Improve Distribution Center Ergonomics With Industrial Cart Casters
How to Improve Distribution Center Ergonomics with Industrial Cart Casters
If your distribution center is typical, your workers are at daily risk of injuring themselves on the job from poor ergonomics.
One of the most common injuries in distribution centers is physical overexertion from pushing picker carts. Overexertion causes 35% of all work-related injuries in the United States each year. Overexertion is also the largest contributor to workers' compensation costs, and the number-one cause of lost work days.
Another common cause of lost work days in distribution centers is lower-back injuries. They account for nearly 20% of injuries and illnesses in the workplace (Bureau of Labor Statistics). Only the common cold accounts for more lost days of work.
And what do overexertion and lower-back injuries have in common when it comes to picker carts in distribution centers? Poor ergonomics. Or, to be more specific, poor ergonomics caused by poor casters.
The majority of picker carts, platform trucks and other material handling systems used in distribution centers are equipped with commodity casters that are notorious for being of poor quality, design and construction. This makes them hard to pull, push and maneuver—particularly when they are overloaded.
Commodity casters keep the sale price of carts down, but they cost workers—and their employers—plenty.
The main problem with commodity casters is that they make carts hard to push, pull and maneuver. To compensate, workers overexert themselves, and hurt their lower backs. Here’s why commodity casters are a cause of poor ergonomics.
1. Zero or Standard Swivel Leads
The swivel lead on a swivel caster is the distance between the centerline of the kingpin and the centerline of the axle. The shorter the offset, the harder the caster is to swivel. In other words, the shorter the swivel lead, the harder the cart is to get moving, push, pull and steer.
The standard lead is the most common variation in caster forks, and its length varies with the diameter of the caster. The majority of commodity casters on OEM carts used in distribution centers have zero or standard swivel leads. Zero and standard swivel leads offer greater strength for moving heavy loads, but they come at the price of making carts harder to push and pull.
Casters with extended swivel leads have a greater distance between the centerline of the kingpin and the centerline of the axle. By extending the swivel lead, the caster naturally settles into the trailing position due to the caster rotating much more easily and freely.
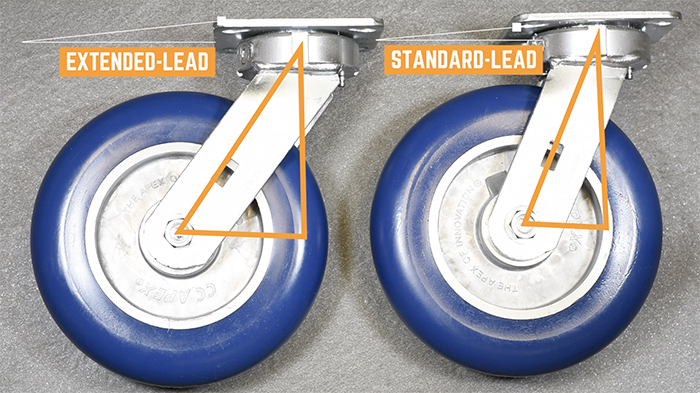
2. No Wheel Bearings
Another cause of poor ergonomic performance in commodity casters is bearings, or rather, the lack of bearings. The casters on most OEM carts lack bearings. This means the metal axle grinds on the plastic core of the wheel. This grinding increases rolling resistance, the amount of physical effort required to keep a caster moving.
Carts with high rolling resistance have to be shoved and tugged throughout the day. And this makes them a leading cause of overexertion and lower-back injuries. Casters fitted with axle bearings, on the other hand, are easier to push and pull, and last longer, too.
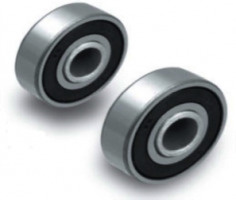
3. Wrong Wheel Material
The resiliency of the wheel is an important factor in determining how easily casters roll along floors and over physical barriers, such as thresholds and debris. Harder wheels typically roll more easily than softer wheels.
If your carts are hard to push and pull, check their wheels to see if they have the right durometer for your floors. Durometer is the scale for measuring or measurement of the hardness of a wheel material. Wheels with the right durometer have better “rollability,” the ease of beginning and maintaining rolling motion.
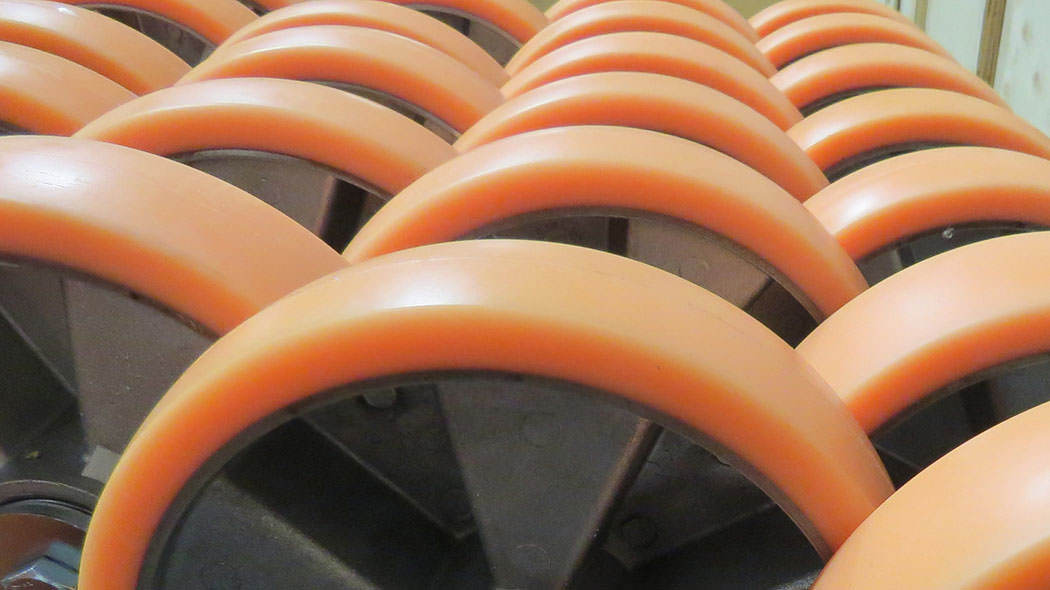
4. Kingpin
Most plate-mount swivel caster rigs feature a kingpin. The caster consists of an upper and lower ball race held together with a nut and bolt, or riveted kingpin. You can typically tighten the kingpin so the caster wears over time, extending the life of the caster.
Kingpinless casters, on the other hand, consist of a forged inner and outer race, held together by the ball bearings. Load is concentrated on the ball bearings, distributing the load over a larger surface area. This allows the rig to be used in heavy and higher-speed applications. The ease of swivel action reduces push/pull force as well.
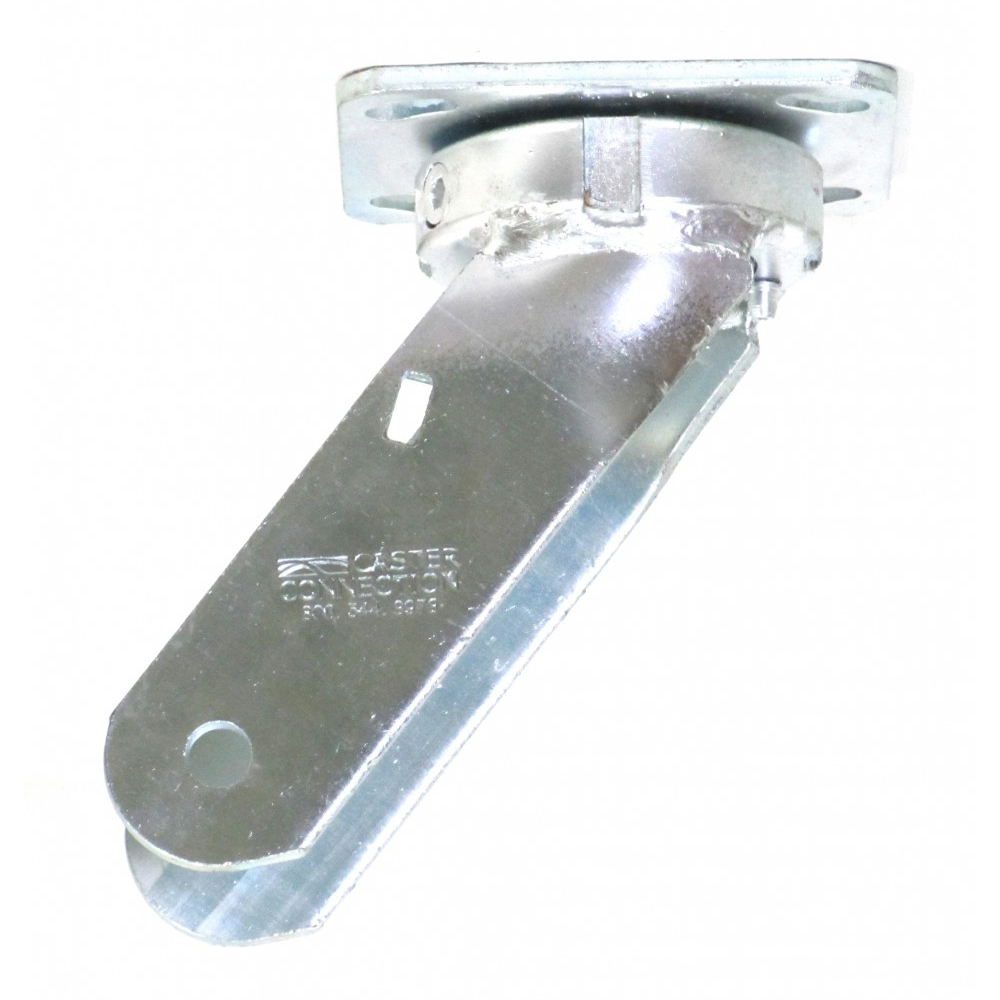
5. Wrong Wheel Diameter
The smaller the diameter of a wheel, the harder it is to push and pull. Or, to put it the other way, the larger the diameter of a wheel, the lower the rolling resistance. If your carts are fitted with caster wheels that are too small in diameter for your application, then they will be harder to push, pull and steer, especially when loaded to capacity, or beyond.
The more uneven or coarse your floor is, the larger your caster wheel diameter needs to be. Rough floor conditions include thresholds, debris, grates, and floors containing embedded rails.
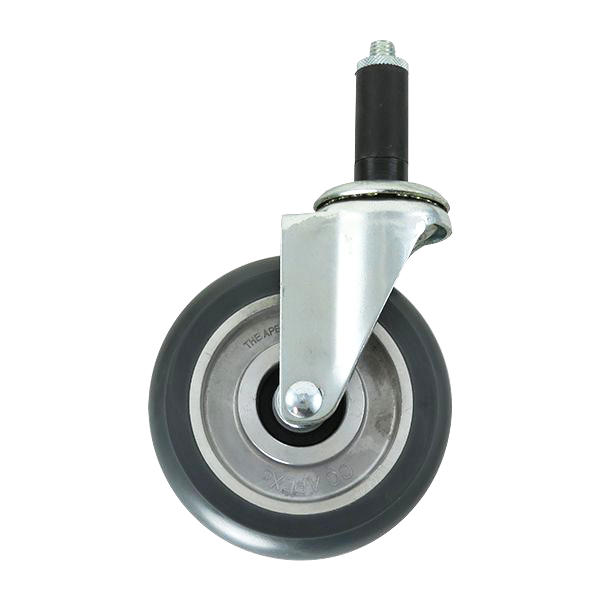
Conclusion
If you want to reduce ergonomic-related injuries in your distribution center, look first to your casters. They may very well be your problem. To deliver the best ergonomic performance, replace your commodity casters with casters that have extended swivel leads, wheel bearings, the optimum wheel hardness, no kingpin and a large enough wheel diameter for the weights you are moving.
Equipped with the right casters, your carts will be easier to push, pull and steer. And your order pickers and associates will be safer—and happier.
Learn More
Learn how better casters are helping distribution centers reduce injuries, improve operations and lower costs. Read our white paper.
Shop casters for distribution centers.
Want to work with a caster solutions expert? Contact us here.