic Performance and Operational Efficiency Improvements With CC Apex
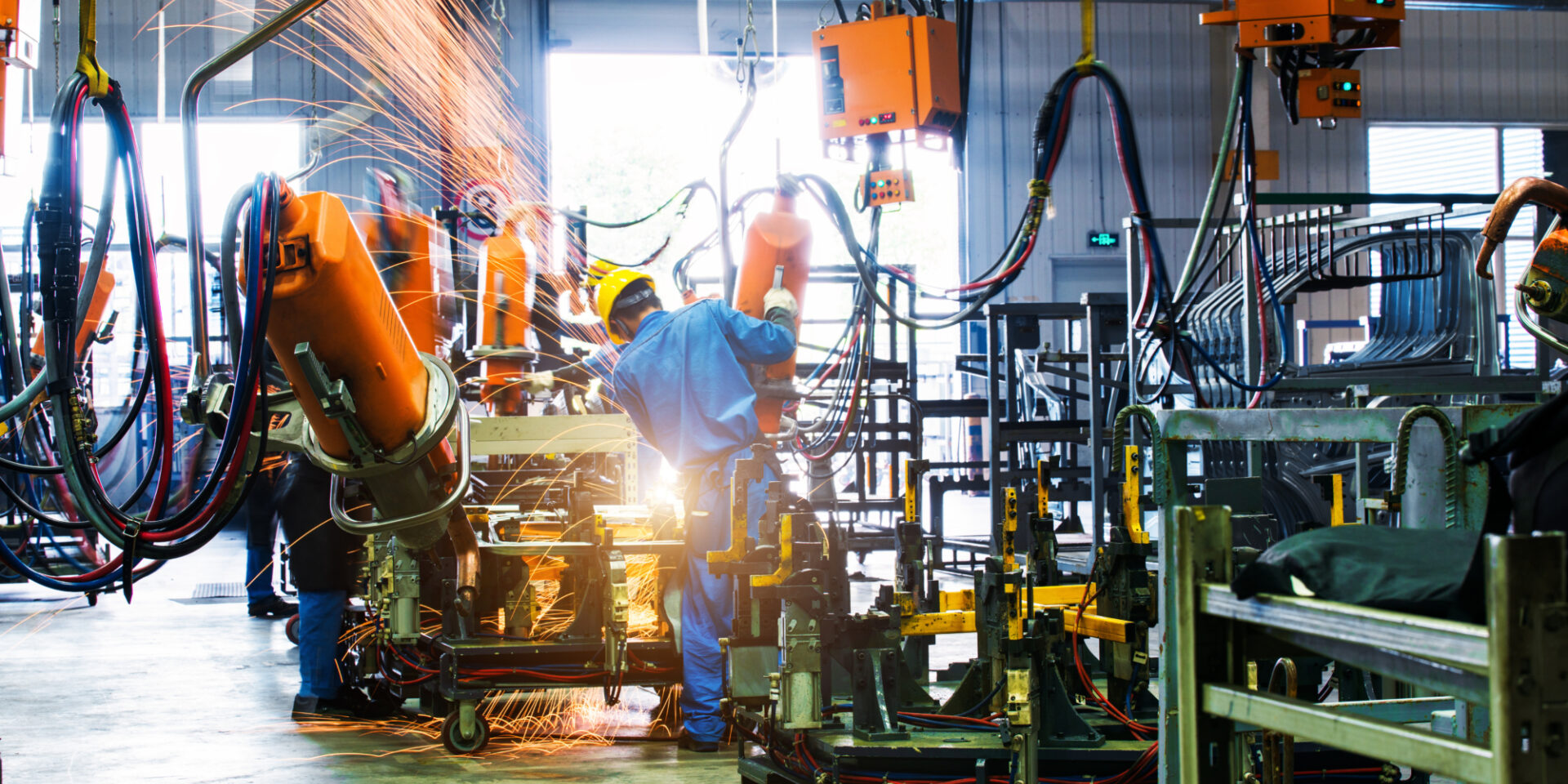
This case study provides a detailed overview of the client's challenges, the collaborative solution provided by Caster Connection, and the resulting benefits and outcomes. It underscores the shared effort taken to address Tenneco's unique requirements and the potential for future expansion and innovation in caster solutions.
Client Background
This Tier 1 facility, a prominent manufacturer of gas-powered engine components, grappled with unique challenges at its Nebraska facility. The use of phenolic casters led to issues such as debris accumulation, floor damage, and ergonomic strain, necessitating a solution that could enhance operational efficiency and workplace safety.
Client Needs
- Address ergonomic issues caused by manual handling of carts.
- Resolve problems related to debris retention, particularly metal shavings on the floor.
- Find a cost-effective solution that ensures long-term durability and performance to prevent downtime.
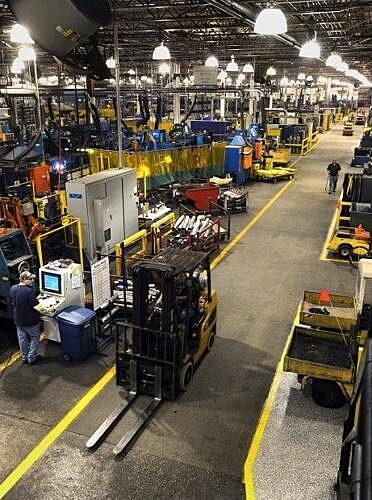
Solution Provided By Caster Connection
Through a collaborative effort, Caster Connection and the tier 1 automotive manufacturer identified and implemented a solution tailored to the specific challenges faced by the company. After a comprehensive assessment of the facility's mobility needs, Caster Connection recommended the use of 6-inch CC Apex casters, specifically the 6 x 2 kingpinless extended lead with matching rigid casters. These casters, with their superior durability, ergonomic design, and debris resistance, were a perfect fit for this facility's manufacturing environment.
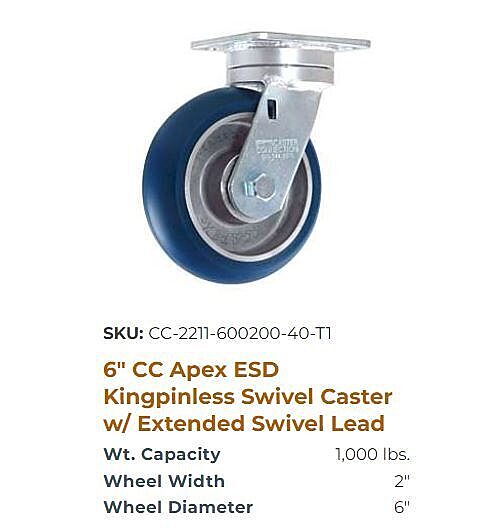
Implementation Process
- Caster Connection conducted a CC CHAT (Caster Health Assessment Tool) session to assess Tenneco's needs and challenges.
- Samples of the recommended casters were sent to Tenneco for evaluation and testing.
- Following successful testing, this facility has adopted the 6-inch CC Apex casters as its standard caster solution for the past five years.
- Caster Connection provided ongoing support and maintenance to ensure optimal performance and customer satisfaction.
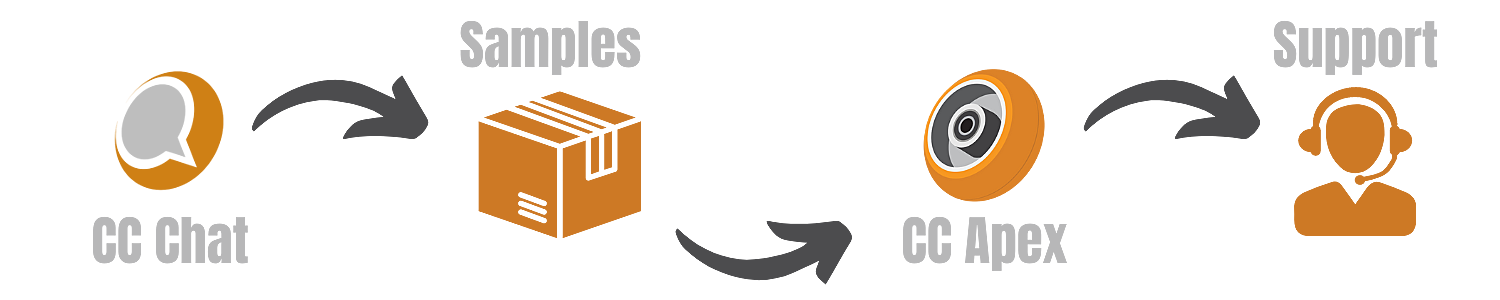
Results and Benefits
- Significant push/pull effort reduction, estimated at 25% or more, alleviating ergonomic strain on workers.
- Improved workplace safety by minimizing debris buildup and floor damage, enhancing overall operational efficiency.
- Cost-effective solution with long-term durability, reducing maintenance costs and downtime.
- Enhanced reliability and performance, contributing to this company's commitment to quality and productivity.
Conclusion
Through collaboration with Caster Connection, this tier 1 automotive manufacturer successfully addressed ergonomic challenges and improved operational efficiency in their manufacturing facility. By adopting durable and ergonomic caster solutions, this facility enhanced workplace safety, reduced maintenance costs, and optimized productivity. This case study highlights the importance of customized solutions tailored to the specific needs of industrial environments, driving positive outcomes for businesses and their workforce.
WANT TO BE OUR NEXT SUCCESS STORY? LET'S TALK!
Get Rolling With Caster Connection →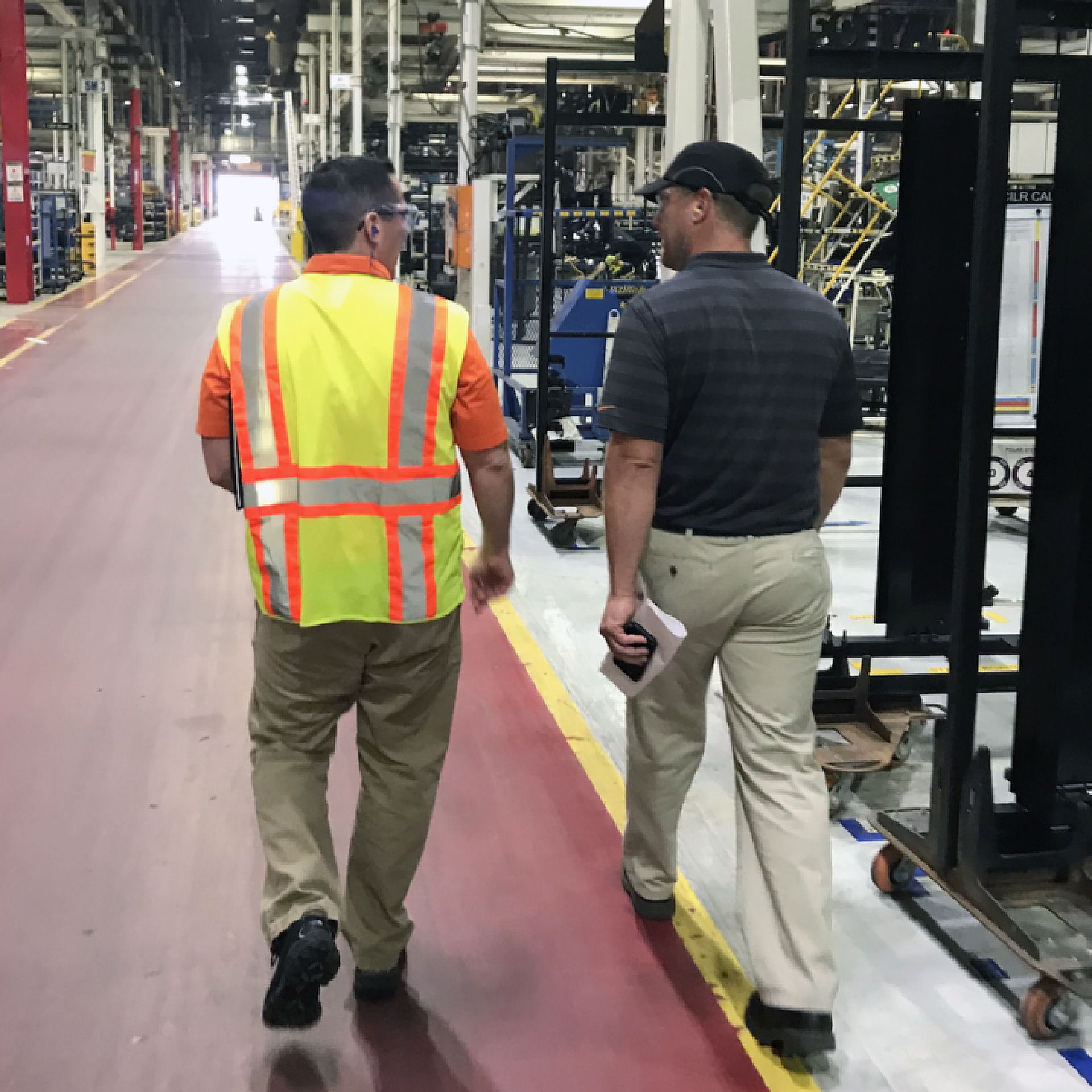