Cost Deployment Modeling For Casters
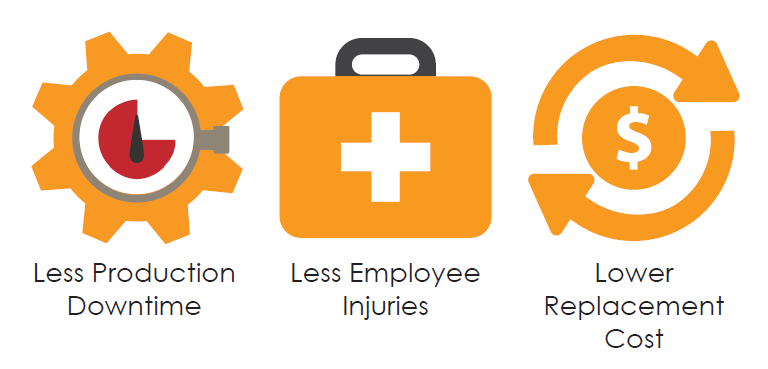
Investigating the relationship between waste, losses and cost reveal data that defines causal loss and resultant loss. An example of causal loss is the cost of downtime of a material handling cart. The cost of mechanical repair/rework can serve as an example of loss due to machine breakdown. The following illustrates a general calculation of costs for reduction of waste and losses:
Downtime Cost = # of people waiting * Downtime * Man-hour cost
Cost of mechanic repair = # of people repairing * Repair time * Man-hour cost
Cost of rework = # of people reworking * Rework time * Man-hour cost
When choosing the correct caster for each application, the goal is to minimize these costs. Caster Connection provides the expertise needed to make educated decisions, and consults each client per application to maximize the ergonomic capacity and longevity for the casters required to capitalize Cost Deployment and Total Cost of Ownership.
INITIAL COST VS. TOTAL COST OF OWNERSHIP
When a company is choosing casters for their application, Total Cost of Ownership must be taken into consideration. High-quality products perform better and last longer, and can be defined by their opportunity costs, demonstrated by less downtime, fewer production interruptions, and maximized production capacity to increase profits.
It is critical for the end user to factor in the Total Cost of Expenses the client will incur during a caster failure. The client will endure the cost of the replacement caster, as well as repairs, replacement frequency, maintenance labor cost, and lost production time. Opting for an inexpensive alternative caster could render downtime, lost productivity and most importantly, lost profits. The up-front cost of choosing the correct caster for an application can provide a significant ROI on the investment made.