Bodyweld: The Right Wheel for the Application
Automotive plants are one of the toughest environments when it comes to operating truck carts, WIP carts, tugger carts and other material handling systems. Automotive plants typically operate morning, afternoon and night shifts, which puts tremendous pressure on the wheels and casters on material handling systems. And that puts tremendous pressure on plant managers to make sure they have the right casters and wheels on their units.
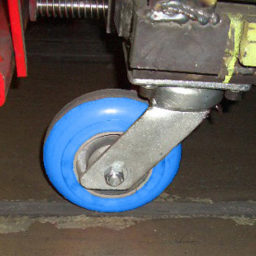
The wrong casters damage floors, injure workers, and increase noise levels, and when a cart fails and has to be taken out of production, that immediately risks halting production—a costly proposition.
This is the challenge that one of Caster Connection’s clients faced.
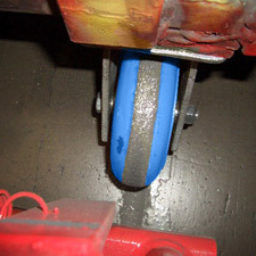
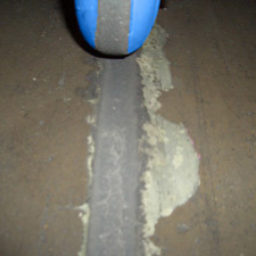
Company
The company is a major automotive manufacturer based in the United States. Their plant operates 24 hours a day, assembling a range of automobiles for a variety of markets. Within the plant is a shop responsible for welding auto body parts.
This shop uses Automated Guided Vehicles (AGVs) to move the auto body components into, through and out of the shop as part of the automotive production process. At this facility, their AGVs are typically loaded 450kg over their rated capacity.
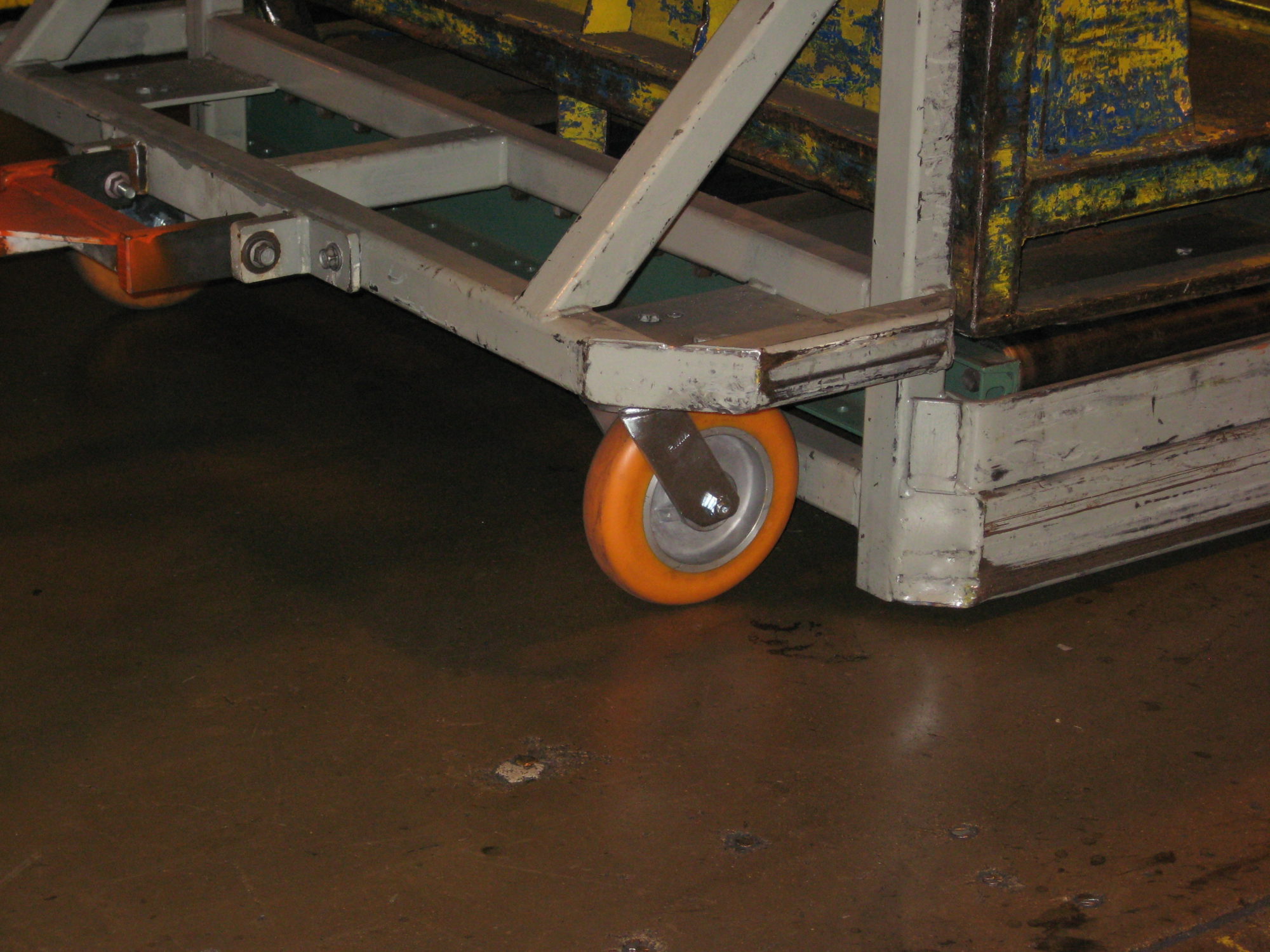
Challenge
The body weld shop had a problem with the casters on its AGVs. The rubber treads on the caster wheels collected weld dust, slag and metal shavings off the shop floor. This debris eventually embedded itself into the tread, so that the entire portion of the wheel coming in contact with the floor was metal, not rubber.
The wheels then damaged the floor in the shop by wearing a permanent groove into the floor. This groove caused many problems for the AGVs, often throwing them off their intended course when the AGVs changed direction, causing them to collide with workers and equipment.
Solution
The automotive plant contacted Caster Connection and invited us in to examine their situation and recommend a solution.
Because of Caster Connection’s extensive experience with automotive applications, we quickly diagnosed that their problem was with the durometer (hardness) of their wheels. The wheels on their AGVs featured a polyurethane tread that was too hard for their application. Instead of deflecting debris, it allowed weld dust, slag and metal shavings to embed in the tread.
What our client needed was a softer wheel, one made from a high-quality polyurethane to withstand the constant movement. We recommended our CC Apex caster, whose high-quality polyurethane tread dispels weld slag, metal chips and other debris to protect shop floors.
The CC Apex also has a weight capacity of 1,500 lbs., more than sufficient for our client’s AGV’s, which were typically overloaded.